3DLevelScanners have been producing highly accurate volume and level measurement in challenging materials held in tanks, bins, and silos for almost a decade. It transmits pulses in a 70° beam angle, accounting for uneven surface topography and recording multiple level measurements when calculating volume. A 3DLevelScanner is the only sensor to map and measure the material surface.
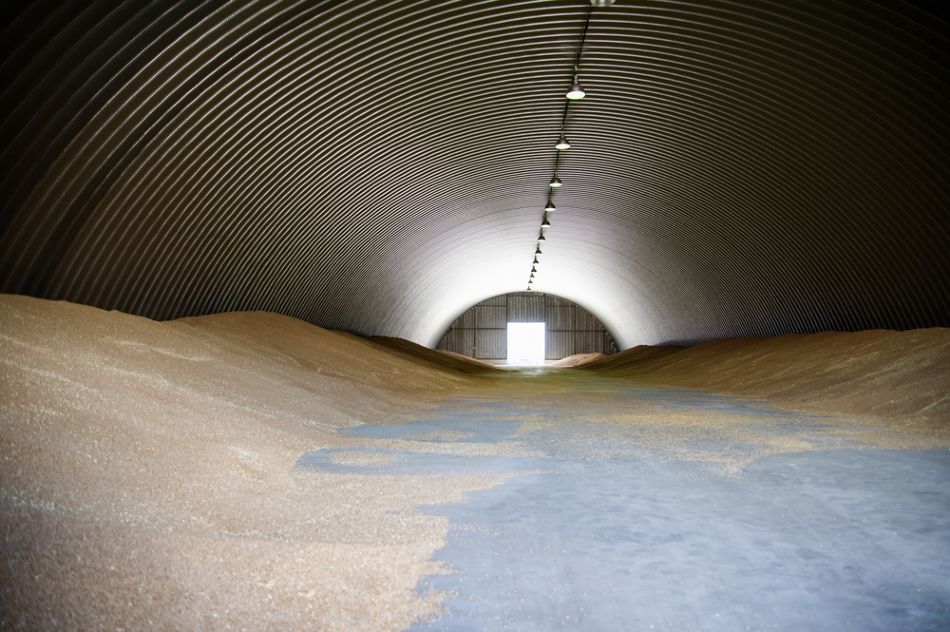
Image Credit: Shutterstock/DCByte
Every sensor includes 3DVision software that records the highest and lowest points detected, plus the average level, from a weighted average of every measurement in the bin. A colorful graphical representation shows where high and low spots are in the silo for the MV and the MVL models. 3D scanners keep addressing the questions of increasingly complex grain storage operations.
View Numerous Silos on One Screen
MultiVision software for inventory visibility across an organization Inventory management affects multiple departments across grain storage or processing operation. Plant personnel need accurate volume to manage storage and sales, and finance needs accurate valuation for financial statements.
To provide corporate-wide visibility, the optional 3D MultiVision software enables users to view data for multiple bins in a single window. Since it is Windows-based, it can be configured for 24/7 access via an organization’s Local Area Network (LAN).
All versions of the dust penetrating, non-contact, 3DLevelScanner, including the RL, can use MultiVision software data throughout the whole organization (or with vendors using VMI) to improve operational decisions, logistics, purchasing, and financial management.
Each user can customize their screen to view all bins or a group of bins and color-code bins by material type because of intuitive operation and a user-friendly setup. Users can set low-level and high alerts to be advised when bins reach critical levels. There are no third party data access fees or applications because the software is installed on the LAN (Images 1 and 2).
.jpg)
Image 1
.jpg)
Image 2
Detect and Alert to Centre of Gravity Danger
Prevent Silo Collapse or Damage Using 3DLevelScanners
Grains are recognized to bridge, pile unevenly, build up on sidewalls, and flow unpredictably from storage vessels. This means that observing the volume of material inside the vessel can be difficult, and uneven disbursement of material can also damage the storage vessel itself.
As time passes, the walls of concrete or steel silos have been known to wear or fail causing buckling, cracking, bending and denting. It can lead to catastrophic silo collapse in the worst cases. This has happened to grain bins worldwide. The walls of large storage vessels give way to the weight of grain which has built up on one side of the bin over a period of time.
