Combustible gas safety monitoring systems for gas, oil, petrochemical or other applications will likely make use of catalytic bead or infrared gas detection technology. Both of these sensing technologies can be beneficial, depending on the specific requirements of the application.
Comprehensively analyzing an application’s particular field environment is necessary in order to ensure optimal safety, performance, reliability and cost-effectiveness. Rushing such a decision may result in poor detector choices, which in turn lead to reductions in performance, safety, maintenance and life-cycle cost efficiency.
MSA is a leading innovator in gas sensing technologies, offering two of the industry’s most popular and dependable approaches to gas sensing: catalytic bead detectors and infrared detectors. Both of these technologies are able to consistently detect gas, either at or below the lower explosive limit (0-100% LEL).
Both of these technologies are well suited for use within a wide range of field application environments - Table 1 provides a list of gases that are generally monitored.
Table 1. Gases Monitored. Source: MSA Safety
Typical Gases Monitored |
Other Gases Monitored |
- Methane
- Ethane
- Propane
- Butane
- Hexane
- Butadiene
|
- Isopropylamine
- Propylene
- Ethylene oxide
- Propylene oxide
- Ethanol
- Methanol
|
Because selecting the most appropriate sensing technology for each individual application is exceptionally important, MSA field applications engineers can conduct a risk assessment audit to ascertain the requirements of any potential safety monitoring system before commissioning an installation.
Catalytic Bead Sensing
Catalytic (or electro-catalytic) bead sensors (Figure 1) are built on a foundation of highly responsive technology with decades of demonstrable real-world experience. Being single-point combustible gas sensors, catalytic bead sensors operate on the fundamental principle that as combustible gas produces heat, it oxidizes.
The sensor converts temperature change to a sensor signal by using a standard Wheatstone Bridge-type temperature transducer.
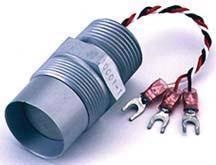
Figure 1. Catalytic bead sensor. Image Credit: MSA Safety
Sensor components are comprised of a pair of platinum heating coils fitted inside of a catalyst. Because all of the reactants are gaseous, the reaction occurs on the element’s surface, with combustible gases reacting exothermically with the oxygen present in air to increase its temperature.
This reaction leads to a change of resistance within the embedded coil and this change in resistance is linearly proportional to gas concentration.
MSA's General Monitors catalytic bead sensors utilize a pair of catalytic beads that are identical in all ways, other than a glass coating being applied to one bead (Figure 2).
The provision of an inert reference bead means that the bead remains permanently non-responsive to gas, ensuring that a stable baseline signal is available to compensate for any environmental changes that may impact sensor stability.
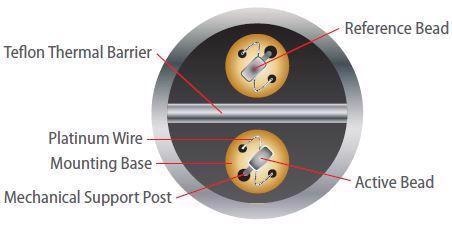
Figure 2. Catalytic bead sensor. Image Credit: MSA Safety
This method of glass coating is unique to General Monitors catalytic bead sensors. The physical and electrical matching of bead pairs means there is no requirement for compensating resistors that often result in operational drift.
The key to a catalytic bead sensor’s accuracy, reliability and longevity is the approach used in designing the substrate and catalyst system. It is vital that an abundance of active sites is maintained, because some of these may become poisoned during service. MSA ensures this essential reliability by employing a highly porous substrate that includes catalyst deposition down to the core.
Advantages
Catalytic bead detectors offer a number of key advantages:
- Robust performance
- Easy operation
- Straightforward to install, calibrate and use
- Long service life coupled with low life-cycle cost
- Established technology offering exceptional predictability and reliability
- Extremely flexible and suitable for use in a wide range of applications
- Effortlessly calibrated individually to accommodate gases such as hydrogen that cannot be detected via infrared absorption
Disadvantages
Catalytic bead detector technology does have some limitations, however:
- Contamination may lead to catalysts becoming inactive or poisoned
- Identification of sensitivity loss due to catalytic poisons involves routinely checking with an appropriate gas, then recalibrating as required.
- Sensors situated in areas known to contain potential poisons must be regularly calibrated and results logged. The manufacture will stipulate the interval between calibrations and this is then field verified.
- Needs oxygen for detection
- Extended exposure to high concentrations of combustible gas can lead to degradation of sensor performance over time.
Infrared Detectors
Gas sensing utilizing infrared (IR) detection relies upon the absorption of infrared radiation at particular wavelengths as this passes through a volume of gas.
IR detection technology combines a light source and light detector which measure the intensity of two distinct wavelengths - both at absorption and outside of absorption wavelengths.
Should gas be present between the source and the detector, the radiation level landing on the detector is reduced and can be monitored continuously. Gas concentration is established through a comparison of relative values between these two wavelengths.
It is commonly understood that most hydrocarbons absorb IR at around 3.4 micrometers, with H2O and CO2 both relatively transparent at this region. Based on this understanding, a dedicated spectrometer operating at this wavelength would be suitable for the detection of combustible hydrocarbons in air.
