This article will examine how free space radars and hydrostatic level sensors have evolved and how they are used in the food and beverage industry.
Hydrostatic level sensors are used in 90% of continuous level measurements, but the landscape is shifting due to the demand for increased accuracy in plant mass balance and inventory-related applications. This has led to a migration towards free space radar, which offers superior measurement precision.
Free space radar has experienced more rapid and extensive advancements among the two options compared to hydrostatic level sensors.
One notable advantage of free space radar is its resilience to temperature, often seen in food and beverage applications due to clean-in-place, pasteurization, and thermal processes.
Unlike hydrostatic sensors, which rely on measuring the pressure of the liquid column (P = density x height of liquid column), free space radar operates by examining the media surface, making it impervious to changes in density.
Another recent innovation involves adopting 80 gigahertz radar technology, resulting in a narrower beam angle that enables radar placement closer to tank walls. This feature allows for more precise level targeting, minimizing interference from internal obstructions within the tank.
The radar can be installed flush to the surface or in nozzles, facilitating easy cleaning—a crucial aspect for maintaining tank cleanliness in the food industry.
While free space radar has surpassed hydrostatic level sensors in terms of advancement, it is worth noting that the latter has also undergone significant improvements.
Notably, there have been enhancements in sensor stability and temperature compensation, which are particularly important in the food and beverage sector, where drastic temperature changes occur during the transfer of cold and warm products.
When selecting measurement instruments, these factors should be considered, as not all pressure sensors are optimized to handle temperature fluctuations, which may lead to substantial zero-point and measurement errors.
What are the Differences Between Free Space Radars and Hydrostatic Level Sensors?
The technologies involved in level measurement differ significantly. One approach relies on measuring the weight of a hydrostatic column above the level sensor to determine the level. This method employs gauging techniques.
In contrast, a free space radar is positioned at the top, observing the surface and utilizing time-of-flight (ToF) technology for level measurement.
While the ultimate measurements may vary slightly, some users aim to minimize or avoid process connections at the tank's bottom to mitigate the risks of leaks or contamination.
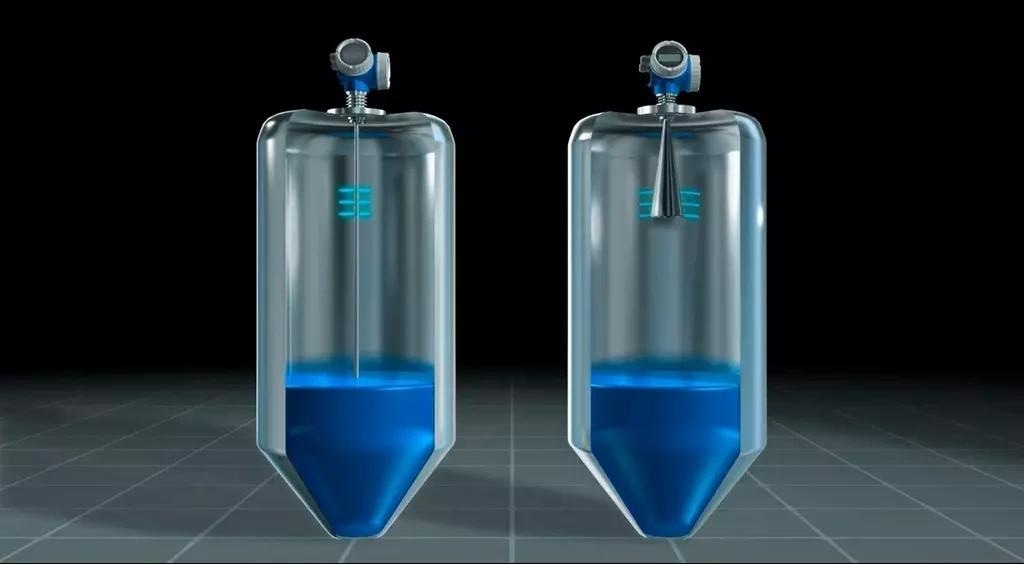
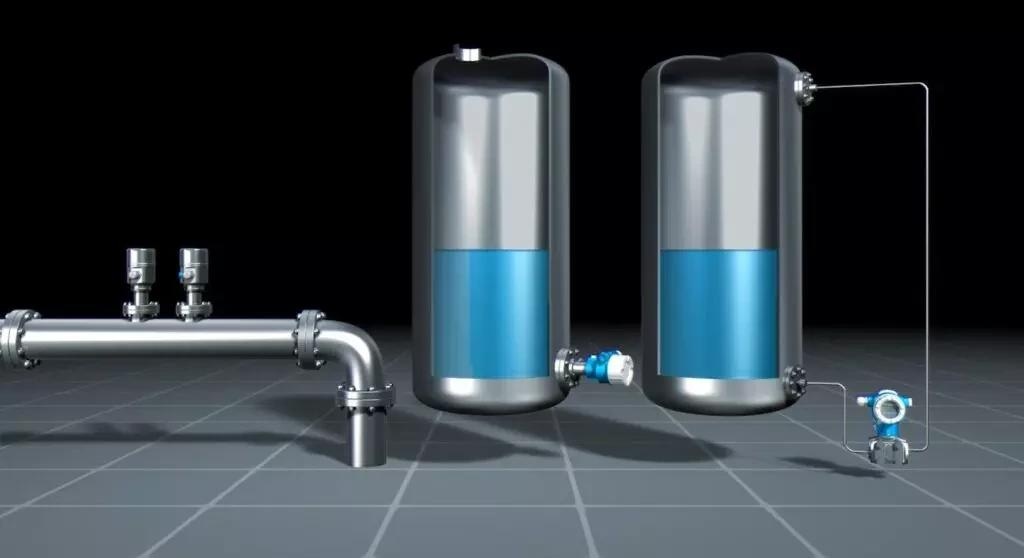
Time-of-flight (top) and hydrostatic (bottom) measuring principles are used in various industries. Depending on your application, your needs may vary for instrumentation and process connections. Image Credit: Endress+Hauser Ltd.
What are the Advantages of Using Free Space Radars and Hydrostatic Level Sensors for Plant Mass Balance?
