In this interview, AZoSensors speaks to Tekscan's Raul Oreste and Calspan's Mateo Gladstone about pressure mapping technology and how it can potentially change the face of the tire industry.
How has the tire industry changed over recent years, and what challenges has this posed for manufacturers?
Calspan:
The tire industry has significantly changed in recent years, particularly in the areas of improved performance, safety, and durability. Run-flat tires, self-sealing tires, and low rolling resistance tires have gained popularity due to their ability to enhance vehicle safety and fuel efficiency.
An optimally designed tire influences the driving experience, including safety, shock absorption, and fuel economy. With the increasing popularity of electric vehicles (EVs) tire manufacturers must adapt to meet certain demands. For example, tire design can greatly impact charge range.
The ever-increasing demands of the automotive industry require manufacturers to address reduced road noise, extended range, and optimized rolling resistance to enhance efficiency. To keep pace, tire manufacturers must continually focus on research and development (R&D) and testing, going beyond the testing methods they have traditionally relied on.
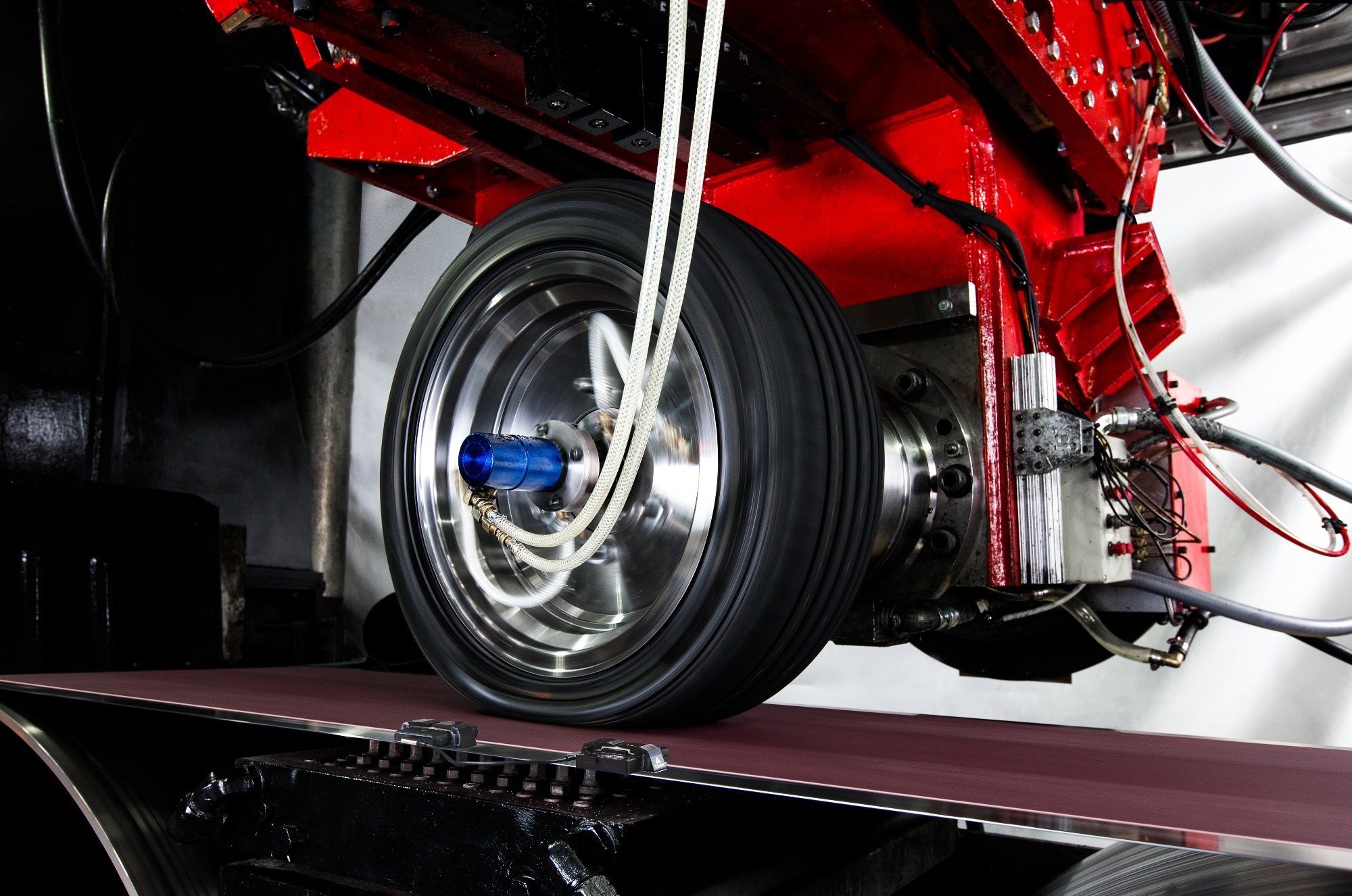
Image Credit: Tekscan
How can robust tire analysis help manufacturers meet and overcome these challenges?
