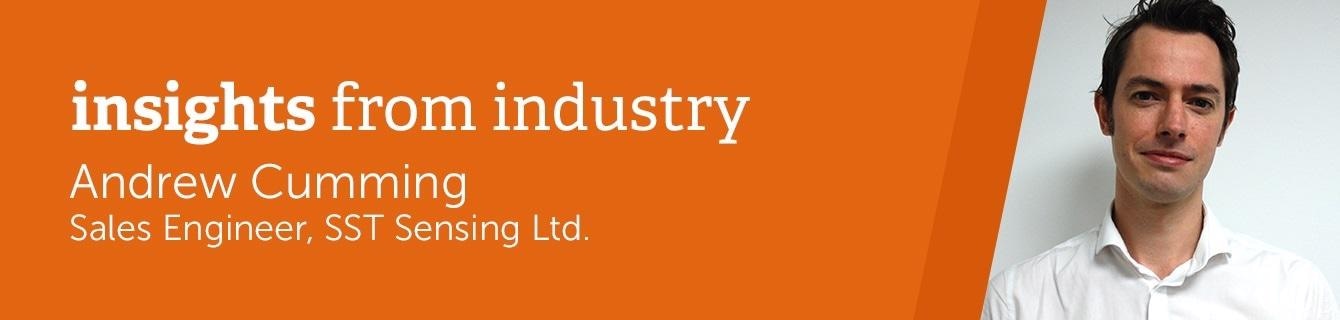
In this interview with Andrew Cumming from SST Sensing we discuss the importance of sensors that are customised your specific needs for various applications and how the solutions from SST Sensing can help you achieve this.
What are SST Sensing’s expertise and do you supply customisation within your range?
Yes, we supply custom sensors. SST Sensing Ltd. design, manufacture, customise and configure sensors and switches for gases and liquids, specifically for oxygen monitoring, CO2 sensors and liquid level detection.
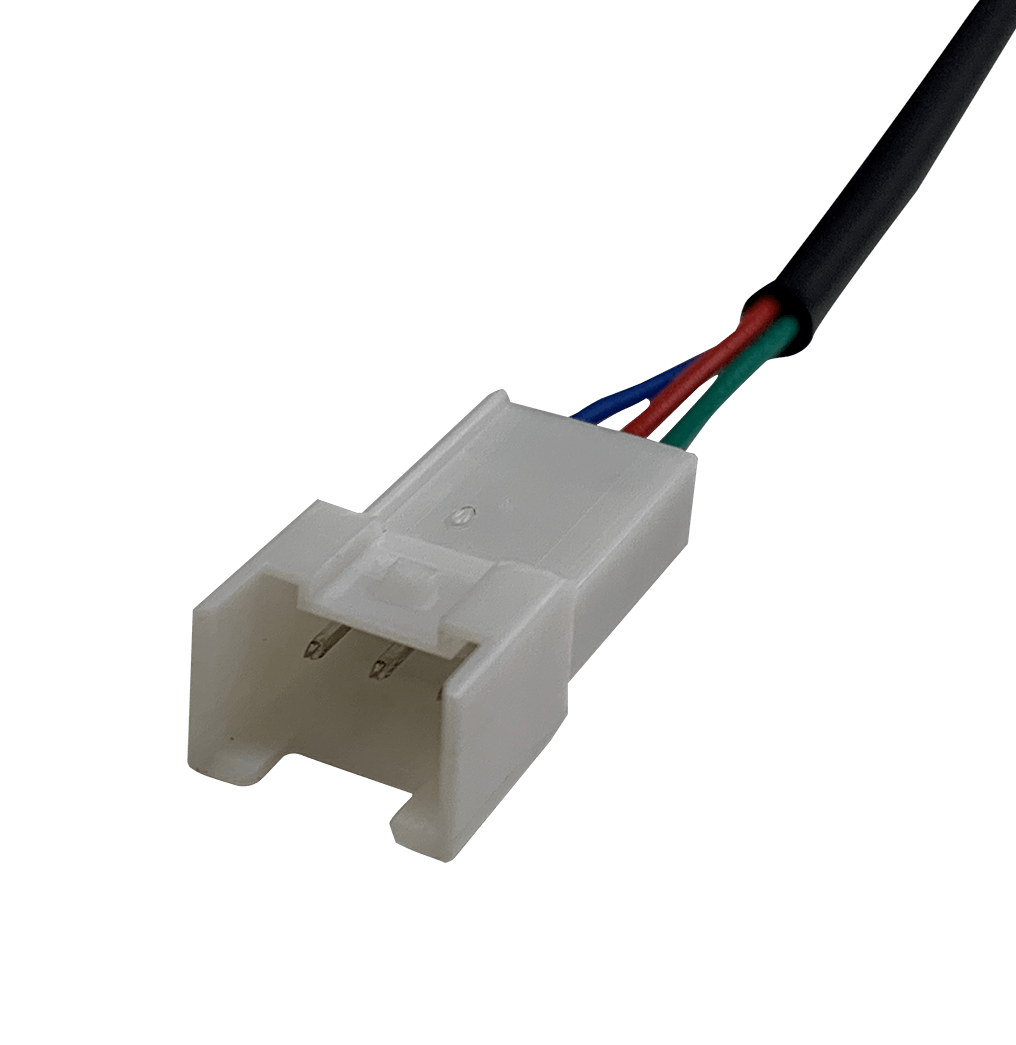
Last year we produced over 390,000 sensors at our 1,400m2 facility in Scotland and have an impressive 98.5% on time delivery to customers, to which we ship globally.
As an ISO9001:2015 accredited company we produce products which are designed and manufactured to exacting standards, with some of our sensors approved for use in aerospace applications.
Established in 2002, SST has a long history of project-based success where we’ve worked with the customer from design to mass production. This has been done with an importance on maintaining a high standard of customer service, technical support and established design principles.
Our sensors are used in many diverse applications within industries such as medical, industrial, pharmaceutical, transportation, marine, aerospace and telecommunications.
What is needed for a custom sensor solution and how can the customer be sure they have the right sensor for their application?
Primarily it is working with the customer to understand the application, asking the right questions and jointly establishing the sensor specification.
Communication is key to this. SST’s understanding of our product, its capabilities (and its limitations) can aid in making the selection of the correct sensor suitable for the application.
SST have a wide range of products we design and manufacture. These are split evenly into general sales items and customised solutions. Our background as a design and manufacturing company means we have the capabilities to create custom sensor prototypes for test within a few days.
