Level detection devices are helpful in inventory control as they eliminate the necessity to check levels by climbing onto the tank and improve safety in the workplace. They help in measuring the amount of space left in the tank through the measurement of the distance to the material or headroom in the tank. Pellets, granular materials or powders have the tendency to compact, shift or settle in the tank. Some sophisticated devices have integrated compaction calculations into their software to offset the material behavior to some extent. On the other hand, a level measurement instrument is not a scale. This application note discusses the some of the level sensor options and considerations.
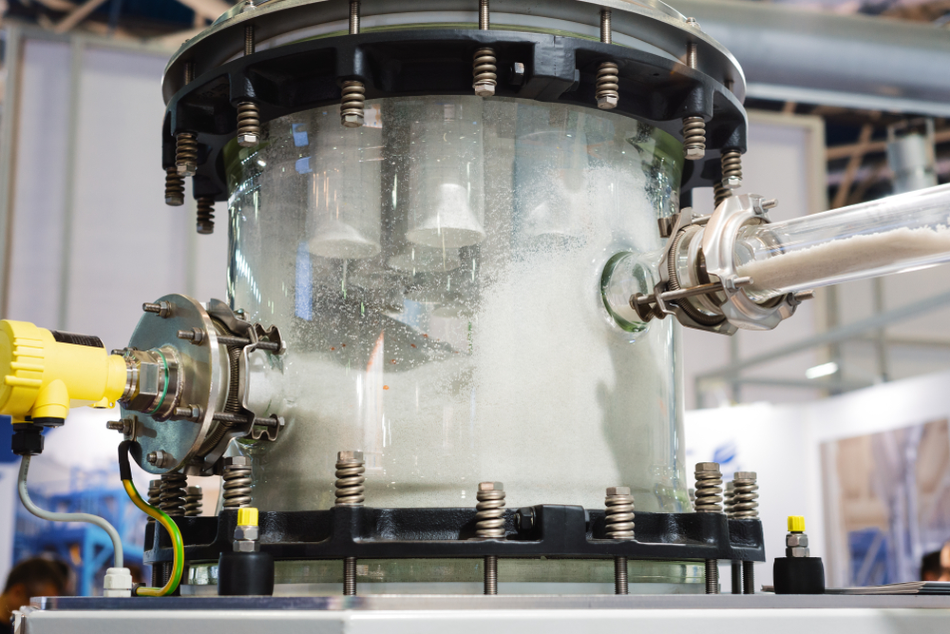
Image Credit: Shutterstock/Nordroden
Rotary Level Indicators
Rotaries are utilized for low or high level point level indication in silos, tanks and bins. They are useful in a variety of powder and bulk solid materials and capable of handling materials having a bulk density of up to 150 lb/ft3. They are employed in a myriad of industries including power generation, mining, pulp and paper, plastics and packaging materials, chemical and pharmaceutical manufacturing, agriculture and food processing, and renewable fuels industries.
.jpg)
For high level detection in a tank, a rotary can also be mounted on the top of the tank and an extension can be custom fabricated to reach the paddle to the desired level.
A vertical extension on a rotary is capable of allowing it to be extended as long as 12 feet down a bin for high level detection at the bin interior. For thick bin walls, a horizontal extension enables a rotary for material level detection through the sidewall. The combination of a horizontal extension and collapsible paddle allows the installation of the rotary via a 1-1/4- or 1-1/2-inch NPT opening without making an entry into the bin.
Capacitance Probes
Capacitance sensors are useful in the level detection of pellets, granulars, powders and other solid or slurry materials. They are utilized for low-, mid-, and high-level detection in vessels such as chutes, hoppers, tanks, silos, and bins where materials are flowing, stored, processed or discharged. They detect the absence or presence of a material in touch with the probe by detecting the capacitance change due to the variation between the dielectric constant of the air and the material inside the tank. It is important to know the radio frequency range of a capacitance probe and its effect on other devices in the plant before selecting the device.
There are capacitance sensor designs that use electronic circuits featuring balanced bridges and frequency shift oscillators operating at a frequency range of 100 kHz to 2 MHz in the RF range. On the other hand, there are capacitance sensor designs that utilize a discharge time constant detector circuit sensing capacitance changes of below 1 pF and operating at only 6 kHz, which is much lower than the RF level of most plant equipment. A shielded, Delrin-sleeved sanitary probe is perhaps suitable for food processing or pharmaceutical applications. A Capacitance probe featuring fail-safe protection is suitable for continuous process operation to prevent process downtime, accidents, empty conditions or overfills.
The capacitance probe can be connected to an extended, flexible cable extension in situations where there is a need to mount the sensor on top of the tank or for high-, mid-, or low-level detection. A flush-mounted probe is useful in narrow or space-constrained areas, or in instances where material bridging or flow may cause damage to a standard probe. A bendable probe is useful in small tanks or where internal obstructions are common. It is better to house the probe and associated electronics in separate enclosures in high-temperature applications or in instances that involve excessive vibration.
