Failing to calibrate flowmeters can impact performance negatively. On the other hand, calibrating too often can lead to increased costs without offering any benefits. So, the question is, how do you know if calibration is necessary and what should the frequency be?
In a number of process plants, flowmeters are calibrated on an annual basis, or sometimes more frequently if that was how it was done in the past.
The combination of new instruments and technologies, in parallel with careful planning and study, can enable plants to calibrate flowmeters at an optimum frequency. This results in better operations and cost savings.
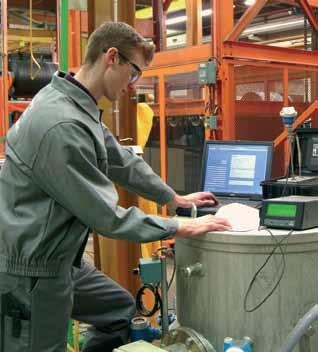
Image Credit: Endress+Hauser Ltd.
A flowmeter that fails to measure accurately can cause a multitude of difficulties. In a custody-transfer application involving crude oil or natural gas, even the slightest mistake can cost a customer millions of dollars per year.
A similar mistake can negatively impact the quality and safety of food products in a food processing plant, resulting in higher costs as a result of such failures. As flow measurements are vital to numerous processes, the industry standard is to calibrate on an annual basis, even if that may not necessarily be needed.
In several cases, this is conducted to show a quality auditor that instruments within the process are under control. For the majority of companies, annual calibration is carried out as a conventional ritual with no scientific basis behind it, except it being the longest period of time they are willing to risk before discovering a possible problem.
In a number of instances, annual calibrations are not necessary, as some flowmeters only necessitate calibration every three or four years depending on the process fluid, operation and criticality.
In other instances, a flowmeter may need calibrating on a regular basis, possibly monthly, to preserve a safe, efficient or regulatory-compliant operation. It is also crucial to realize that calibration intervals are not always fixed, meaning that they might change based on usage or historical performance.
Only by planning a calibration schedule that follows best practices for flow calibration can you know exactly when to calibrate a flowmeter.
The Importance of Instrument Assessment
The first step in a calibration plan is to carry out a plant-wide evaluation of all your instrumentation, including flowmeters. To execute this effectively, you must first identify and list of all the equipment parts and instrument-related systems.
This list should also detail elements such as location information, description, operating conditions, working range, history and any other key points that offer a better understanding of the part’s role.
The first stage in evaluating this data is to determine which instruments are crucial to the application, the environment and operator safety.
To begin with, the Head of Metrology (Quality) and Head of Maintenance — or adjacent professionals who carry the most detailed knowledge of the process and relative instruments — should determine their understanding of the process environment, the state of the installed instruments, the kind of maintenance work previously conducted and, finally, any limitations the plant enforces in terms of servicing.
Once this information has been gathered, it is essential to start from the finished product — and the tolerance permitted in relation to its quality — and backtrack through each of the stages in the production process.
At each stage, it is crucial to carefully evaluate each instrument and flowmeter in place and ask, “Does this instrument have an impact on the quality of the product (or intermediary product) on process functioning, or operator safety?”
The total installed base will establish at what frequency calibration of flowmeters is necessary. The following step will be to then plan a calibration schedule based on these factors.
The flowmeter manufacturer can also communicate with the Head of Metrology (Quality) and Head of Maintenance to identify which factors should be considered when determining which measuring points to include and assess the plant’s installed base. They can also help establish the appropriate calibration plan based upon your frequency needs.
Prioritize Your Flowmeters
After an installed base audit has been carried out, it is essential that all flowmeters are categorized by critical importance. Flowmeters can be grouped into one of four categories, ranging from critical to non-critical importance.
The first category — flowmeters critical for the product — are those that directly influence product quality. This is the starting point because these flowmeters directly link company profits, whether it comprises measurement of ingredients in food processing, mixing of chemicals or custody-transfer applications.
The next category — flowmeters critical to the process — can disturb the overall processes of the plant or even shut the entire process down, resulting in inefficiencies and production losses. However, this category has no direct effect on product quality or safety.
Flowmeters critical for safety have a direct influence on operator safety, equipment protection and/or the environment. These flowmeters do not need to be highly accurate, but they should, by all accounts, work properly and reliably.
Finally, non-critical flowmeters have no influence on product quality, the overall process, safety or the environment.
After all flowmeters have been determined and placed into one of these four categories, each device is allocated a Maximum Permissible Error (MPE). MPEs underline the tolerance for each function being measured.
A critical flowmeter will typically necessitate a more stringent MPE than a non-critical flowmeter. Suppose you can demonstrate to an auditor or another responsible entity that a non-critical flowmeter has no direct influence on product quality, safety or the environment, and its MPE is higher. In that case, you can claim periodic calibration is not necessary.
On the other hand, it may be necessary to calibrate critical flowmeters more often than just once a year to preserve critical product quality, process operation or safety
Four Categories of Critical Importance
Instruments should be ranked according to one of the four categories of critical importance listed below:
- Instruments critical for the product: Instruments that, if faulty, could have a direct influence on product quality.
- Instruments critical for the process/system: Instruments that, if faulty, may have a direct influence on process or system performance without impacting the safety or quality of the final product.
- Instruments critical for safety/the environment: Instruments that, if faulty, may have a direct influence on operator safety or the environment.
- Non-critical instruments: Instruments that, if faulty, are thought to not have any influence on safety, product quality, process or system performance or the environment.
