For decades, industrial and service robots have been heavily reliant on vision systems and inertial sensors to perceive and interact with the world around them. However, these modalities lack the critical human sense of touch.
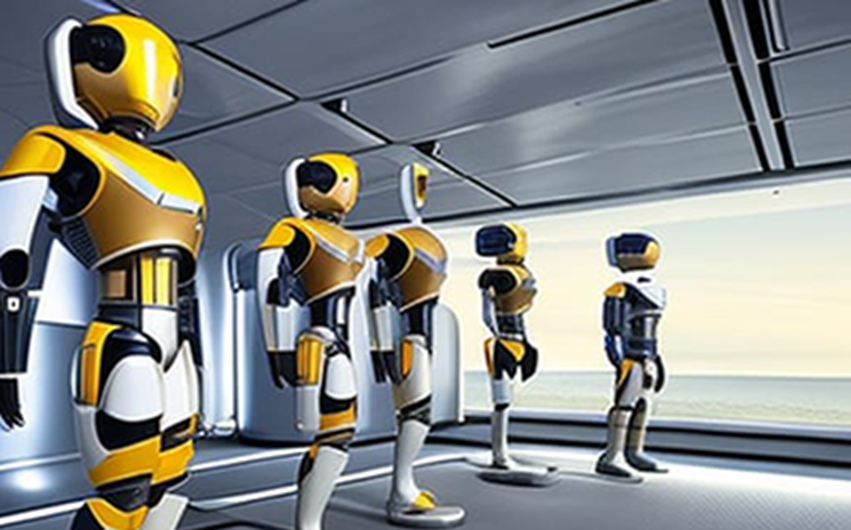
Image Credit: Superior Sensor Technology
Robots that are only equipped with cameras and accelerometers do not have the capacity to collect data on surface textures, detect tactile physical forces, or acquire proprioceptive feedback on their movements and joint positions.
This lack of tactile awareness substantially limits the robots’ ability to move adaptively through complex environments, handle objects with dexterity, and respond to physical contact in a safe manner.
Pressure sensors can be used to deliver crucial tactile feedback to robots to enhance their abilities. Continuous monitoring of pneumatic and hydraulic pressures within robotic joints and actuators provides robots with proprioceptive awareness of their own motion and torque exertion.
This feedback allows the advanced control of movements as well as targeted joint forces to be applied.
Covering robot surfaces with conformable, flexible pressure sensor arrays produces an artificial sense of touch. The skin-like pressure-sensing layers detect and map external forces from contact, human interaction, or collisions, allowing the robot to respond to such forces.
With enough pressure data integrated into control loops, robots can achieve human-like dexterity and adaptability. Tactile pressure feedback progresses robotics toward safe and seamless collaboration with human coworkers in factory settings.
This also holds great promise for robotics in high-risk environments such as healthcare, defense, disaster response, and space exploration, where blind automation is inadequate.
Pressure Sensor Applications in Robotics
Pressure sensors serve a fundamental function in modern robotics, yet they are often undervalued.
Pressure sensors provide continuous monitoring of internal pneumatic and hydraulic pressures, external forces, and environmental conditions. This offers critical feedback to robots to enhance internal monitoring, dexterous movement control, environment interaction, and tactile sensing.
A crucial application is proprioceptive sensing, i.e., utilizing pressure measurements inside joints to calculate the applied torque and forces. This information on the robot’s motion and loading allows for far more precise control, greatly enhancing manipulation capabilities and stability.
Tendon-driven robot designs use pressure sensors for measuring tendon tensions, which directly correlate to the force produced at the joints. More conventional robotic techniques install load cells to measure joint pressure differentials and infer the torque.
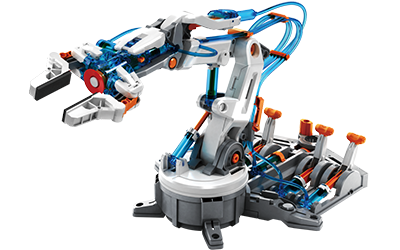
Example of a hydraulic robot arm. Image credit: Superior Sensor Technology
Some advanced systems utilize ultra-miniaturized MEMS pressure sensors applied directly to robot joints to provide high-resolution proprioceptive feedback. This pressure-sensing method is comparable to biological proprioception and enables robots to be aware of their own movement and loading conditions.
Likewise, integrating pressure sensors into the exterior skin of a robot exterior offers tactile feedback regarding contact forces. Large sensor arrays with multiple individual pressure sensors help map the distribution and magnitude of forces across the robot’s body.
Such arrays enable the robot to form suitable reactions to physical contact, including a gentle touch or a damaging collision. These tactile skin systems utilize conformable and flexible pressure sensor matrices to provide robots with sophisticated environmental awareness and a human-like sense of touch.
Other environmental interactions utilize differential pressure sensors for the detection of collisions. By measuring fluctuations in pressure inside fluid-filled bladders, sensors can be used to detect impending impacts and help initiate bracing maneuvers.
This collision-sensing technique also works for soft-bodied robots that lack a solid frame. By controlling contact forces, pressure sensors further help robots react safely if they or a human collide.
Internal pressure sensors monitor the hydraulic and pneumatic systems that enable movement. Abnormal drops in pressure allow the detection of leaks and enable repairs to be conducted promptly before total failure.
Flow sensors that utilize differential pressure principles can monitor pump and motor operation. Changes in height and altitude are also detected from pressure differences as the robot ascends or descends. This sensory feedback supports reliable and stable mobility.
Additionally, pressure sensing allows robots to be weatherproofed if they operate outdoors or in demanding environments.
