Vibrating fork level instruments — also known as vibronic instruments — are used extensively in the process industries. A number of manufacturers make these devices available and across the world, millions of these devices have been installed over the past few decades.
One such manufacturer, Endress+Hauser, produces 330,000 Liquiphant level instruments (Figure 1) annually and has sold six million units since 1983.
While the fundamental elements of vibronic instrument technology have not changed a great deal over the years, today’s instruments now implement technological innovations to bring them into the digital age, meeting the needs of Industry 4.0 and the Industrial Internet of Things (IIoT), provide diagnostics themselves and offer access from mobile devices.
This article aims to detail such developments and demonstrate how they can be advantageous to end-users.
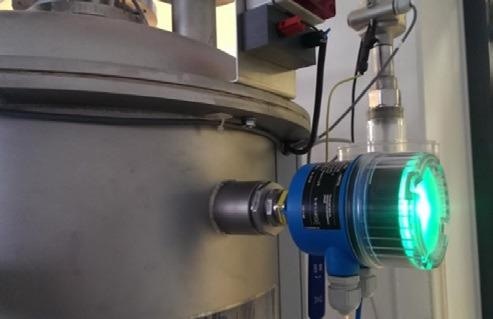
Figure 1. Vibrating fork point level instruments, such as this Endress+Hauser Liquiphant® FTL51B, are widely used in the process industries. Image Credit: Endress+Hauser Ltd.
Inside Vibronic Instruments
Vibronic instruments are comprised of a transmitter and a sensor. The sensor portion of the instrument uses a tuning fork (Figure 2) that is excited by a piezoelectric crystal at its resonant frequency, with a second crystal acting as a detector to pick up the vibrations produced by the first.
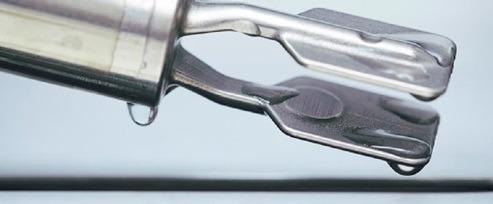
Figure 2. The oscillation of a tuning fork instrument changes when a liquid reaches the two forks. Image Credit: Endress+Hauser Ltd.
When a liquid covers the fork, the frequency reduces, and this change is analyzed and converted into an on/off output signal by the instrument’s transmitter.
Vibronic instruments are well adapted for liquid level applications, such as point detection at the top and bottom of tanks, use in hazardous environments, certified leakage monitoring and overfill prevention and in applications that demand safety certification in accordance with integrity level (SIL) 2 and 3.
These instruments can be deployed in containers, storage tanks and pipes for point-level detection of all kinds of liquids. In the oil and gas sector, refineries depend on vibronic instruments because they are amongst the most reliable measuring instruments.
This permits the use of these devices in critical applications such as overfill protection and pump dry run prevention. Unlike float switches, vibronic instruments do not require maintenance and have a prolonged service life. Moreover, the majority of these devices are corrosion-resistant.
Other advantages of vibronic instruments include:
- Easy installation and ready for use without calibration — in most cases, a vibronic instrument works in the application without any additional adjustments or calibration.
- No wear and tear, maintenance-free — a vibronic instrument has no moving parts and requires no maintenance other than periodic cleaning.
- Self-monitoring — new vibronic instruments are fitted with internal diagnostics and the ability to perform proof tests and verification automatically.
- Unaffected by media — vibronic instruments can be used to measure the presence of liquids with viscosities up to 10,000 mm2/s and densities greater than 0.3 g/cm3.
- Unaffected by media properties — a vibronic instrument is not affected by changing flow, turbulence, gas bubbles, foam, vibration, solids content or build-up.
Checking for Corrosion
Vibronic instruments contain no moving parts, so the only physical issues that could arise include corrosion and build-up of process materials on the tuning forks.
