Aug 21 2012
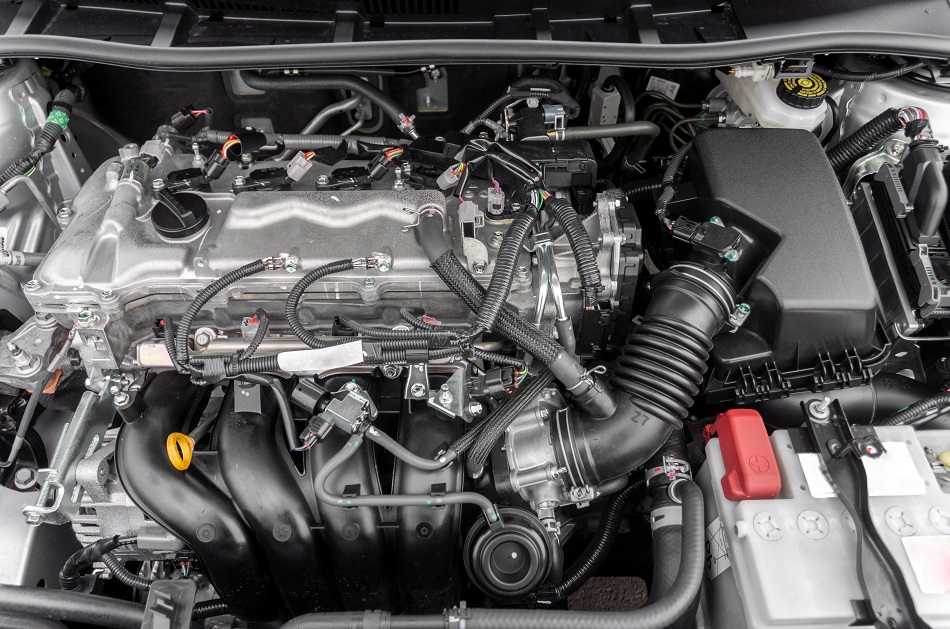
Image Credit: SvedOliver/Shutterstock.com
You’ll often experience a forward shift in the weight of a car during hard braking. Without a proportioning valve sensor, the shift in weight that unloads the rear axle can cause the rear car wheels to lock, potentially spinning the vehicle out of control.
So, when braking, it is obvious that the driver will be exerting a proportional amount of pressure to the braking system to stop the car. This applied pressure is controlled by a proportioning valve, which works to control the actual pressure applied to the rear brakes.
The idea of an internal car component being able to balance the front and rear pressure to a moving vehicle was introduced in the late 1960s. Early designs of a standard proportioning valve, including disc and drum brakes, are still used in some modern automobiles.
The proportioning valve operation was designed to be specific to front disc, rear drum components. Later car designs with four-wheel disc brakes have been introduced with proportioning valves for each of the rear disc brakes.
Automotive design and engineering will continue to work on creating the most efficient braking system where there is a balance in the friction coefficient between all four tires to a vehicle. With the imbalance in the front and rear wheel pressure is the reason for using a proportional valve, this component still only serves as one way to adjust the balance.
The disc front and drum rear is the main combination that will benefit from a proportioning valve. It is worth noting that disc brakes fixed to the front of a vehicle can achieve around 70% of the stopping force without overheating. Drum brakes have less directional stability, so with lighter vehicles, there is less of a difference between the disc rears and drum rears.
Overall Structure
A standard proportioning valve system is part of a large combustion valve structure that can be sectioned into three individual parts: the metering valve, the pressure differential valve, and the proportioning valve. Each section is bridged by a master cylinder.
There is an inlet passage from the master cylinder at one side of the valve and a rear brake passage protruding at the opposite end of the positioning valve. A proportioning piston sits in a stepped bore inside the valve, and the stepped bore is also connected to a valve stem. It is the valve stem that carries out the proportioning to a braking system – the stem moves inside the bore via the spring-loaded piston (see video below to understand the structural components of a proportioning combination valve for braking systems, its functions, use, and importance).
Master Power Brakes Combination Valve Video
Functional Principle
The following video animates the internal structure of a positioning valve and how this works to help introduce proportioning valve operation in a car brake system.
Brake regulator valve. Depending on the load.
By adjusting the braking force, the positioning system can allow the vehicle to control the load transfer. During regular braking in a moving vehicle, the spring-loaded piston is normally in a relaxed position. The poppet valve to this system is held in position with a spring which allows the fluid to travel through the main valve into the rear car brake system.
Now, imagine slamming on your brakes to stop the car immediately in its tracks – the pressure applied to allow for heavy braking causes the outlet pressure to rise in the positioning valve, which creates an imbalance in the force between the two areas of the spring-loaded piston and moves the piston against a pressure spring. This movement of the piston against the pressure spring limits the amount of pressure delivered to the rear brakes by closing the valve stem. Thus, more pressure is applied to the front disc brakes and less pressure is applied to the drum brakes.
Car manufacturers will continue to make vehicle braking systems safer and more efficient. BMW has tested the active hazard braking concept to explore ways to avoid rear-end collisions. The research team has tested the use of a proximity warning system that can preload the brakes and activate these brakes as an alert to a possible collision in their new research prototype (see video). This new initiative demonstrates how car manufacturers are looking for ways to integrate the brake system with additional safety components in a vehicle.
BMW X5 Active Hazard Braking
Sources and Further Reading
- Owen, C.E. (2004). Shop Manual for Automotive Brake Systems. USA, New York: Thomas Delmar Learning.
- Gilles, T. (2005). Automotive Chassis: Brakes, Suspension, and Steering. USA, New York: Thomas Delmar Learning.
This article was updated on 13th February, 2020.