Both technologies offer distinct advantages. Free space radar and hydrostatic level sensors are highly reliable for plant mass balance. In terms of the benefits offered by free space radar, it is typically mounted on the tank’s top, reducing its exposure to external washdowns and accidental damage.
The need for frequent replacement of hydrostatic sensors often arises due to mishandling during installation or calibration, leading to damage to the pressure-sensitive membrane. Radar technology eliminates this risk.
Hydrostatic level sensors have long been recognized for their advantages in general-level measurement applications, such as balance tanks, buffer tanks, and cook kettles.
While the author considers radar the more dependable measurement technology, there are valid reasons to consider both.
How are these Sensors Applied for Inventory Purposes?
When it comes to inventory assessment, utmost accuracy is usually sought. However, having precise knowledge of the exact inventory quantity is crucial. Both principles offer high levels of accuracy.
The percentage of the measured range determines hydrostatic accuracy and can typically achieve 0.1% accuracy. Realistically, in an installation, accuracy between 0.1% and 1% can be expected, depending on the height of the measured range.
With a radar unit, an accuracy of 1/24″ to 1/12″ (one to two millimeters) can be achieved, irrespective of the tank's height.
In What Instances Should I Choose One of These Tools Over the Other?
For the tank type and measurement method, if the objective is to achieve high accuracy for inventory management, the recommended primary option would be the free space radar.
Storage or buffer tanks that require superior performance, such as final product tanks preceding filling machines, benefit significantly from their high accuracy.
This accuracy is significant when balancing product volume with packaging materials or aligning filling machine schedules to match the available product closely.
For smaller balance tanks, process tanks, or surge tanks where accuracy is not highly critical, the hydrostatic level sensor is the preferred choice to consider initially. The hydrostatic option is recommended for applications involving heavy foam, agitation, or turbulence.
In the case of smaller surge tanks that demand swift operation but do not require high accuracy, hydrostatic sensors usually provide the best solution.
How Do I Know If I Am Optimally Using My Free Space Radar Or Hydrostatic Level Sensor Technology?
The process begins by determining the desired performance, the specific requirements, and the application parameters.
The challenges associated with installations, cleaning, maintenance, connectivity, and other relevant factors must be addressed. Ultimately, if the chosen solution functions appropriately, it ensures optimal utilization of technology.
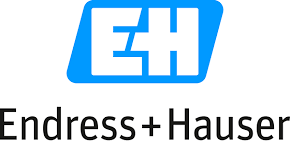
This information has been sourced, reviewed and adapted from materials provided by Endress+Hauser Ltd.
For more information on this source, please visit Endress+Hauser Ltd.