Can you introduce yourself and your role at Tekscan?
My name is Raul Oreste. I have more than twelve years of experience spanning business development, product management, and engineering across diverse sectors, from aerospace to manufacturing. As a Product Manager at Tekscan, my focus is on working with our customers to understand their applications and craft a roadmap for new products that cater to their surface sensing requirements.
What is pressure mapping?
A Pressure mapping system measures the interface pressure between two surfaces. Tekscan has developed a measurement solution that is comprised of three components: an ultra-thin sensor, scanning electronics, and a software analysis tool.
The first part of the system is the pressure mapping sensor, made of polymer sheets with a conductive layer printed on each side.
When there is no load on the sensor, those two resistive materials touch each other but have very high resistance. When the sensor is not being pressed, that resistance is very high. As you add force, the resistance goes down. That difference in resistance correlates the pressure measurement.
The sensor is a very dimensionally stable printed circuit which can be loaded up to 6000 PSI, and can fit in tight areas due to its small size and thin profile. The sensor provides a distribution map that is connected to the electronics, the second part of the pressure mapping system. The electronics gather information from each sensor point where the resistive materials cross. The distribution map represents how the pressure is being applied to that surface or the contact you are making against the sensor.
After the electronics gets the data from the sensor, the pressure mapping software creates a visual representation for analysis.
All the electrical signals from the sensor create a digital image, a distribution map. You can manipulate this data by recording it, creating playbacks, and creating static, dynamic measures.
This is the essence of our pressure mapping technology.
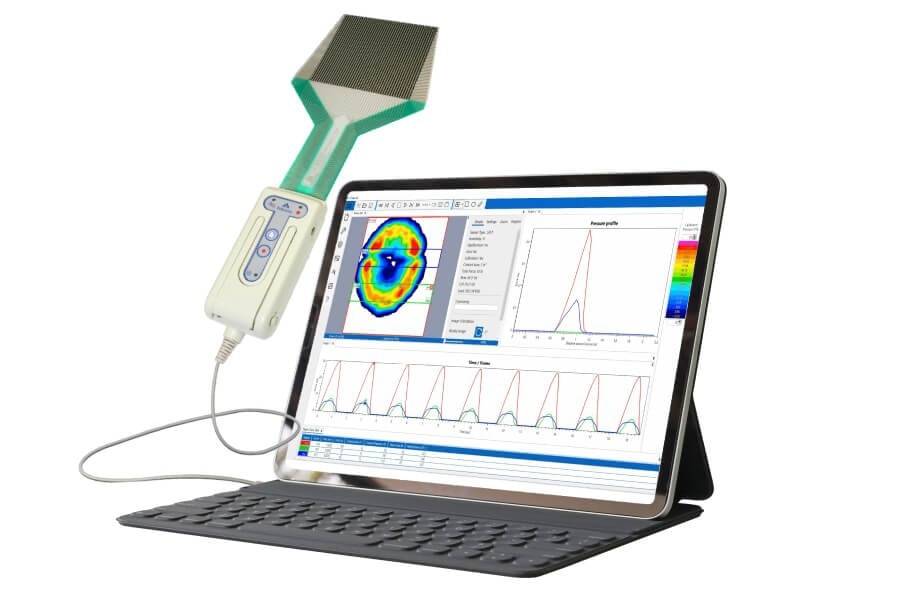
Tekscan’s I-Scan™ Pressure Mapping System
How can Tekscan technology be used to characterize battery pressure with pressure mapping?
The electric vehicle (EV) industry faces battery performance optimization challenges. Engineers are working to optimize batteries for safety, longer-term stability, energy density, and charging time.
Getting the charging speed as quick as possible is one of the most significant challenges. You want it to be comparable to fueling a car. And all engineering improvements need to be manufacturable as well as cost-efficient.
All these requirements conflict with each other. A better charging time affects durability, safety, size, and capacity. For example, if you have a battery with a higher energy density, it will be small and have a higher charge capacity, but it will be more prone to thermal and safety issues.
All this applies to both established and emerging battery technologies: lithium-ion batteries and solid-state batteries. Both types of design can make use of pressure mapping.