When do customers come to SST looking for a custom sensor technology?
Often a customer comes to SST because they are having a technical or supply chain issue.
A common response we hear are that the customer is using an alternative product that is failing in the field or that this other supplier is constantly changing prices, failing them on lead times and not answering technical support. In today’s global economy this is unacceptable and this is where the customer needs something to fit into their product without having to make any changes. We can use customisation to fill that space for them.
Sometimes someone is entering into a new venture and looking for an engineer to talk them through the technology and help to advise on implementing their design. Often we find it is the mechanical engineer that has been tasked with finding a solution in the unfamiliar territory of liquids and gases. The primary solution is to offer our standard products but discussions can easily turn into a new concept for a custom sensor technology.
What process does SST have to ensure that the customer gets the best custom sensor for the application?
SST has a dedicated team of engineers who are tasked with the daily management of custom sensor projects. The customer engineering team is headed up by Technical Director, Patrick Shannon. As a veteran in the field of engineering, he draws from his own experiences and knows all to
o well that the key to success needs engineer-to-engineer conversations with quick turnaround and a high degree of flexibility.
It is this team that provides the clear communication needed to transition from concept, to design and into the production stages. The results are customers getting the right custom sensor at the right price, that allows a quick time to market.
The experience gathered within SST from each project cycles back into our NPI (New Product Introduction) process. A review process that keeps our roadmap competitive and, where appropriate, allows the introduction of competitive products to the standard line card.