Calspan:
Numerous considerations are involved in tire development and design, and manufacturers require access to test and measurement technology that can swiftly provide crucial insights that might otherwise remain unrealized.
One specific assessment area in particular can give researchers vital data concerning a tire's strengths and weaknesses. Critical components of a vehicle's performance, such as load-bearing, cornering, traction, braking, and acceleration, are all interconnected with the tire contact patch – the portion of the tire tread that comes into contact with the road or driving surface.
As the tire touches the surface, it undergoes deformation in multiple directions. Understanding the pressure distribution from this deformation when the tire is in motion proves invaluable for tire manufacturers who dedicate numerous hours to research and development to optimize tire materials for the desired stiffness and construction.
The method we employ for tire analysis to assess this is known as Dynamic Contact Patch Pressure testing, with pressure mapping playing a pivotal role in this process.
What is the tire contact patch and why is it important to understand?
Calspan:
The tire contact patch refers to the area of the tire that makes direct contact with the road surface. When a vehicle rests on its tires, the only part of the vehicle in contact with the road is the contact patch, typically just a few square inches in size for each tire.
Understanding the importance of the tire contact patch is crucial due to its significant influence on various aspects of a vehicle's performance and safety. Take traction, for example. The contact patch serves as the primary point of contact between the vehicle and the road, determining the amount of grip or traction the tires can generate. Adequate traction is essential for acceleration, braking, and cornering performance.
Contact patch also influences handling and stability. A larger contact patch allows the tire to distribute the vehicle's weight more evenly, improving cornering capabilities and reducing the risk of skidding or sliding during specific maneuvers. It also enhances braking effectiveness by reducing the stopping distance required.
The contact patch's size and condition also impact tire wear and longevity. Uneven wear patterns can indicate suspension or alignment issues that require attention. Additionally, the contact patch can affect fuel efficiency. A properly inflated tire with an appropriate contact patch experiences less rolling resistance, reducing fuel consumption. These examples illustrate how the contact patch directly affects safety and performance.
What is pressure mapping and how can it be used in tire analysis?
Tekscan:
Pressure mapping is a technique used to measure and visualize the pressure distribution between two mating surfaces. It is often used in manufacturing processes to optimize the design and performance of products.
Research and development allow engineers to study how pressure distribution affects various materials, products, or surfaces.
A pressure mapping system consists of three elements: a thin piezoresistive sensor (which comprises an array of individual sensing points to enable high-resolution output), data acquisition electronics, and software.
At Tekscan, we have more than 200 standard sensors in varying form factors and pressure ranges, and we also customize sensors to customers’ unique specifications. The electronics scan thousands of sensing points within each sensor and relay data to the software, which displays the pressure distribution data on the screen in multiple formats.
The tire industry has extensively used Tekscan technology for over 25 years to measure the detailed tread pattern of static or slow-rolling tires.
Incremental updates were made to Tekscan’s core technology for the new High-Speed TireScan™ System, which Calspan applies in its DCPP tests to measure the shape and pressure distribution of the contact patch of fast-moving tires.
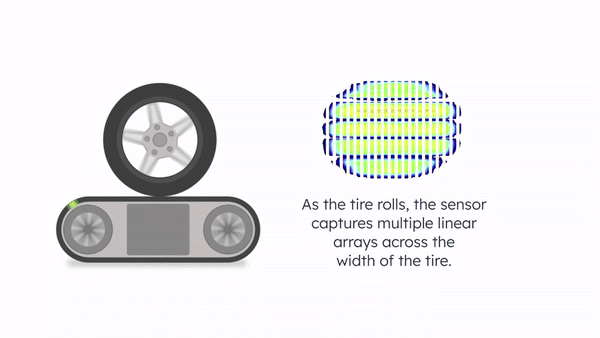
Image Credit: Tekscan
What are some of the advantages of this method of tire analysis, and how does it help overcome the challenges of conventional tire testing?
Calspan:
While there are multiple techniques for measuring the contact patch while the tire is in a static state, dynamic measurements have consistently been a challenge to capture.
Over the years, tire manufacturers have relied on several systems and approaches for evaluating tire contact patch pressures. There are a range of limitations to these methods. Ink footprints, for example, do not account for rolling tires/dynamic forces or provide pressure. With on-road testing, there are too many uncontrolled variables, which lead to poor measurement repeatability.