Lithium-ion batteries use liquid electrolytes. One key parameter of battery assembly is the stack pressure, which is applied to each cell when putting it on a housing. If that stack pressure is below the optimum level, it can allow too much expansion, leading to thermal runaway or premature failure during cycling.
On the other hand, if it is higher than desired, the stack pressure can harm overall battery performance and damage internal components. Getting to a point where you find the correct pressure in this battery pack is essential.
Deterioration occurs in both solid-state batteries and lithium-ion batteries. In lithium-ion batteries, the battery tends to breathe: there is expansion and contraction as the battery goes through charging and discharging cycles.
In the case of the solid-state battery, you have a solid electrolyte. This will not expand as much as the liquid electrolyte in lithium-ion but will crack if the pressure gets too high. Pressure monitoring allows us to prevent issues caused by expansion in lithium-ion batteries and cracks in solid-state batteries.
How have you validated the use of pressure mapping in batteries?
Pressure mapping can locate pressure on batteries with both liquid and solid electrolytes.
To validate this, we analyzed published studies characterizing the impact of pressure during charging and discharging cycles.
A 2014 study from the University of Princeton measured stack pressure, simulating a fixture of a battery pouch and a cell battery.
The researchers in the study used a load cell to measure the force the battery pouch was exerting as it was charging and discharging; they could see the force but nothing else. As it was charging, the force was increasing, but no more information was available.
By adding a Tekscan sensor to the fixture, the researchers measured the force and load distribution of the battery pouch when charging and discharging. They were able to identify local peaks of pressure in the stack from small defects in the manufacturing process of the cells.
Cells in which extreme local pressure areas were observed were found to degrade faster than those with relatively uniform pressure distributions. The higher the pressure, the faster the degradation, which is an interesting insight.
Pressure mapping and battery lifecycle testing are minimally invasive. Pressure mapping identifies high points of pressure by using the distribution of sensors across the area. The sensors are very thin, flexible, and non-intrusive, allowing them to be added to any test fixture. You can add them between the pouches and measure pressures in a stack, an individual pouch, or an individual cell.
When testing pressure mapping and battery lifecycle testing, one of our engineers at Tekscan built a fixture.
We used the VersaTek electronics with the dual-handle 1526 pressure mapping sensor and a battery pouch. We placed this battery pouch with a steel plate over the sensor.
The first thing that showed up in the software when fixing the fasteners was the spike in pressure in the middle of the battery immediately after pressing. It was understood that a compliant material was needed between the pouch and sensor to equalize or distribute pressures better. Spiking did not occur because of the rigid plate material against the sensor.
The engineer put the compliant material between the battery and the sensor and fixed everything again. He tightened the fixture’s fasteners and observed the growing pressures.
We carried out a test, starting cycles of charge and discharge, looking at different factors like the gradient of pressure across the surface in a moment in time or total force versus time. This would match what you read in the load cell.
We can get a visual representation of pressure distribution to see how the pressures are presented in the exercise. We then get the results of the charging and discharging cycle and view it. We can see that as it discharges, all the forces go down, and the pressure eases, and as it charges, pressures go up.
The central pressure remains relatively uniform, with more pressure in the middle. The pressure tends to relax about halfway through the charge and discharge process. It is not a constant increase in pressure. This could be due to the chemical composition or something in the battery, evening out pressure distribution.
These are fascinating insights that users would not see with other invasive tools.
You can also recognize unusual pressure regions, perhaps the Teflon or the battery connector creating excessive pressure, that could be avoided using a different design. We can also graph how the battery fluctuates between expanding and contracting.