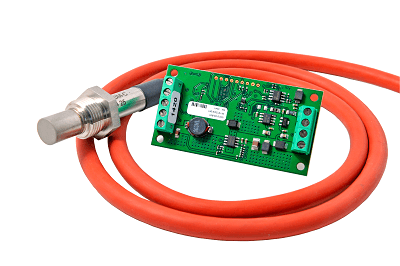
Can you give examples of the types of customisation available?
A general summary of customisation capabilities for both gas and liquid sensors would be:
Connectors and cables: we can make custom sensors with specific terminations. This can be a branding requirement or a need to retro fit into an existing space or a one source option.
Special outputs: Many liquid detection sensors can require special programming to counter specific application conditions. Their microcontroller means they can be factory programmed and tuned to counter such conditions containing foams or condensation.
A time delay can be used to allow confidence before switching. Narrowing a high/low output between the voltage rails can add a degree of failsafe behaviour to the sensor.
Some of our oxygen sensor control boards can have a different analogue output range or specific start up requirements to integrate into an existing boiler system.
Custom housings: We already have a wide range of material options but sometimes another is required due to the environment the sensor is exposed to.
One of the success stories with SST zirconia sensors measuring oxygen in the flue gas of boilers. A customer requested a sensor with an M18 thread similar to the popular LSU 4.9 Bosch Lambda sensors. The SST ‘screwfit’ type housing now allows the easy Lambda sensor replacement and for the customer to take advantage of our zirconia technology’s benefits.
The above would really encompass a majority of what we would class as simple customisations.
Typically, the initial stage would be to see if a general sales item is available to test the suitability of the technology. Along with responsive technical support to understanding its implementation.
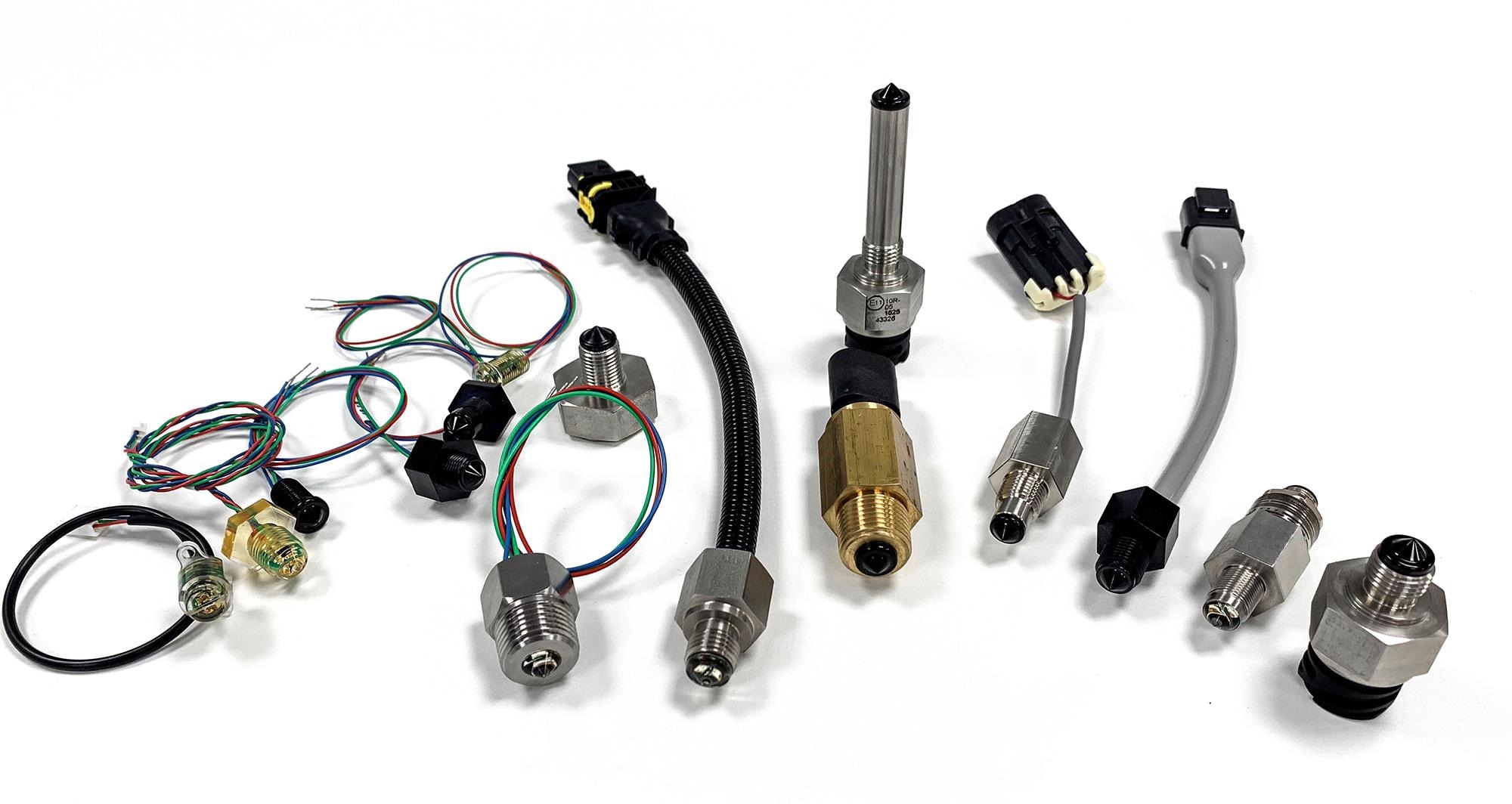
What is a recent example of customisation you provided for a customer?
SST was quick to offer a lot of customers an alternative solution to the recent obsolescence of Honeywell liquid level sensors.
A new family of SST ‘alternatives’ directly matched to the Honeywell part numbers of LLE and LLN products were implemented to save customers the painful experience of product redesign. Not only this but using our knowledge of the products, the SST electrical designs are more robust in their design.