The installation of micro-machined pressure sensors with waterproof membranes inside the robot body enables any water ingress from rain or flooding to be quickly detected before any electrical components are damaged. Subsequently, the robot can act to protect internal components or signal for assistance.
Technology Innovations Driving Progress
Several major advances in technology facilitate more pervasive and powerful implementation of pressure sensing within the field of robotics.
Microelectromechanical systems (MEMS) manufacturing allows the use of high-resolution and extremely compact differential pressure sensors that can integrate proprioceptively into robotic joints and actuators.
For instance, Superior Sensor Technology’s MEMS-based pressure sensors integrate advanced features, including advanced digital filtering, closed-loop control, and software-based pressure switching.
These sensors are fully integrated and deliver the essential internal torque and force feedback required for precise motion control and dexterous object manipulation abilities.
Flexible pressure sensor arrays that are printed with quantum tunneling composites, graphene, or other nanomaterials also enable conformable and stretchable electronic skin layers to be wrapped around robot structures. Materials like nanotube-infused latex produce sensor skins that can be stretched over complex joints and surfaces.
This artificial sense of touch using flexible printed sensors allows dense pressure mapping with high spatial resolution over the whole robot body. The skin-like precision tracking allows the safe detection, reaction, and interaction with humans in collaborative workspaces.
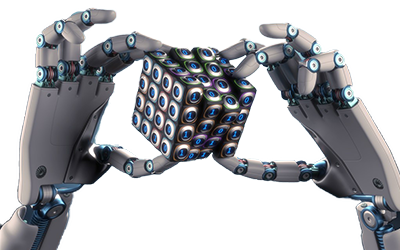
Robot hands with flexible pressure sensing arrays. Image credit: Superior Sensor Technology
Regarding data processing, advanced machine learning methods such as deep neural networks can be used to optimize controls and responses using real-time pressure data from sensor arrays.
The computational models use pressure patterns from proprioceptive and tactile sensors to inform reflex reactions and manipulator movements. For instance, one study utilized reinforcement learning on pressure input to train a robot arm with advanced dexterous manipulation skills, such as rolling a ball in its palm.
New soft actuators and grippers that employ fluidic elastomer technology are heavily reliant on monitoring pressure throughout the entire structure for precise control and feedback.
These pneumatic soft robotics actuators with integrated pressure sensors can be used to smoothly conform to grasped objects. This technology permits safer physical human-robot collaboration in shared workspaces where the use of traditional rigid robots would entail too much risk.
As these various innovations progress, pressure sensing promises to become an essential integrated feedback modality embedded across future robotics, from industrial automation to medical devices. We are beginning to understand the potential of responsive, adaptive robotics enabled by artificial touch sensing.
The Future Robotics: Human-Like Tactile Sensing
As pressure sensor technologies and integration continue to develop, the use of robots with artificial touch sensing will transform many fields:
- Human-Like Dexterity: With adequate tactile pressure data, robots can realize remarkably human-like dexterity, manipulating objects with high precision across various weights, textures, and shapes. This dexterity will advance automation in manufacturing, warehousing, surgery, and more.
- Hazardous Environment Operation: Pressure-sensing durable robots can carry out high-risk tasks such as mining, deep-sea exploration, disaster response, and space missions where direct human involvement is hazardous. Pressure data helps robots react and adapt.
- Seamless Human Collaboration: Ultra-sensitive pressure skin will enable future robots to collaborate safely and seamlessly beside human coworkers. Pressure feedback inhibits injurious contact forces during physical interactions.
- Smart Infrastructure: Robot inspectors that are covered in pressure-sensing skin could be used to monitor wind turbines, oil pipelines, bridges, and other infrastructure. Pressure data uncovers any developing faults.
- Medical Applications: Tactile pressure sensing will facilitate breakthroughs in robotic surgery, prosthetic limbs, rehabilitation, and assistive robotics, where safe interaction with humans is crucial.
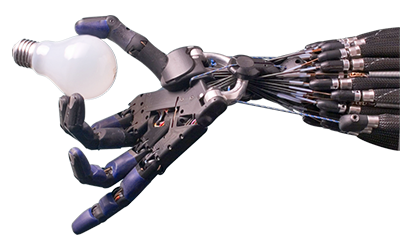
Robotic hand handling a light bulb. Image credit: Superior Sensor Technology
As costs decrease and integration advances, tactile pressure sensing will likely join vision, positional, and inertial sensing as standard modalities in advanced robots. Pressure sensing enables a future where capable and useful robots can operate efficiently and safely beside humans in dynamic real-world environments.
Conclusion
Pressure sensors provide robotics with critical capabilities, including tactile sensing for responsive interactions and proprioception for dexterous manipulation.
Continuous monitoring of internal hydraulic pressures, external contact forces, and environmental conditions provides pressure data that enables robots to move, handle objects, and respond to physical stimuli with human-like sensitivity.
Continuing developments in flexible printed arrays, MEMS sensors, and machine learning integration will facilitate breakthroughs in multi-modal robot perception and seamless human collaboration.
As costs decrease, pressure sensing shows great promise for a standard feedback modality integrated into future robot designs across medical, industrial, assistive, hazardous environment, and infrastructure monitoring applications.
There is great potential as pressure sensors offer robots the feedback required to function reliably, safely, and intelligently in the dynamic physical world.
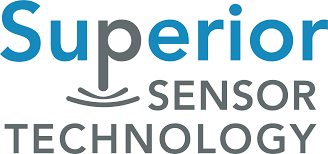
This information has been sourced, reviewed and adapted from materials provided by Superior Sensor Technology.
For more information on this source, please visit Superior Sensor Technology.