When dust levels are high, they tend to reduce the performance of certain non-contact bin measurement tools and thus make them ineffective. Numerous plants operate on three production shifts and continue to fill and empty silos that include ingredients for the production process. However, during production and delivery deadlines, sufficient time is not available to discontinue the filling and emptying process and wait until the dust settles down to calculate material levels.
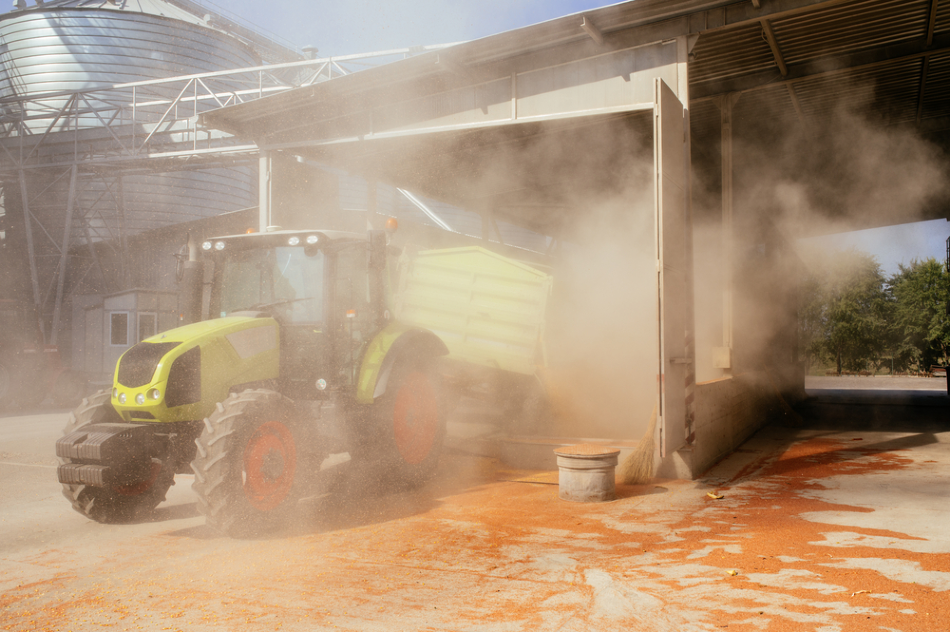
Image Credit: Shutterstock/bbernard
Acoustic Technology
A 3DLevelScanner uses acoustic technology, which is capable of calculating precisely even in very dusty conditions. It runs at a low frequency of 3 to 10 KHz which enables the signal to infiltrate dust and reach the surface of material.
.jpg)
Figure 1. Acoustic technology can penetrate dust to reach the material surface, enabling more accurate measurements despite extremely dusty conditions.
Powder Challenges
One challenge faced during powder measurement is that the powder may not often flow freely and produces an uneven material topography in the silo. This problem gets further intensified with the combination of clumping material and numerous discharge points in the vessel. Material at a single point in the vessel could be lower or higher in contrast to other points in the vessel. In such situations, a single measurement point may not be sufficient in determining the material volume in the bin.
3DLevelScanner
A 3DLevelScanner includes three transducers that repeatedly determine the surface of the material in a 70° beam angle. Since the device is capable of taking various measurements of the material surface, it can precisely assess the material volume in the vessel and even offers average, minimum and maximum distances, as opposed to a single measurement of a static location. While the 3DLevelScanner recognizes each measuring point as an x, y, z coordinate in the vessel, it maps the surface of material surface. Sophisticated software can then create a three-dimensional (3D) visualization of the material surface. This data allows plants to easily manage the filling and emptying processes and schedule appropriate maintenance to eliminate build-up.
Alumina Powder Application
Alumina powder is an exceptionally dusty material that has a volume density of approximately 18 lb/ft3. When the vessel gets filled up, it creates large quantities of dust that never settles down because the operation runs round the clock. Moreover, the concrete and carbon steel bins tend to have flat top and bottom and measure 65 ft in diameter and 70 ft in height. The bins are usually filled and released from the middle; however, the powder material was not able to flow freely. The 3DLevelScanner model MV equipped with 3D visualization was positioned on the vessel’s roof. This was the only device that could operate consistently in the application.
.jpg)
Figure 2. A special neck extension allows the scanner's transducers to protrude further into the vessel to reduce potential signal problems.
Additionally, for silos having more surface area to calculate, the BinMaster MVL multiple scanner system can be employed with two or more scanners. The HE model of the 3DLevelScanner has been designed to determine the level and assess the volume in silos comprising alumina. The HE model can also be utilized for fly ash, clinker and other challenging materials. It is suitable for using in the powder, cement and aluminum industries where high humidity and dust are encountered.
Talc Powder Application
Generally, talc powder is kept in compact vessels that range from 60 to 80 ft in height and 20 to 30 ft in diameter. Talc is an ingredient found in various make-up and personal-care products and hence a non-contact sensor was found to be appropriate for use in talc as this will prevent potential contamination. The 3DLevelScanner offered precise and instant measurement of level and volume along with 3D visualization of the silo contents.
.jpg)
Figure 3. A non-contact sensor sits atop a talc powder vessel to help avoid potential contamination.
This information was utilized to enhance the talc’s inventory management. The 3D visualization, on the other hand, identifies buildup that could occur within the silo repeatedly. This is essential for cleaning and scheduling maintenance so as to eliminate disruptions.
Carbon Black Applications
During the filling and emptying processes, carbon black produces excessive amount of dust and typically clumps and sticks to silo walls, thereby causing build-up. The advanced dust-penetrating technology in the 3DLevelScanner provides precise, consistent, and instant measurement of volume and level of carbon black even in extreme environment. It also offers a 3D image of how carbon black is dispersed within the silo.
Detergent Application
Granular brightening powder used in detergents was stored in carbon steel bins with a plastic lining. The high dust material was also potentially explosive, so the sensor had to meet hazardous location standards. The 3DLevelScanner was able to meet regulatory requirements.
.jpg)
Figure 4. Granular brightening powder is a high-dust material that's potentially explosive, so sensors must meet hazardous location standards.
Polyurethane Powder and Silica Granules Application
Polyurethane powder is a complex material and is quite difficult to manage. A composites manufacturer dealing in roofing and waterproofing products required better inventory management. In this situation, the 3DLevelScanner’s non-contact technology provided precise and continuous measurement of volume. Similarly, silica can prove difficult for certain non-contact sensors to calculate, because of irregularly shaped particles and hence may result in incorrect measurements. The 3DLevelScanner was able to deliver precise and real-time measurement of the volume and level of silica granules in the vessel.
.jpg)
Figure 5. Silica used to make coatings can be difficult for some non-contact sensors to measure due to irregular particle shape which may deflect pulses and cause inaccurate measurements.
Conclusion
In North America, the 3DLevelScanner has been deployed in more than 400 operations. Each installation has its own set of exclusive operational concerns and data requirements for decision making. Although it cannot solve all problems of level measurements at the facilities, the 3DLevelScanner has proved to be suitable for plants where other volume measurement solution are unavailable.
.bmp)
This information has been sourced, reviewed and adapted from materials provided by BinMaster.
For more information on this source, please visit BinMaster.