Interview conducted by Courtney Garner, MAApr 17 2020
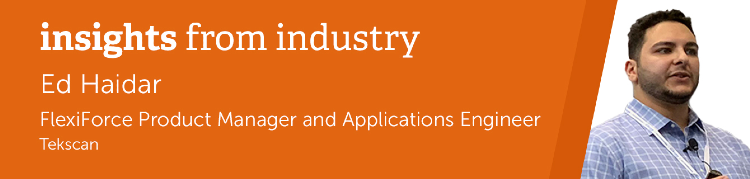
AZoSensors spoke to Ed Haidar, FlexiForce Product Manager and Applications Engineer at Tekscan, about how Tekscan's force and pressures sensors work, why sensor characterization is important, and how Tekscan's products can be used for this application.
Could you give readers an overview of Tekscan and the solutions you provide?
At the core, Tekscan is a manufacturer of thin, flexible force and pressure sensors as well as complete pressure mapping systems. We serve varied customers across industries with unique application needs, from engineers at Fortune 500 companies to startups and entrepreneurs to hospitals, researchers, and dental offices. The common thread among this very varied customer base is that they are looking to use force or pressure sensors to innovate their products, research, or clinical practices.
We have dedicated teams and products to support each of these types of customer. For example, we manufacture FlexiForce™ sensors which are compression force-sensitive resistor technology for design engineers seeking a thin, low-power force sensor to incorporate into a product or device. For these customers, we offer a wide range of standard FlexiForce sensors as well as customized sensors, and we have dedicated applications engineers who work with customers to ensure that their sensor integration project goes as smoothly and efficiently as possible. What really defines us, and what we pride ourselves on, is the specialized experience and expertise we bring to these varied customers and applications.
How do Tekscan’s FlexiForce sensors work and what are some embedded or OEM applications?
The FlexiForce sensor acts as a variable resistor with respect to force, in an electrical circuit. When a force is applied to the sensor, there is a proportional increase in sensor conductance (1/Resistance). This change in conductance, or sensitivity, can be customized depending on the needs of the application. The conductance of FlexiForce sensor is linear through its intended force range, allowing the sensor to be easily calibrated.
Embedded applications for FlexiForce sensors include contact/touch detection, rate of change in force, and force threshold triggering. In medical devices like wearable drug delivery devices, for example, slight changes in force can be an indicator of system misuse or malfunction. In some of these devices, FlexiForce sensors are embedded within or around critical areas of the device and serve as a key component to monitor for changes in force and trigger alerts accordingly.
FlexiForce sensors are appealing to design into these applications because of their thin, flexible profile, low power requirements, and low cost relative to other force sensing technologies.
What are some of the challenges of designing in components like force sensors, and how does Tekscan’s new product range help overcome this?
In any one project, engineers are tasked with familiarizing themselves with many technologies and components. Unless they are fully immersed day to day with a given technology, it is unrealistic to expect them to anticipate the inherent electrical and mechanical nuances. To come forward with a viable prototype, engineers need a thorough fundamental understanding of the sensor in order to have confidence that the sensor will work as intended in the final design, and they need to gain it quickly. Without a thorough understanding of the technology, the odds of encountering costly delays and redesigns increase.
FlexiForce has introduced new development products intended to aid engineers and designers in the successful progression through the sensor integration process. These products were developed based on our years of first-hand experience working directly with OEM’s, design houses, and engineers. They are a game changer for those integrating FlexiForce sensors. From sensor characterization to prototyping through final design, these products provide a comprehensive platform employing the methodology recommended by Tekscan’s applications engineers.
The open source nature of the products allows for them to be adapted to the specific needs of an application. Users are empowered with products that can characterize circuit performance, static or dynamic loads, and sensor response with respect to material interface. Sensitivity adjustment and calibration approaches can be adjusted programmatically in the source code of the products. These are just a couple ways these new products can be easily adapted to fit the needs of an application. The goal of these products is to allow users to evaluate and optimize all aspects of their design and easily migrate it into the final product.
Why is sensor characterization important, and how do these products help with this?
