Six Considerations for Success
Many organizations will have heard of level sensors and the wide range of available measurement technologies. Not everyone understands how sensors function, and the other components offered to provide a total management solution to silos or the variations between the types of sensors and each of their advantages and disadvantages.
This article has been created to provide a basic understanding of silo inventory system components to help companies ask their vendors' informed questions. It will also offer insights into certain elements that may be overlooked but can optimize any plant's efficiency.
The following are six factors to consider when devising a silo inventory system:
- Sensor Selection
- High-Level Alerts
- Wireless Options
- Remote Monitoring
- Local Data Access
- Flow Detection
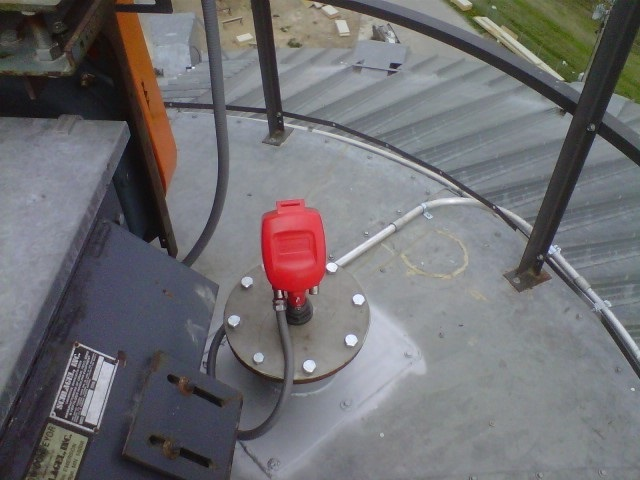
Image Credit: BinMaster
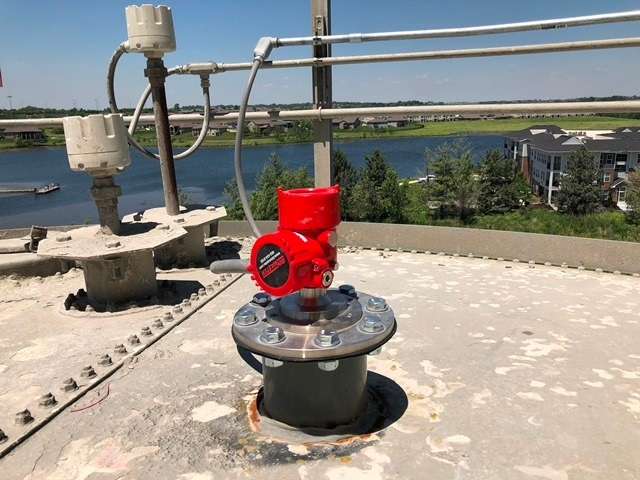
Image Credit: BinMaster
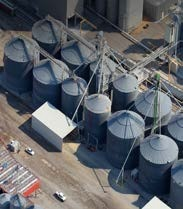
Image Credit: BinMaster
Sensor Selection (Hero New 3D)
When inventory changes need to be monitored, continuous level sensors will consistently take measurements over time to offer the most recent data. These sensors are broadly divided into two types.
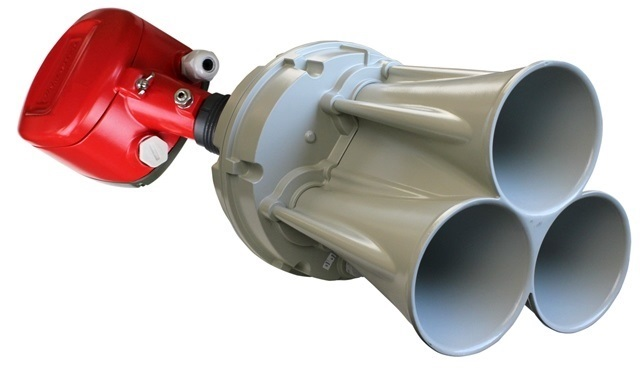
Image Credit: BinMaster
Technologies like radar, acoustic, ultrasonic, and laser are used in non-contact sensors. The value of using non-contact sensors is that they do not physically contact the material or intrude into the silo. There is no risk of cables impeding augers or different internal mechanisms within the silo.
On the other hand, cabled sensors will have intermittent or frequent contact with the material. Examples of these are weight-and-cable or bob type sensors and guided wave radar sensors.
Each of these types is highly dependable when maintained, applied, and installed correctly. Each technology has its place in relation to the material being measured, the vessel's size, the relative cost of the sensor, and the physical environment.
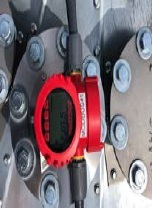
Continuous level sensors take frequent readings. Image Credit: BinMaster
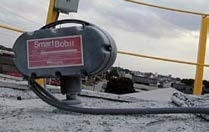
Image Credit: BinMaster
High-Level Alerts
A point level indicator is another type of sensor that is crucial to an inventory management system. As the name suggests, it senses and triggers an alert when the material in the silo reaches a defined level. The most widespread point level indicators employed in inventory management systems are vibrating rods, rotaries, and capacitance probes.
Point level indicators are an inexpensive addition to silo equipment that can generate cost and time savings. When a silo is nearly full, they function as a redundant alert. The prevention of overfills means that time spent cleaning up messes is removed, but more crucially, these sensors guard the more costly continuous level sensor at the top of the silo, which could be harmed from an overfill.
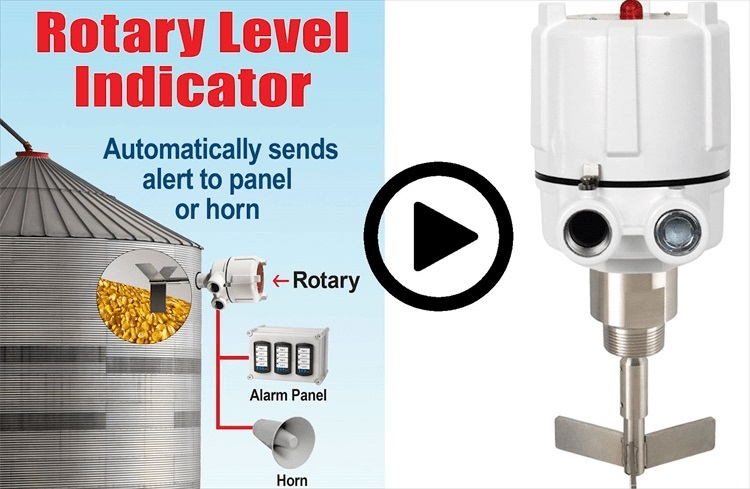
Video Credit: BinMaster

Video Credit: BinMaster
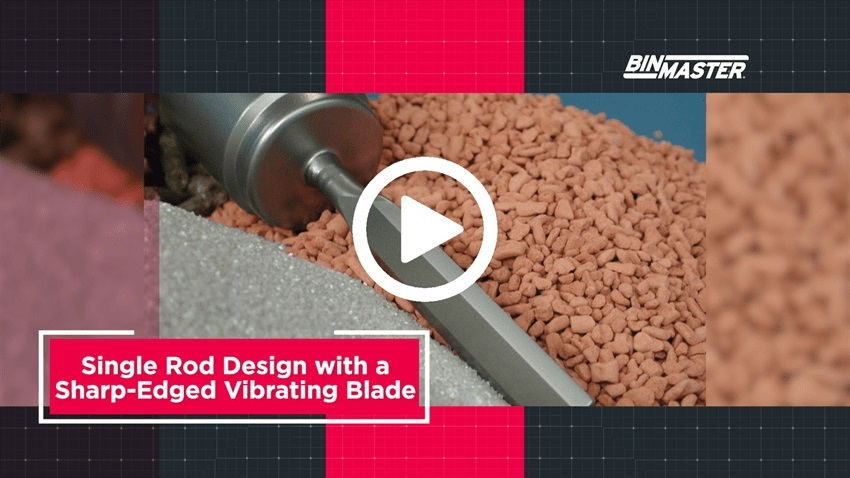
Video Credit: BinMaster
An additional function of a point level sensor is that when the silo is nearly empty, the sensor triggers a low-level alert. This helps personnel to know when the inventory is running out before a process must be stopped. While the continuous level sensor will be monitoring inventory as runs out, the point level sensor will make sure personnel are alerted to replenish before production is halted.
