Atomic Force Microscopy (AFM) is a microscopy technique within the branch of scanning probe microscopy (SPM) that is used to obtain a topographic image of a specimen at nanometer (nm) resolution1. The technique involves scanning a cantilever with a sharp tip - which appears as a tall pyramid with its end radius measuring between 15 – 40 nm - across the surface of the specimen1.
AFM can also be used to obtain measurements of local properties such as height, friction, magnetism, and even force between the probe and sample2.
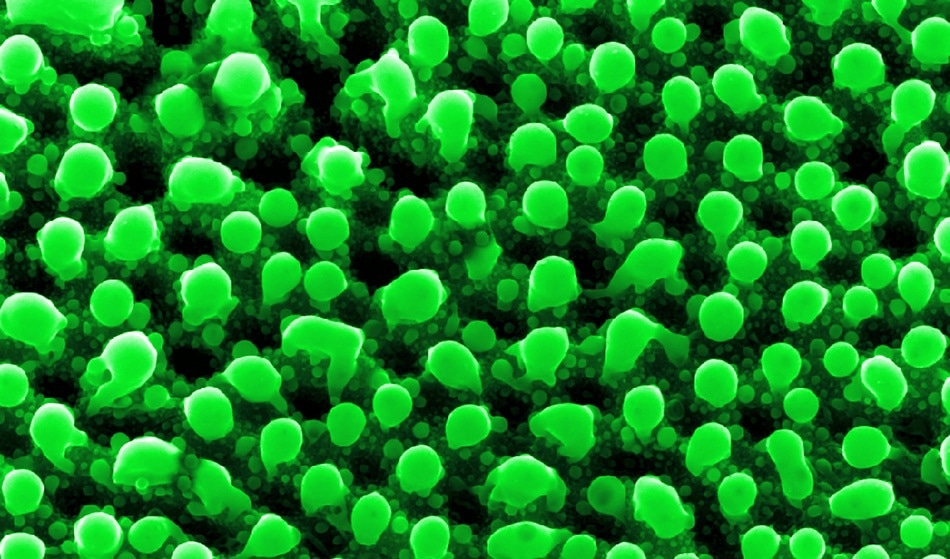
Georgy Shafeev / Shutterstock
Working Principle of AFM
The working principle of AFM begins with a laser beam focused on the top of the cantilever. The reflected laser beam is then sensed by a position sensitive detector. While the tip of the cantilever scans across the specimen, the vertical and lateral deflections of the cantilever are obtained via an optical lever.
The reflected beam then strikes at a particular point of the four-segment photo-detector2. To obtain data, the differences found between the segments of the signals acquired by the detector indicate the position of the laser spot on the detector. The angular deflections in the cantilever can therefore be sensed and quantified2.
Modification of AFM Aensors to Increase Imaging Speed and Accuracy
When present in the contact mode, an increase in the scanning speed is typically associated with compromised imaging quality3. The limited bandwidth of the AFM components often causes a number of artifacts to arise when this technique is conducted at higher scanning speeds. One of the major reasons for these artifacts is the contact loss between the tip of the cantilever and the specimen surface.
Researchers at the Vilnius Gediminas Technical University have recently developed a novel solution to this problem by applying an additional nonlinear force through the use of precisely regulated compressed gas airflow onto the upper surface of the cantilever3. This addition ensures that the tip of the cantilever remains in contact with the specimen surface throughout the full scanning duration that occurs at high scanning speeds. The results from this study demonstrated that the application of 40 Pa of air pressure onto a soft cantilever increases the scanning speeds at least 10 times3.
Self-Sensing Cantilevers
The image quality and overall signal to noise ratio can be significantly improved by using smaller cantilevers that are comprised of advanced materials, as well as by increasing the resonance frequency4. For example, Nano3Dsense technology incorporates the sensing unit directly in the cantilever, thereby eliminating the need for complicated laser optics and ultimately simplifying the AFM architecture4. As a result, this technology significantly reduces equipment size while also eliminating the hassle of calibrating the optical unit of the AFM4.
While traditional AFMs requires movement of the inert sample stage, AFMs that are equipped with self-sensing cantilevers only require the dynamic measuring head to travel across the specimen4. Piezoresistors, or laser optics failure, is a well-known dilemma when conventional AFMs are used; however, AFMs with self-sensing cantilevers are not subjected to these units, which makes these AFMs much safer alternatives4.
These advanced AFMs present several advantages when compared with traditional AFMS, some of which include: space-saving integration into Scanning Electron Microscopes (SEM); the ability to conduct the analysis of biological samples with superior imaging quality; and the incorporation of these systems into high resolution force microscopy and even various applications within the semiconductor industry4.
Despite the powerful and impressive force sensing capabilities that are maintained during difficult conditions (on both the cantilever and measuring environment), one of the most important advantages associated with the incorporation of Nano3DSense technology is that of ‘material freedom’4. Unlike traditional AFMs that are equipped with piezoresistors or laser optics, AFMs equipped with self-sensing cantilevers do not exhibit any cantilever material restrictions.
In addition to silicon (Si), a variety of materials can be used, including silicon nitride (SiN), SU8, steel and many more. Therefore, the cantilever material can be chosen based on the type of specimen (hard or soft) and the investigator’s preference in this advanced AFM with optics-free architecture4.
References
- “Atomic force microscopy” – Nature
- “Fundamental Theory of Atomic Force Microscopy” – Professor Zhong L. Wang’s Nano Research Group
- Dzedzickis, A., Bucinskas, V., Virzonis, D., Sesok, N., Ulcinas, A., Iljin, I., et al. (2018). Modification of the AFM sensor by a precisely regulated air stream to increase imaging
- “Ultra-Small Force Sensors for Atomic Force Microscopy (AFM)” – Nanoscale Systems GmbH
Disclaimer: The views expressed here are those of the author expressed in their private capacity and do not necessarily represent the views of AZoM.com Limited T/A AZoNetwork the owner and operator of this website. This disclaimer forms part of the Terms and conditions of use of this website.