Camera systems using glass plates are not ideal for this type of measurement because the low surface friction of the glass changes how the rubber interacts with the road surfaces (especially at high slip).
Drum testing has been widely used, but an obvious limitation is that the curved road surfaces of the drum change the contact patch shape and pressure distribution, making it challenging to predict real-world performance on flat surfaces.
As the tire quickly spins, in-plane friction forces across the tire patch, plus centrifugal forces, change the tire patch's shape, changing the tire's performance. The High-Speed TireScan™ System is a reliable, repeatable method for measuring a tire's Dynamic Contact Patch Pressure (DCPP) on a flat track machine.
Tekscan:
We were eager to collaborate with Calspan to pioneer a new method for adapting and applying our technology for robust tire analysis. The piezoresistive sensor can measure the vertical load of the tire on a flat track in various load conditions.
The electronics are housed in lightweight wireless devices that scan the 128-point sensor array at up to 20 kHz and can capture tire contact patches at speeds up to 265 km/h. Finally, the software streamlines data collection and creates an image of the tire footprint or contact patch.
How does Tekscan’s High-Speed TireScan system contribute to this process?
Tekscan:
To obtain a contact patch image, the High-Speed TireScan™ system captures multiple linear arrays across the tire's width as it rolls across a single-sensing column. Users input the tire's velocity and load, and the software generates a contact patch image or footprint that displays the shape and pressure distribution of the tire. The columns in the footprint image represent different moments in time. The system uses the velocity input to set the aspect ratio of the columns to ensure the tire footprint image accurately depicts the contact patch.
The High-Speed TireScan electronics are mounted to the edge of the belt surface using a mounting sleeve adhered to the steel belt. The sensor is then mounted perpendicularly across the tire path with double-sided tape. Despite its thin design, the sensor has a durable construction that can endure 15 kN of shear force from slip angle tests and can measure the contact patch at speeds up to 165 mph. It can withstand pressure loads of more than 600 psi.
Calspan:
Measuring tire contact patch pressure on a flat track allows for accurate, repeatable, high-speed measurements of the contact patch. In such a test environment, variables can be isolated and introduced in a controlled manner to ensure a proper correlation between operating conditions and contact patch pressure behavior. At our test facility, the tire test rig controls operating conditions, such as load, slip angle, acceleration, braking, camber angle, velocity, inflation pressure, and temperature.
How can this data be applied in practice?
Tekscan:
A prime use case example for the High-Speed TireScan™ system is benchmarking similar-style tires from different manufacturers. The system provides unique insights into how the tire design, material, reinforcements, and construction yield different tire patch distributions among tires from other manufacturers.
For example, in one test situation comparing three summer performance tires, the High-Speed TireScan™ system showed that the contact patch length and width increased as the load on the tire increased. Some tires showed significantly higher loading on the edge from sidewalls bearing more load at very high loads.
Calspan:
There are some valuable insights to be gained from this technology. We were able to observe a unique phenomenon during an extreme cornering test. The dynamic contact patch measurement revealed a gap in pressure within the contact patch of a tire experiencing 9 kN of shear force from cornering.
We hypothesized that lateral forces caused the tire's belt package to buckle, lifting part of the tread off the road and resulting in no contact. We verified our theory by synchronizing thermal video with the High-Speed TireScan™ data. A lower temperature was detected in the sensor area that had no pressure, indicating a lack of frictional heating, in turn verifying a lack of contact.
What should a manufacturer do if they are interested in utilizing this technology to test their tires?
Tekscan:
We encourage any manufacturer or researcher to contact us if they want to understand dynamic contact patch pressure. We are happy to discuss your application, and if there is interest, we could even coordinate with Calspan to arrange a demonstration with your tire.
Calspan:
Yes, we periodically conduct dynamic patch pressure tests at our facility, and these tests can offer incredibly insightful data on how your tire behaves under dynamic conditions.
About the Speakers
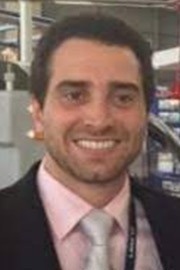
Raul Oreste has more than twelve years of experience spanning business development, product management, and engineering across diverse sectors, from aerospace to manufacturing. As a Product Manager at Tekscan, his focus is on working with Tekscan's customers to understand their applications and craft a roadmap for new products that cater to their surface sensing requirements.