A point level indicator should be thought of as an insurance policy. It may not be needed all the time, but it is crucial when required. It has a long service life and offers a fast return on investment.
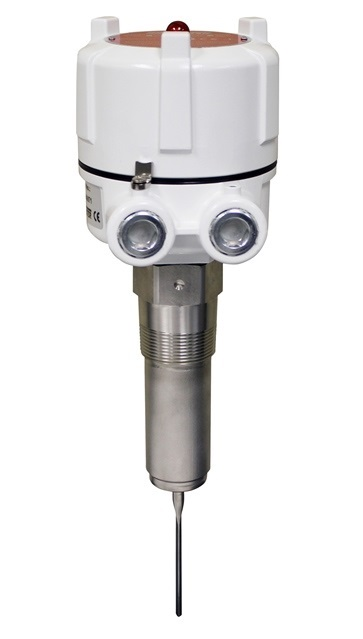
Image Credit: BinMaster
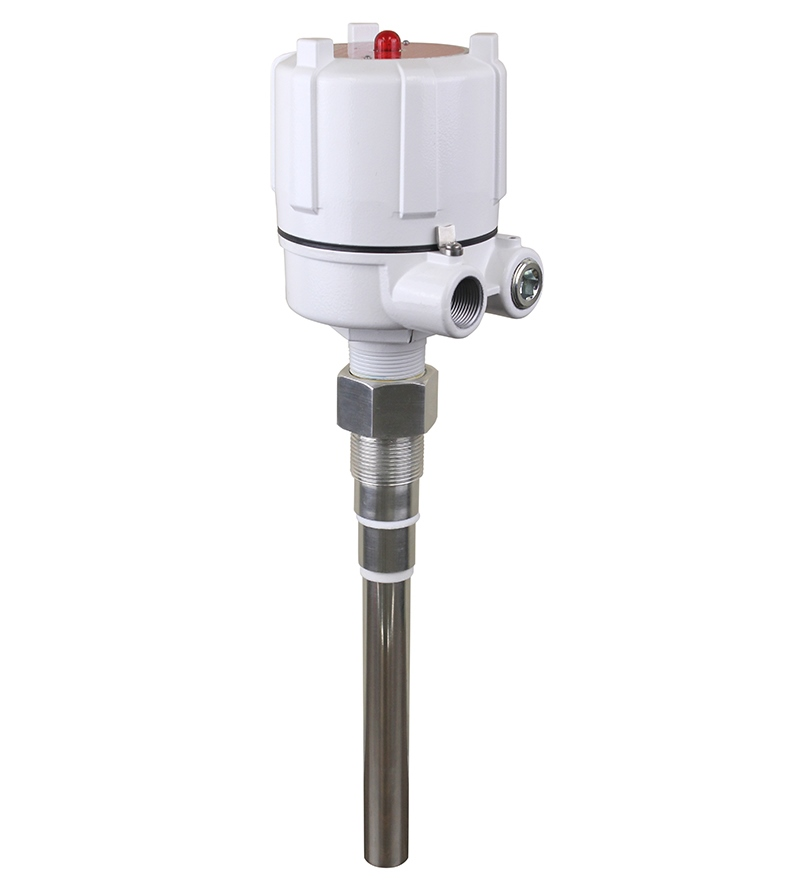
Image Credit: BinMaster
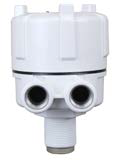
Image Credit: BinMaster
Wireless Options (BinCloud Gateway)
High-cost wiring is often a barrier to plant owners gaining an automated inventory system. Still, there are options to partially or almost completely replace long spans of wire that increase installation expenses.
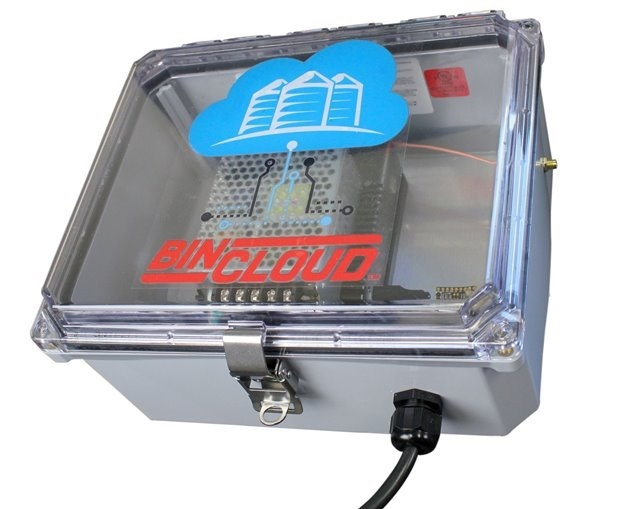
Image Credit: BinMaster
Arranging a group of silos together in a ring, in a daisy-chain formation, is one of the more popular solutions to this challenge. This wiring arrangement enables several sensors to be wired together in series to decrease the amount of wiring required significantly. A single wireless gateway is then constructed to transmit level data for several sensors seamlessly to the cloud for processing.
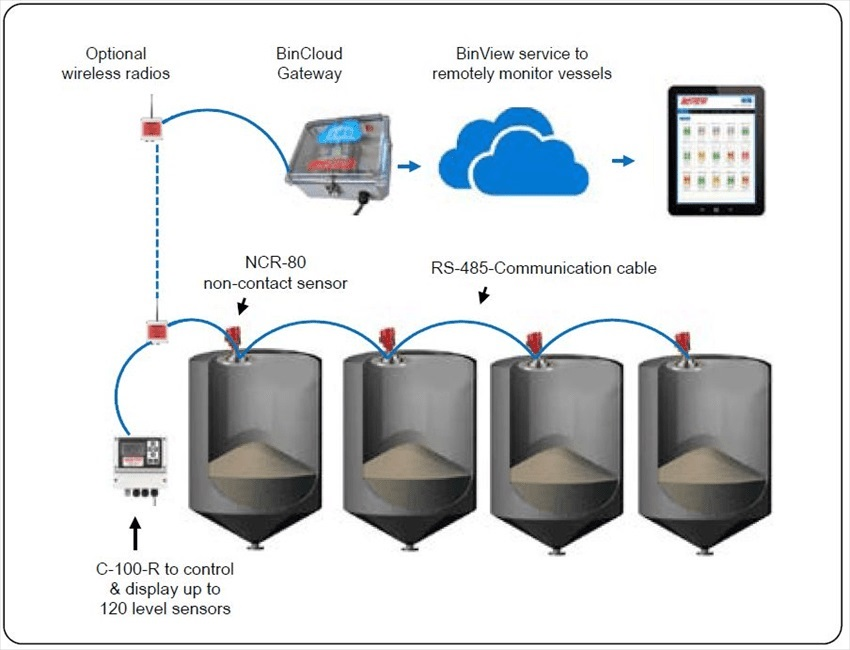
Daisy-chaining reduces wiring costs. Image Credit: BinMaster
When several groups of sensors in large plants, gateways, and daisy-chaining enable the whole plant to be connected at a much smaller cost than conventional wiring.
