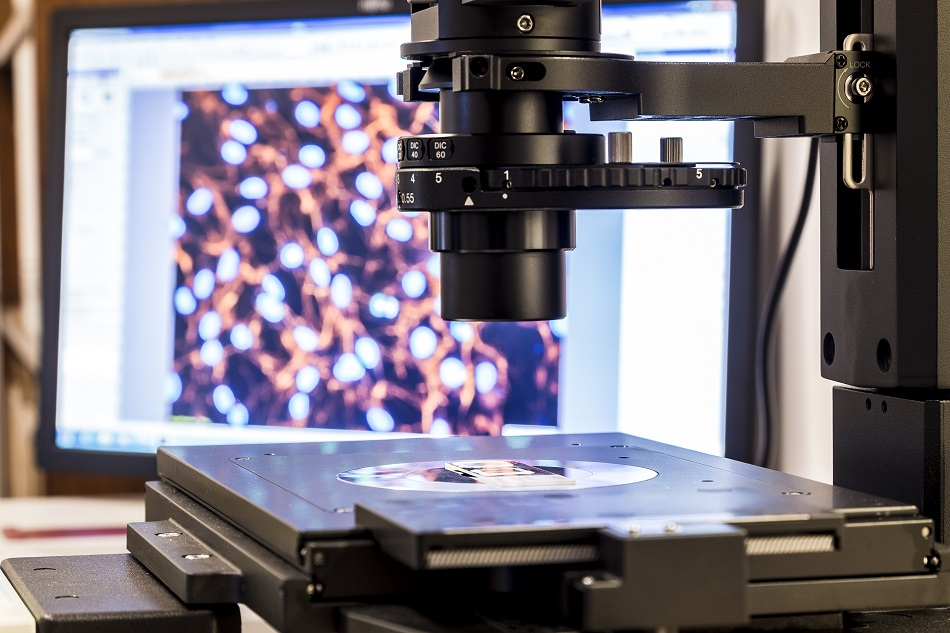
Image Credit: dominika zara/Shutterstock.com
Atomic force microscopy, also known as AFM, is a high-resolution procedure used to acquire images and other figures from a variation of materials. At the nanometer scale, effective, straightforward, and rapid sensors can be built from standard atomic force microscopy cantilevers - which are long beams fixed at a single end and used in forms of bridge construction.
Atomic force microscopy measures forces between a sharp probe and surface at a small distance, and at the nanometer scale, reveals a three-dimensional profile of the material’s surface. The probe is propped on a flexible cantilever and the AFM tip lightly grazes the surface of the material and records the minor force between the surface and probe.
How Does AFM Measure the Forces?
The device’s probe is positioned on the side of the cantilever - the amount of force between the probe and the sample is reliant upon the spring constant, which is the stiffness of the cantilever, and the distance between the sample surface and the probe. This metric can be visually transcribed using Hooke’s law: when the tip is close to the sample surface, forces between the two stimulate a deflection of the cantilever.
Usually, probes are made from silicon nitride or silicon. Varying cantilever materials and shapes generate different resonant frequencies and spring constants. Certain probes might be created with other materials for additional scanning probe microscopy applications, such as chemical force microscopy - a method that uses direct chemical functionalization of AFM probes with particular functionalities at a direct level - or magnetic force microscopy - which is a sharp magnetized tip that runs across a magnetic sample and simultaneously detects and uses these interactions to reshape the magnetic structure of the material’s surface.
How are Contact Mode Images Created?
The motions of the probe are controlled and measured using a feedback loop and an electric scanner. Piezoelectric material reacts with user-specific voltages - with the applications of different voltages, the device can reshape or deform materials, and that is how the cantilever is controlled. The process incorporates a beam bounce, in which the laser beams off the back of the cantilever and onto a position-reactive photodiode detector. These detectors usually have four quadrants and are specific light detectors used to translate light into voltage based on the device’s mode of operation.
Once the detector calculates the bending of the cantilever as the tip is scanned over the sample, a feedback loop mediates a certain position of the laser on the photodiode. Then, with the desired voltage being applied to the piezoelectric scanner, the tip is scanned over the sample by modifying or altering the cantilever position. Each picture in the image is monitored and used to form a typography map.
The feedback loop can also monitor other types of signals such as tapping mode or noncontact mode.
The Three Primary Imaging Modes in AFM
The three primary imaging modes in atomic force microscopy are contact, intermittent contact, and non-contact.
Contact atomic force microscopy stress sensors are typically at < 0.5 nm probe-surface separation. When the spring constant of the cantilever is below that of the surface, the cantilever will curve. By using feedback loops and continuing the constant cantilever deflection, the force between the probe and the sample remains stable and an image of the surface is made. Although this technique is usually quick, used in friction analysis, and accurate for rough samples, it also can damage or reshape soft samples.
Intermittent contact, or tapping mode, is usually at 0.5-2 nm probe-surface separation. This is a similar process to contact AFM, but the cantilever is swayed at its resonant frequency, with oscillation amplitudes up to 100 nm. The surface is contacted at the bottom of its swing once the probe gently taps on the sample’s surface while scanning. Once everything is maintained in the interaction, an image of the surface is made. Intermittent contact can ensure high-resolution samples that are typically vulnerable to damage, as well as provide credible biological samples. However, this specific technique tends to be more challenging when creating images of liquids.
Lastly, non-contact AFM is most often at 0.1-10 nm probe-surface separation. This method sways above the fluid layer on the surface during scanning and does not contact the sample surface. A feedback loop tracks and maintains changes in the amplitude in order to make an image. Non-contact AFM applies low force on a sample, but normally provides lower resolution and requires an ultra-high vacuum for desired imaging.
Sources and Further Reading
Disclaimer: The views expressed here are those of the author expressed in their private capacity and do not necessarily represent the views of AZoM.com Limited T/A AZoNetwork the owner and operator of this website. This disclaimer forms part of the Terms and conditions of use of this website.