Smart pumping applications are intentionally designed to modify the speed of a pump to offset fluctuating process conditions or plant requirements.
To achieve this, adjustable speed drives are typically used to control pump speed; smart valves to control flow; pump controllers ranging from on-board microprocessors to PLCs, PACs and DCSes and — of course — smart instruments.
For instrumentation, a smart pumping system (Figure 1) requires flow, temperature and pressure devices that are accurate, dependable, able to identify any process conditions that may cause problems and anticipate when maintenance is needed.
Several instrument providers manufacture various types of “smart instruments,” and their approaches may differ. This article explains how Endress+Hauser flow sensors with Heartbeat Technology offer the kind of information required for the implementation of smart pumping.
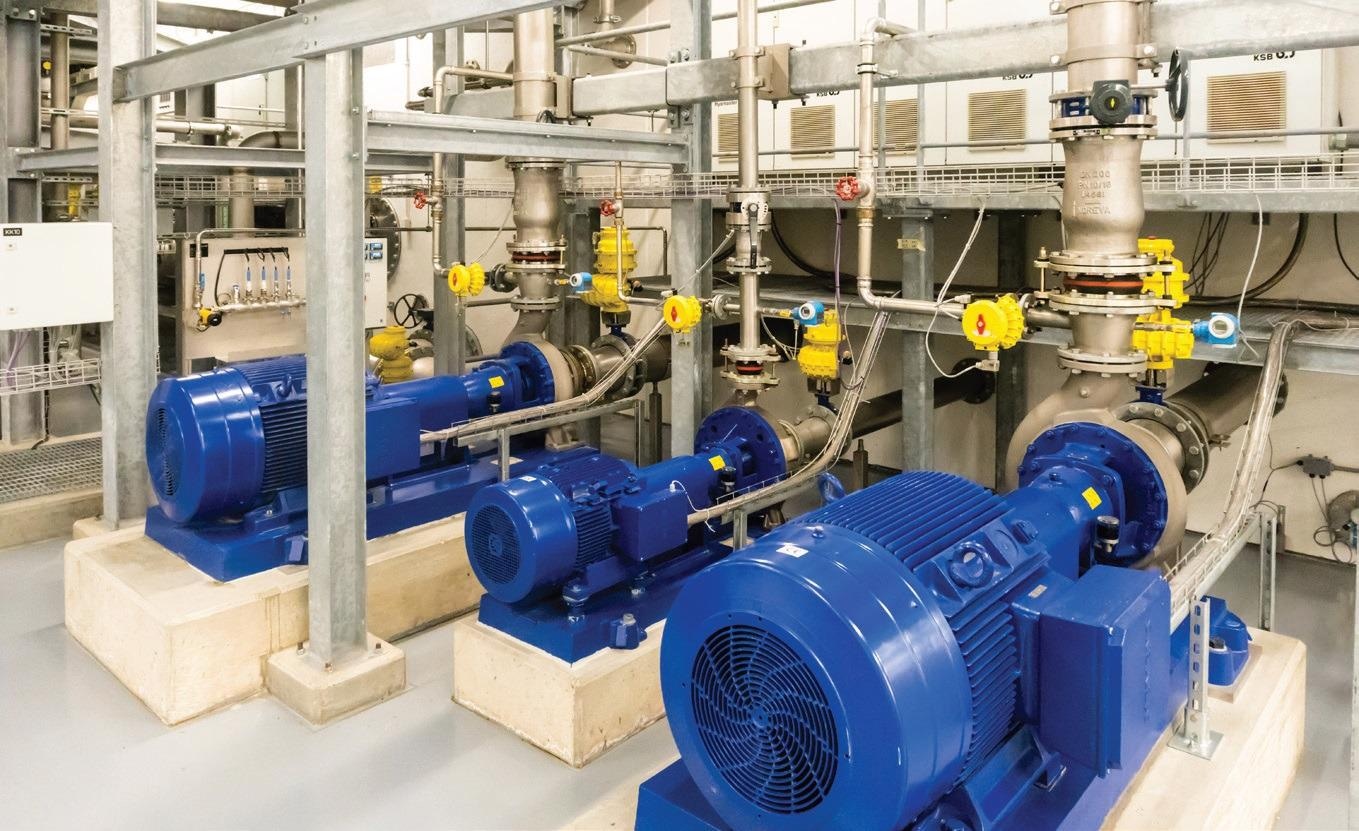
Figure 1. With smart pumping, cascading pumps from large reservoirs ensure required flow rates are achieved reliably and efficiently based on system demand. Image Credit: Endress+Hauser Ltd.
