The requirement to check fine tolerances in quality control is a challenge for metrology. In addition to being precise, the sensor can't overlook any relevant information, so the entire functional surface must be characterized.
As contacting measurements are time-consuming, only a few random samples can be examined on the manufacturing line in the time available.
Short reaction time is desirable in case of problems to occur. So, implementing a full-field optical method offers great potential for saving costs.
Optical surface measurement instruments provide a solution to characterize an entire surface quickly. As each camera pixel works as a sensor, 2 million pixels are equivalent to 2 million measurements.
Additionally, interferometric methods help to achieve such high accuracy in a vertical direction, irrespective of the measurement area and the field of view.
Therefore, parallelism, step height, or flatness, etc., can be determined reliably and rapidly with a white-light interferometer.
This article presents two different kinds of white-light interferometers: a white-light interferometer with the ability to measure large surfaces for shape measurements and a white-light interferometer microscope with the potential to reveal finer structures. Structural parameters or texture parameters such as roughness can also be determined by the microscope.
Surface Profile Versus Line Profile
Compared to line profiles, surface measurements offer more information, for instance when determining flatness. They ensure a reliable recording of the highest and lowest points and local unevenesses.
Where there are contact surfaces, localized surface waviness can lead to high local loads, which influence the life of a component. A measurement taken with a white-light interferometer where the height information is shown through colors is given in Figure 1.
The instrument can create circular profiles on ring-shaped surfaces. A profile that runs between the inner and the outer edges with a flatness deviation of +/-100 nm can be seen in Figure 2. High reproducibility is ensured by the alignment at anchor points and edge lines.
.jpg)
Figure 1. Flatness measurement of a contact surface
.jpg)
Figure 2. Surface and line profile of a ring-shaped surface (measured by a TMS-300 TopMap in.Line)
This also applies in cases where the step height between two surfaces is of significance, as can be seen in Figure 3. When both surfaces are observed separately, it can be seen that the lower (outer) one has differences in height of several µm and the upper (inner) surface, located 425 µm higher, has a conical shape (Figure 4).
Based on the points chosen on each surface, measurements of step heights between two points can vary significantly. The centers of gravity of both surfaces and their parallelism can be determined with surface measurements.
.jpg)
Figure 3. Two circular surfaces (measured by a TMS-300 TopMap in.Line)
.jpg)
Figure 4. Details of the circular surfaces. Left: surface measurement with a probe; right: surface measurement with an interferometer
The TMS-100 and TMS-500 have a telecentric optical configuration, meaning that shadowing will not occur. Therefore, it is possible to characterize surfaces that are at the bottom of deep holes. A measurement of a slightly crooked and curved surface, which is positioned 40 mm inside a hollow cylinder, can be seen in Figure 5.
The scan depth range of TMS-100 and TMS-500 white light interferometers from Polytec, used for the large measurement surfaces, can range up to 70 mm. This means that they have the capacity to characterize multiple surfaces with large height differences. They can also determine radii, inclination angles, and lateral distances, in addition to parallelism and flatness.
.jpg)
Figure 5. Characterization of a deep-set surface
Examples show that as compared to traditional tactile methods, an optical surface measurement can provide considerably more information. This is illustrated by the coin example in Figure 6. The tactile probe surface measurement (left) is made of individual lines. The interferometer measurement found in the right side is more comprehensive. While the tactile measurement takes 30 minutes, a surface measurement can be performed in less than one minute.
.jpg)
Figure 6. Comparison of tactile (left) with an optical measurement (TMS-100 TopMap Metro.Lab) (right) on a coin
Short Measurement Times Are Required
When it comes to quality assurance, traceability, comparability, and reproducibility often play a significant role in addition to measurement times. Regardless of the operator, the comparability of results measured at different sites must be ensured.
The measurement procedures must be automatable for integration into both the production line and routine measurements. This is illustrated by the example on small wheels.
Several wheels are placed in the field of view and measured simultaneously in order to increase the clock rate (Figure 7). The initial set-up is made at one sample, and the measurement procedure and evaluation algorithms are determined. At the same time, the sensor learns the shape of the first component and using this information it recognizes and automatically measures the other components. The initial set-up took less than two minutes in this case.
.jpg)
Figure 7. Simultaneous measurement of several small wheels; the framed wheel was used for set-up (measurement with TMS-500 TopMap)
The initial set-up is stored and can be accessed for all subsequent measurements, regardless of the operator. The results are exported or shown in a good/bad table post measurement. Inferior parts can be inspected visually once again if needed (Figure 8). Even without the optional shape recognition, the measurements and analyses can be defined and retrieved.
.jpg)
Figure 8. Visually inspected individual measurement
International Standardization
Until now, tactile methods have been the most popular approach for surface measurements, with almost all international standards referring to this method. Meanwhile, international standardization should pay attention to optical methods as optical measurement instruments are gaining popularity.
High Precision
As shown, white-light interferometers measure with great precision. While the resolutions (smallest distinguishable step height) are in the sub-nanometer range, flatness, step height, roughness, and other texture parameters can be determined with nanometer precision.
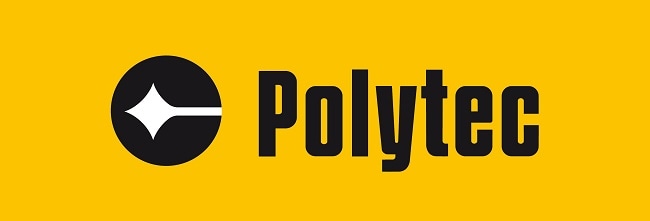
This information has been sourced, reviewed and adapted from materials provided by Polytec Ltd.
For more information on this source, please visit Polytec Ltd.