Almost all capacitive sensor applications are a measure of displacement (position change) of an object. This application details the specifics of making such a measurement and what is required to make reliable measurements in mirco- and nano-displacement applications.
Linear Displacement Measurement with a Capacitive Linear Displacement Sensor
Here linear displacement measurement refers to the measurement of the position change of an object. The specific focus of this article is linear high-resolution non-contact displacement measurement of conductive objects with capacitive sensors. Capacitive sensors can also measure non-conductive objects.
Related Terms and Concepts
A sensor configured for a linear displacement measurement is sometimes called a displacement meter or displacement gauge. At the micro- and nano-level, capacitive displacement sensors are suitable for displacement (change in position) measurements, rather than absolute measurements.
Displacement Versus Absolute Position
The capacitive sensor calibration shifts over time. This is mainly a DC offset in the output of the sensor. Sensitivity changes of the sensor are much smaller. Determining position changes requires a consistent sensitivity and is not impacted by long-term shifts in DC offset of the output. Displacement is normally measured as a result of some variable.
- Intentional Displacement: This is when an object is intentionally moved by a motion control positioning system. The non-contact displacement measurement indicates the accuracy of the intended displacement of the object.
- Part Dimension: The system configuration is done with a known good “master” part after which the master part is replaced with a part for test. Differences in the dimensions of the test part relative to the master part are indicated as a displacement measurement by the capacitive displacement sensors.
- Temperature: The object’s position is measured at an initial temperature. The temperature of interest is changed and a displacement measurement indicates the magnitude of the position change due to temperature.
- Vibration: Linear displacement measurements are done in real time with the help of capacitive displacement sensors with an oscilloscope or data acquisition system to indicate the displacements of the object and their frequencies.
- Pressure: Air bearings and other fluid bearings can operate at different fluid pressures. Displacement measurements of the object at different pressures indicate the actual behaviour of the machine as the pressure changes compared to its intended operation.
- Wear: As bearings and slides wear, non-contact displacement measurements of the moving parts will indicate increased movement in unintended directions.
Linear Displacement Measurements are Relative Measurements
Linear non-contact displacement measurements are relative measurements and indicate the change of an object’s position from an initial location in one or more linear axes. A separate capacitive displacement sensor channel is required for each axis of linear displacement measurement.
Basic Linear Displacement Measurement with a Capacitive Non-Contact Displacement Sensor
The mounting of a capacitive displacement sensor is done in a fixture such that the object to be measured is within the measurement range of the sensor. If the sensor includes a zero (offset) adjustment, the sensor may be calibrated as such at this location to make for easier interpretations of linear displacement measurements when the object moves.
Calculating Displacement from Capacitive Displacement Sensor Output
Capacitive sensors for measuring displacement have a “sensitivity” specification which specifies the amount of change in the output relative to a given change in the target position. For analog voltage output sensors, this value is given in Volts per unit-of-distance or length (e.g. mm, inch etc.). For digital output sensors, this value is given in Counts per unit-of-distance.
Formula for calculating displacement from a sensor output:
Displacement = Output Change/Sensitivity
Analog Voltage Output sensors:
Output Change = Volts; Sensitivity = Volts/Unit of distance
Digital Output sensors:
Output Change = Counts; Sensitivity = Counts/Unit of distance
.gif)
Figure 1. At the micro- and nano-level, capacitive displacement sensors are best suited to displacement (change in position) measurements, rather than absolute measurements.
Micro-displacement Errors and Concerns
High-Performance capacitive displacement sensors are normally used for measurements of micro-displacements. When measuring very small displacements at the micro-displacement level, error sources that are normally inconsequential become a more significant factor.
Thermal Effects
Thermal expansion and contraction of the mounting system that holds the capacitive non-contact displacement sensors will introduce errors into the measurement. As the fixture expands or contracts, the sensor may move toward or away from the target object.
Micro-displacement Sensor Mounting
Added to thermal concerns, mechanical stability is more complicated at the micro-level. The capacitive displacement measurement sensors must be held firmly in place by the mounting system. A simple set-screw type mount may not be sufficiently stable when measuring displacement at the micro-level.
.gif)
Figure 2. Set-screw mounting locks the probe along the probe’s axis, but there may still be movement in the other two axes, especially at the micro- and nano-levels.
.gif)
Figure 3. A clamp mount is a more stable mount than a set-screw mount. But at the micro- and nano-levels, form errors can result in only a two-point clamp much like a set-screw mount.
.gif)
Figure 4. The ideal mounting configuration for positioning a cylindrical linear displacement sensor.
There are different methods for mounting a cylindrical linear displacement sensor. Using a set-screw in a through-hole mount only holds the probe at two points – the set-screw and the point opposite the set-screw. A better, but not perfect linear displacement sensor mounting scheme is a clamp type mount.
An optimal mounting system uses a three-point clamp with each point covering some significant length along the axis of the probe. The three-point clamp system begins with a typical clamp mounting configuration but also removes material from the clamping hole between three points 120° apart.
Other Capacitive Displacement Sensor Mounting Considerations
The “spot-size” of capacitive displacement sensors is about 130% of the sensing area diameter. For this reason, they are generally immune to any surrounding objects, and they can be mounted flush with the mounting bracket surface. The only exception is calibrations that use an extremely long measurement range relative to the size of the sensing area; this does not apply to any off-the-shelf calibrations available for Lion Precision probes.
Environmental Considerations
Linear displacement measurements with a capacitive sensor must be made in a clean environment. The displacement measurement will be affected by anything (other than air or vacuum) in the space between the capacitive probe and the object it is measuring.
Typical changes in humidity do not have a significant effect on capacitive displacement measurements. Extremes of humidity will affect the output with a worst case being condensation on the probe or target.
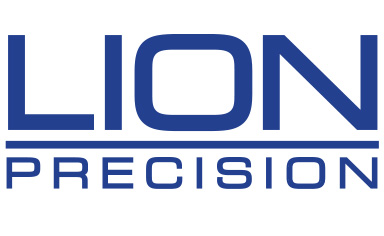
This information has been sourced, reviewed, and adapted from materials provided by Lion Precision.
For more information on this source, please visit Lion Precision.