What is a Smart Instrument?
Smart instruments can provide an automation system with a considerable amount of information in contrast to conventional instruments, which only offer a 4-20 mA output proportional to the process variable.
A ‘smart’ flow transmitter, for example, usually provides a flow signal and a range of status and diagnostic information. A Coriolis flowmeter not only transmits a flow signal, but it can also send data on temperature, mass, density or even viscosity.
This data is usually transmitted via fieldbus or a 4-20 mA signal with HART.
Several instruments take the smart concept one step further. Not only do they transmit a signal for flow or pressure with diagnostic information, their internal electronics continuously monitor process and device health to provide convenient information with suggested remedies as and when problems occur.
In pumping applications, these instruments do not inform operators if there is a problem with a pump; rather, it detects conditions that can lead to pump problems. For instance, the Endress+Hauser Proline flowmeter can detect entrained air, corrosion, coating, vibration (which could be caused by pump cavitation) and inhomogeneous or unsuitable media.
These could all could impact the pump and its performance. The flowmeter can also diagnose itself with electronic or subcomponent problems. When the appropriate process conditions are in place (Figure 2), the flowmeter will transmit an event message.
Table 1. Typical errors that can be generated by a Proline flowmeter, which can detect up to 125 different problems. Source: Endress+Hauser Ltd.
Error code |
Error |
Actions |
Alarm type |
843 |
Process limit |
Check process conditions |
Alarm |
962 |
Partially filled pipe |
Check for gas in process
Adjust detection limits |
Warning |
910 |
Tubes not oscillating |
Check input configuration
Check external device
or process conditions |
Alarm |
912 |
Medium inhomogeneous |
Check process condition
Increase system pressure |
Warning |
913 |
Medium unsuitable |
Check process conditions
Check sensor |
Alarm |
948 |
Oscillation damping too high |
Check process conditions |
Warning |
The diagnostics and error reporting are achieved via Endress+Hauser’s built-in Heartbeat Technology. No external software is necessary. While each manufacturer’s instrument diagnostics vary, each tends to monitor internal parameters, track changes and diagnose problems.
For instance, Proline Coriolis flowmeters can monitor oscillation damping and frequency, signal asymmetry, temperature, carrier pipe temperature, exciter current, frequency fluctuation and other parameters. Changes in these parameters may signal potential problems.
For example, a variation in the frequency fluctuation is a signal of rapidly changing process conditions such as gas present in a liquid fluid, while drift in oscillation damping can be the result of the formation of coating or buildup — or by corrosion, fouling or abrasion.
Heartbeat Technology can also produce a Heartbeat Sensor Integrity (HBSI) parameter using Heartbeat Verification. This parameter constitutes the relative change of the entire sensor, with all its mechanical, electrical and electromechanical components.
The reference HBSI is set when the flowmeter is calibrated at the factory. Any fluctuations that occur between the calculated HBSI and the reference HBSI signals a change in the sensor.
This can be caused by increased mechanical or thermal strain on the sensor, excessive wear from corrosion or abrasion, multi-phase fluids, wet gases, the formation of buildup in the measuring tube or other conditions.
Whenever a deviation occurs in the HBSI, built-in intelligence investigates changes in all the parameters, identifies the likely cause and sounds an alarm or warning message to the operator.
