In this article, First Sensor’s LDE differential pressure (Δp) sensors are experimentally compared to other manufacturers’ sensors based on the same (thermal-anemometer-based, non-membrane) sensing principle, where differential pressure is inferred from a gas flow via the sensor. In the case of high-humidity environments, all other sensors with flow impedances ranging between 15 Pa/(ml/s) and 300 Pa/ (ml/s) either failed completely or went out of calibration, whereas the LDE sensors with a flow impedance of >10 kPa/(ml/s) were able to retain their calibrated sensitivity. The LDE/LME/LMI Δp sensors from First Sensor need only small flows through their body and thus provide excellent immunity to humid environments.
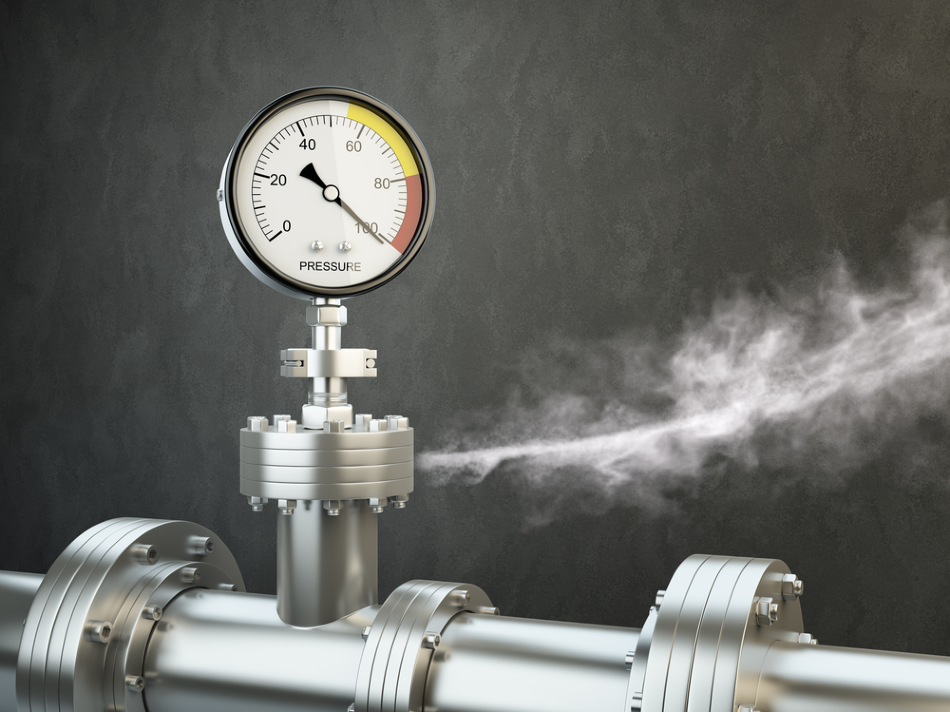
Image Credit: Shutterstock/tridland
Flow-Through Leakage
Due to the sensing mechanism, nonzero air flow leakage occurs through the sensor itself. This holds true for all differential pressure sensors based on the thermal-anemometer sensing principle, (compared to dead-end sensors such as piezo-resistive membrane-based sensors, whose sensing element does not leak at all). Regardless of this fact, thermal-anemometer-based Δp sensors continue to have substantial success in the marketplace, because they allow cost-effective and practical sensing of extremely low Δp, such as a few hundred Pa full-scale and below. The question that emerges at this point is how much flow-through leakage is too much? The answer relies on application details and the way the Δp sensor is coupled and used.
The Δp sensor can measure differential gas pressures below a few hundred Pa, and with resolution better than 0.1 Pa. As a result they may be influenced by other parts of the measurement system such as connecting tubes/pipes and filters, and by the quality of the gas which may possibly include liquid droplets, dust or humidity.
There are some manufacturers of thermal-anemometer-based Δp sensors who propose the use of connection tubes with a specific length, so as to ensure that the response of the manufacturer-calibrated sensors is not distorted in any way. They may also use dust-segregation mechanisms/elements as part of their sensors, or also propose the use of dust filters.
