Interview conducted by Olivia FrostJul 10 2023
In this interview, Daniel Haefliger, the CEO at Sateco Group, talks to AZoSensors about the current advancements in the prostheses industry, and how sensors are being integrated into prostheses.
Could you provide an overview of the current advancements in prostheses and how they contribute to improving the quality of life for individuals affected by trauma or accidents?
An increasing number of trauma cases and accident injuries are being observed worldwide. Prostheses can improve the quality of life for people after such drastic events in the long term and facilitate their reintegration into society.
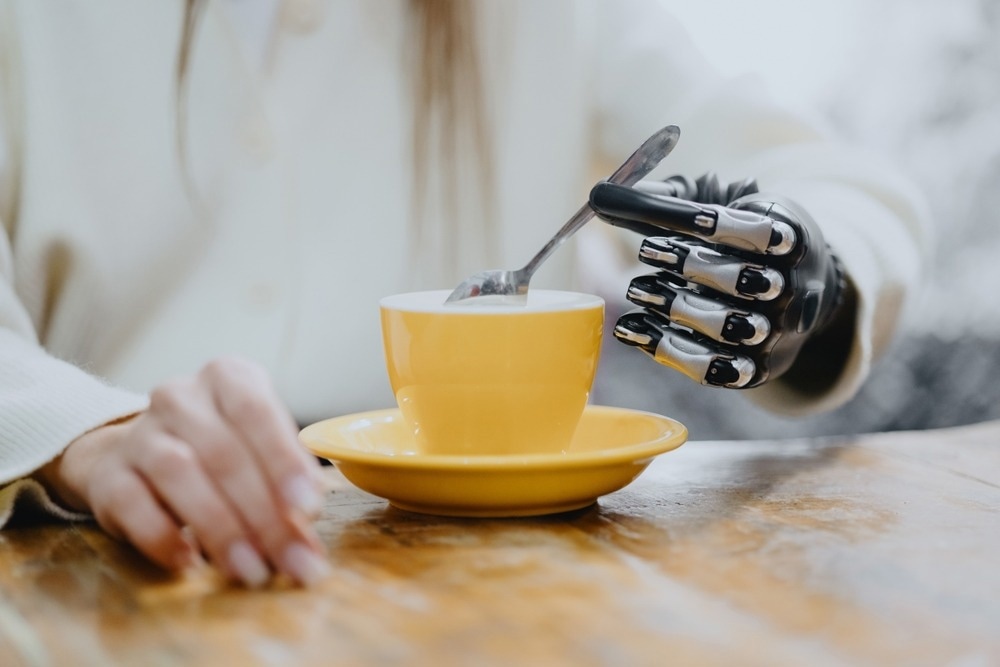
Image Credit: ShutterStock/My July
How have prostheses improved over the last decade, and what are the key technical developments that are driving the progress of novel prosthetic systems?
Technical advances towards lightweight materials with high mechanical stiffness as well as improvements in the programming of electromechanical interactive systems are currently fueling the development of novel systems that actively support the human musculoskeletal system. These systems are wearable and combine support structures with motors, sensors and control electronics.
What are some of the considerations that have to be taken when creating prostheses?
Prostheses operate at a moving interface between a flexible soft body and hard materials. The position between the two can vary during the use. This variation can create high wear on materials and the body. Special attention needs to be placed on the design and selection of materials to optimize mechanical load and wear resistance.
How are sensors being integrated into prostheses?
Various sensors can be used to measure the human movement sequence, for example to determine the position and acceleration of the limbs or the force between the limbs and the prosthesis. It should be noted that the sensor is in physical contact with the surface of the limbs and the prosthesis, especially when measuring mechanical interaction during the entire motion sequence.