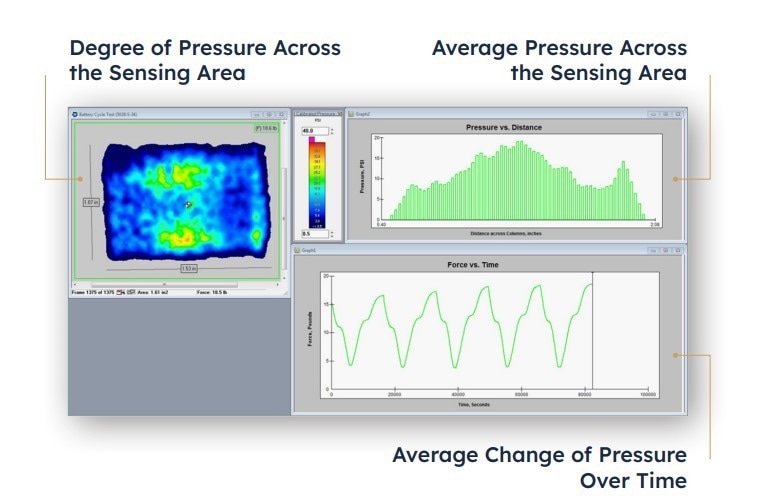
Measuring Battery Pressure with Tekscan Pressure Mapping Technology
How can pressure mapping be used beyond R&D?
I have talked about R&D so far and how pressure mapping could help in R&D applications, but at Tekscan, we are discovering applications beyond R&D.
It could be very valuable, for example, in quality control in manufacturing. Monitoring the evenness of pressure during the formation process has been shown to reduce dendrite formation and improve product quality.
It is possible to design a small embedded Tekscan sensor inside the fixture. This can provide data on the battery management system in a feedback loop, so you can constantly monitor the battery to know if it is overcharged.
If one cell is getting too much pressure compared to the other, how is it discharging on that particular application? You can monitor that pressure stack over time to get an indicator of battery health and potential safety issues.
It is not just batteries that make up the potential of Tekscan technology. The car manufacturing industry is going through changes, and pressure mapping could potentially drive the design of electric vehicles.
We have tons of information on vehicle design as we have been working with the automotive industry for many years. All the information we have, and everything we have been doing with the sensor, has been applied to create a better electric vehicle.
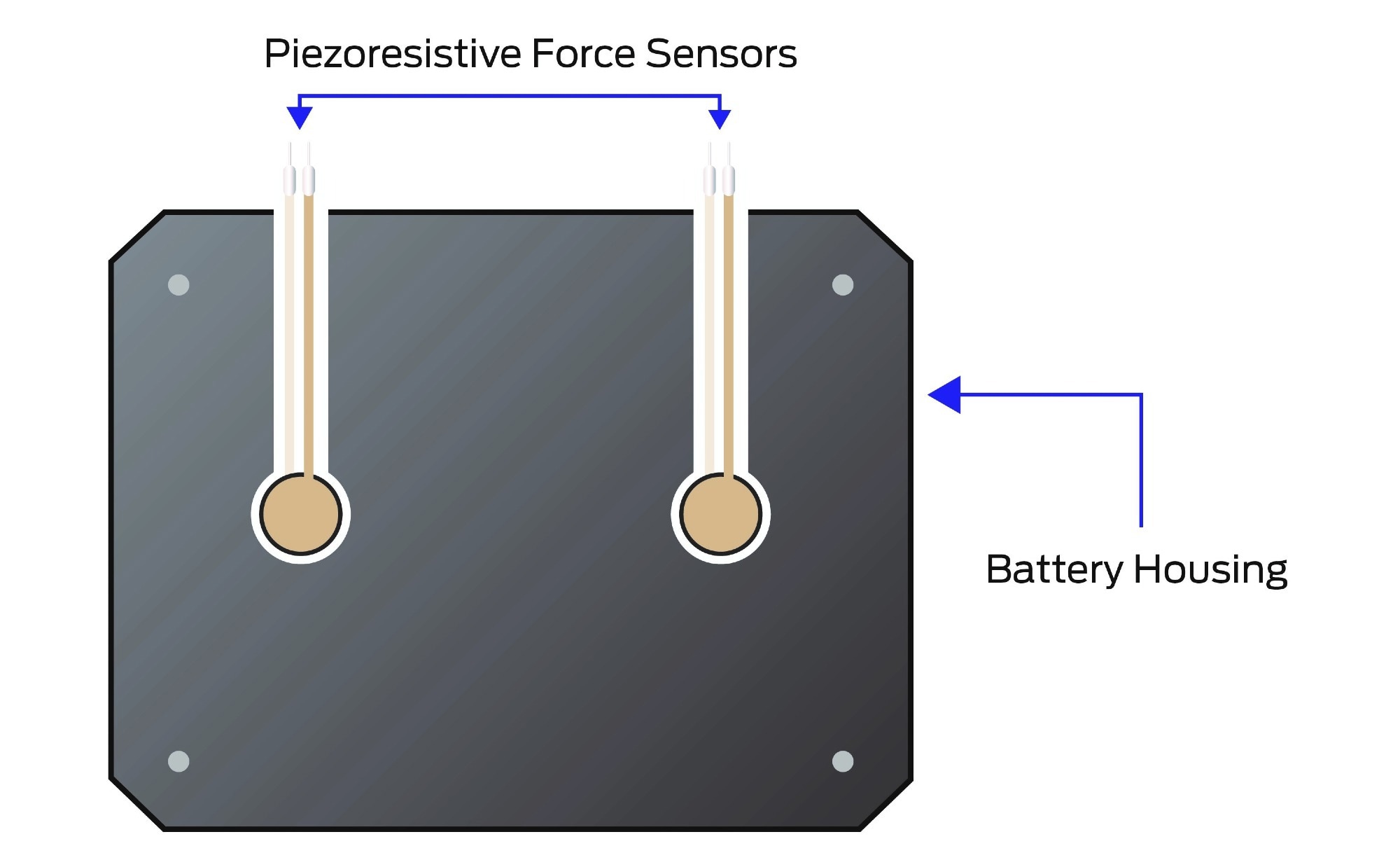
Representative design of prototype with two embedded piezoresistive single-point Tekscan sensors measuring force feedback from the battery
What changes to seat design could be made in the automotive industry with the direct application of your sensors?
Vehicle seating design, such as the seatings, seat belts, or the position of a person, will be different from the car's design today.
We are noticing that there will be autonomous vehicles, for example, that will not require you to be in front of the wheel—your whole driving position changes.
There is also a potential application in the redesign of seatbelts. A different seatbelt design could be more comfortable for a person that is not going to be at the wheel, who is just going to be sitting in a vehicle getting transported from point A to point B.