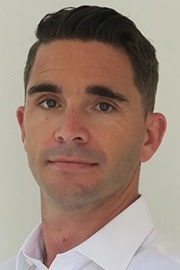
Mateo Gladstone is a tire testing and modeling expert with an excellent track record of measuring and understanding tire performance in the Automotive and Motorsport fields. A few highlights of Mateo’s many accomplishments are the development of an on-vehicle tire testing platform for measuring tire data on any type of road surface, leading tire development projects within a premium European car manufacturer. As director of R&D at Calspan, Mateo works with tire and vehicle manufacturers worldwide to enhance their tire testing and modeling programs. He holds an MSc in Motorsports engineering.
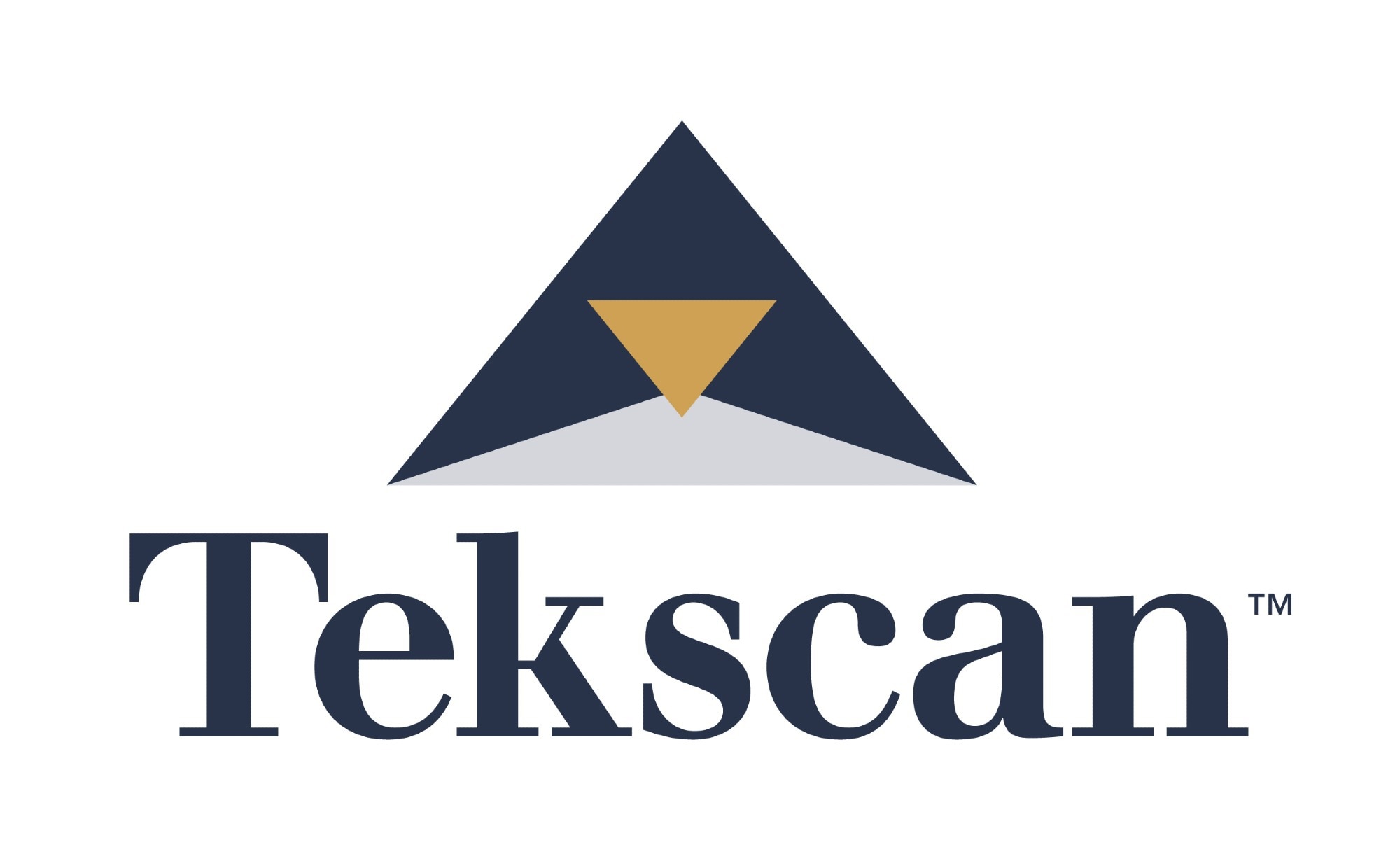
This information has been sourced, reviewed and adapted from materials provided by Tekscan, Inc.
For more information on this source, please visit Tekscan, Inc.
Disclaimer: The views expressed here are those of the interviewee and do not necessarily represent the views of AZoM.com Limited (T/A) AZoNetwork, the owner and operator of this website. This disclaimer forms part of the Terms and Conditions of use of this website.