Wireless transceivers and antennas can additionally be used to cover large distances. Long-range or LoRa communications can be employed for an unobstructed line of sight and can reach distances of up to one mile.
Remote Monitoring
Remote monitoring is now a necessity rather than a luxury with many people working from home. Even staff who continue to work at the office or plant must instantly access inventory data. Additionally, many colleagues are responsible for locations across the country or across town.
Inventory management programs, which can be accessed from an app, a corporate server, or a website, are simple to use and deliver the information required for personnel across many functional areas of a company to carry out their roles.
A number of organizations provide inventory access to logistics, production, financial groups, and purchasing at the same time. When inventory data is automated, self-service, and up-to-date, teams can spend less time sending emails, on phone calls, and in meetings.
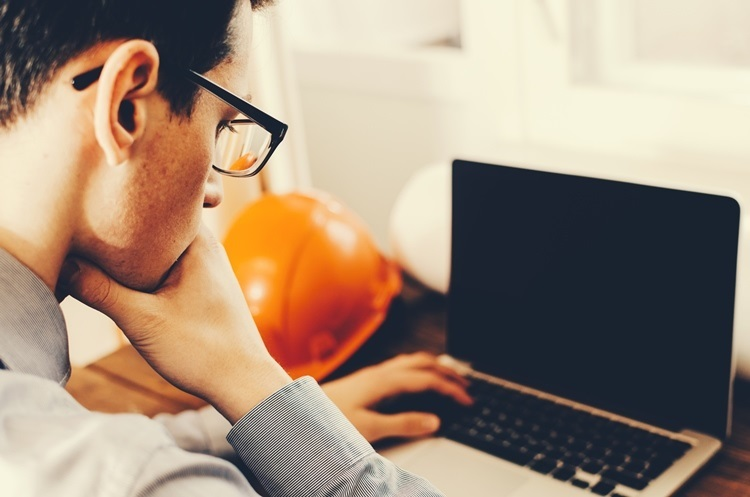
SaaS web sites provide inventory data. Image Credit: BinMaster
Several operations teams ask their suppliers to be involved in the delivery and ordering process. When this happens, the vendor gains access to the plant’s silo information. Vendor managed inventory enables collaboration between plants and suppliers and shares live data to uphold consistency in the supply chain.
The next step in this process is to monitor the inventory using a secure website once level sensor data has been connected to the cloud. Many types of inventory monitoring programs have been developed. Some are for specific materials or industries, whereas others can be deployed across a broad range of geographies, industries, and materials.
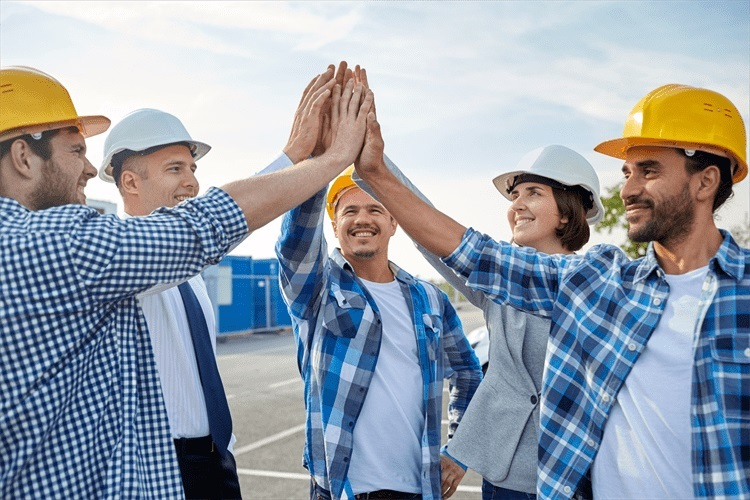
Vendor managed inventory reduces material outages. Image Credit: BinMaster
Developers understand that chemical or cement plants' requirements can differ from a plastics plant or a feed mill. Cement plants must connect dispatchers to batch plants and suppliers. Hog feeders need to monitor daily feed consumption, monitor bins simultaneously, and track different feed types.
It is crucial that all personnel involved are making decisions on the same data at the same time. This results in reduced safety stock, increased inventory turns, shorter lead times, enhanced cash flow, and higher profitability.
Local Data Access (Updated C-100 Console)
Frequently running to the control room or the office is not viable during a busy workday. Climbing a silo is even less practical. Production employees frequently want an efficient reading of what is in stock. Drivers want to understand if a total load will fit into a silo.
Adding a digital panel meter or a control console enables personnel to drive or walk up to a console installed at an accessible location. These rugged and compact devices can be set up to monitor one or several silos with the push of a few buttons. Silo levels are displayed in real-time along with the height of the material and the headroom (distance to the material).
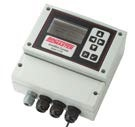
Image Credit: BinMaster
They function by programming the key parameters such as silo diameter and height into the console. The need to walk to each separate silo is excluded as users can easily scroll through the silos configured on the console.
Consoles can simply integrate within an inventory management system or can be used as a standalone display. They are compatible with sensors with a 4-20 mA or Modbus output.
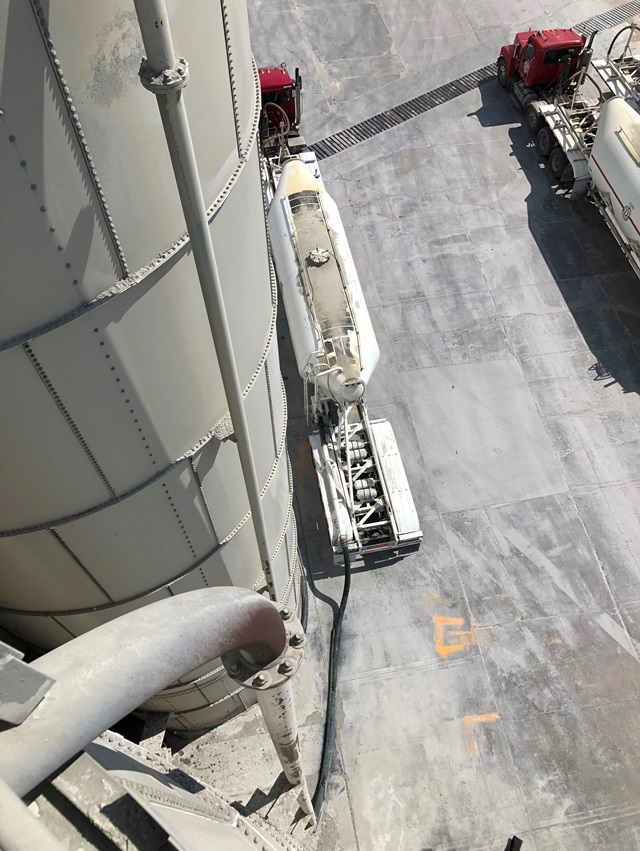
Image Credit: BinMaster
Flow Detection (FD-2000)
Sensors to monitor flow is another feature to consider in an inventory management system. Conveyors, distributers, and chutes that move material into silos or from one process to another can become overfilled, clogged, or can become empty.
Plants that process several products must ensure that the proper ingredients are funneled into the process without being cross-contaminated.
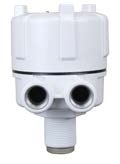
Flow detectors ensure continuous processing. Image Credit: BinMaster
A flow detection sensor identifies flow or no-flow environments. They are highly sensitive and can observe tiny amounts of flow in the small powders or granules. Flow detection is fundamental when changing from one ingredient to another during processing in sectors like animal or human feed, cement manufacturing, or chemical processing.