IR point detectors possess a fixed path length between the IR source and the IR receiver (Figure 3). This path length is generally short (just a few inches) and it is assumed that gas concentration is uniform across the path. By using a fixed path length, it is possible to directly express measurement of IR beam absorption by the gas measured (% LEL in this instance).
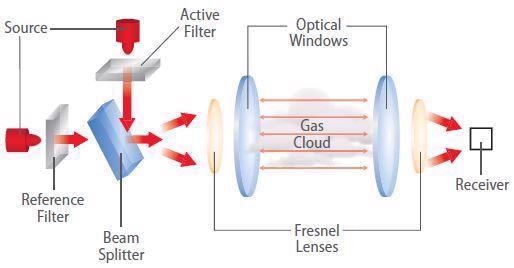
Figure 3. General Monitors IR400 Point Detector—optical scheme. Image Credit: MSA
A point IR detector is therefore able to provide true measurement of gas concentration at the point of detection. Open path IR detectors are able to expand a gas sampling path from inches to 150 meters, enabling the monitoring of large facilities for potential gas clouds (Figures 4 and 5).
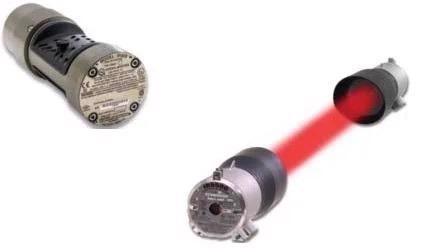
Figure 4. General Monitors' IR400 IR Point Detector and IR5500 Open Path Detector for hydrocarbon gas. Image Credit: MSA Safety
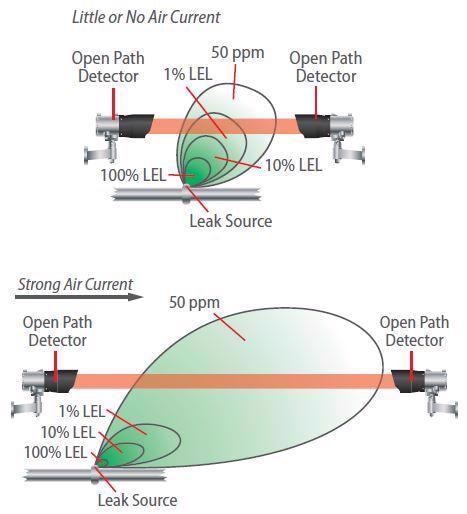
Figure 5. IR5500 and evolution of a leaking gas cloud. Image Credit: MSA Safety
Advantages
IR gas detectors offer the following advantages:
- Immunity to poisoning and contamination
- Fail-to-safe operation
- No need for routine calibration
- Able to function either without oxygen or in enriched oxygen
- Able to function when there is a continuous gas presence
IR detectors are factory-calibrated and practically maintenance free thanks to the current range of sophisticated optical designs in use. IR technology is particularly beneficial in instances where detectors must be fitted in inaccessible areas.
Maintenance requirements are minimal, with only periodic cleaning of optical windows required to ensure dependable performance.
Disadvantages
IR technology has a number of limiting factors including:
- Only infrared active gases such as a hydrocarbon can be measured
- It is not possible to detect gases that do not absorb IR energy, such as hydrogen
- Humid, dusty and/or corrosive field environments have the potential to increase maintenance costs of the IR detector
- Routine calibration to different gas is not practical
- Response testing requires a relatively large volume of gas
- Detector use is limited to a maximum ambient temperature of 75 °C
- IR is not ideal for sensing in multiple gas applications
- The IR source can't be replaced in the field - must be returned to the factory for repair
Application Requirements
The effective application of both catalytic bead or infrared detectors relies on the utilization of a detection system with detectors and sampling techniques appropriate to the area being monitored.
Different gases necessitate the use of different detection technologies and no one detection principle is able to provide the correct response and sensitivity for every gas.
Equally, detector heads should be matched to ambient conditions around the measurement point. MSA field engineers are able to help users determine the most critical factors to success of any application.
Site Location and Experience
Both catalytic detectors and IR point detectors boast long life expectancies even when operating in severe environments like the North Sea. IR detectors offer fail-to-safe operation within harsh refinery environments, but these should still be routinely checked with gas in order to confirm that gas is free to enter the optical path.
Dust shields and splashguards may become blocked in some environments or conditions and experience has demonstrated that users of both catalytic bead and IR technology tend to prefer to check detectors with gas as standard, meaning there is no notable difference in overall maintenance requirements.
Catalytic bead detectors remain the most suitable option for climates with high and low temperature extremes, around hot or vibrating machinery and in very humid conditions.
Calibration of Detectors
Both IR and combustible gas detectors’ measurement quality is reliant upon accurate calibration based on known gas concentrations. IR and catalytic bead detectors are both smart microprocessor-based devices which feature single-point calibration. There are no tools or area declassifications required – the calibration simply needs to be activated and the calibration gas applied.
Placement of Detectors
Catalytic and IR detectors offer users the option of three monitoring strategies: point, area and site perimeter.