Asset Management Software
To store flowmeter data from the audit, an asset management, maintenance management or instrumentation management program should be utilized.
One of the principal advances in recent years has been the development of instrumentation management software. These systems offer key information, including spare parts lists, drawings specific to the flowmeter, and original calibration data and certificates (Figure 1).
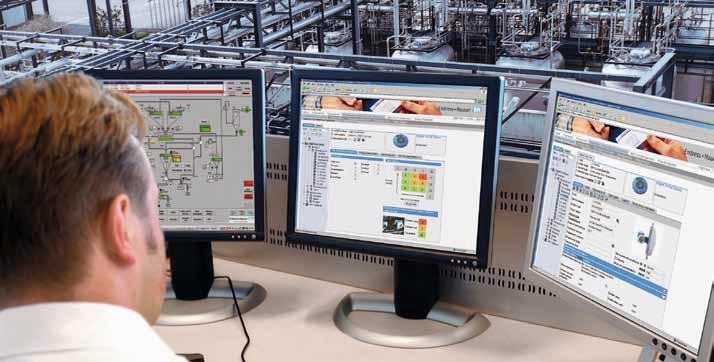
Figure 1. Flowmeter calibration data stored in an asset management system, such as Endress+Hauser’s W@M Life Cycle Management System. Image Credit: Endress+Hauser Ltd.
Each flowmeter manufacturer will calibrate the instrument prior to delivery to the customer, and the calibration data is entered into asset management software.
Subsequently, when a flowmeter is recalibrated, the device’s calibration history can be revised and can be automatically loaded via an electronic calibrator connected to the asset management system.
Another recent update offers maintenance personnel mobile access to the information in an asset management system networked to mobile devices (Figure 2). From the field, a technician can look up the diagnostic data, calibration history, troubleshooting instructions and other information necessary to identify a flowmeter problem.
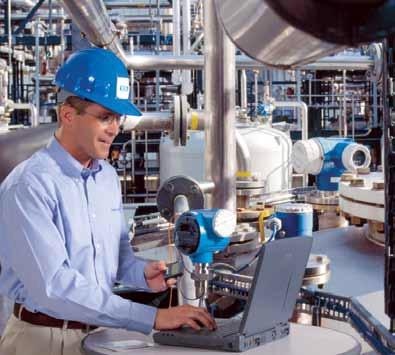
Figure 2. A technician manages a flowmeter’s calibration data via a software system, such as Endress+Hauser’s CompuCal calibration management system. Image Credit: Endress+Hauser Ltd.
The automation system and/or the asset management system can read the diagnostic data from each flowmeter. For instance, diagnostic data for a Coriolis flowmeter includes empty pipe detection, electronics error, sensor error, sensor drift, inhomogeneous mixture error, ambient and process temperature errors and other information.
This data can be utilized for optimal calibration, to diagnose problems and to determine minor issues before they become significant problems.
All flowmeter vendors can offer this kind of information in real-time, usually via fieldbuses such as Profibus PA, Foundation Fieldbus or EtherNet/IP. Depending on the fieldbus, flowmeters can also grant field technicians direct access to the diagnostic data.
EtherNet/IP, for example, allows devices to be polled by a condition monitoring or automation system to establish if there are any diagnostic messages that must be sent to maintenance personnel as an alert.
An industrial PC loaded with asset management, maintenance, condition monitoring or HMI/SCADA software can gain access to all the real-time data and diagnostic information it requires directly from the devices.
In a number of cases, modern flowmeters equipped with leading diagnostics can establish if there is a potential problem, and condition monitoring or other software can alert the maintenance department via an alarm that a specific flowmeter may be having problems.
Deciding When to Calibrate
Planning and following a flow calibration schedule for individual instruments often necessitates collaboration with the flowmeter manufacturer and a qualified calibration company with industry experience. They are the most eligible to advise on how regularly a flowmeter should be calibrated in a conventional installation.
The end-user must then act on this advice and use it based on specific service conditions, functions of the meter and their experience.
Calibration frequency is contingent on the criticality and MPE, the continuity of the process (continuous use or intermittent use), as well as the nature of the product being measured, the need for clean-in-place (CIP) operations and the severity of process impacts.
Furthermore, the type of flowmeter (contact or non-contact), and how easy it is to access and remove the flowmeter for calibration should be taken into account.
In some instances, a flowmeter may only be accessed during a total process shutdown; in other cases, a flowmeter might always be accessible for calibration. In a new plant, setting the flowmeter calibration frequency is typically based on expected operational parameters and advice from the flowmeter manufacturer and qualified calibration team.
But in an existing plant, the calibration frequency can be determined by actual historical experience and previous documented calibration performance with the flowmeters and processes that generate better results.
It’s essential to note that in either case, quality, regulatory or safety requirements could direct a specific calibration interval irrespective of the advice from the flowmeter manufacturer or historical data from past calibrations.
Once a calibration plan has been in place for a few years, the role the instrument management software plays takes on greater significance.
When a calibration is done on a flowmeter, new data is recorded and stored in the data base. This data displays the status of the flowmeter before and after calibration, and it may determine that the flowmeter does not necessitate calibration as often as expected.
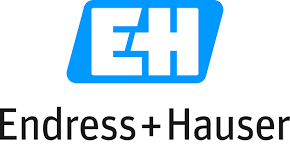
This information has been sourced, reviewed and adapted from materials provided by Endress+Hauser Ltd.
For more information on this source, please visit Endress+Hauser Ltd.