While every sensor integration project is unique, sensor characterization is a crucial step in all of them. Sensor characterization is the process of establishing and understanding the fundamental performance of the sensor technology in a known and controlled loading environment. The FlexiForce Sensor Characterization Kit allows for users to test linearity, hysteresis, drift and repeatability via a desktop sensor loading fixture and pre-programmed loading profiles. The output of these loading profiles can be measured using three different analog circuits included with the product. Users can select the circuit that best suits their needs and establish a stable baseline of sensor performance within that circuit. The loading profiles and circuit components can all be easily modified to best fit the intended use and application.
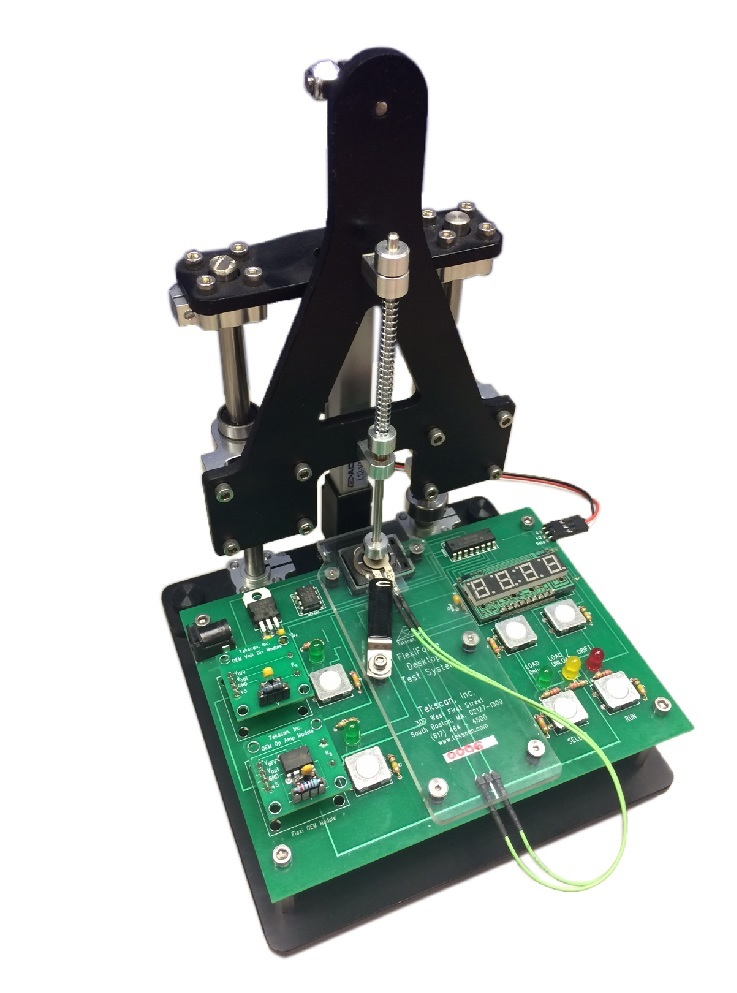
The FlexiForce Sensor Characterization Kit. Image Credit: Tekscan
Characterizing sensor performance and establishing a performance baseline are key towards troubleshooting and debugging in later stages of the integration. When unexpected data is obtained in later integration stages, users can refer back to the baseline, identify deviations and determine what part of the system needs to be examined or modified. This allows for an efficient integration process. Skipping sensor characterization can result in uncertainty when trying to identify root cause of unexpected system behavior, thus making the troubleshooting and debugging process more iterative than it needs to be.
The FlexiForce Sensor Characterization Kit includes a linear actuator loading fixture, a calibrated load cell, three interchangeable circuit modules, and open-source software to characterize FlexiForce sensors right at their desk. Not only does the Sensor Characterization Kit save the engineer time developing their own testing fixture, but it follows the same essential parameters that our Tekscan application engineers use when testing sensors, and working with OEM customers.
How do these products save time for engineers in the prototyping phase?
If the engineer or designer takes the time to characterize the sensor before proceeding into proof-of-concept or alpha- and beta-prototyping, they’ll more than likely have their interfacing materials and circuitry selected for these later stages. That, right off the bat, will save them a lot of time in these advanced phases of the integration process.
