Generally in ethanol facilities, there are large silos that continue to fill up and empty. Such facilities can significantly benefit from a reliable and highly precise inventory data so that they can improve operational efficiency, plan deliveries and appropriately report their inventory value.
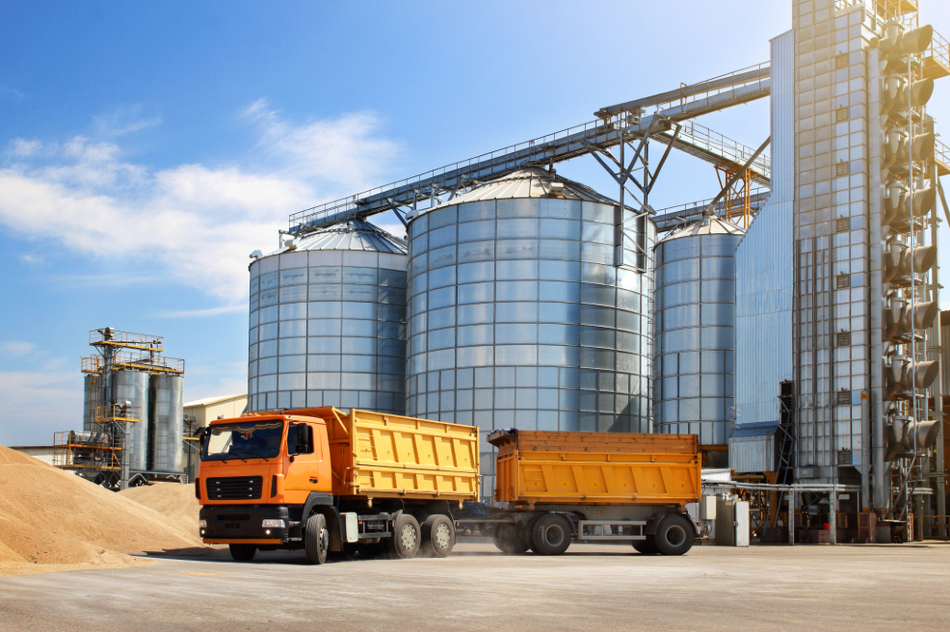
Image Credit: Shutterstock/golubsergei
Based on 3D mapping capability and multiple-point measurement technology, the BinMaster 3DLevelScanner precisely calculates the volume of material in the silo. Therefore, multiple-point measurements provide improved accuracy. While a single-point measurement device can be quite accurate in center-fill, center-discharge silos, the corn’s topography can be uneven as a result of multiple discharge or filling sites, side wall build-up, bridging, ‘cone up’ or ‘cone down’ during filling and emptying processes.
.jpg)
3DLevelScanner now installed on 4 large silos.
After calculating and mapping the surface of the material at various points, the BinMaster 3DLevelScanner uses an algorithm to find out the average height from all those points and then measures a volume estimate that is more precise than other single-point systems.
.jpg)
The image on the left shows uneven bin material. The graphic representation generated by the mapping software is on the right.
The BinMaster 3DLevelScanner, if properly applied, can provide 0.5% to 3% accuracy in silos having numerous filling and discharge sites. Conversely, a single point device achieves 5% to 7% accuracy. Also, with a single point device accuracy estimation is rather complex and often tends to be off by 15% or more.
Resistance to Dust Ensures Reliable Measurements
A low frequency acoustical signal is used by the BinMaster 3DLevelScanner to infiltrate dust that is produced during filling and emptying cycles. The device precisely measures the distance. These measurements are ascertained depending on the time it takes the signal to reach the solid material and return back to the device.
Non-contact Reduces Contamination Risk
Based on a non-contact, acoustics-based technology, the BinMaster 3DLevelScanner ensures that equipment does not come into contact with material, and hence eliminates the danger of equipment breakage or potential damage to conveyors in the bottom of the silo.
Mapping Software Detects Irregular Material
Multiple measurements are taken by 3D technology, which then maps the material’s topography. This produces a visual representation of the material that can denote build-up of material on the sides of the silo, as well as bridging. By finding out irregularities in the surface of the material, extreme amounts of build-up can be taken into account for in-volume calculations. On the other hand, with single point devices, a measurement could indicate that the bin is virtually empty, even when a large amount of material is left in the bin.
The mapping software creates images, which can be utilized for preventive cleaning and maintenance of silos. This means, with early detection of sidewall build-up, silos can be cleaned before the material hardens and makes it difficult to wash the silo.
Self-cleaning for Minimal Maintenance
The scanner is a self-cleaning device and this feature brings down the need for preventive maintenance in even the dustiest conditions. In some types of devices, suspended dust can stick to the surface and requires cleaning or maintenance at regular intervals. To this end, the BinMaster 3DLevelScanner should be examined and cleaned every six months to enable optimal and error-free operation.
.jpg)
3DLevelScanner mounted on top of cement silo.
.jpg)
Conveyor fill on top of the silo.
Application of 3D Technology
One particular ethanol facility had to deal with three kinds of challenges such as reliability, accuracy and dust. During fill rates, excessive dust made it very difficult to detect the filling and emptying cycles. To deal with the problem, the plant was utilizing guided wave radar, which is a single point measurement technology, in a huge bin of irregular topography. Since the material level differed considerably in multiple areas of the bin, sufficient level of accuracy could not be achieved with a single measurement. This problem was further intensified by the subsequent breaking of sensing cable on the guided wave radar. This made it impossible to take measurements and stalled the operations until the cable could be retrieved from the material contents and then restored.
The MV model of the BinMaster 3DLevelScanner was placed on a concrete silo that contained whole corn. This silo measured 150´ in height and 75´ in diameter. In addition, numerous discharge sites produced irregular material levels in the silo.
.jpg)
The 3DLevelScanner uses non-contact, dust penetrating technology to create a visual map of the material surface in storage and process bins.
In such a scenario, the multiple-point measurement proved useful to account for irregular material levels. With mapping capabilities, the MV model presented where the low and high points are located in the silo. With various discharge sites, the BinMaster 3DLevelScanner provided better volume accuracy when compared to the single-point guided wave radar device.
3DLevelScanner Sensor for Inventory Management — BinMaster
Conclusion
The 3DLevelScanner is a safe and smart choice and removes the risk of breaking cables and prevents operation shut down. These aspects can provide inventory measurement data to plant personnel where it is required and can allow the plant to optimize its filling and emptying processes.
.bmp)
This information has been sourced, reviewed and adapted from materials provided by BinMaster.
For more information on this source, please visit BinMaster.