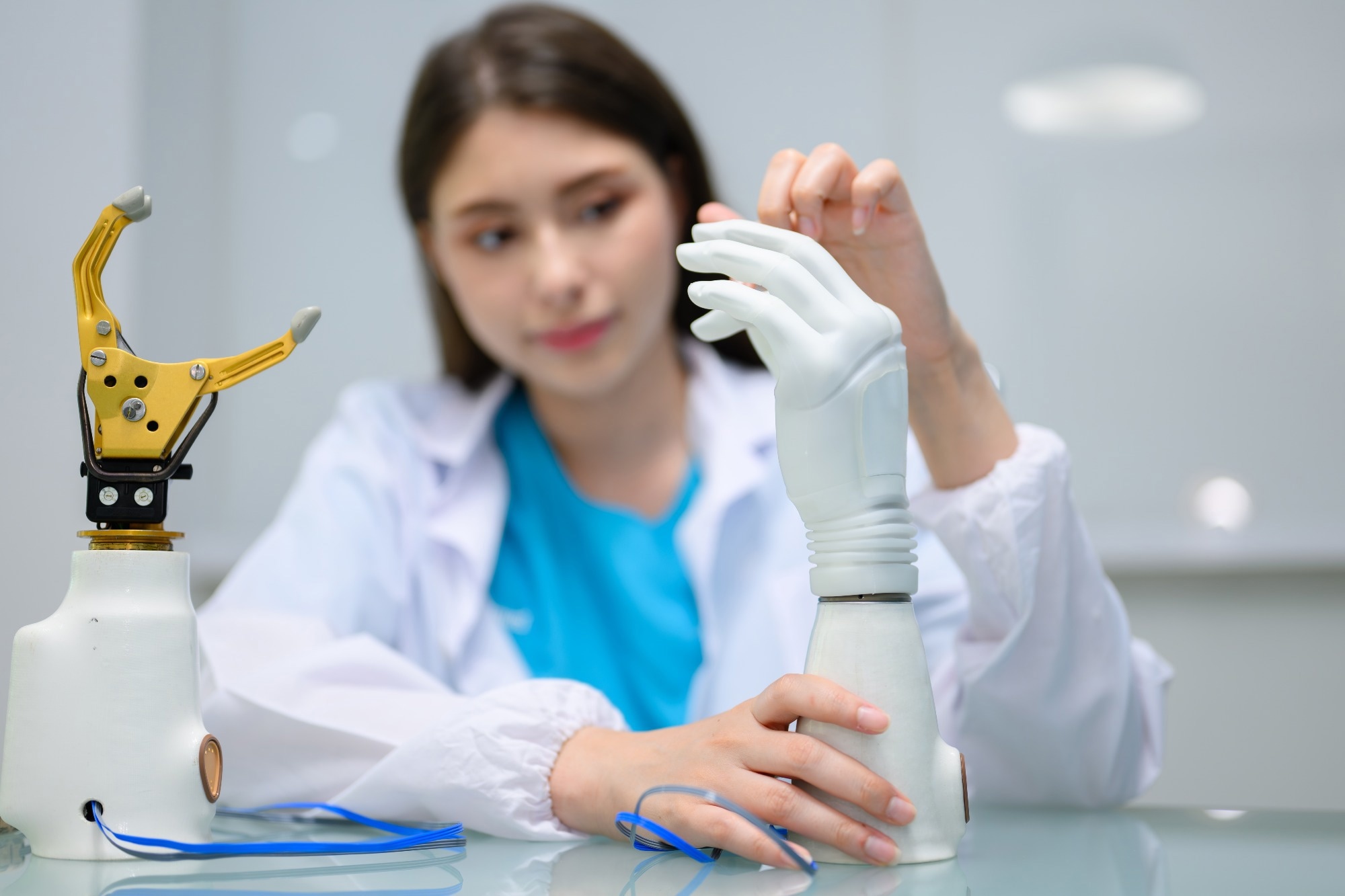
Image Credit: ShutterStock/1st footage
What are these sensors designed to do, and how does this help the user?
The system is designed to measure the wearer's movement at appropriate points, analyze the data, and control the impact on the human accordingly to effectively support the wearer's movement.
What are some of the different sensors used in this field, and what are their relative advantages and drawbacks?
A common technology for measuring forces in wearable systems is based on a force-sensitive resistance sensor. This sensor consists of at least two layers of foils with a conductive material embedded between them. Under the effect of force or pressure, the sensor is compressed in such a way that the electrical resistance of the sensor changes. This change in resistance can be measured at terminals of the sensor. In addition to resistance sensors, there are also force-sensitive foil sensors, which are based on the capacitive principle. In this case, the application of a force causes a change in the internal capacitance of the sensor, which in turn can be measured at terminals.
What are some of the challenges associated with the unification of sensors and prostheses?
Since both the human body and the prosthesis have a soft surface, this places particularly high demands on the sensor. It must be ensured that the sensor neither slips, detaches from one of the surfaces, or is compressed by them in such a way that it can no longer measure or is even damaged. The latter, in particular, can lead to sensor fatigue and permanent failure during repetitive motion sequences.
How does the Sateco Group tackle these challenges?