The majority of vibronic instruments are available with tuning forks comprised of corrosion-resistant metals, such as 316/316L stainless steel, Alloy C22 and PFA coatings, but even these types of materials are vulnerable to aggressive chemicals.
When tuning forks corrode, they can snap off, erratically vibrate or completely fail. Build-up of process materials on the forks can also appear, specifically in processes with entrained solids, turbulence or foam.
While a limited amount of coating can influence the probe’s frequency it does not cause it to fail, i.e. a lightly coated instrument is still capable of operation. But when signs of excessive build-up are visible on the tuning forks, it can lead to a failure in the device and changes in liquid level could go undetected.
Modern vibronic instruments have integrated diagnostics to detect corrosion and build-up by monitoring the frequency of the tuning fork. Early detection means that plant personnel address issues in an active manner before failure occurs.
Proof Testing
A proof test confirms the SIL rating of a safety instrumented function (SIF). NAMUR offers regulatory advice on what proof testing is required to meet the conditions of IEC 61508-6, B3.2.5.
NAMUR Worksheet NA-106 (Issue: 2018-09-06), Annex D, is usuallyy referenced in the process industries — such as chemical, petrochemical and oil and gas — as well as in other process plants that undertake hazardous operations.
Periodic testing of point-level instruments in these and other similar applications is necessary to meet various safety regulations. This can present a problem with older instruments as they may have to be extracted from the process for testing.
Fortunately, a number of new vibronic level instrument have the capability to perform a proof test on demand which is in accordance with IEC 61511 and ISA 84 safety standards.
For instance, a proof test for the Endress+Hauser Liquiphant FTL51B can be initiated from a control room by transmitting a command over a wired connection, from a mobile device via wireless Bluetooth® (Figure 3), or directly at the device.
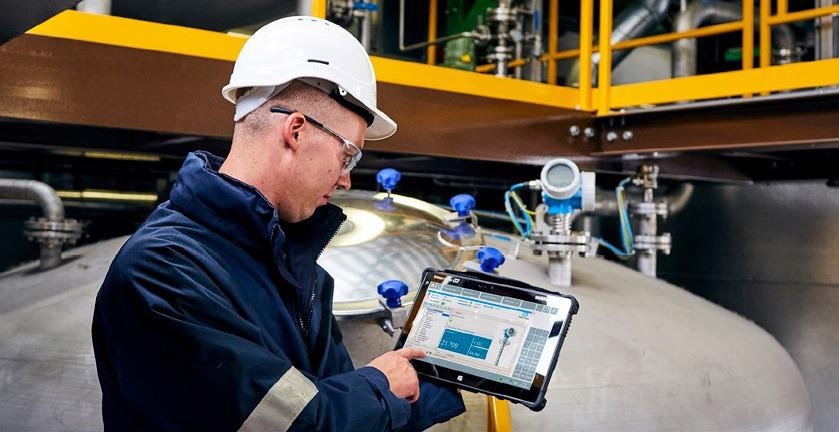
Figure 3. With Bluetooth wireless communications, a technician with a handheld device — such as an Endress+Hauser Field Xpert® SMT70 tablet PC tool can activate a proof test from up to 40 feet away from the level instrument, making it easier to perform tests on level instruments installed at the top of tanks or in inaccessible locations. Image Credit: Endress+Hauser Ltd.
The Liquiphant transmitter checks the instrument’s level notification and fault notification (alarm) functions when activated. After the instrument power supply has been interrupted, a test cycle begins, which checks the instrument and electronics.
This test is authorized for IEC 61508-6 and for overfill protection in line with the German Water Resources Act (WHG). Validating Verification Process manufacturing and other industrial facilities must usually offer documented evidence of level instrument performance to preserve compliance with numerous regulatory agencies.
