Graphene materials have gained significant attention for sensor applications, including detecting humidity, temperature, gases, chemical substances, and physical properties such as mechanical strain and pressure due to their exceptional structural, thermal, optical, and physical properties and electrical conductivity.
Graphene is synthesized using different methods, such as chemical reduction of graphene oxide, epitaxial growth, chemical vapor deposition (CVD), and mechanical exfoliation. Although high-quality graphene can be prepared using the mechanical exfoliation method, the method cannot be used for large-scale graphene production due to its low efficiency.
CVD can be used to synthesize high-quality and large-area graphene. However, high cost and energy consumption are the major disadvantages of this method. Similarly, high energy consumption, transfer cost, and high-temperature processing are the key drawbacks of the epitaxial growth method, which is used to prepare graphene films with high optical transmittance and good electrical conductivity.
Chemical reduction of graphene oxide also leads to environmental pollution during the graphene preparation process. Thus, the drawbacks of the existing methods necessitated the development of a high-efficiency, low-cost, and pollution-free graphene synthesis method.
Recently, the laser direct writing method has received attention from the scientific community for different applications owing to its distinct advantages, such as localized and selective reduction, fast and precise patterning, and the absence of additional chemicals and masks.
In this technique, a laser is utilized for irradiating the carbon precursor to generate graphene by in situ scribing. The entire process of laser scribing requires only a few minutes, which improves graphene preparation efficiency significantly.
LSG films have been used in several applications, including sensing, holography, and photodetection, owing to their excellent electrical conductivity, thermal stability, and surface area.
LSG Preparation and Modification
Precursors, such as polymers and graphene oxide, are primarily irradiated using a laser for graphene fabrication. Various graphene conversion processes are involved during the laser treatment. For instance, the graphene oxide is converted into graphene by laser reduction, which depends on the photothermal and photochemical effects of the laser.
Similarly, direct polymer carbonization is triggered by laser induction to fabricate graphene. Additionally, the wettability, carbonization characteristics, and surface morphology of LSG can be modified by varying the laser power, pulse repetition frequency, and scanning aped.
Several combinations of laser parameters, such as porous, sheet, and needle, can be used to generate various surface morphologies, while a high pulse repetition frequency and scanning speed can be applied to enhance surface hydrophilicity.
Doping methods, such as post-processing doping and in situ doping, can also effectively improve the sensitivity and range of LSG used for sensors. For instance, gold nanoparticles have been used as dopants to fabricate LSG strain sensors.
LSG Application in Sensors
Graphene synthesized using laser scribing processes can be used in different graphene-based sensors, including gas sensors, humidity sensors, temperature sensors, biosensors, and stress sensors.
Stress Sensors
LSG can effectively respond to different externally applied stress forms, such as a human finger touch, physiological motion changes, and vocal cord vibrations, and convert these stress forms into electrical signals for detection due to its exceptional mechanical properties and electrical conductivity, and high specific surface area.
Thus, LSG-based stress sensors can be used for sound sensing, soft robots, health monitoring, and tactile sensing. LSG stress sensors based on capacitance variations have a long service life and good temperature stability.
Biosensors
Biosensors detect chemicals regarding food safety, disease, and environmental chemical hazards through the identification of ions, small biological molecules, and biological macromolecules.
LSG-based ion selective electrodes (ISEs) can be utilized to detect different ions. For instance, ISEs were prepared by functionalizing a carbon dioxide LSG with potassium ion and ammonium ion-selective membranes to obtain potassium and ammonium ion sensors.
Different small molecules, such as hydrogen peroxide, dopamine, and glucose, can be effectively detected using LSG-based electrochemical biosensors. For instance, a glucose detection biosensor was fabricated by immobilizing chitosan-glucose oxidase on the LSG electrode surface. LSG-based biosensors can also be employed to detect biological macromolecules, such as proteins, including insulin and protein biomarkers, and nucleic acids.