In order to provide reliable long-term operation, designers of a flow-measurement system, using a thermal-anemometer-based differential pressure sensor, should consider a number of factors caused by non-zero gas flow via the sensor. However, no standard test/certification processes are available and no detailed technical information is there to address these problems. Thermal-anemometer-based sensors from various manufacturers were used to perform the following tests. These tests were done to show how the flow-through leakage (flow impedance or pneumatic impedance) of the sensors enables reliable operation in practical applications. It must be remembered that such precautions are not necessary for membrane-type sensors, where there is zero gas flow via the connection tubing (in static mode).
Note: The sensor’s pneumatic impedance Rpn, which is calculated in [kPa/(ml/s)], determines the flow of gas through the sensor at a certain pressure drop, Δps across the sensor:
Flow-through leakage = Δps /Rpn
Flow Measurement Using Differential Pressure Sensors
Normally, micro-flow-based differential pressure sensors are used to determine the differential pressure produced by the gas flowing through a “flow tube” or air-flow duct. Some examples include respiratory flow measurement in medical ventilators and filter control or air flow measurement in HVAC applications.
For instance, consider the sensor used in a shunt configuration to detect differential pressure Δp = p1 – p2 across a flow-restrictive element in an air duct, thus inferring measurement of air flow in the duct (Figure 1). These conversion elements are developed for various applications and include baffles, orifices, calibrated diaphragms, Venturi tubes, Pitot tubes and specialized flow-to-pressure converters that are used in respiration equipment such as Lilly or Fleisch tubes.
The differential pressure sensors, LDE/LME/LMI, are characterized by extremely high flow-through impedance, which is up to hundreds of kPa/(ml/s) for higher full-scale ranges and higher than 10 kPa per (ml/s) for the most-sensitive models. When compared to other sensors with lower flow impedance, differential pressure sensors with high flow impedance require less parasitic flow to make a measurement and hence, cause fewer disturbances to the main flow. This makes the latter almost equivalent to dead-end type or membrane-type differential pressure sensors with regard to this critical aspect of performance for many different applications.
.jpg)
Figure 1. Typical volumetric flow measurement set-up with differential pressure sensor. Image Credit: First Sensor
Risk from High-Humidity Environments
In certain applications, the main gas flow is warmer than the ambient temperature and contains significant humidity. This is common for applications such as medical respiration measurement, where humidified air is exhaled by the patient. This air is usually at a temperature higher than the temperature of the measuring equipment or the ambient room temperature. In such scenarios, water may condense from the gas flow on the inner walls of the gas flow ducts or from connectors, connecting tubes and other elements.
Although fine condensed water droplets may not be affected by gravity, the small water droplets form larger water drops by joining together which then form larger water accumulations. This may take place in the sensor, or in the main gas flow path, in the connectors and tubes to the sensor. These water accumulations can either obstruct (or block completely) a connection tube or connector, or alter the pneumatic properties of the measurement system, thereby defeating or degrading the measurement system.
While the presence of high humidity poses an operational/reliability hazard, the level of the hazard is mainly determined by the flow-through impedance (pneumatic impedance) of the sensor.
Experimental Investigation of Effects of High-Humidity
Comparative experimental studies were carried out to examine the risk posed by high humidity. The experimental set-up was designed and developed to provide controllable and reproducible conditions for the tested sensors and also to enable a fair comparative analysis of a wide range of sensors. Keeping this target in mind, sets of Δp sensors based on the thermal-anemometer sensing principle were exposed to applied differential pressures. In all the experiments, two or more sensor samples, usually having different flow impedances, were linked in parallel to make sure that all sensors have a common differential pressure.
Experimental Set-up
Figure 2 shows the set-up which was designed and developed to provide reproducible near 100% humidity in a test volume within a plastic tube with a 2 cm inner diameter. A typical household warm steam vaporizer was used to feed the test volume and the other end of this main tube was joined to the air blower via a flow-restrictive element. Another (narrower) plastic tube serves as the flow restrictive element with a length of approximately 5 cm and an inner diameter of 1/16 inch. Also, a water collector was linked between the flow-restrictive element and the test volume to prevent water blockage of the flow-restrictive element. With a volume of 1.5 L, the water collector had a much larger inner diameter than that of the test volume, which was joined to a single port of each sensor.
