Choosing the Right Sensor For Your application
Plant management and maintenance use point level sensors as a critical tool in managing the process of production.
Employed as high, mid-level, or low sensors, they can ensure a constant flow of material into a production process and mitigate downtime. When utilized in combination with an alarm, like a light or a horn, or wired to a PLC, they ensure workplace safety by removing the requirement to climb vessels.
Point level sensors are simple to install using an existing mounting connection, and many provide a range of power supplies, making it easy to wire them to the existing electrical system.
Mini Capacitance Probe Point Level Measurement — BinMaster
Video Credit: BinMaster
Cost Effective
The majority are affordably priced at a few hundred dollars, and point level sensors may be categorized within the MRO budget of a company rather than requiring the approval of a capital expense.
MRO purchases can frequently be completed on a credit card, dissimilar to a full inventory management system that is likely to require corporate authorization.
Light and compact, point level sensors can be installed gradually in several vessels at a time, without a massive investment in either money or time.
Overfill Protection
A frequently overlooked benefit of point level sensors is that they perform a crucial role in redundancy within an inventory management system. Point level sensors can warn users of potential overfills, performing as a high-level indicator.
Working in synergy with non-contact or continuous contact sensors, these highly dependable devices may identify a possible issue that may result in material waste or damage to the costly equipment, structure, or existing sensors in the vessel.
Meet Your Expert
A 23-year veteran of the level measurement field, Scott Bonine (pronounced Bo-neen) collaborates with customers across the globe. Scott became a part of BinMaster in 2010 and is the present sales manager for the Midwest region.
His knowledge in applications reaches a range of industries such as mining, plastics, cement, aggregates, agriculture, and much more. Scott regularly attends many industry events and trade shows, for example, ConExpo, NPE, the Powder Show, and GEAPS Exchange.
Process or Inventory Control
Bonine states that recognizing the distinction between point level detection and continuous inventory control is the best starting point.
Point level does exactly as the name infers—the sensor alerts you when material in the bin reaches a certain point. Most often they are used for process control to stop filling a vessel when it is almost full. Conversely, a low-level alert can signal to add material before running out.
Scott Bonine, BinMaster
Continuous inventory control utilizes different kinds of sensors, for example, guided wave or non-contact radars, ultrasonic or cable-based sensors, or 3DLevelScanners that continue to measure as levels change.
“Continuous level sensors serve a different purpose in ongoing inventory management,” explains Bonine.
He adds, “However, it’s always a good idea to use a point level sensor as a backup. They are relatively inexpensive and using them as a high level shut off prevents overfilling or damaging a more costly continuous level sensor. It’s a small price to pay for peace of mind.”
Rotary Level Indicators
Rotaries are a common and well-known device utilized for low to high-level point level indication in silos, bins, and tanks.
Rotaries are flexible enough to be employed in almost any material from granules and powders with a minimum bulk density of 2 lb./ft.3 to lumpy, coarse materials with bulk densities up to 150 lb./ft.3
BinMaster Rotary — BMRX 100, 200, 300 — Ultimate Point Level Indicators
Video Credit: BinMaster
The operating system for rotaries is easy to understand. When the rotary is utilized to identify when a material has reached a high level when the tank is filling, the paddle constantly rotates until the material comes in contact with it.
The paddle ceases rotation when it meets resistance from the presence of a material and triggers an alert to a control room or via a light, alarm panel, or horn.
As a low-level indicator, the paddle will start to turn when material falls under the level of the paddle and will communicate an alert or can be wired to stop a system in the process.
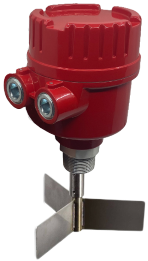
Image Credit: BinMaster
When configured for process control, it is crucial that a rotary with a fail-safe feature is utilized to make sure that it triggers a warning in case of a rotary failure. Rotaries are being used in increasingly innovative and new ways.
For high-level detection inside of a vessel, a rotary can reach as far as 12 feet down into the tank, silo, or bin using a vertical extension. This set-up is suggested for center-fill vessels when the process needs a particular amount of headroom.
A vertically-extended rotary, connected on top of the vessel, can send a notification when material is higher toward the center of the container instead of just identifying the level of material by the sidewall, which may be at a higher level when emptying (cone down) and a lower level when filling (cone up).
For thick tank walls, for example, those found in cement silos, a horizontal extension enables a rotary to be employed to identify the level of material through the sidewall.
When a collapsible paddle is used with the horizontal extension, the rotary can be set up without entering the vessel through a 1 to 1/4? or 1 to 1/2? NPT opening.