Flow detectors can also trigger an alert when a conveyor has run empty or if the material is not flowing through a pipeline or a chute. This can stop materials being conveyed into a silo, which would lead to a material shortage or means the process has to be stopped.
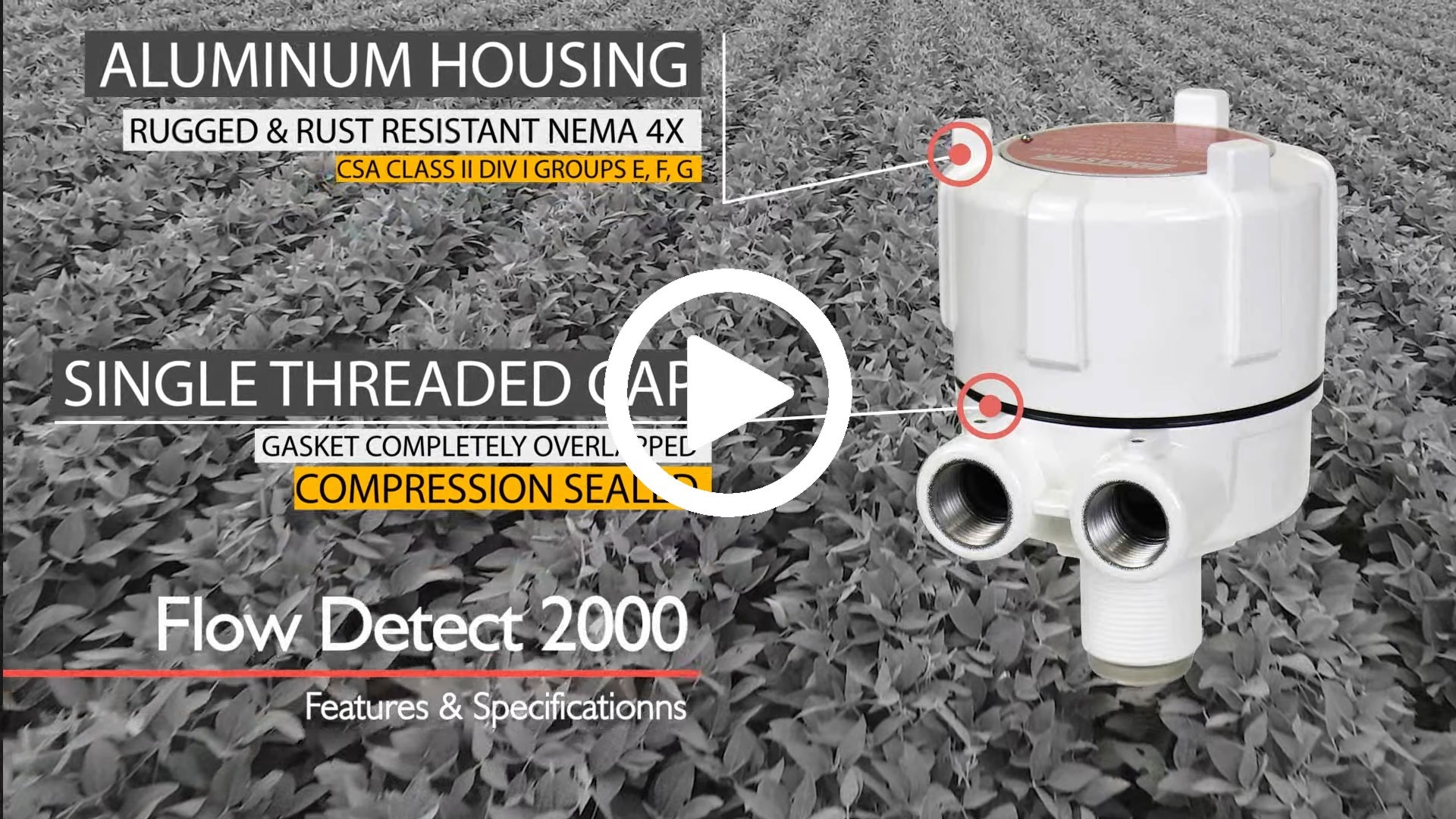
Video Credit: BinMaster
Reasons Inventory Systems Fail
These are the most common reasons for inventory system failure:
- Spreadsheets or tape measurements are relied on
- People create their own ways to manage inventory
- It is too far to walk to the control room
- Nobody wants to climb silos
- The sensor has been incorrectly installed
- The sensor technology is inappropriate for the task
- Everyone is looking at different data
- People require their data instantly
- The inventory data is not up to date
This article helps plant owners to avoid these mistakes.
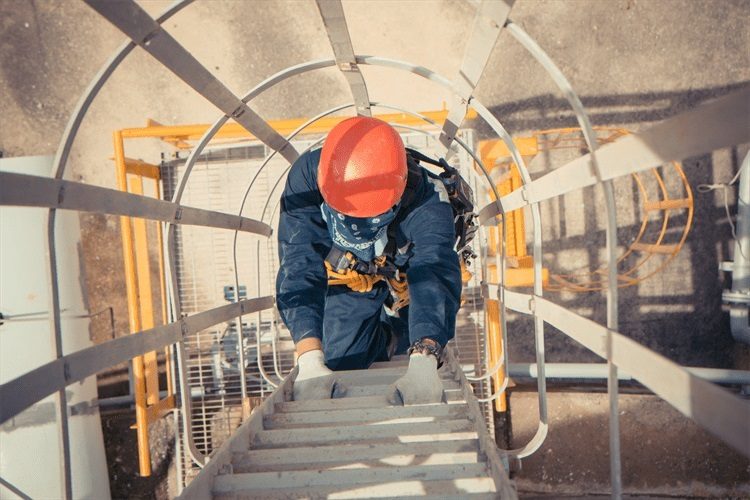
Image Credit: BinMaster
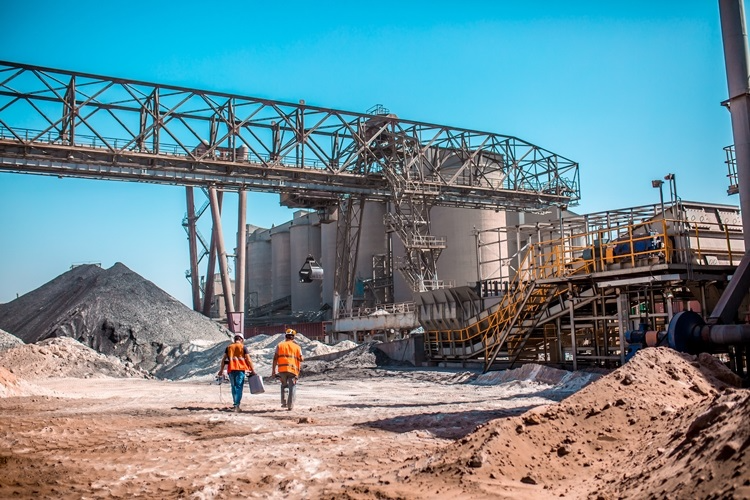
Image Credit: BinMaster
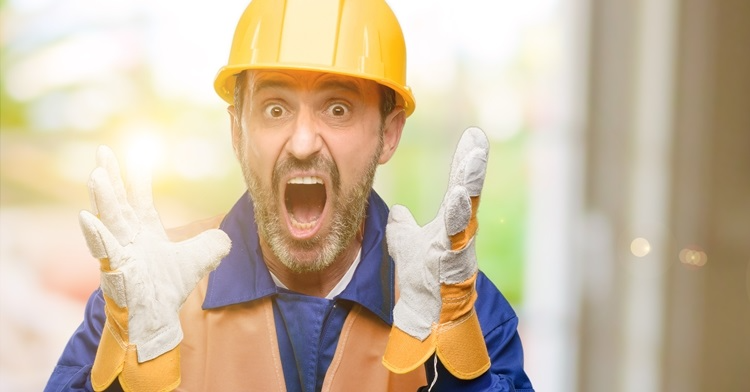
Image Credit: BinMaster
Weight and Cable (SmartBob)
The weight-and-cable sensor or bob-style sensor functions as an automated tape measure. The sensor drops a weighted cable to the material's surface, where it is fixed to the top of the silo. The cable retracts upon impact where it counts pulses, which are calculated into a level measurement.