The design was intended to maintain the pressure in the test volume very close to the ambient atmospheric pressure, while slowly pulling humidified air from the vaporizer into the test volume. The temperature of the humidified air directly at the output of the vaporizer was approximately 90 oC, which was considered to be too high to imitate normal operation of the sensors. As a result, the test volume was located about 25 cm from the vaporizer output. Two NTC thermistors monitored temperatures T1 (at the input to the test volume) and T2 (at the other end of the test volume) within the test volume. The air flow produced by the air blower controls the temperature distribution across the test volume. When this air blower is turned off, the test volume temperature becomes close to room temperature.
.jpg)
Figure 2. Schematic diagram of experimental setup. Image Credit: First Sensor
Test #1
In the first test, all the four sensors identified above were linked to the test volume, with each sensor using 10 cm of 1/8 inch ID plastic tubing. Figure 3 shows the sensor output signals measured during the test.
.jpg)
Figure 3. Sensor output signals during Test #1. Image Credit: First Sensor
During the entire test, the pressure Δp applied to the sensors was kept at a constant level of about 230 Pa. The air blower and the vaporizer were turned on for about 30 minutes before connecting the tested sensors. This time delay was intentionally made to produce a warm, humid environment in the test volume. The sensors with their connection hoses (10 cm, as explained above) were then linked to the test volume. Instantly (within 30 seconds from the time of connection of the sensors), traces of water condensation (Figure 4) can be seen within the connection tube to Sensor 2-1, which possesses the lowest pneumatic impedance among the four sensors. Sensor 2-1 was the one that lost proper function the earliest. After about 1 minute, it showed a quick decrease in its output signal while the green line, indicating the membrane-type pressure sensor, displayed a relatively constant applied pressure. After about another minute of irregular output voltage behavior, Sensor 2-1’s output voltage reduced considerably from ~120 mV to ~0 mV, induced by visible blockage or obstruction of its connection tube by the accumulation of water.
When Sensor 2-1 was obstructed, air temperature in the test volume decreased suddenly (Figure 3), in addition to a short spike in the measured air pressure, as the feedback circuit of the air blower adjusted the air flow. Moreover, Sensor 1-1 lost proper function rapidly after about 4 minutes. The output voltage of Sensor 1-1 reduced to zero, again owing to visible obstruction of its lower tube connector by the accumulation of water (see left-most tube in Figure 5).
Figure 5 was photographed toward the end of Test #1. The two rightmost tubes linked to the LDE sensors — LDES050UF6S and LDES250UF6S — did not show any visible traces of water and also there was no condensation within the LDE tubes during the entire ~55-minute test. During the ~55 minutes of the test, there was no degradation in the output signal of the LDES250UF6S sensor. The output of the LDES050UF6S sensor was saturated as the applied pressure Δp surpassed its operating range of 50 Pa.
.jpg)
Figure 4. Connecting tube of sensor 2-1 ~30 s after start of Test #1. Image Credit: First Sensor
.jpg)
Figure 5. Connecting tubes ~10 min after start of Test #1. Image Credit: First Sensor
Test #2
The second test was set up in such a way that sensor 1-1 had an advantage while the LDE sensors were handicapped. Sensor 1-1 was linked to the test volume with wider 1/4” ID tubing (double the earlier ID of 1/8”), whereas the LDE sensors were positioned closer to the test volume at a distance of 3 cm rather than 10 cm, using the same 1/8” ID tubing used earlier. In Test #2, Sensor 2-1 was not tested.
The wider 1/4” ID connection tubing for Sensor 1-1 was meant to make it less susceptible to obstruction by water accumulation, because of a wider cross-section close to the connector which can collect a higher amount of condensed water without becoming blocked. Figure 6 shows the output signals of the sensors measured during Test #2. Figure 7 depicts photos, which show the process of clogging of 1/4” tubing.
