Originally developed in the 1960s, mass flow devices are important components in systems that generate the specialty gas standards required for the calibration of a wide variety of gas analysis instruments. Mass flow devices create a signal that is directly proportional to the mass flow of a gas.
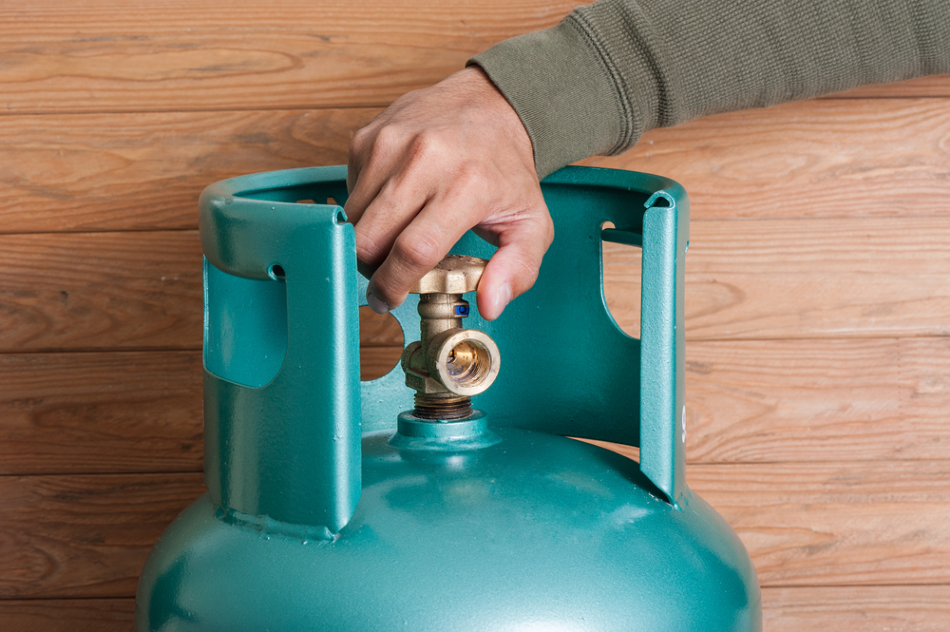
Image Credit: Shutterstock/Nor Gal
The specific heat of a gas is unique to every gas, therefore mass flow devices are essentially independent of any potential fluctuations in temperature and/or pressure of a sample. It can therefore be determined that the signal generated by mass flow devices is both highly stable and accurate.
If the signal from a mass flow device is used to determine flow, it is denoted as a Mass Flow Meter (MFM), whereas if the signal from a mass flow device is used along with a controlling valve and a reference signal, it is grouped as a Mass Flow Controller (MFC).
When a number of MFC’s are electronically controlled within specified tight limits and operated in parallel with each other, the resultant gas mixtures are highly accurate according to the basic principle of a filling technique known as ‘Dynamic Blending.’
Dynamic Blending
Lead-time and price are two important considerations that must be made when a certified gas mixture is ordered from a calibration gas producer, as these factors can influence the calibration magnitude of the analytical instrument. When the urgency and volume are critical considerations to be made in order to meet the specified calibration needs, the purchase of a dynamic gas blender may be more cost-effective than purchasing the calibration gas.
As compared to other types of systems that create calibration standards, dynamic gas blenders are capable of quickly producing the end product at a lower cost and higher accuracy in most situations. Some dynamic gas blenders that are used to create mixtures for the calibration of ambient air pollutant monitors are also capable of creating precise ozone levels that can be subsequently utilized for the calibration of various nitrogen oxides (NOx) and ambient ozone monitors that require gas phase titration with ozone.
Numerous factors have the potential to impact the overall accuracy of an MFC-based dynamic gas blender, of which can range from the initial choice of the MFC, to the care taken by the end-user in operating and sustaining the equipment.
Qualifying and Selecting a Mass Flow Controller for a Dynamic Gas Blender
The flow sensor is one of the most important components of a mass flow controller, similar to the way in which the MFC is a significant part of a high accuracy gas blender. Thermal mass flow controllers are the most common and standard method that are used to control and measuring mass flow, as this type of device can measure the temperature shift (or differential) that occurs in a small tube as heat transfers to and from the gas.
When choosing an MFC for a gas blender, the sensor data provided by the manufacturer should be reviewed to ensure that it includes long-term repeatability and stability. To ensure that no potential inherent flaws are present within the gas blender, manufacturers are required to provide any relevant research data on the type of sensor being used.
The calibration of flow controllers should be performed along with the process gas that will be analyzed, however this is not always possible. If the process gas cannot be employed for calibration, a surrogate gas can be used as an alternative, during which a conversion factor (K) is applied to ensure the accuracy of the flow through the MFC in regards to the process gas.
.jpg)
Figure 1. A thermal mass flow sensor. As gas flows through the sensor tube, it collects heat when it enters the tube and transfers some amount of heat back to the tube as it exits. Two independent temperature sensors, TC1 and TC2, measure the temperature differential in the tube. The sensors generate electrical signal that is amplified and converted into a linearized signal that is generally recognized by instrumentation. Image Credit: Environics
It is necessary for the manufacturer of the dynamic gas blender to confirm that the MFC device supplier has committed an adequate time for the proper development and evaluation of the K-factors, which should ideally be derived empirically, for all the gases that will be employed while using the blender.