A Proline flowmeter has a variety of outputs — including 4-20 mA with HART, EtherNet/IP and PROFINET— and Proline 300 and 500 devices can also have a WLAN enabled display. The pump control system can acquire monitoring information, Heartbeat diagnostics and alarm messages via any desired communication protocol.
Additionally, operators or maintenance technicians can view the diagnostics on the meter’s display or on their laptop, smartphone or tablet across the WLAN connection.
Minimizing Maintenance
Smart pumping systems are dependent on precise data from flow transmitters, so each instrument must have the capacity to detect when it is in need of recalibration or verification. In some industries, such as water recovery, it is necessary to verify flowmeters at regular intervals.
Verification must be conducted by a qualified third party with an approved inspection method based on quality regulations such as ISO 9001, and a test report needs to be supplied for documented proof of evidence.
Verification can be performed in the field as a manual process with a verification tool and a simulation box. Throughout the field verification process, the transmitter is exposed to the atmosphere, and the meter cannot be used to measure and control the process for the duration of the test.
External verification must be conducted by a trained technician, and the verification tool itself is categorized as test equipment in accordance with ISO 9001, which means that it must undergo periodic traceable calibration.
Some plants do not possess the capacity to verify a flowmeter manually or do not want to shut the pumping system (Figure 3) down to achieve it. If a plant doesn’t have internal capacity, a third-party firm must be hired to validate the meter, or the meter must be removed from service and sent to an offsite calibration facility.

Figure 2. This smart pumping application in UV disinfection uses smart instruments to monitor flow control and pump speed to ensure water is passing through the system at precise rates to guarantee quality. Image Credit: Endress+Hauser Ltd.
Modern flowmeters have built-in verification into the device itself, so verification does not need a skilled technician, instrument extraction or a process shutdown. For instance, Proline flowmeters from Endress+Hauser have built-in self-verification that can be triggered from the pump control system at any time.
During flowmeter verification, the existing conditions of various parameters are compared with their reference values, thereby revealing the device status. Heartbeat Technology generates a “pass” or a “fail” statement based on the tests carried out by traceable and redundant internal references.
The individual tests and test results are recorded automatically in the flowmeter and used to print a verification report. A traceable and redundant reference, held in the verification system of the device, is utilized to ensure the reliability of the results. In the case of an electromagnetic flowmeter, this is a voltage reference, which offers a second, independent reference value.
As with the Proline flowmeters, integrated self-monitoring supersedes the necessity for external test equipment only if it is based on factory traceable and redundant references.
The reliability and independence of the testing method are safeguarded by traceable calibration of the factory references and by the constant monitoring of the flowmeter’s long-term stability throughout the product’s lifecycle.
The verification process for Endress+Hauser flowmeters usually takes less than five minutes. Suppose the flowmeter has a permanent Ethernet or other digital bus connection to the pump control system. In that case, the procedure can be carried out from a distance using a PC located in the maintenance department or the plant’s control room or from the control system.
If the verification procedure establishes that the flowmeter requires maintenance or recalibration, Heartbeat Technology alerts the plant operators.
Summary
Smart instruments guarantee that reliable, accurate data is provided to a smart pumping system on a consistent basis. When problems crop up during the process or in the instrument itself, the smart instrument alerts the pumping system controller and offers the necessary advice.
Moreover, with automatic self-verification, the plant will be aware of when an instrument needs to be extracted for maintenance or recalibration and can stay in compliance with regulations. All this guarantees reliable operation and minimal maintenance.
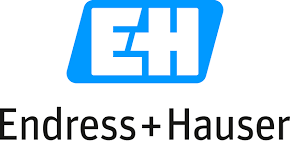
This information has been sourced, reviewed and adapted from materials provided by Endress+Hauser Ltd.
For more information on this source, please visit Endress+Hauser Ltd.