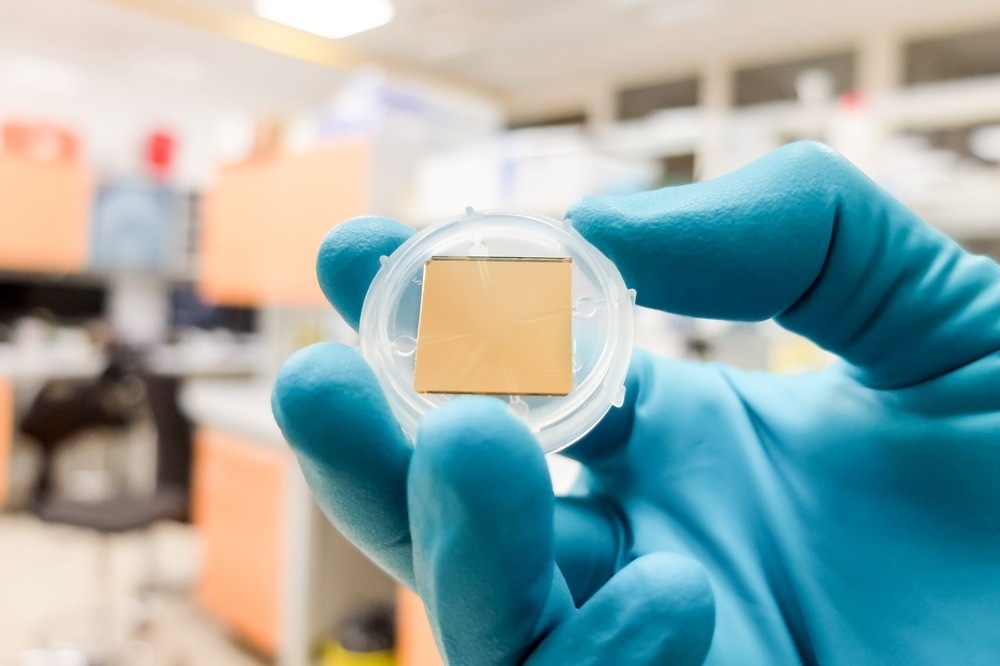
Image Credit: Artur Wnorowski/Shutterstock.com
Temperature Sensors
LSG-based temperature sensors can precisely detect temperatures due to their small size, fast response time, and high wearability. For instance, LSG-based flexible temperature sensors have been developed to measure body temperature accurately.
These sensors demonstrate a linear correlation between the body temperature range of 30–40 °C and resistance, with the resistance being stable at every temperature without fluctuations. Similarly, temperature sensors that adhere to fire suits have been fabricated using poly (diallyldimethylammonium chloride) (PDADMAC) complexes and LSG.
Gas Sensors
LSG has been synthesized for gas sensing applications to improve the sensing performance as LSG possesses a large number of three-dimensional (3D) micro-nano-porous structures, which provide more diffusion paths and active sites for gases.
For instance, LSG gas sensors based on thermal conductivity have been developed for gas detection. These sensors utilize LSG as the electrode material with an LSG filament in the middle. Thermal conductivity fluctuations of the gas surrounding the filament lead to changes in the LSG filament resistivity.
Thus, the sensor possesses different sensitivities to various gases and can effectively detect different gas mixtures. An LSG hydrogen sensor has also been developed based on the turbinate structures in animal noses.
Humidity Sensors
LSG-based humidity sensors display more thermal stability and higher linear response to humidity changes than other functional conductive materials. For instance, an LSG/graphene oxide capacitive sensor has been developed for real-time tracking of transpiration from stomata without damaging the plant.
Similarly, a humidity sensor based on an interdigital electrode (IDE) fabricated using LSG from a commercial digital versatile disc (DVD) with a graphene oxide layer drop-casted on the IDE as a sensing material displayed enhanced sensitivity as the hydrophilic nature of graphene oxide promoted water molecule absorption.
To summarize, the laser scribing method can effectively overcome the challenges of conventional graphene preparation methods, which makes LSG suitable for many applications. Moreover, the advantages of LSG, coupled with the possibility of one-step modification, make LSG an excellent option for sensor applications.
References and Further Reading
Liu, X., et al. (2023). Laser-scribed graphene for sensors: preparation, modification, applications, and future prospects. Light: Advanced Manufacturing 4, 11. doi.org/10.37188/lam.2023.011
Laser-scribed graphene for sensors [Online] Available at https://www.eurekalert.org/news-releases/995143
Wang, H., et al. (2022). Laser-Induced Graphene Based Flexible Electronic Devices. Biosensors, 12(2), p. 55. doi.org/10.3390/bios1202005
Disclaimer: The views expressed here are those of the author expressed in their private capacity and do not necessarily represent the views of AZoM.com Limited T/A AZoNetwork the owner and operator of this website. This disclaimer forms part of the Terms and conditions of use of this website.