Plants Run on Rotaries
Rotaries are the most frequently used point level device. “They are known to work, are a familiar fixture on many vessels, and are used in every industry,” explained Bonine. “There is nothing to calibrate and, outfitted with the right paddle, rotaries will work in about any dry solid material.”
He continues, “When used for process control, a rotary with a fail-safe option is recommended. This feature keeps you apprised of the status of the unit, and most importantly, lets you know if it’s not working.”
“For example, a failsafe rotary can alert to the loss of power, failure of the motor, or failure of the electronics,” adds Bonine. A further consideration is rotary customization.
You might not realize how versatile a rotary can be and how many options there are. There are 19 different paddles for very light to heavy materials, vertical, horizontal, and flexible extensions, heat tubes for high temperatures, and stainless-steel connection options for sanitary or corrosive applications. Mini versions of rotaries are ideal for small vessels and tight spaces.
Scott Bonine, BinMaster
Capacitance Probes
Capacitance sensors are produced for a varied range of applications and can conveniently be tailored with many types of lengths, extensions, or probes.
These sensors can be utilized for low, mid, and high-level detection in silos, bins, hoppers, tanks, chutes, and alternative types of vessels where materials are processed, stored, or are flowing.
Capacitance Probe Overview — BinMaster
Video Credit: BinMaster
Capacitance sensors work by measuring the absence or presence of material reaching the probe, determining tiny variations (as small as 0.5 picofarad) in capacitance.
These variations are a result of the difference in the dielectric constant of the material against the air. Capacitance probes are supplied with many different options.
If the application is in an environment where there are excessive vibrations or high temperatures, the installation of a capacitance probe that keeps the probe and the electronics in separate enclosures is recommended.
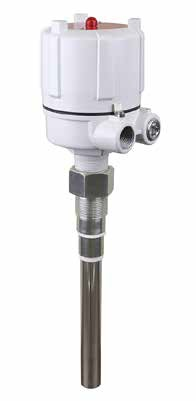
Image Credit: BinMaster
A flexible, extended cable extension can be mounted to a capacitance probe in circumstances where the sensor is attached to the top of the tank and can be utilized for low, mid, or high-level detection.
For applications that involve space constraints, narrow areas, where bridging or material flow could damage a standard probe, a flush-mounted probe is suggested.
When the vessel has internal obstructions or is small, a bendable probe can be employed to work around obstructions while still enabling sufficient probe surface area to identify the absence or presence of material.
Words of Wisdom about Probes
Bonine’s simple advice is, “A capacitance probe can be a great next step if you are using a rotary and want to move up to the next level.”
He suggests, “When side mounting a probe, you will want to keep the probe length short to avoid material bending the probe. A 6-1/2” probe generally works well. Better yet, use a heavy-duty probe, like the one commonly used in power plants or mining operations.”
“It’s best to talk with someone at the manufacturer before you spec in a capacitance probe. You might not know you should avoid using probes in low dielectric materials, as they may not sense them.”
Bonine continues, “If you are changing materials frequently in a silo, you may need to recalibrate a probe. A rotary may be a better solution.”
There are Teflon, Delrin, bare, 3A, unshielded, shielded, flush, and hanging options when it comes to the choice of probes. He concludes, “A Delrin probe is a great all-purpose choice. If you are using a probe in high temperatures or chemicals, a Teflon probe may be a better alternative.”
Vibrating Rods
The vibrating rod or vibrating level sensor is a piezoelectric driven vibration type level switch that can be utilized for level detection in hoppers, bins, and silos containing dry bulk solid materials.
Very light, fluffy materials, as light as 1.25 lb./ft.3, can be detected by vibrating level sensors. Examples of these are flakes and powders. They can also work with heavy materials like pellets or granules.
Vibrating Rod Level Sensors by BinMaster
Video Credit: BinMaster
Vibrating rod level sensors vibrate when the active rod has no material covering it. The vibration decreases when the rod is covered with material, and an electronic circuit prompts a relay to switch and triggers an alert.
The vibration starts again, and the relay switches back once the rod is uncovered. With developments in product design, the majority of vibrating rods do not need calibration and can simply adapt to the required level of sensitivity.
In process-critical applications, features like a fail-safe alert are crucial, as they trigger an alert when power is interrupted to the unit and reduce the chances of an empty tank or overfills that can close operations.
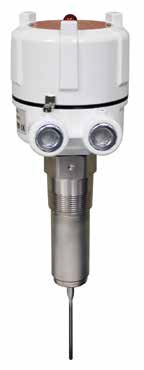
Image Credit: BinMaster
These sensors are becoming more and more versatile, with available features that can include remote electronics or models for high temperatures.