The most critical step that a gas blender manufacturer involves is the choice of the MFC that will be used to assess one set of MFC’s over a period of several months from each qualifying manufacturer. The most important characteristics to be analyzed during this process involve the stability, repeatability, as well as the short and long term drift.
.jpg)
Figure 2. A partial list of the K-factors provided by the company HFC-202, as well as the methods employed to derive them.
Note: A “K” factor is defined as the ratio of the actual gas flow rate to the equivalent nitrogen flow rate. To obtain the equivalent nitrogen flow rate, divide the actual gas flow rate by the K factor. Image Credit: Environics
.jpg)
Figure 3. An evaluation spanning seven months. On the day of each test, the MFC was flow-tested, using a primary flow standard at four points, throughout the full scale range; 10 repeatability points were taken at all four major flow rates to establish the average repeatability of each test. Image Credit: Environics
Developing and Manufacturing an Accurate Dynamic Gas Blender
The use of a highly accurate MFC is just one aspect of the process required to develop an accurate gas blender, whereas a second aspect involves the ability of the company to develop the controls and software involved in validating the accuracy chain. If the MFC’s that are controlled through an analog voltage are used, a minimum of 12-bit ADC and DAC should be incorporated into the design of the instrument.
It is also important that the accuracy of the precision reference voltage is also directly applied to these devices. With a resolution of 12-bit, increments of 0.0012 VDC are applied to the MFC to obtain precision control.
Additionally, the MFC’s and the equipment should both be CE certified to ensure that the instrument will not be vulnerable to electrical interference. The system should also be designed using MFC’s, 316 SS electro-polished tubing and fittings. Alternate seal and tubing materials may also be compatible with different types of gases. A considerable amount of money can be saved through proper selection of these various components.
The development of the software used to control a gas blender must be primarily interested in improving the MFC specifications, as some blender manufacturers that use thermal mass flow controller have been notorious for installing an MFC as it was received from the manufacturer without performing any additional calibration.
If users depend on the accuracy of an MFC manufacturer’s specifications without conducting their own validation processes, it is possible that their gas blender will exhibit faulty specifications. A good gas blender manufacturer will always utilize a calibration standards lab to verify the factory specifications of an MFC.
Double Check the Flow Standard
An accurate flow-measuring instrument with a specification of 0.2% of reading or more should be used to calibrate each MFC that is installed in a gas blender. A minimum of 11 calibration readings should be collected on the flow standard to obtain the highest and most accurate results with a gas blender. The calibration data should then be entered into the gas calibrator software for future use as a reference table.
Following this, a flow-correcting algorithm, such as a linear interpolation model, should be applied by the blender software to enhance the linearity and accuracy of the MFC’s. The gas blender should be equipped an option that allows the entire gas path to be purged with an inert gas. The same principle should be applied to K-factor correction.
After an MFC manufacturer is chosen, the blender control software should use the manufacturer’s library of K-factors to make the appropriate corrections as alternate gases are employed.
.jpg)
Figure 4. The Model 2000 application of K-factor correction. This mode allows the operator to enter the gas types being fed into the MFC’s and equipment’s input ports. The software features a built-in standard that allows it to automatically compare the process gas to the original calibration gas for each MFC installed (up to 9 MFC’s). For all the gases corresponding to the calibration gas of the MFC, the system automatically calculates and applies the K-factor. This figure also illustrates three component gases in a nitrogen balance. Image Credit: Environics
The Responsibility of the End User to Maintain the Accuracy Chain
The end-user and owner of the gas blender are both responsible for maintaining accuracy of the instrument, as this aspect of the device is critical for ensuring that any input gases that are fed into the gas blender are clean and free from moisture. Most anhydrous gases are inert and therefore are unaffected by the standard materials used in a gas blender, however, when in the presence of moisture, these gases can become corrosive.
Additionally, contamination is also a concern, as the potential of contaminants to be carried downstream into the MFC sensor and completely disable the device. Contamination on the sensor tube walls can also reduce the effectiveness of the heat transfer between the sensor tube and gas, which can ultimately lead to the blocking of the tube’s small inner diameter and subsequent failure of the blender. It is important to determine that all gas ports are capped when they are not in use to ensure that all particulates, moisture and other airborne contaminants do not enter the system plumbing.
Cylinders with 100% pure gases should be used if possible, as a pre-mixed gas that is not properly handled or checked can introduce contaminants to the blender and subsequent errors in the gas blending system that cannot be offset by a dynamic gas blender. If a premixed gas must be used, certified cylinders should be used for instrument calibration procedures, especially in situations where the regulations or guidelines of the blender mandate it.
The most critical responsibility of the end-user is to follow all manufacturer-prescribed calibration and maintenance precautions provided for the specified equipment. In situations where the manufacturer’s regulations and guidelines do not mandate calibration of the gas blender to create the calibration mixture, the dynamic blender should be calibrated at least once a year. Following all these basic guidelines will guarantee an accurate and long life of an MFC-based dynamic gas blender.
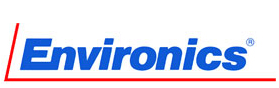
This information has been sourced, reviewed and adapted from materials provided by Environics, Inc.
For more information on this source, please visit Environics, Inc.