A manufacturer of knife and blade sharpness testing machines is using non-contact magneto-inductive displacement sensors from Micro-Epsilon to calibrate the length and speed of the blade stroke.
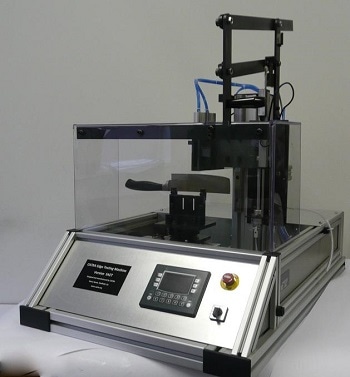
This is important as it enables the test machines to objectively compare the sharpness of various knife blades and determine which one is superior to another. The sensors were selected for their cost effectiveness, ease of set up, simplicity of use, robustness and non-contact wear-free operation.
Originally the Cutlery and Allied Trades Research Association, CATRA was established in Sheffield in 1952 to carry out research and development for the local cutlery industry. CATRA now specialises in cooperative investigations into materials, stainless steels, manufacturing methods, machinery, automation, robotics, product and performance testing.
One of the primary areas of research and development for CATRA is the sharpness testing of knives and blades. CATRA designs and builds a range of test machines for this purpose, which are supplied direct to manufacturers of knives and blades.
The CATRA TESTERS are automatic and semi-automatic knife sharpness and life testing machine that measures the sharpness and edge life (durability) of a wide range of blades and knives for quality control, R&D and competitor product evaluation. This machine is the only proprietary cutting test machine on the market that fully conforms to the International Cutting Test Standard (BS EN ISO 8442-5.2005). The lower capital cost, semi-automatic benchtop version of this machine utilises magneto-inductive sensors from Micro-Epsilon.
Testing Method
The blade is mounted in a position with the edge vertical and a pack of specially developed synthetic paper is lowered onto it. By oscillating the blade back and forth, the blade cuts into the paper, the depth of the cut being the measurement of sharpness. The test media is loaded with 5% silica, which has a mild wearing effect of the blade edge. By repeating the back and forth motion, the further cuts are made, which wears the cutting edge. The measurement of cut depth at each subsequent stroke can then be plotted to produce a wear curve for each blade tested.
Over the last two years, we’ve purchased 12 magneto-inductive sensors from Micro-Epsilon for use in our benchtop knife sharpness testing machines. We considered linear transducers [LVDTs] but these are contact sensors and so are prone to wear and are difficult to mount. We preferred the ease of set up of the magneto-inductive sensors from Micro-Epsilon as these operate on a non-contact basis, are reliable, robust and easy to use.
Simon O’Leary, Senior Development Engineer at CATRA
The mainSENSOR range of displacement sensors from Micro-Epsilon operates on the magneto-inductive measuring principle. The sensor coil is supplied with alternating current, resulting in a primary magnetic field. This magnetic field induces eddy currents in the electrically conductive material arranged opposite the coil. In the field of the eddy current sensor is a special film, which attenuates the eddy current sensor depending on the strength of the magnetic field. Using this method, a linear relationship between the distance to the magnet and the output signal can be established. As printed coils can be used inside the sensor, manufacturing does not rely on any semiconductor processes.
The sensors combine the robustness and proven measurement performance of eddy current sensor technology with the latest printed coil and permanent magnet technology. This means that customers not only benefit from having an extremely compact design relative to the measuring range, but the sensors also provide an attractive price-performance ratio for OEM applications.
Although the mainSENSOR uses a permanent magnet as the target, unlike Hall Effect sensors, it does not suffer from relatively low sensor accuracy or high temperature drift. mainSENSORs use Micro-Epsilon’s unique, patented measuring method, which is based on a linear relationship between the position of the permanent magnet and the output signal. As well as providing a simplified displacement measurement technique, mainSENSOR also offers extremely high basic sensitivity, excellent temperature stability (low thermal drift) with a maintenance- and wear-free measurement solution.
In the CATRA benchtop knife sharpness testing machine, the mainSENSOR is set up to measure the distance (and speed) of each blade stroke (max. stroke 40mm). The cutting speed is 50mm/s and a typical test time is 15 minutes for 60 cutting strokes.
As the machine is running, I am able to collect the measurement data as a complete curve. The magnet is positioned on the moving slide, whilst the sensor is fixed into position at a gap of 50mm. The voltage level tells us the distance the blade has moved for each stroke and the time taken the average velocity. It’s a simple set up that is reliable, cost effective, long life and we don’t have any mounting issues. In two years of using the sensors, we’ve had no reliability problems whatsoever.
Simon O’Leary, Senior Development Engineer at CATRA
For more information on magneto-inductive sensors from Micro-Epsilon, please call the sales department on 0151 355 6070 or email [email protected]