Interview conducted by Alex SmithJul 12 2023
In this interview, AZoSensors talks to Xing Fei He from Teledyne about line scan imaging, its advantages, emerging developments, and the future of the field.
What is line scan imaging and how is a line scan image created?
Line-scan cameras use one-dimensional linear arrays, which allow fast transfer of image data from the sensor to the camera and then to the host computer at speeds reaching hundreds of kilohertz. The second dimension results from the motion of either the object being imaged or the camera.
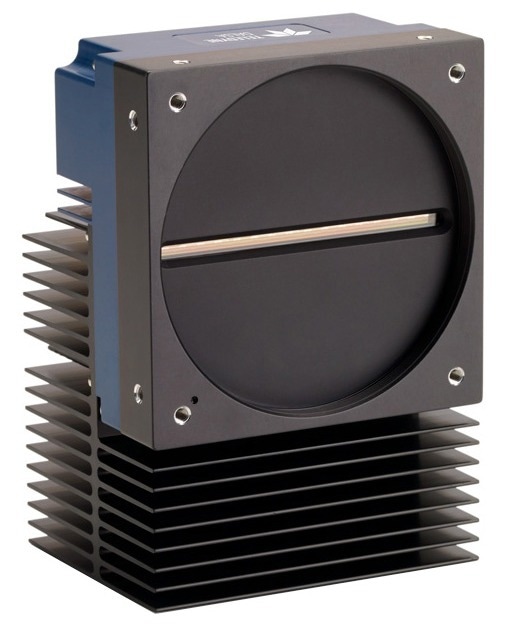
Image Credit: Teledyne DALSA
What are some examples of line scan imaging devices?
The most common example is a fax machine.
How are these devices used?
Two-dimensional images are acquired line by line by successive single-line scans while the object or camera moves (perpendicularly) past the line of pixels in the image sensor.
For a given field of view, one 2k line scan camera cost-effectively provides the exact resolution as 4 mega-pixel area scan cameras without image smear or the redundant processing of frame overlaps.
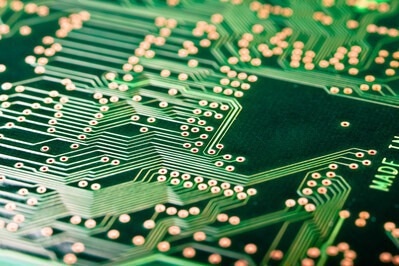
Image Credit: Teledyne DALSA
How have line scan image devices changed over the last decade?
Line scan cameras can now capture and merge multiple images to achieve high resolution in low light. Recent advancements also enable the incorporation of numerous visible and nonvisible spectral bands to enhance vision capabilities.
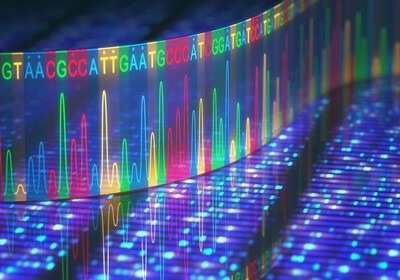
Image Credit: Teledyne DALSA
Time Delay Integration (TDI) has become a proven technology for high-speed imaging in light-starved conditions. TDI uses multiple exposures to collect more photons while maintaining low read noise. More and more high-speed applications today require time delay integration, especially if increasing light intensity on the imaged object is not an option.
Contact image sensor (CIS) technology has been around for a while, but developments in this area may advance line scan technology even further. CISs are highly integrated, compact, and valuable when space is premium. The working distance of a CIS may be as little as 10~15 mm, and in some cases, it can be larger.
What is Teledyne DALSA’s history with these devices?
Our latest Linea2 4K Multispectral 5GigE line scan cameras capture high-resolution RGB plus Near Infrared (NIR) multispectral images to reveal invisible features that cannot be detected using visible lighting alone. This makes it ideal for identifying hard-to-see defects, contaminants and security features in applications such as automated optical inspection, printing inspection, optical sorting systems, material grading and inspection, web inspection and many other machine vision applications.
The Linea SWIR allows users to detect light in the short-wave infrared spectrum to identify details below the surface while inspecting fruit and other foods. It can also determine water content, an essential factor for gauging food quality. Linea SWIR can also be used in solar cell inspection.
Our Linea HS-16K BSI is based on multi-array charge-domain CMOS TDI technology, offering advanced capabilities including mono/HDR, color, multifield, and super-resolution imaging for imaging applications, such as wafer, flat panel display and electronic packaging inspection as well as photoluminescence and life science imaging.
AxCIS Contact Image Sensors combine all-in-one sensors, lenses, and lights, offering a lower-cost inspection system for many demanding machine vision applications. AxCIS delivers 120 kHz line rates for mono, 60 kHz x 3 for color, at 900 dpi resolution, so defects can be detected with unprecedented precision. Its unique staggered sensor design covers the whole field of view without missing pixels, providing a 100% seamless image without any interpolation.