There is a software option that utilizes 3DLevelScanners to detect the center of gravity, show it graphically, and alert when the center of gravity moves outside of a chosen area. This is useful for plant operations that want to detect uneven loading of silos that contributes to structural wear or failures.
A 3DLevelScanner is mounted in an optimal location on the roof of the silo to observe the material surface in the silo. Level measurements are employed to establish the X, Y, and Z coordinates of the center of gravity depending on the material topography.
Users define the accepted area and alert parameters into which the center of gravity must be contained. The coordinates are processed in 3DMultiVision software via a proprietary RS-485 communication protocol. A 3D visual will illustrate the location of the center of gravity and display if the current center of gravity is within the allowed area (Image 3).
This unique solution to help reduce structural stress when emptying or loading a silo can be utilized by operators. It is a helpful preemptive maintenance application that can warn users about the need for cleaning or inspection. Silo integrity is improved with use over a period of time, which creates a safer environment by forewarning of potential structural stress generated by uneven loading (Image 4).
.jpg)
Image 3
.jpg)
Image 4
Measure Volume in a Wedge or Pie-shaped Silo
Accurate inventory for ingredients in segmented silos (Image 5)
Milling or grain operations regularly handle grains at different phases of processing, which are normally kept in segmented silos. Irregularly shaped spaces can be tricky, especially for grains or flours that can build up on the outer silo perimeter or interior walls, so calculating inventory by volume is difficult.
Purchasing personnel or Plant operations with the task of supervising inventory in silos or pie-shaped segments now have a solution that supplies volume data that is extremely accurate. The 3DLevelScanner calculates and models the topography of material within these unusual pie-shaped wedges. The measured distances are applied to a 3D model of vessel dimensions and converted it to a concise volume measurement in the newest update of 3DVision software.
.jpg)
Image 5
Lack of material flow or the location of the filling or emptying points can cause uneven piling of material, which could result in inventory estimates that are based on a single measurement to be incorrect.
Other measurement sensors, such as guided wave radar, non-contact radar, or weight-and-cable style sensors measure only a single distance in these formidably shaped segments. In comparison, the 3DLevelScanner surveys the material surface, considering variations or buildup, then factors in the height and radius of the section being measured, resulting in very precise volume accuracy.
Using a system that gives correct data about the dollar value and amount of material on hand can help increase inventory turns, reduce safety stocks, and ultimately pay for itself by freeing up funds that are tied up in inventory. This can be the case, particularly for oilseeds, high-dollar rice, and grains, that are used in many organic or contemporary food products.
Furthermore, buildup on the outer perimeter of the silo segment or along the interior walls of each segment can be identified, accounted for in inventory, and addressed by maintenance if needed. The same 3DLevel Scanner can be utilized for either round or segmented silos, which means it is an adaptable choice throughout its long sensor life.
Level Monitoring in Flat Storage Warehouses
Breakthrough technology measures level per section (Image 6)
There is a shortage of grain storage because grain production worldwide has hit peak levels which means valuable commodities await additional processing. A short-term solution to preserve grain is the use of large, sheltered storage buildings where grain can be stacked using vehicles or overhead conveyors. Although, it is extremely difficult to gauge the amount of grain in these temporary warehouses because of irregular piling.
.jpg)
Image 6
A new software option that calculates the amount of materials piled under structures is another revolutionary breakthrough unavailable with any other inventory management system. Numerous sensors measure and map levels over the material surface, while MultiVision software divides the piled material into virtual sections. Maximum, minimum, and average levels for each section are detailed for up to 99 unique sections. The data is formed to output a visual showing the topography of the whole storage building (Image 7).
.jpg)
Image 7
This pioneering solution is used to gauge inventory and enhance production efficiency. Identifying high and low sections makes way for managing the filling or extraction of materials and automating process control. Up to 20 3DLevelScanners have been mounted in the upper structure of a warehouse roof in proven installations.
The building is virtually separated into sections as small as 1.5 by 1.5 meters with 3D sensors constantly calculating adjustments across the surface and supplying data reporting and unique visual of inventory in the huge structure.
This leading technology is excellent for corn or other grains stored in covered buildings. 3D scanner technology began a revolution in precise inventory management in 2009. Their evolution is ongoing and is constantly addressing the distinct needs of industry, as software and sensor hardware intersect with new solutions.

This information has been sourced, reviewed and adapted from materials provided by BinMaster.
For more information on this source, please visit BinMaster.