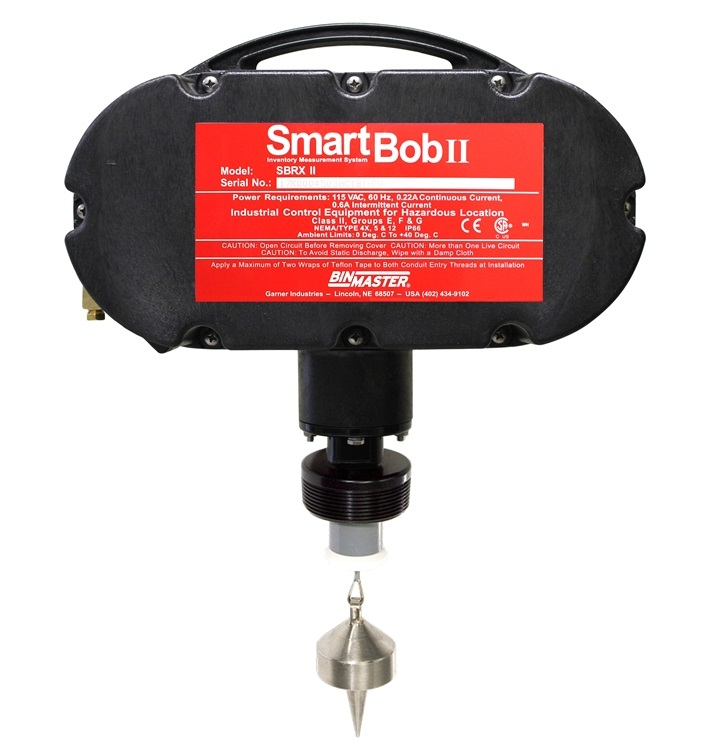
Image Credit: BinMaster
Measurements are scheduled at predefined time intervals to monitor inventory changes over time. These sensors are employed in liquids or solids and can also determine the level of sediment that has gathered in a liquids tank.
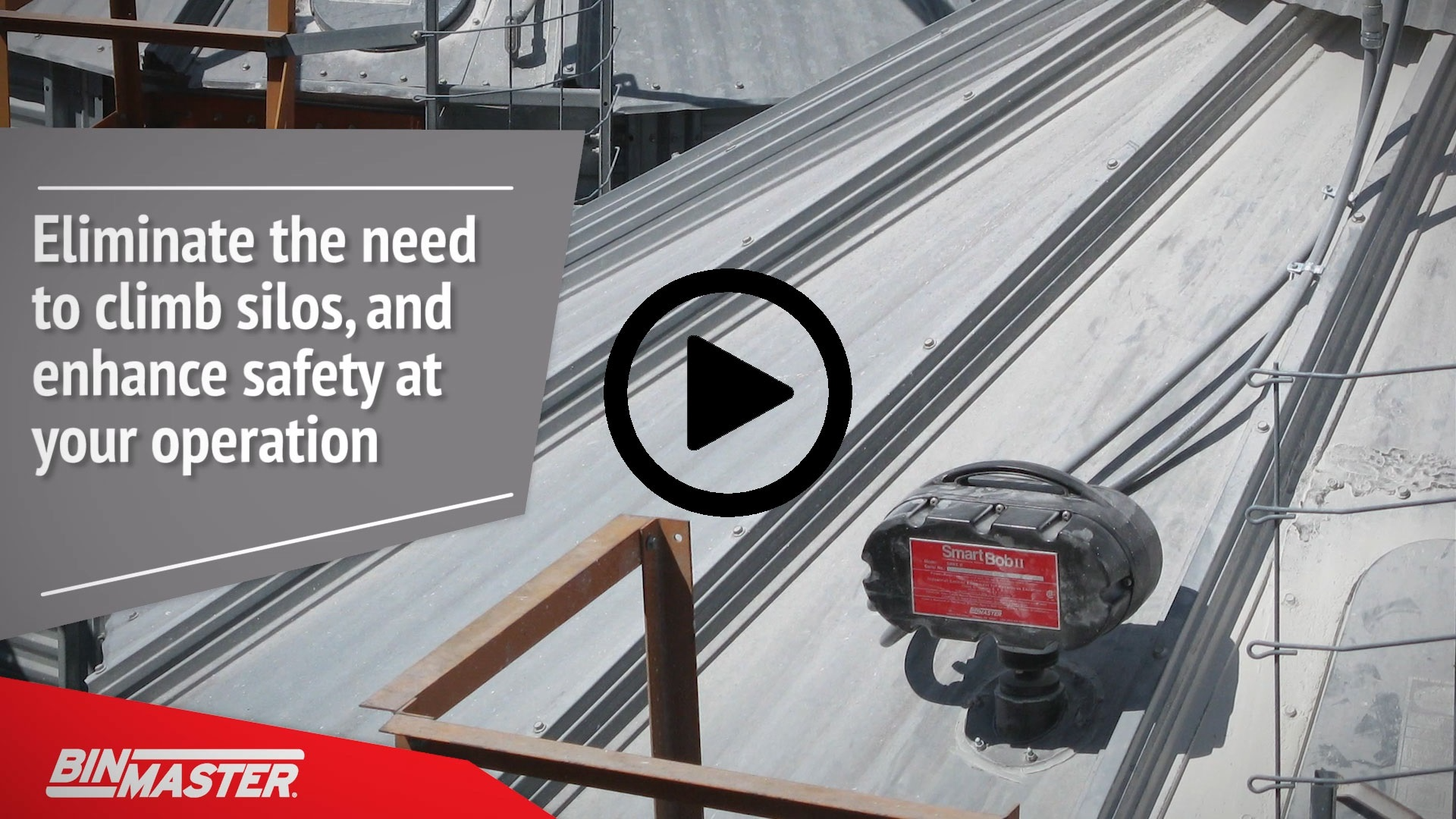
Video Credit: BinMaster
Strengths
- Not impacted by material buildup on the sensor
- Not impacted by dust or other challenging process environments
- Measures bins up to 150 feet
- Can be used in signal absorbing and very light materials
- Calibration is not required
- Not impacted by the characteristics of a material such as the angle of repose or low dielectric constant
- Can be purchased at a low cost ($900 to $1,600)
- High-temperature models are offered up to 1000 °F
- Accurate, consistent, and repeatable measurements
- Very simple to set up and install
- Compatibility with Binventory® and BinView® software
- Minimal contact with the stored material
- Wireless communications are available to decrease installation costs
- Hazardous location approvals are available
- A range of analog and digital outputs are available
Considerations
- As it is an on-demand system, it does not supply an instant response to variations in the material level.
- If air purge is not utilized, seasonal maintenance may be necessary to clean out the mechanical cavity in very dusty environments.
