Level measurement in containers and storage tanks plays an important role in many different processes, but before purchasing any equipment Plant Operators should consider the type of sensor that meets their specific application needs.
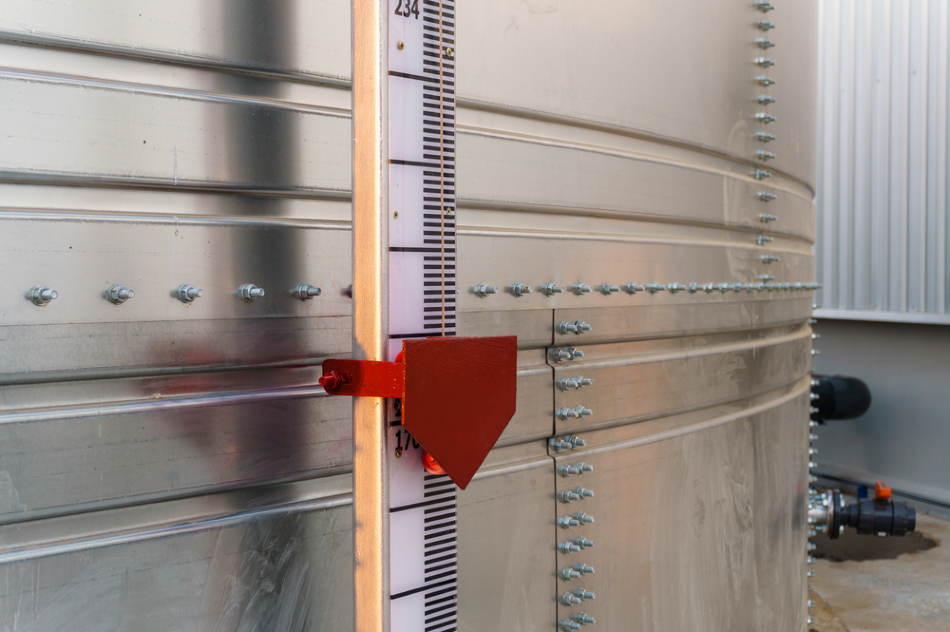
Image Credit: Shutterstock/Yuthtana artkla
Level sensor technology covers a broad range of options from optoelectronic to hydrostatic sensors, but then not all sensor systems can be used for every application or job. Also, development support and customization are some of the determining decision factors for Development Engineers and System Designers. There are many methods of level measurement, but defining which method is most suitable for a given application depends on the type of measurement required (limit or continuous value), the medium being measured, demands for interfaces and data transfer and also on the budget. Also, the characteristics of each application can differ widely, from powdery, aggressive or sterile media to fluids or foam with varying densities and extra challenges, for instance.
Another factor that needs to be taken into account is the kind of tank where the sensor will be ultimately installed. The material of the tank/container, geometry, size and any current tank installations such as agitators are key elements which affect the appropriate selection of sensors.
Hydrostatic Level Sensors
A hydrostatic sensor is generally installed as a dip probe directly above the body of water or the bottom of the container and measures the pressure of the liquid column, thus determining the fluid level. Based on the device, the measurement data is conveyed as digital or analog signals in a continuous measurement.
A hydrostatic pressure is generated by a fluid column at the bottom of a reservoir or tank which is a function of the liquid’s height and density. The hydrostatic pressure can be measured by a pressure sensor, and the liquid level can be established following calibration to the specific density of the process media. Gage pressure sensors measure relative to atmospheric pressure. These sensors are used in open container or vented tank applications to prevent false results caused by barometric pressure fluctuations. In the case of pressurized tanks, it is important to measure the difference between the gas pressure above the liquid surface and the pressure at the bottom of the tank. This can be accomplished by one differential pressure sensor or two individual gage pressure transmitters.
With the help of a cable, dip probes can be directly lowered into the media from the top of the tank. Hydrostatic level sensors are rugged and highly resistant to aggressive and corrosive liquids, because the sensor housings may be made from either plastic or stainless steel. Leading Manufacturers provide the right type of housing for every pressure, media and temperature range, along with a choice of sensor cables.
Other sensing options can also be included in hydrostatic level transmitters. For example, dip probes are provided on roof tanks installed on skyscrapers. These probes measure rainwater levels and at the same time take temperature measurements.
When the water in the cisterns falls below a minimum temperature, freezing is prevented through heating. First Sensor developed and implemented this combined solution to meet the specific needs of customers. Hydrostatic level sensors are also used in applications such as the condition monitoring of dykes for coastal protection or the balancing of ballast tanks in ships.
However, hydrostatic dip probes can only be used on a limited basis. For example, submersible sensors cannot be used when an agitator is operating. Here, if the application enables a hole to be drilled, then a threaded hydrostatic pressure transmitter can be mounted to the base of the tank via the wall.
.jpg)
Optoelectronic Level Switch
Optoelectronic level switches provide a simple and low-cost solution for many level measurement applications. A light receiver (phototransistor) and a light source (LED) are included in the sensors. In gas or air, the light generated from the LED is reflected back to the phototransistor in the sensor tip by total internal reflection. When the tip of the sensor is surrounded by liquid, light is refracted into the liquid and a weaker signal approaches the phototransistor, which, in turn, actuates a switching output.
Optoelectronic level sensors are compact, easy to install and can be employed in a wide range of applications. First Sensor and other Manufacturers also provide different housing options for ease of installation and optimal media compatibility.
Point level sensors with plastic polysulfone housings can be used in a variety of OEM applications, such as HVAC, medical equipment, hydraulic reservoirs, compressors, leak detection, machine tools as well as pharmaceutical, food and beverage processing. Trogamid plastic housings can also be used with a wide range of liquids which cannot be used with conventional polysulfone housings, such as halogenated hydrocarbons (e.g. chloroform), acetone, methanol, ethyl acetate and fuel. In addition, Trogamid is approved for direct contact with drinking water and food.
.jpg)
Customization and Development Support
Standard level sensors can also be bought as catalog items. Yet, the situation looks entirely different if customer or application-specific solutions are required to acquire the requested quality, accuracy or ease of integration. Also, customization begins with basic mechanical modification of threads, cables or connectors, but even in these cases catalog distributors reach their limits. Electrical connection to the customers’ systems is another major aspect. If the appropriate output signal, interface, or data format is provided by the sensor manufacturer, the design phase can be shortened and development costs can be saved.
Valuable development support is also provided by premium sensor Manufacturers. Experienced sensor experts provide their expertise in sensor systems and applications to the client’s development teams. This can be performed in a sub-project or in a joint development project in accordance with functional specifications.
In this fashion, customers will not only benefit from the Manufacturer’s know-how in the areas of self-test functions, integrated designs, remote measurement and microcontroller programming, but can also gain considerable competitive advantages. Another aspect that is particularly valuable to customers is the sensor Manufacturer’s expertise with the long term stability and accuracy of the measurement solution, as they do not have to develop this understanding which would be a costly and time consuming process.

This information has been sourced, reviewed and adapted from materials provided by First Sensor AG.
For more information on this source, please visit First Sensor AG.