Vibrating Level Sensors
The vibrating level sensor or vibrating rod is nothing but a piezoelectric-driven vibration type level switch used in detecting levels in hoppers, silos, and bins filled with dry bulk solid materials or powders. Vibrating level sensors are capable of detecting extremely light, fluffy materials of 1.25 lb/ft3. These rugged sensors are made of durable stainless steel and virtually free from wear and maintenance. It is possible to mount them on top of a tank for high level detection or in the bottom cone of a tank for low level detection. Vinrating level sensors feature a single rod shaped vibrating element that vibrates in the absence of material. When the material covers the element, its vibration gets dampened, which in turn sends an alert by causing a relay to switch by an electronic circuit. When the rod is uncovered with the material, the relay is switched back due to the restart of the vibration.
These piezoelectric devices are useful in applications that face problems due to variations in material density, temperature, humidity, or dielectric constant. Calibration is not required for most vibrating rods thanks to advancements in product design, thus enabling them to adjust easily to the designated sensitivity level. Other features offered include models with remote electronics or for high-temperature applications.
Bob-Style Sensors
A weight and cable-based or bob-style sensor is suitable for cost-efficient and accurate continuous level measurement in areas where minimal contact with the material inside the tank is acceptable. It is useful in a myriad of applications as it is not affected by dielectric constant, temperature, humidity, dust, or fumes in the bin.
.jpg)
A bob-style sensor provides high accuracy when mounted near the outer perimeter of the tank.
A bob-style sensor works in almost any material irrespective of bulk density or particle size and in bins up to 180 feet tall as well as in active, tiny process bins below 40 feet tall. It is trouble-free, does not require calibration and is useful to monitor different types of waste, packaging or processing materials in multiple tanks. It is possible to integrate bob-style sensor networks using different communication options.
.jpg)
Windows-based software available with bob-style systems allows for viewing the levels of multiple tanks simultaneously.
Ultrasonic and Radar
Ultrasonic and radar devices eliminate the risk of interfering with the internal bin structure or contamination as they avoid contact with the material inside the bin. They provide highly accurate measurements in liquid applications because liquid levels are uniform across the tank. They are single-point, continuous measurement devices for measuring and monitoring levels in tanks that are as tall as 100 feet. Ultrasonic devices generate and send ultrasonic pulses to the surface of the material inside the tank. These pulses get reflected off the product and returned to the sensor as an echo.
The time taken for the returning of the echo to the sensor identifies the distance to the material. Radar-based devices generate and send electromagnetic waves to the surface of the material inside the tank. These waves are then reflected off the material surface and returned to the sensor. The distance to the material is measured based on the time taken by the wave to return from the material surface. Current ultrasonic and radar devices offer wide processor capabilities that have PC software to monitor tanks and facilitate remote display options on a dedicated display panel.
Ultrasonic and radar devices deliver inconsistent performance in high dust conditions as their signals may become confused, leading to inaccurate measurements or no data at all. For hygienic applications, special care needs to be taken for sanitary fittings. A pulse radar device with Teflon antenna in an aluminum housing is suitable for level measurement applications in the pharmaceutical industry. It is better to select a self- calibrating or easy-to-calibrate ultrasonic or radar device because of the variability of materials being measured.
3D Scanners
A 3D scanner is a non-contact, dust-penetrating bin volume measurement device. It utilizes acoustics-based technology for measuring bin contents at multiple points inside the bin. Ultrasonic or radar devices can only measure one point and determine a single distance, while 3D scanners are capable of taking measurements at multiple points within the bin and using these points in estimating the volume of the material inside the bin.
.jpg)
A 3D Scanner is a non-contact, dust penetrating device that measures multiple points in the tank to provide greater accuracy.
The 3D scanner features software to display the tank data in easily readable format. It operates in tanks as tall as 200 feet and in materials having bulk densities higher than 12 lb/ft3. It is ideal in instances that require highly accurate volume inventories in optimizing production planning, purchasing, delivery logistics, and financial management. By determining build-up, it helps in protecting the tank from structural stress by allowing the maintenance crew to conduct timely preventive maintenance and cleaning.
.jpg)
The3D scanner can provide a visual representation of bin contents depicting high and low levels in the tank. The visual on the left is the tank contents and the 3D representation is on the right.
Conclusion
Type of information to be required comes first in controlling inventory in any tank in an operation. The number of tanks, tank size and whether they need to be networked are the other considerations to be taken into account while selecting a specific type of system.
.bmp)
This information has been sourced, reviewed and adapted from materials provided by BinMaster.
For more information on this source, please visit BinMaster.