Our BPMS sensor is an application of seat design that uses the body pressure measurement system to improve the design and comfort of seats. This is one type of application that we had a lot of success with.
How does pressure mapping apply to tire design?
Tire design is also essential to electric vehicle design. We have technology that analyzes tire footprints. As vehicles change, tire and automotive manufacturers are looking at ways of maximizing tire life. They have relied on pressure mapping systems for a long time. Technologies such as our own TireScan are used to understand how a tire responds to different loads and conditions.
With the evolution of electric and autonomous vehicles, engineers will keep changing the tire for different requirements. We know electric engines and motors could have much higher torques than regular combustion engines.
That requires new insight into the design of the tires to make them last longer or even last as long as they do now.
Another example could be the bidirectional tires in EV design because we are talking to designers who are thinking of autonomous vehicles that will have the four wheels turning, and this creates an entirely different wear profile of the tire than the regular car.
These are just some of the applications we are seeing inside tire design.
What role can your sensors play in protecting battery packs?
We had a particular manufacturer interested in knowing the impacts or forces that could hit the battery pack and how they would have to design their housing to avoid any pebbles or debris in the street hitting that battery and damaging it.
This involves testing an undercarriage or a chassis to design it to better fit the design of the battery pack being put on a particular vehicle. This is an essential part of EV vehicle design.
How can your sensors be applied to door seals?
Another application is seal measurement on the doors. After using a Tekscan sensor on a doorframe, we were able to adjust that door in a way that the seal, after the adjustment, would be much more even across the surface.
If the door seal is uneven and you have varying pressures, it creates an uneven surface of pressure distribution that does not provide a proper seal but also more wear on your seals. It can increase noise coming from the exterior. A set of issues can be avoided entirely when the seal is evenly distributed across the sensing area.