Typical requirements are:
- A test report needs to be provided for documented proof of verification
- Level instruments must be verified at regular intervals
- Verification has to be conducted by a qualified third party and with an accepted inspection method predicated on quality regulations such as ISO 9001
The chemical and oil and gas industries have regulations for proof testing per IEC 61511, ISA 84 and other standards, while the oil and gas industry must comply with contractual agreements between buyer and seller and adhere to government agency mandates.
The majority of level instruments at the bottom or high point of a tank are routinely immersed in liquid and activated regularly. But, some high-high level instruments (Figure 4) are hardly or never immersed in liquid, so they only necessitate periodic verification.
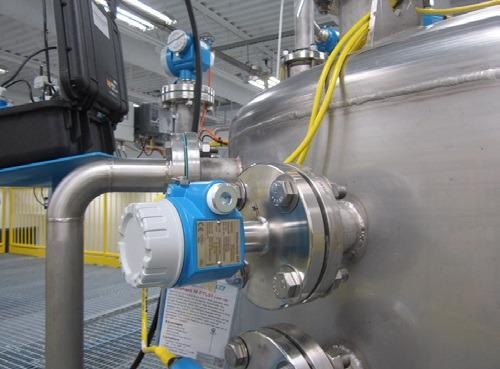
Figure 4. This Endress+Hauser Liquiphant high-high level instrument detects a level that’s too high and could cause a spill. Image Credit: Endress+Hauser Ltd.
Regulatory requirements are frequently fulfilled by extracting the level instrument, taking it to a lab, and immersing it in a liquid to confirm operation (typically called a “bucket test”).
Damages that occur during transport or handling can sometimes go undetected and lead to a situation where an instrument that has been tested recently is not performing per specifications.
Conducting verification in this manner is also time-consuming, leads to increase costs and necessitates field work to extract and reinstall the instrument. Operator exposure to the chemical process is another safety concern.
To confront these issues, a number of modern vibronic instruments can perform on-board verification in situ.
The instrument’s transmitter electronics perform an on-board diagnostics program, where all applicable components of the instrument are tested to confirm and document that none of the components have drifted outside original tolerances and that it is still in calibration.
For instance, verification of an Endress+Hauser Liquiphant level instrument includes testing all electrical connections and power against factory specifications.
Endress+Hauser’s Heartbeat Technology® is in full compliance with the requirements for traceable verification in line with DIN EN ISO 9001:2008, Section 7.6 a, “Control of monitoring and measuring equipment.”
The technology produces a PDF report summarizing results upon completion of verification, which can be used to meet audit requirements.
Meeting IIoT Demands
For point-level instruments, the demands of Industry 4.0 and IIoT remain limited. However, predictive maintenance and process optimization software programs require data relevant to instrument performance.
Most instrument manufacturers have comprehensive software offerings to acquire, store and analyze data from smart devices, such as vibronic point level instruments. These software packages — like Endress+Hauser’s Heartbeat Technology — have the capacity to evaluate the data from proof tests and verifications.
Mobile computers and wireless technology allow a technician on the plant floor to easily identify a device, commission it, check the status, conduct a proof test or verification and download verification documentation.
Subsequently, if the situation demands further attention, the technician can download the relevant manuals, certificates or other documentation related to the instrument. This level of digital competency allows vibronic instruments to meet Industry 4.0 and IIoT requirements.
Summary
Point level instruments were once resigned to a simple life, only indicating if a liquid was present or not.
However, level instruments now have to meet a range of safety regulations and have the ability to diagnose themselves, perform self-testing and offer relevant data for IIoT and other digital initiatives.
Today’s advanced vibronic instruments are up to the task, continuing to offer reliable operation for level detection, with extra functionality to meet current and future demands.
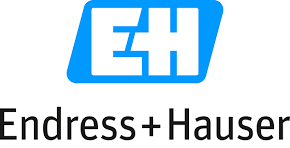
This information has been sourced, reviewed and adapted from materials provided by Endress+Hauser Ltd.
For more information on this source, please visit Endress+Hauser Ltd.