It was no wonder that Sensor 1-1 operated for a longer time in Test #2 than in Test #1, prior to complete clogging of the connecting tube. The connection tube to Sensor 1-1 got blocked about 60 minutes after the beginning of Test #2. Several partial and temporary reductions of the output signal of Sensor 1-1 also occurred (at constant applied differential pressure). These were seen at ~20 minutes and ~40 minutes, as shown in Figure 6. Such partial reductions are due to partial restriction/clogging of the flow passage, either within the sensor’s flow channel assembly or close to the connection to the test volume. As there is a continual flow of air via the sensor, such restriction can be “cleaned out”, which would explain the transitory reduction and subsequent restoration of the output signal to the original (unrestricted) level of about 2 V.
Similar to Test #1, no sign of significant obstruction or degradation was shown by the two LDE sensors (Figure 6) through more than 2 hours of operation with 3 cm-long 1/8” ID connection tubing.
.jpg)
Figure 6. Sensor output signals during Test #2. Image Credit: First Sensor
.jpg)
Figure 7. Process of clogging of 1/4” tubing of sensor 1-1 in Test #2. Image Credit: First Sensor
Discussion
These tests prove the significance of high pneumatic impedance of the micro-flow sensors, for consistent operation in systems where the flow rate of warm, humid air has to be determined.
In both Tests #1 and #2, the LDE sensors were deliberately linked to the hottest spots in the test volume and were then subjected to air containing the highest concentration of moisture, with the greatest potential for considerable condensation. Still, there were no traces of water condensation within the connections to the LDE sensors in 1 to 2 hours of operation at constant differential pressure of 230 Pa applied across both sensors, which continually measured properly.
Additionally, in Test #2, the LDE sensors were linked at a shorter distance of 3 cm from the test volume. Both LDE sensors continued their normal function, whereas Sensor 1-1 was prevented from making its intended pressure measurements due to an accumulation of water in its connecting tube.
Tests #1 and #2 described above demonstrate systematic differences in performance and function, related to differences in the sensors’ pneumatic impedance. If the pneumatic impedance of the shunted sensor is not sufficiently high, the sensor’s function will need substantial air flow via the sensor. However, when there is substantial moisture-bearing air flowing to the sensor, the connections and tubing to that sensor may have significant water condensation. If the connections encourage or allow water buildup, the system may develop potential blockage, which will lead to loss of function.
In addition to those systematic differences, it must be remembered that during the test, large drops of water will condense from the main gas-flow onto the walls of the test volume, as shown in Figure 5. Such water drops tend to agglomerate and/or displace themselves due to surface tension or gravity, to accidentally block any connector, thus possibly disrupting the operation of any type of sensor linked to the main flow path. While this did not happen in the experiments illustrated herein, this accidental effect may occur with all types of differential pressure thermal-anemometer-type or sensor membrane-type, irrespective of pneumatic impedance. For each specific application, the designer of the flow path and measurement system is responsible for protecting the flow and measurement system against this type of accidental water clogging.
Conclusion
In the case of differential pressure sensors that use the thermal-anemometer sensing principle, which involves intentional non-zero leakage through the airflow channel of the sensor, the flow-impedance of that airflow channel is a vital factor to establish the sensor’s immunity to condensation – that is induced blockages and functional failure.
With high humidity in the air flow, First Sensor’s LDE sensors with flow impedance >10 kPa/(ml/s) were directly compared with two other manufacturers’ sensors that are based on the same sensing principle, but have a relatively lower flow impedance, 15 Pa/(ml/s) to 300 Pa/ (ml/s). In all instances, the sensors with lower flow impedance lost calibration and/or failed entirely following =1 hour of normal operation. No degradation or blockage was shown by the LDE sensors. The high flow impedance lowers the volume of humidity-bearing air which can reach the sensor’s input, which in turn, reduces the amount of available moisture to condense and possibly block or restrict pneumatic connections.
The less air flow the sensor needs through its body to make a measurement, the more suitable the behavior of the sensor, and the better the immunity to humidity-bearing air. First Sensor’s LDE/LME/LMI differential pressure sensors provide high flow impedance and thus significant benefits.
Potential users of thermal-anemometer-based Δp sensors can repeat the same or similar humidity tests to validate suitability for use within the conditions of their own specific application(s).

This information has been sourced, reviewed and adapted from materials provided by First Sensor AG.
For more information on this source, please visit First Sensor AG.