For a large scope of industrial applications, from quality control in manufacturing to process automation, imaging sensors are key. These sensors are able to gather visual information by converting the intensity of light into small bursts of current, which can be subsequently converted to digital signals.
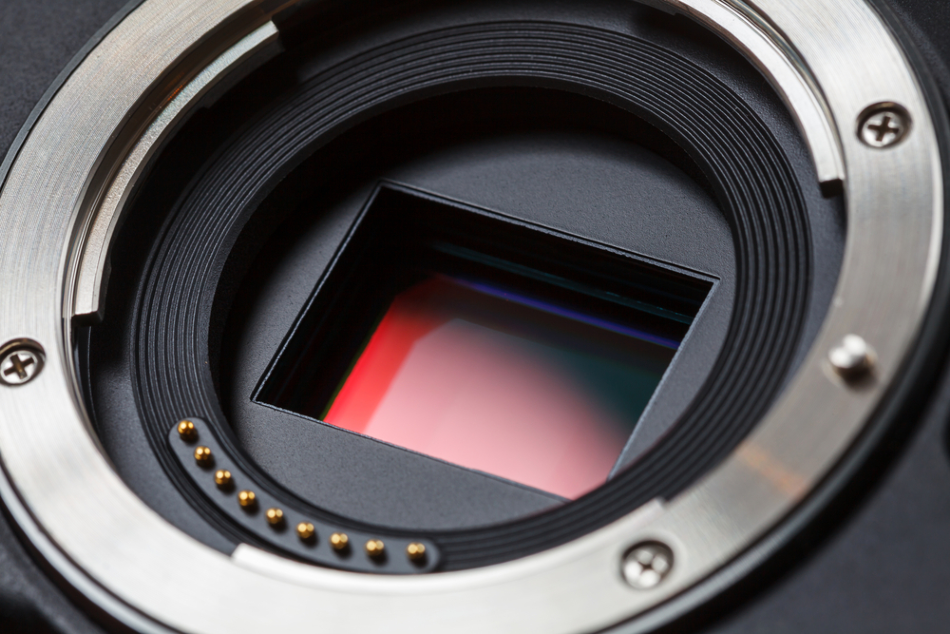
Image Credit: Shutterstock/Alex Yeung
CCD and CMOS technologies are the two main kinds of imaging sensor designs, these both have their associated benefits and drawbacks for different applications.
When selecting an imaging sensor for an application, the resolution requirements are one of the determining factors. In a standard imaging set-up, the resolution of a sensor is established by the number of pixels, with a bigger amount of pixels in a given field of view, the higher resolution.
Higher resolution makes it possible to resolve more detail on an object. Yet, while better resolution might seem desirable, higher resolution sensors are not always needed for all applications and may even present undesirable problems.
Less is More?
The angle through which the device can detect electromagnetic radiation is determined by the field of view on a camera. Wider fields of view equal larger viewable areas, which may be helpful for quality control on the manufacture of bigger items so the whole object can be imaged at once.1
Expanding the field of view while maintaining the resolution means raising the total number of pixels per area which grows sensor costs. More pixels also means a lot more data that must be read out and transferred from the sensor.
Regardless of its physical size, each pixel contains a lot of information. While chip architectures can be designed to quicken readout speeds and decrease the electronic noise which is introduced with this process, the larger the amount of pixels, the longer the overall readout time.2, 3
For applications which need high frame rates, or experiments that require cameras to be synchronized to other aspects of the experiment, like a laser, this limits the overall repetition rates that can be obtained.
In terms of data bandwidth and overall framerate, longer readout times may not be desirable, this is also true if any processing and calculations are to be carried out on the data.
For instance, a number of manufacturing quality control processes utilize automated computer vision to identify faults but more ‘webcam-like’ sensors can be employed for remote inspection of processes.4
In the case of remote inspection, if some type of algorithm must check pixels and their neighbors as part of an image recognition process, the higher the amount of pixels the more challenging this becomes, and not necessarily with the achievement of better fault recognition.
The Right Tool
This means that it is imperative to identify the real resolution needs of the application when selecting imaging sensors. For instance, not many automated processes will require the resolution offered by 31 MP camera sensors which are popular in microscopy and medical imaging applications.5,6
This is why market leaders in camera technology and image capture solutions, Allied Vision, provide custom, highly tailored solutions for customers’ imaging requirements.7
Some key factors to consider will be if the sensor needs to capture moving or still images, and so what frame rate will be needed, the size of the smallest resolvable detail necessary, and so the resolution, and how and where the captured data will ultimately be shown.
For instance, filming sports events necessitates a high frame rate so that sprint finishes and fast-paced tackles do not simply become a blur, but it is also required for the recording of high quality images.8
This is because sports events are typically seen on large screens at a long distance so the original image must be of sufficient resolution to cope with it. This makes for an especially challenging set of demands as the sensor must be able to cope with both resolution and high frame rates.
The resolution will be key for engineering problems where defects must be identified that are close in proximity and small in size, but resolving each defect spatially is crucial, as this establishes the minimum resolvable distance between objects for imaging.
Several sensors may be needed depending on the shape of the object, in order to form part of an intelligent machine vision network to fully visualize it in 3D space. The employment of multiple sensors for a single quality control measurement may mean costs become more prohibitive when identifying the right sensor.
In terms of resolution, for a number of industrial machine vision applications, less may be more but it is important to check that if small objects need to be imaged, there are enough pixels per area to resolve fully and unambiguously identify the object.
Establishing how many pixels are needed for clear identification of a feature of minimum size is key in working out the minimum resolution needed. More challenging imaging conditions, like poor lighting, may also affect the overall sensor resolution required.
References and Further Reading
- Tarabanis, K., Tsai, R. Y., & Allen, P. K. (1994). Analytical Characterization of the Feature Detectability Constraints of Resolution, Focus, and Field-of-View for Vision Sensor Planning. CVGIP: Image Understanding. https://doi.org/10.1006/ciun.1994.1024
- Bigas, M., Cabruja, E., Forest, J., & Salvi, J. (2006). Review of CMOS image sensors. Microelectronics Journal, 37(5), 433–451. https://doi.org/10.1016/j.mejo.2005.07.002
- Reibel, Y., Jung, M., Bouhifd, M., Cunin, B., & Draman, C. (2003). CCD or CMOS camera noise Characterisation. European Physical JournalApplied Physics, 21, 75–80.
- Chiou, R., Mookiah, P., & Kwon, Y. (2009). Manufacturing e-quality through integrated web-enabled computer vision and robotics. International Journal of Advanced Manufacturing Technology, 43(7–8), 720–730. https://doi.org/10.1007/s00170-008-1747-3
- Medical Imaging (2020) https://www.alliedvision.com/en/applications/medical-imaging.html, accessed 14/03/2020
- Science and Research Applications (2020) https://www.alliedvision.com/en/applications/science-research.html, accessed 14/03/2020
- Allied Vision (2020) https://www.alliedvision.com/en/about-us/about-us.html, accessed 14/03/2020
- Sports and Entertainment (2020) https://www.alliedvision.com/en/applications/sports-entertainment.html, accessed 14/03/2020
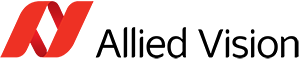
This information has been sourced, reviewed and adapted from materials provided by Allied Vision Technologies, Inc.
For more information on this source, please visit Allied Vision Technologies, Inc.