We do offer an additional testing platform for these later phases, called the FlexiForce Prototyping Kit. This small, battery-operated kit offers engineers and designers the freedom to test their sensor in their prototypes with their preferred circuit modules, make sensitivity adjustments, and gain more confidence in how the sensor will behave in their product. It also includes an open-source software to calibrate, monitor and record sensor performance in real-time.
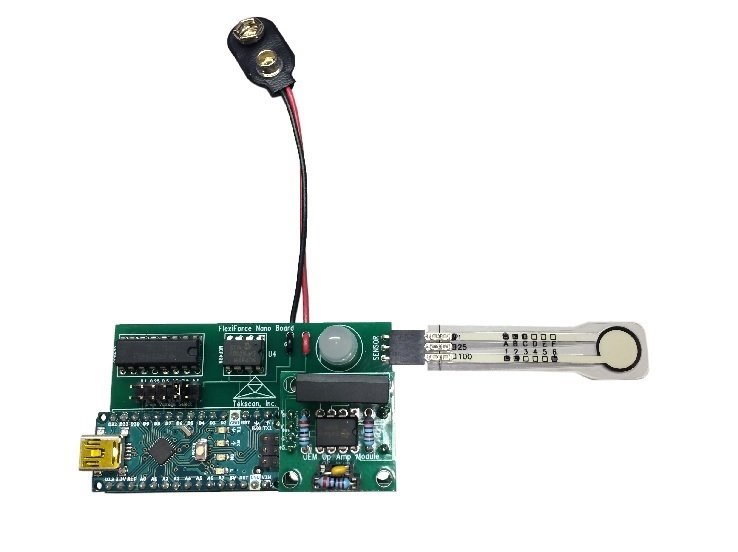
The FlexiForce Prototyping Kit. Image Credit: Tekscan
Building and debugging circuitry and other components can be time consuming, so the Prototyping Kit helps engineers stay efficient. The FlexiForce prototyping kit includes the same three circuit modules included with the Characterization Kit. This allows for the prototyping kit to be used independently if a user already has their own testing fixture. It also provides consistency in hardware if a user is using it in conjunction with the FlexiForce Sensor Characterization Kit.
What’s next for Tekscan?
We are always listening to our customers and looking for ways to help make things quicker and easier for them when it comes to embedding FlexiForce technology. We are constantly creating new content in the form of tutorials, integration guides, and how-to videos. We already offer a pretty wide variety of low cost standard products that customers can purchase online to get acquainted with our technology, and this year we plan to offer some additional off-the-shelf standard sensor sizes. Beyond that, Tekscan is collaborating with industry partners like SEMI-FlexTech Technology to explore the development and commercialization of new types of flexible sensor technology. Even after over 35 years, we’re still continuing to innovate.
About Ed Haidar
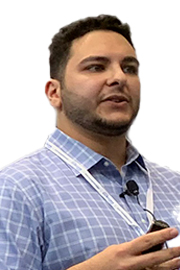
Ed Haidar, FlexiForce Product Manager and Applications Engineer, has been involved in a number of initiatives over his years with Tekscan, including design consultation, product development, technical documentation development, and more. Ed has extensive experience working with engineers and OEMs across industries on FlexiForce sensor integration; projects have included medical infusion pumps, surgical instruments, consumer electronics, and physical rehabilitation equipment. Ed has also worked in the field of optical components prior to his years with Tekscan, and has been credited with a patent in this industry.
Ed holds a degree in Electromechanical Engineering from the Wentworth Institute of Technology (Boston), with a concentration in biomedical systems.
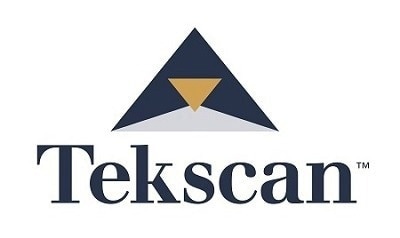
This information has been sourced, reviewed and adapted from materials provided by Tekscan, Inc.
For more information on this source, please visit Tekscan, Inc.
Disclaimer: The views expressed here are those of the interviewee and do not necessarily represent the views of AZoM.com Limited (T/A) AZoNetwork, the owner and operator of this website. This disclaimer forms part of the Terms and Conditions of use of this website.