With this situation a quick turnaround customisation became essential and this is where SST excels.
One such customer was a food processing company who needed a specific cable termination for their Honeywell sensors, LLE102000 and LLE103000. It became clear after establishing the application detail that they had been using the Honeywell sensor successfully in an unconventional manner.
As the original sensor was of an old design where the LED was on most of the time and consumed more power. Subsequent designs of this technology had changed the operation of the sensor to consume less power as well as able to operate in an environment with high levels of condensation.
Another part of their application required the sensor to work in high fat content milk, which is a high amount of solid fat suspended in liquid. This can also have issues with creating a reflective surface to which the sensor needs to counter.
Usually a simple customisation of the SST software would be able to counter either of these issues but the customer wanted one sensor for both applications.
The solution was to supply an SST sensor with both software and hardware customisations. The specification for samples, technical support and clear communication from both parties were what made this a successful case.
Where can the reader go to find out more about your solutions and what can they do to get in contact?
Our website gives the best overview of our general sales items, but when it comes to customisation there really is an infinite amount of possible modifications.
The best way is a conversation with us. It is the quickest way to establishing the requirements and route to a solution.
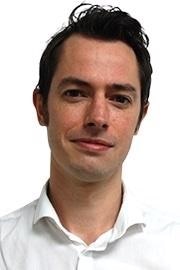
About Andrew Cumming
Andrew has worked at SST Sensing for 3 years as Senior Technical Sales Engineer. He is SST’ primary contact to customer technical queries and support requirements. Based in Glasgow, Scotland, he originally studied Electronic Engineering BSc(Hons) where his career began in the semiconductor industry. He has over a decade’s experience that has focused on customer and technical support.
Disclaimer: The views expressed here are those of the interviewee and do not necessarily represent the views of AZoM.com Limited (T/A) AZoNetwork, the owner and operator of this website. This disclaimer forms part of the Terms and Conditions of use of this website.