Sponsored by CSEMSep 29 2021
There is a significant need to integrate numerous heterogeneous technologies to enable robust structural health monitoring for preventive maintenance or better control the feedback of integrated actuation moveable mechanisms and adaptive objects.
This is also key to moving additive manufacturing (AM) beyond state-of-the-art technologies of topology optimization, whereby it is essential to develop concepts and technologies that can facilitate these extra functionalities while maintaining the versatility and flexibility at the core of AM.
CHAMELEON aims to support the use of developing technologies in the manufacture of metal-based 3D parts with embedded functionalities, for example:
- Compliant mechanisms
- Electrical and pneumatic feedthroughs
- Sensors
- Actuators
It aims to achieve this using a combination of:
- Advanced design
- Inkjet printing (IJP)
- AerosolJet printing (AJP)
- Polymer casting
- Laser powder bed fusion (L-PBF)
- Surface post-treatment
CHAMELEON’s primary applications focus will be on markets already employing AM in production settings where users have requested additional functionalities.
Additive Manufacturing Benefits
AM is becoming increasingly central to the production of high-end components in the aeronautics, space and medical fields.
The critical needs of these industries can be met using the features available from AM, in particular AM’s capacity to produce components with complex geometries at moderate production volumes, as well as the weight reduction afforded by AM’s topology optimization.
Despite this, many AM applications are based on the manufacture of ‘passive’ elements with no functionality beyond their mechanical structure.
To continue to enhance AM’s market attractiveness, it is necessary to develop the technological foundations of new and ‘active’ AM functionalities, prompting CSEM to investigate the use of combined 3D printing and 2D printing to generate 3D compliant mechanisms with embedded sensors suitable for use in complex AM-based mechatronics devices.
Several key technology milestones have been demonstrated thus far.
It has been possible to achieve high precision and low stress stainless steel 17-4PH L-PBF manufacturing with high fatigue resistance, using this to manufacture flexure blades down to 0.1 mm and with a 45° angle.
The electrical wiring throughout the structure was also fabricated as part of this manufacturing phase.
It has also been possible to offer advanced surface polishing of the L-PBF structures down to 100 nm to ensure suitability for sensor printing.
Notable advances have been made in the 2D printing (InkJet or AerosolJet Printing) of a conductive and an insulation layer to form the strain sensor, with sensor performances currently including:
- Gauge factor (sensitivity) superior to 2 - better than or equivalent to a commercial thin film metal strain gauge
- Linearity better than 99.9%
- Yield of 100%
- R variation within a fabrication batch in the range of ±15% - offering the potential to produce thermally compensated strain gauges using Wheatstone bridge
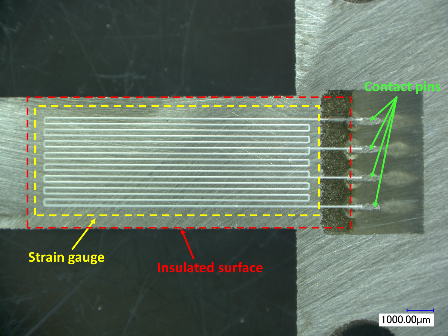
Figure 1. Printed insulation and strain gauge by AerosolJet Printing on a 300 μm-thick flexure element. Image Credit: CSEM
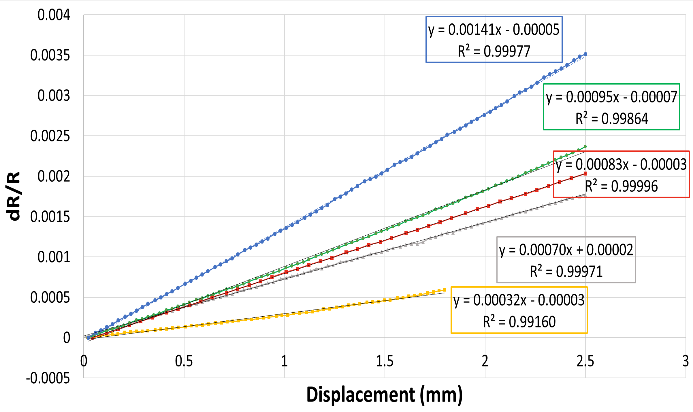
Figure 2. Performance of strain gauges from AerosolJet Printing for difference printing and/or curing conditions. Image Credit: CSEM
An initial demonstrator has been fabricated, featuring a ±5 mm stroke XY stage with a laser attached to the output platform.
High precision linear motion is achieved thanks to the integration of 300 µm-thick flexure elements, which feature built-in electrical wires. These wires both supply the laser source and deliver an appropriate interface for the printed strain sensors.
The overall structure represents a total volume of approximately 80x50x80 mm3, while the demonstrator’s actuation is provided by servo motors. Sensor integration is currently underway.
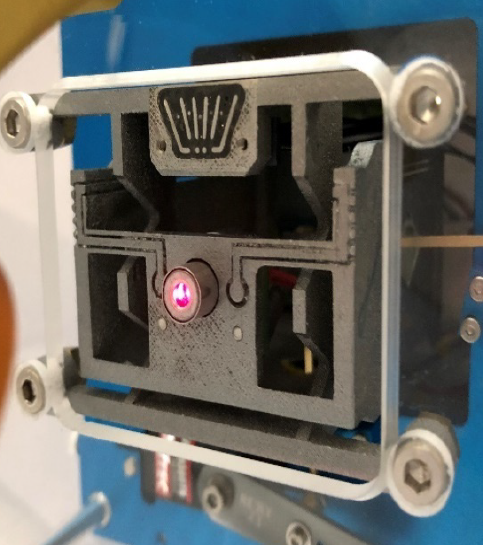
Figure 3. 3D printed XY-stage with embedded sensor and external actuator. A laser pointer is integrated to the moving platform to illustrate the capacity of the demonstrator to power a device through flexure blades. Image Credit: CSEM
A new material has also been developed via L-PBF, offering a low CTE (<1 ppm) and making use of a FeNi alloy (INVAR).
Acknowledgments
Produced from materials originally authored by S. Lani, N. Hendricks, S. Zabihzadeh, G. Perruchoud, L. Kiener, F. Cosandier, N. Marjanovic, J. Disser from the Swiss Center for Electronics and Microtechnology.
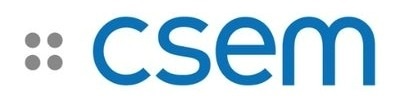
This information has been sourced, reviewed and adapted from materials provided by CSEM.
For more information on this source, please visit CSEM.