Door design is another area that is being completely changed by EVs. We have seen the Tesla Model X with its wing doors that go up in the air. You need to consider a whole new set of rules to design doors for EV vehicles.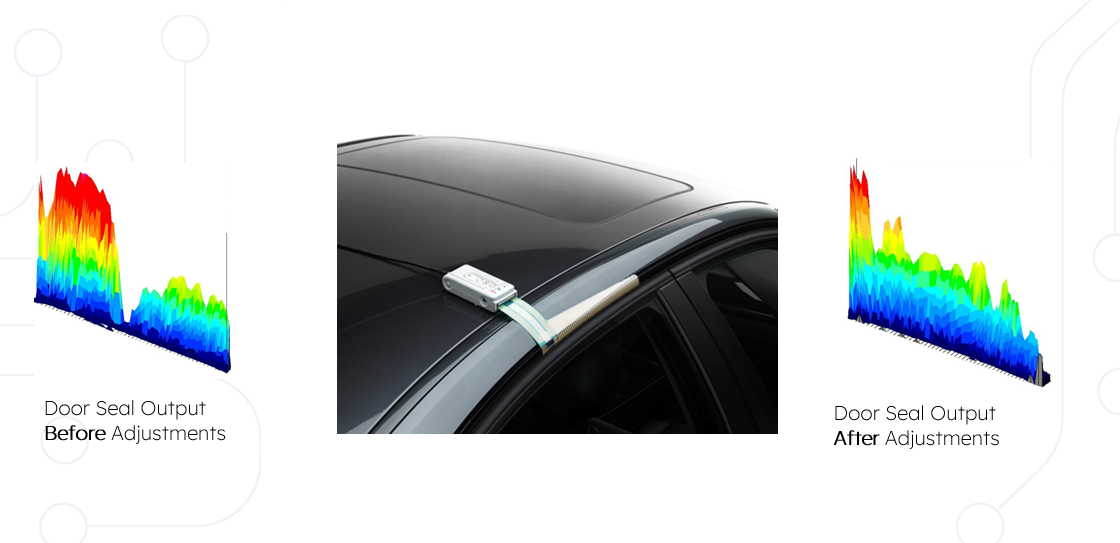
Tekscan Pressure Mapping Sensor Measuring Door Seal Pressure
Do you have specific sensors for different applications?
We have an extensive catalog of standard sensors and also can create custom sensors. We can connect you with our sales and engineering teams if you require a battery pack or any other necessary component for your application. They will assist you in identifying the appropriate sensor required for your needs. We can design a sensor specifically for what you need.
Where can customers find more information?
We could go much deeper into the mobility industry and applications for Tekscan sensors to map the distribution of pressures and create better, optimized designs. For more information, I welcome you to visit our automotive page to see all the applications we've worked on in this space.
At Tekscan, we pride ourselves on providing our customers with the best tools for surface-sensing insights. We want the industry to create better products and to make the next generation of vehicles superior. We are not experts in EVs, but we know how to support the experts with pressure mapping and force measurement tools to fulfill the industry’s potential.
Please visit the webpage, and if you have any questions, do not hesitate to reach out. I would be happy to connect if you want a demo or have particular questions about your case.
I am very excited about the future of this industry and look forward to seeing everything that will happen.
About the Speaker
Raul Oreste has more than twelve years of experience spanning business development, product management, and engineering across diverse sectors, from aerospace to manufacturing. As a Product Manager at Tekscan, his focus is on working with Tekscan's customers to understand their applications and craft a roadmap for new products that cater to their surface sensing requirements.
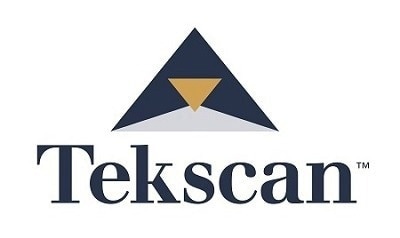
This information has been sourced, reviewed and adapted from materials provided by Tekscan, Inc.
For more information on this source, please visit Tekscan, Inc.
Disclaimer: The views expressed here are those of the interviewee and do not necessarily represent the views of AZoM.com Limited (T/A) AZoNetwork, the owner and operator of this website. This disclaimer forms part of the Terms and Conditions of use of this website.