- It is not designed for use in high-pressure bins.
3DLevelScanner
Acoustics-based technology is used in a 3DLevelScanner. Sound waves are delivered by three transducers at a very low frequency to the material surface. The sensor receives echoes that return from several points on the surface, which are calculated into distance measurements.
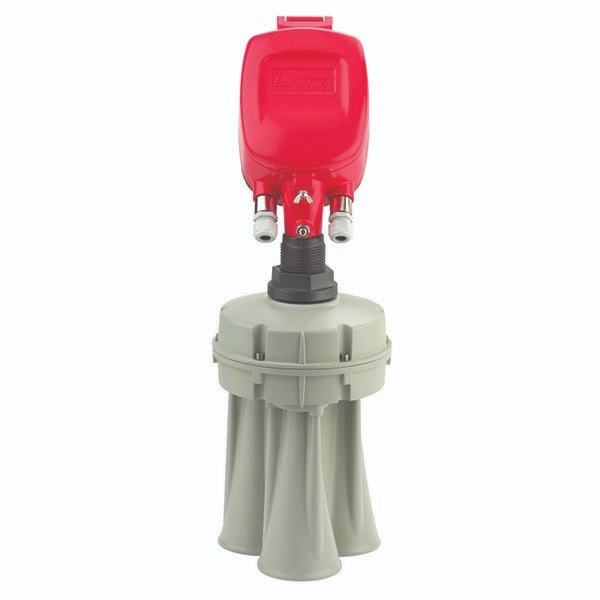
Image Credit: BinMaster
In the software, advanced algorithms assign each measurement to an XYZ coordinate which is mapped to create a 3D image. The software produces a graphical depiction of the material topography in the silo. Volume calculations account for variations in the surface.
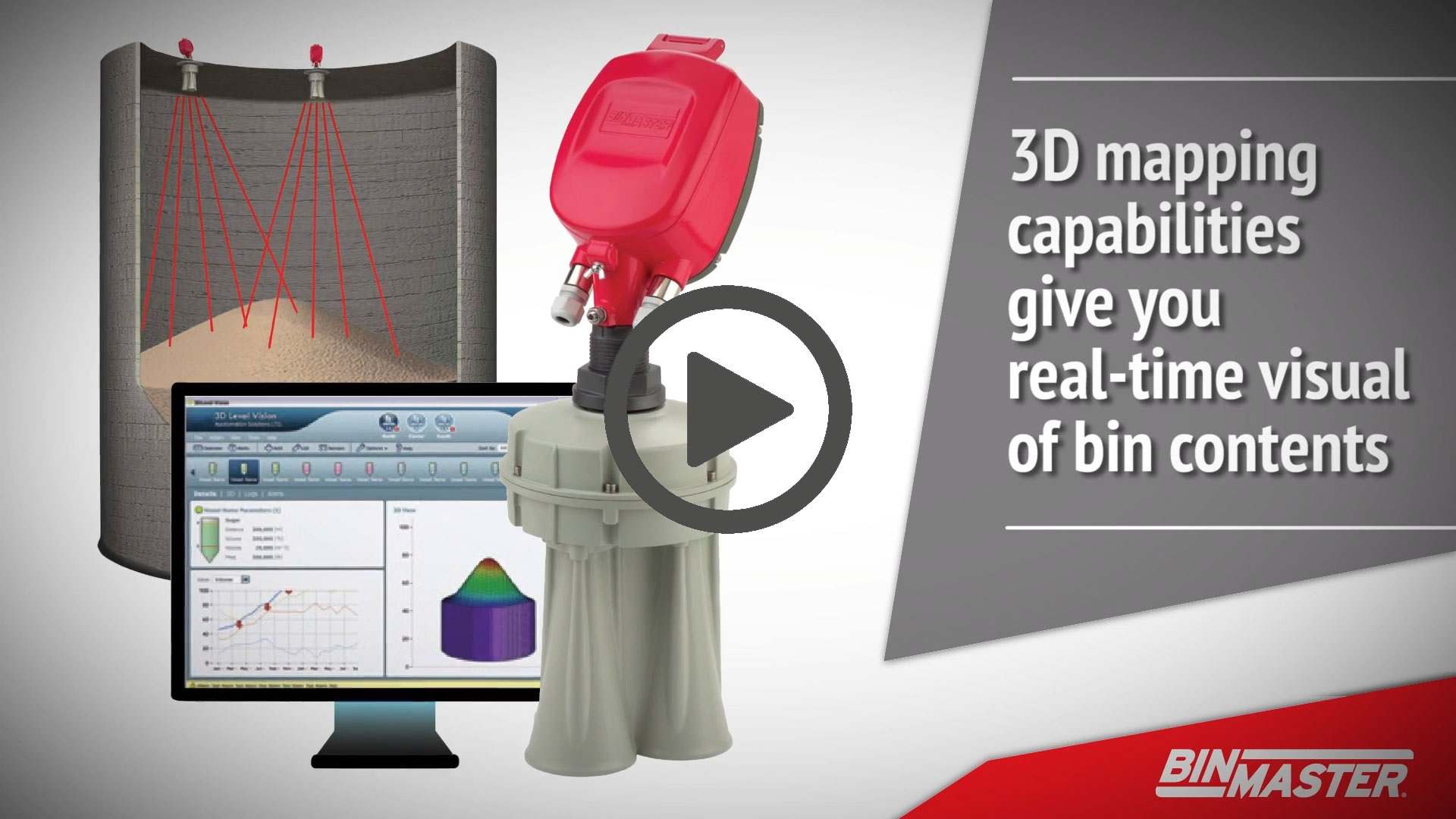
Video Credit: BinMaster
Strengths
- Non-intrusive, non-contact arrangement
- Continuous level measurement
- Identifies cone up, cone down, and sidewall buildup
- Measures irregular solid or powder material surfaces
- Performs in extreme dust levels
- Supplies maximum, minimum, and average distances
- Measures a range of up to 200 feet
- Highly accurate bin volume calculations are provided as the surface of the material is mapped with several measuring points
- High-temperature applications up to 365 °F
- Self-cleaning with minimal maintenance
- Digital and analog communications are available
- Automatically compensates for changes in temperature
- Can produce a 3D image of the material surface
- Cutting-edge 3D MultiVision networkable PC software is available to monitor multiple vessels
- Approved for hazardous locations
- Wireless interfaces are available to replace cables
- Not impacted by low dielectric constants or material characteristics
Considerations
- Care must be taken when setting up the sensor in the correct location and when mapping the vessel
- The 3DLevelScanner is an acoustic device where its performance can be influenced by high background noise
- Not recommended for liquid applications
- The time taken to process several pulse echoes limits the sample rate
- Not recommended for materials with a bulk density of less than 11 lb./cu. ft. as they may absorb the acoustic pulse
- The corrugation on small vessels can result in false echoes
Non-Contact Radar (NCR-80 Metal Jacketed)
Non-contact radar level sensors generate a narrow beam of microwaves from an antenna system through the air to the product’s surface. The surface of the product reflects the microwaves which are received back by the antenna system.

Image Credit: BinMaster
Internal electronics determine the time taken for the pulse to return to the antenna, which is known as the time of flight (TOF). The TOF is changed into a level measurement according to the vessel parameters installed into the sensor. Non-contact radars consistently quantify solids or liquids with levels taking only seconds to update.