In circumstances where the potential source of a gas leak is known and prompt detection is essential, a point monitoring strategy with detectors close to potential leak sources (for example, tank valves) is ideal.
A point detector grid system can be developed in large chemical processing or refining plants in order to monitor specific zones like storage tank areas (Figure 6).
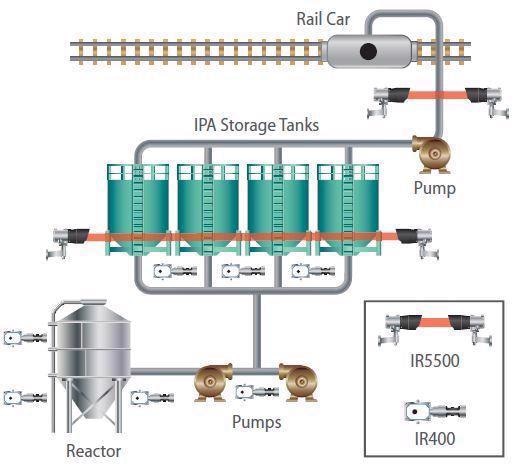
Figure 6. Typical installation for point and open path gas detectors.
Image Credit: MSA Safety
Where the layout of a plant makes identifying specific leak sources problematic because these may spread to other locations, a wider area monitoring system may be more suitable. These systems employ point gas detectors at pre-set geographic distances in order to ensure sufficient coverage.
Some plants may also need to employ outer perimeter monitoring along property fence lines, in order to ensure that gas does not pass beyond facility boundaries. Furthermore, open path IR detectors may be beneficial in settings where there is a need to detect gas clouds that can disperse over a wide area or become airborne (Figure 5).
A Modbus-compatible remote transmitter unit (RTU) is able to provide two-way addressable communications for alarm, status, fault and a range of information required to properly operate, troubleshoot or program detectors. Up to 128 point detectors can be networked in series and it is possible to network as many as 247 point detectors using repeaters.
Figure 7 displays a common system configuration which links 20 point IR gas detectors and 20 open path detectors.
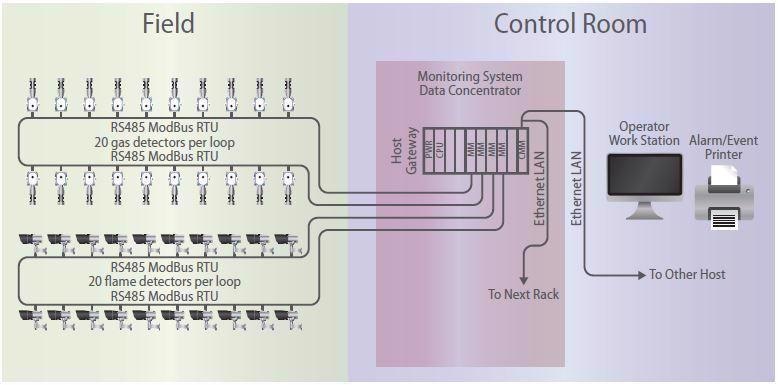
Figure 7. Multi-drop addressable system. Image Credit: MSA Safety
Maintenance and Repair
Routine checks of catalytic bead gas detectors should be performed every 90 days. IR detectors do not generally require routine calibration but it is advisable to perform a gas check every 90 days regardless. Calibration generally takes between one and three minutes.
A catalytic bead sensor can easily be field replaced if this is required. IR point detectors do require factory repair but repair frequency is generally very low. A spare IR detector may be installed, however, as the defective detector is sent for repair.
Anticipated Detector Life
Catalytic bead and IR gas detectors from MSA Safety offer sensor life expectancies of as long as five years (cat bead) to ten years (point IR). One cylinder of gas can be used to calibrate catalytic bead detectors 50 times and, while IR detectors do not require routine calibration, a cylinder of gas can be used to calibrate these detectors 10 times.
The initial cost of IR is generally higher than that of catalytic bead detection, but IR maintenance costs are lower overall.
Performance and Reliability
IR detectors offer superior reliability due to their ability to function without oxygen and their fail-to-safe-style immunity to poisons. Meanwhile, catalytic bead detectors provide simple maintenance, low replacement costs and application flexibility.
Both of these technologies are accurate, reliable and offer rapid detection. Neither is necessarily appropriate for every application and it's not unheard of for plants to install a combination of both types of sensor depending on the process area.
Conclusion
Both IR and catalytic bead detectors are necessary, beneficial technologies. When choosing between the two it is important to thoroughly consider variables in detector design between manufacturers and the field environment that the detector will be located within. Life-cycle cost assumptions will likely vary between environments.
The same approach may be applied when comparing detector mean-time-to-repair or failure data between a number of manufacturers. Thorough analysis of detectors, suppliers and field experience is important in selecting the most appropriate IR or catalytic bead detector for a specific application.
Field applications engineers from MSA can also provide valuable insight and expertise, supporting users to make the best sensing technology choice.
This information has been sourced, reviewed and adapted from materials provided by MSA Safety.
For more information on this source, please visit MSA Safety.