An example of a soft, flexible force sensor is represented by the SXTSC silicone force sensor. The sensor is made of elastic silicone and operates according to the capacitive measurement principle. The elastic mechanical structure allows the required flexibility in the installation and use of the sensor in a prosthesis. Silicone is known to be an ideal material for medical applications because it is chemically inert and odorless. In addition, the material is pleasant to wear on the skin and can be ergonomically shaped thanks to its elastic behavior. The elasticity of the material moreover allows for repetitive motion sequencies and thereby enhances the durability of the sensor.
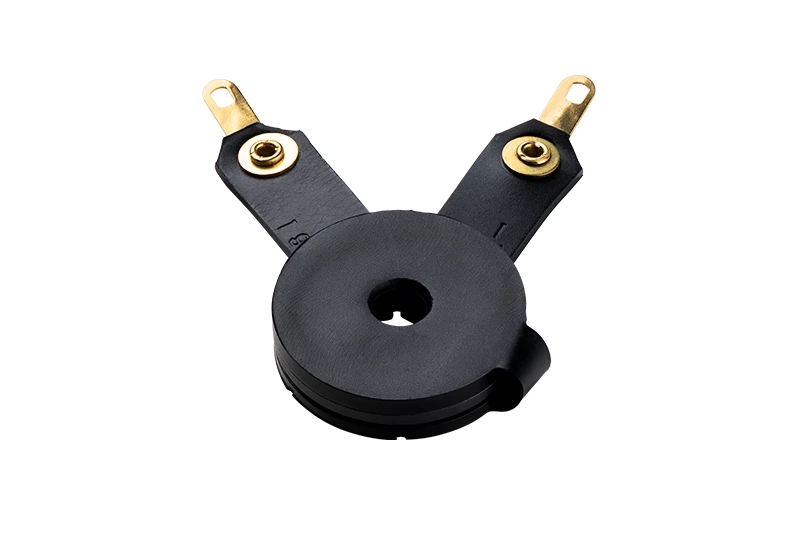
Image Credit: Sateco Group
What are some of the wearable neuroprostheses currently in development? Why are these unique systems?
The areas of application for soft sensors are very diverse. For example, the sensor can be installed in the sole or footrest of a walking prosthesis to analyze the patient's gait. In this case, several sensors are installed at different points on the sole. The rolling behavior of the foot, for example, can be tracked by cleverly selecting the installation points. This rolling behavior serves as a control variable for the prosthesis, which therapeutically influences the posture of the impaired person accordingly. The sensor is already being used in walking prostheses for neurologically impaired persons and is being tested for use in orthoses designed to correct the chewing gait of children.
Other applications are potentially in rehabilitation devices, e.g. for hands. Here, traumatized hands are treated using an active system. Sensors in gloves can monitor and control the grasping process, training local fine motor skills.
As advancements in force sensor technology continue to unfold, what future possibilities do you envision for prosthetic systems? How might these advancements revolutionize the field of prosthetics?
Artificial Intelligence is playing an increasingly important role in medicine technology. The core element of a novel neuroprosthesis is an intelligent shoe sole in which several SXTSC silicone force sensors are installed. These provide data on walking behavior, which is analyzed by an algorithm based on artificial intelligence. This drives a system of neuromuscular electrostimulation electrodes, which is thus able to reproduce functional movements in a personalized and safe manner. This compensates for deficiencies in the sensorimotor performance of the musculoskeletal system.
About Daniel Haefliger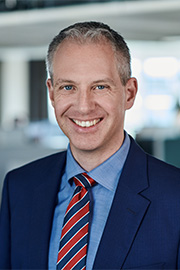
Daniel Haefliger is the CEO of Sateco Group. Haefliger is also a member of the Executive Board of a growing, Swiss/international medium-sized supplier of the global automotive industry.
About Sateco Group
The Sateco Group is one of the world's leading manufacturers of keypads, and silicone sensors. Sateco combines years of know-how and innovative technology with customized solutions, and it sets standards for creating controls and switches. This Swiss family-owned company with approx. 800 employees maintains subsidiaries in Europe, the U.S., and Asia. With consistent quality management and immense innovative strength, Sateco creates tangible added value for its prominent customers from many different industries.
For more information, please visit satecogroup.com
Disclaimer: The views expressed here are those of the interviewee and do not necessarily represent the views of AZoM.com Limited (T/A) AZoNetwork, the owner and operator of this website. This disclaimer forms part of the Terms and Conditions of use of this website.