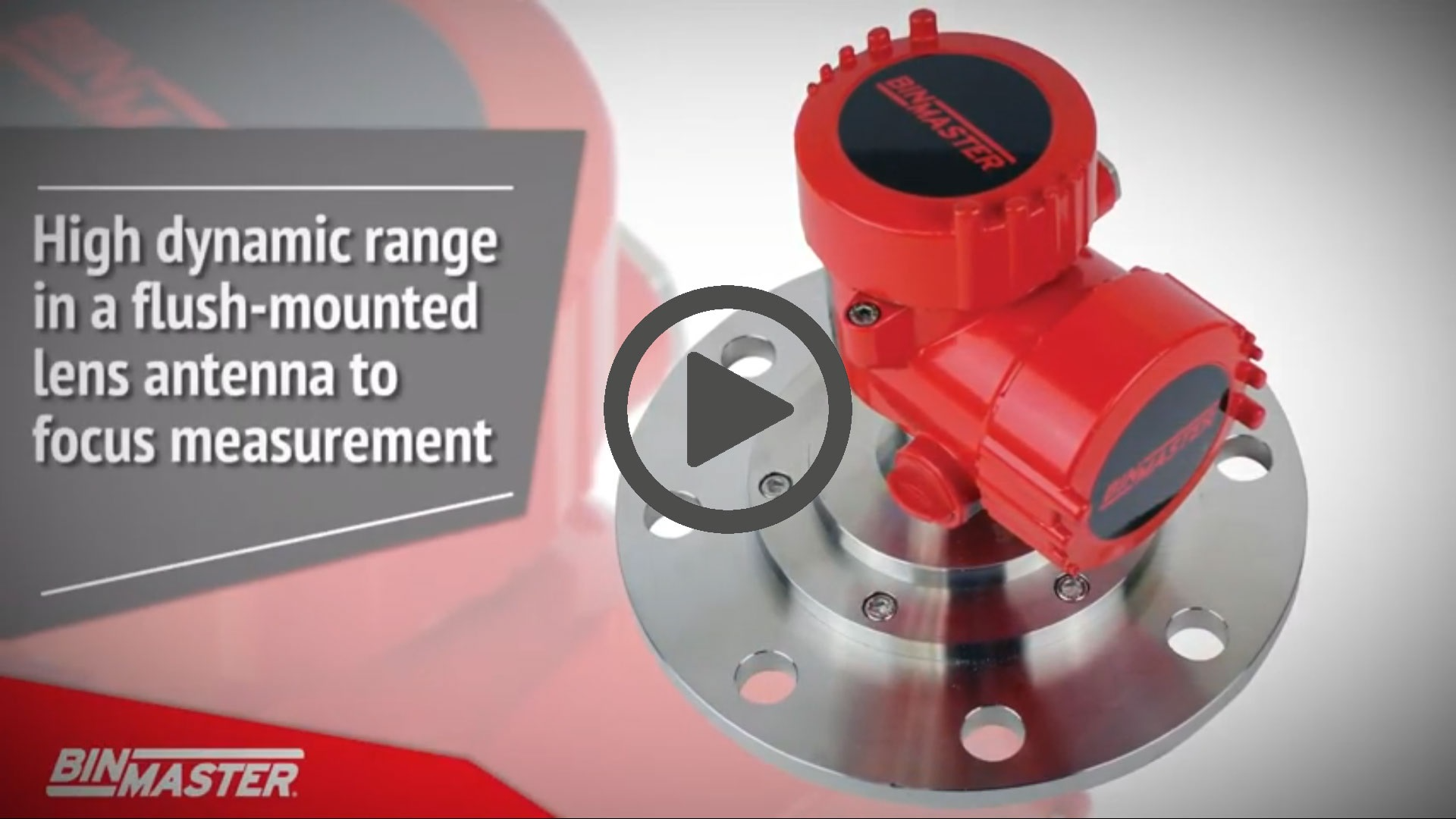
Video Credit: BinMaster
Strengths
- 4° versus 10° beam angle for higher precision
- Powerful 80 GHz radar performs more effectively than conventional 26 GHz technology
- Uses same technology employed in self-driving cars
- Significant measuring range of 393-foot
- A narrow beam can be precisely aimed to avoid structure
- Strong signal performs effectively in dust
- Versatile for use in liquids, slurries, and solids
- Efficient reaction/update time monitors emptying or filling activity
- Loop power capability
- The signal is unaffected by corrugation
- 4-20 mA and Modbus RTU communications
- Wireless communications available to decrease installation costs
- Compatibility with BinView® software
Considerations
- The minimum dielectric constant of material must be higher than 1.3
- Variations in material topography will not be accounted for in the single-point measurement
Guided Wave Radar (GWR-2000)
Time-domain reflectometry (TDR) is used in a guided microwave level transmitter to consistently measure the level of liquids or solids. A high-frequency microwave pulse is emitted by the transmitter, which is guided along a rod or cable.
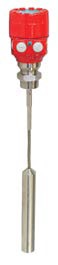
Image Credit: BinMaster
The pulse energy is reflected back along the cable to the head of the sensor when the pulse makes contact with the surface of the material. The level is determined according to the time difference between the pulse being delivered and the reflected pulse being received.
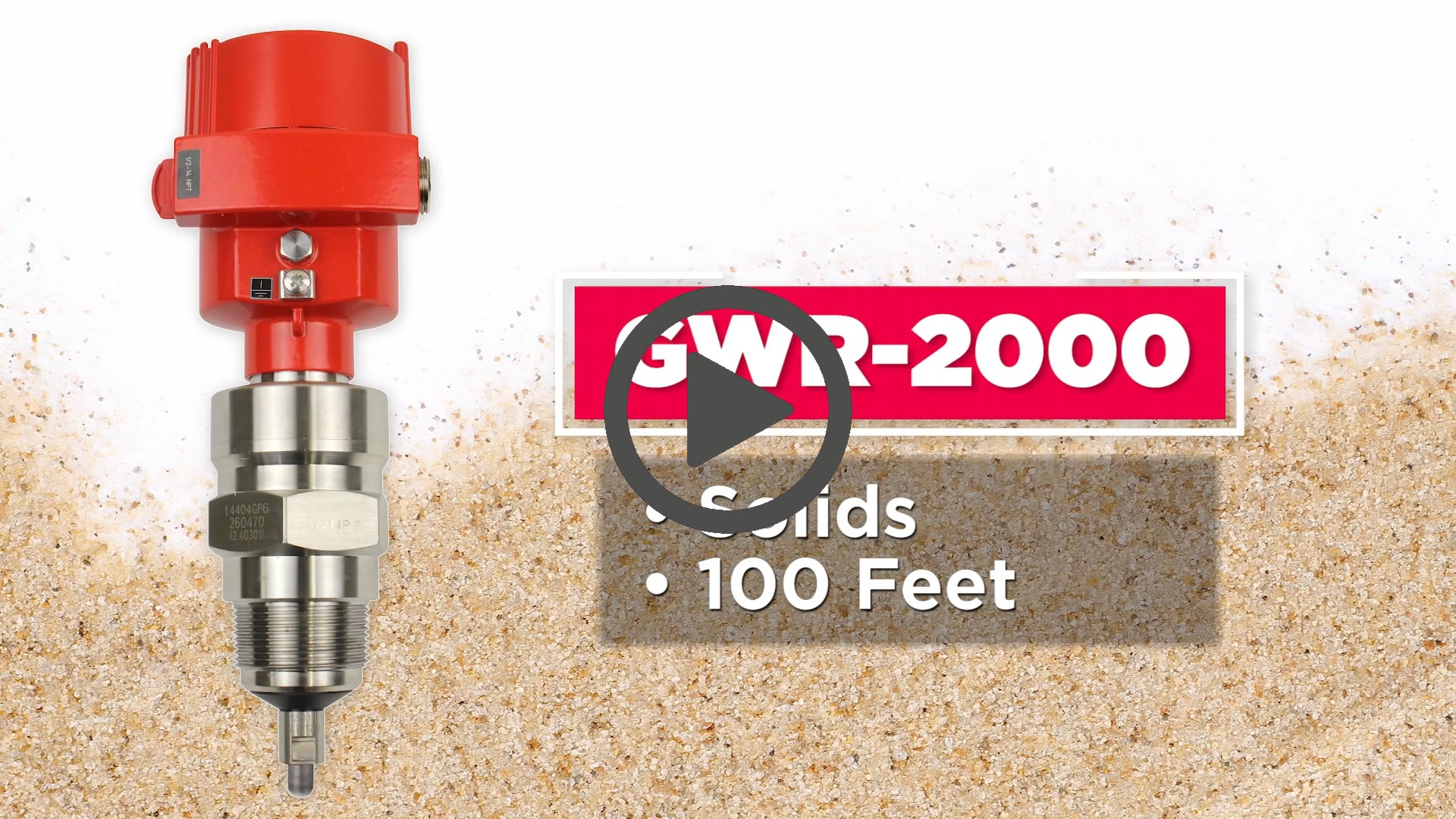
Video Credit: BinMaster
Strengths
- Measures distances of up to 75 feet for liquids and 100 feet for solids
- Offers continuous level measurement in liquids, bulk solids, granules, and powders
- Provides interface or level measurement in liquids
- Can be used for heavy or light bulk solids
- Performs in solids that are vulnerable to high dust
- 4-20 mA and Modbus RTU communications
- Can be used for vessels with almost any diameter or shape, such as standpipes or narrow tanks
- Almost no maintenance is required
- Immune to condensation
- Hazardous location approvals
- Dependable accuracy within 0.08”
- Compatibility with BinView® software
- Wireless communications are available to decrease installation costs
- Simple setup and configuration with BinDisc
Considerations
- The minimum dielectric constant of material must be higher than 1.3