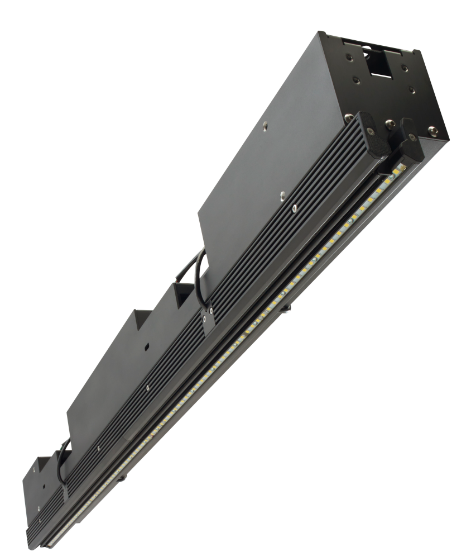
Image Credit: Teledyne DALSA
What are some of the line-scan devices in the Linea range offered by Teledyne DALSA?
Our Linea line-scan product portfolio consists of the following:
- Linea is our original line scan camera with resolutions from 2K to 16K, line rates to 71 kHz.
- Linea2, with quadlinear color plus NIR multispectral technology, offers a 5GigE interface with five times the bandwidth of the Linea GigE camera.
- Linea Lite is designed with a 45% smaller footprint than the original Linea. The Lite version offers superior color fidelity with a GigE Vision® interface.
- Linea ML offers multiline technology, including options for monochrome/HDR, color, and multispectral imaging.
- Linea SWIR is our short-wave infrared GigE line scan camera, allowing customers to see their products like never before.
- Linea HS 16K BSI offers enhanced sensitivity and is ideal for Near Ultraviolet (NUV) and visible imaging applications.
How does Teledyne DALSA help clients choose between these products?
The three most important considerations when choosing a line scan camera are sensitivity, resolution, and line rate.
For sensitivity, we ask, “Is the camera getting enough photons to perform the machine vision task?” It is usually difficult to answer this question only from component specifications, as too many variables exist. In practice, we estimate the light intensity needed, specify more light intensity than our estimate, and then verify that we have the required sensitivity by testing.
The field of view (FOV) and minimum defect size must be specified to determine camera resolution. The camera should have enough resolution to have at least 3 or 4 pixels “covering” the minimum defect size.
The line rate is set by the FOV, object speed, and object pixel size. For example, if the FOV is 12”, the part speed is 60” per second, and you are using an 8K (8,192 sensor pixels) camera, then: (Object pixel size in the FOV) = FOV/(camera resolution) = 12/8192 = 0.001465” object pixel size in the FOV Line rate needed: 60”/0.001465” = 40.956 kHz
What are the advantages of line-scan image devices?
- Very high speed
- Price/pixel–line scan offers much more cost-effective implementations of very high spatial resolution image capture.
- Dynamic range that can be much higher than alternative image capture methods
- High pixel fill factor (typically 100%) to maximize sensitivity
- Smear-free images of fast-moving objects without expensive strobing or cumbersome shuttering
- Processing efficiency – line scan imaging eliminates the frame overlaps required to build a seamless image. Frame overlaps represent redundant data that uses precious processing bandwidth, particularly in high-speed, high-resolution applications.
What are some of the challenges associated with this technology?
The trade-offs in line scan imaging usually relate to lighting and optics. The illumination must remain reasonably uniform over the entire field of view.
Integration times in line scan imaging are typically very short, so illumination intensity must be high.
Mechanical movement and alignment at high magnification imaging is also a challenge.
How does Teledyne DALSA address these challenges?
In-camera flat-field and lens shading correction are available on almost all of our cameras, which can compensate for poor uniformity.
Our high-sensitivity TDI line scan products offer 100x greater sensitivity than most comparable line scans to address illumination intensity.
What advancements to line-scan technology is Teledyne DALSA currently working on?
We continue to see the demand for high-speed and high-resolution line scan cameras for many industries, including automotive, manufacturing, and food and beverage. In addition, CMOS cameras continue to gain popularity with their small form factor, high-speed performance, and low power consumption. These cameras are increasingly used in applications where power consumption is a concern or space is limited.
About the interviewee
Xing-Fei He is a Senior Product Manager for Teledyne DALSA’s CCD and CMOS product lines. His areas of expertise include product imaging, display, and optoelectronics with emphasis on product planning, development, and rollout.
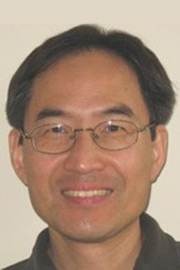

This information has been sourced, reviewed and adapted from materials provided by Teledyne DALSA.
For more information on this source, please visit Teledyne DALSA.
Disclaimer: The views expressed here are those of the interviewee and do not necessarily represent the views of AZoM.com Limited (T/A) AZoNetwork, the owner and operator of this website. This disclaimer forms part of the Terms and Conditions of use of this website.