Certain vibrating rods can be increased to a tailored length, enabling the vibrating sensor to be utilized in a top-mounted application for high-level detection. Vibrating rods or forks manufactured with CSA or FM approval can be used in hazardous applications.
The Lowdown on Vibrating Rods
“Vibrating rods are often the best choice for extremely lightweight or low dielectric materials that can’t be sensed by a capacitance probe,” explains Bonine.
“They are also good for light, fluffy materials like Styrofoam that won’t cause enough resistance to activate an alert when using a rotary. Sawdust bins and hoppers containing plastic pellets are places where vibrating rods are often the best choice.”
Bonine warns, “When using a vibrating rod be sure the target material is not sticky, viscous, or clingy as this can dampen the vibration and cause false signals.”
He adds, “Vibrating rods can offer a lot of versatility in processing operations. There are models that can be used in super high temperatures up to 482 degrees Fahrenheit. They can also be extended up to 13 feet into a vessel when rigid or flexible extensions are added. You might not know they can be used to detect sediment settled at the bottom of a tank.”
Diaphragm Switch
The pressure or diaphragm switch was the first kind of point level sensor and is still one of the most well-known today. These switches are the most inexpensive and are very dependable when utilized in free-flowing granular and dry materials.
Diaphragm Switch Prevents Silo Overflows — BinMaster
Video Credit: BinMaster
Models can be supplied for standard environments along with hazardous surroundings that carry the risk of combustible dust. When the material reaches the level of the switch in the bin, the diaphragm switch functions by triggering a sensitive microswitch which delivers a signal.
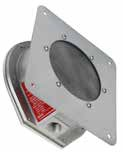
Image Credit: BinMaster
This signal can be utilized to stop or start an alert or a process to a low, medium, or high-level in the vessel. Diaphragm switches can be used for either external or internal mounting, and a range of diaphragm materials are available. They can be wired to an alarm, light, horn, or into a business’ PLC to show an alert.
Tilt Switch
A tilt switch is an inexpensive and dependable high-level indicator that is simple to install and does not need frequent maintenance. A hanging tilt switch is set up by hanging it from a flexible cable above a control point.
The concept behind its operation is straightforward. The switch tilts when material reaches it. When the tilt reaches 15 degrees, a microswitch is activated. Tilt switches are commonly utilized in silos or bins, or over an open pit or conveyor belt.
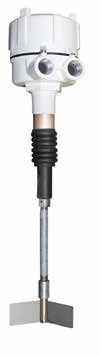
Image Credit: BinMaster
A hanging tilt switch can additionally be employed for plugged chute detection. On the other hand, a fixed-mount tilt switch can be installed externally on the top of a vessel using a process connection.
It functions by using an angular motion changed into linear motion to trigger an electrical microswitch that can be utilized to activate an external alarm or can directly communicate with a control system.
A fixed mount tilt switch can be customized in lengths from one to eight feet, according to the distance from the top of the bin where an alert should be triggered.
The latest, patented models are provided in a design that is free from mercury for applications that forbid the presence of mercury in their operations.
Myriad Mounting Options
Flexibility is an important characteristic of point level sensors. While they are more frequently employed for high-level indication, they can activate an alarm at any point across the vessel wall, in the cone, or a hopper. This signifies low levels for prompt refills and to adapt to differences in seasonal high-level inventory fluctuations.
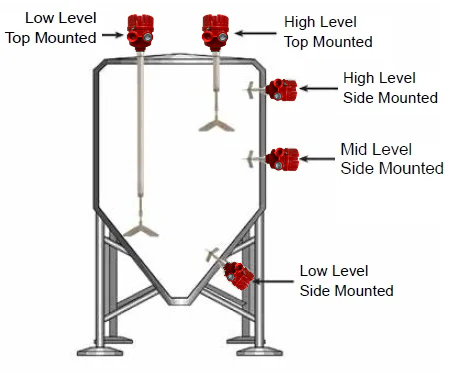
Image Credit: BinMaster
The Easiest Way to Avoid Mistakes When Selecting a Point Level Sensor
Point level sensors are affordable, highly durable, and simple to use. The key to success is choosing the correct sensor for the application.
Within each type of point level sensor there are so many options it can be overwhelming. You don’t want to use a baseball bat to hit a hockey puck. Talk is cheap. Make a phone call or send an email to the manufacturer to get free advice on the best solution for your material, application, and budget.
Scott Bonine, BinMaster

This information has been sourced, reviewed and adapted from materials provided by BinMaster.
For more information on this source, please visit BinMaster.