- Sensing cable or rod must always be in contact with the material
- Some materials such as large rocks can damage the probe and be challenging to detect
- The maximum range for solids is restricted to 100 feet, and it may not be suitable for heavier materials due to tensile load
Lasers (SPL-200)
Laser-level measurement sensors deliver a laser beam to the surface of the material. Like a guided wave or non-contact radar, a time-of-flight calculation is used by the sensor to quantify the distance to the material.
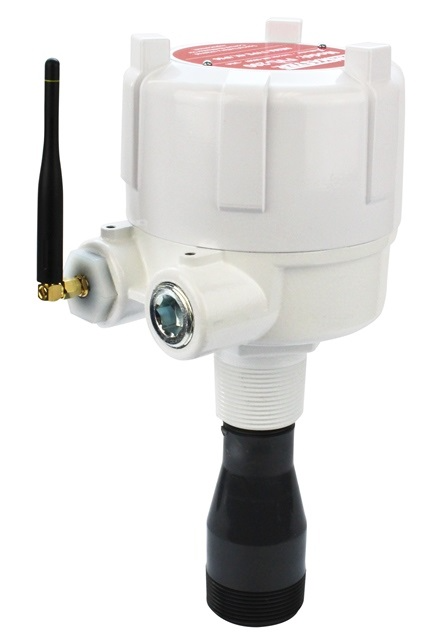
Image Credit: BinMaster
A microprocessor is integrated within the sensor that determines the distance by measuring how long it takes for the laser to travel from the transmitter to the surface and back.
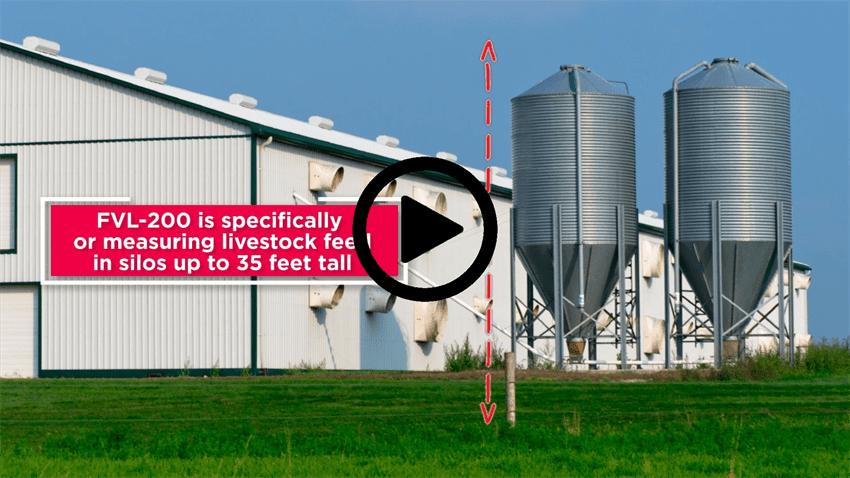
Video Credit: BinMaster
Strengths
- Accuracy of +/- 1 inch and a range up to 160 feet
- Measures in a very tight 1° beam with no beam divergence
- Suited to constrained spaces or very narrow vessels
- Can monitor during fill in low dust environments
- Structures in the vessel can be avoided through precise targeting
- Not impacted by corrugated bin walls
- Versatile for pellets, bulk solids, opaque liquids, and granular materials
- Can be used for monitoring sidewall buildup or plugged chute detection
- Not impacted by pressure or heavy vapors
- Can be used for almost any dielectric material
- Configuration can be carried out with no need to fill or empty the vessel
- The 10° mounting flange can be adjusted for precise targeting
- Dust protection is included for reduced maintenance
Considerations
- Clear liquids will be penetrated by the laser
- Single point measurement will not consider differences in the topography of the material
- Performance can be decreased by dusty environments
- Dusty environments can result in a potential build-up on the lens
Conclusion
Applying the Guidelines
Now that this article has outlined practical knowledge about the options available for silo inventory management, it is time to put this knowledge into practice. Contact a vendor with specific application needs and requirements to get the ideal system for any plant.
To learn more before getting started, watch this webinar.
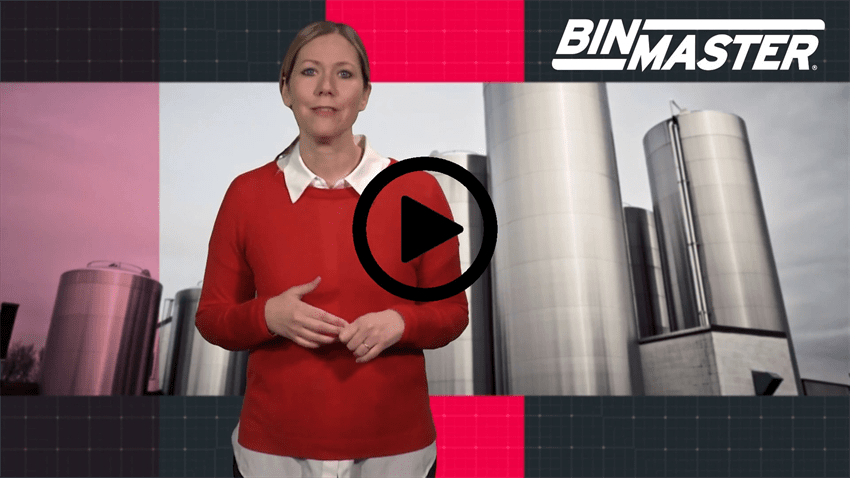
Video Credit: BinMaster

This information has been sourced, reviewed, and adapted from materials provided by BinMaster.
For more information on this source, please visit BinMaster.