Differential pressure sensors are an integral part of bioprocessing in pharmaceutical, vaccine, and biotechnology production, providing essential data for monitoring and controlling various operations.
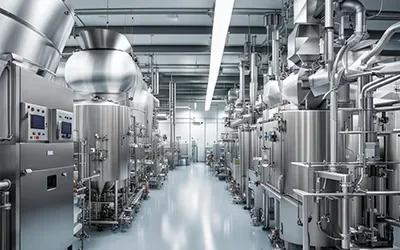
Image Credit: Superior Sensor Technology
For applications ranging from fermentation in bioreactors to separation and purification techniques such as chromatography and filtration, maintaining optimal pressure is vital for achieving good process efficiency and high product quality and yield.
In contrast with absolute pressure sensors, which employ a reference vacuum, differential pressure sensors enable real-time, localized monitoring of conditions in complex bioprocessing workflows.
The widespread adoption of differential pressure sensors in bioprocessing is due to their versatility, reliability, and sensitivity. The detection of minute variations in pressure allows for strict process control.
Differential pressure data can uncover filter fouling, leaks, pump cavitation, and blockages, enabling bioprocess engineers to diagnose issues, optimize parameters, and ensure vital product and patient safety.
With advances in biopharmaceutical manufacturing sophistication and scale, the use of differential pressure sensors is becoming increasingly prominent.
Bioreactor Monitoring
Bioreactors are a key component of biopharmaceutical manufacturing, in which cells or microorganisms are carefully cultured to produce therapeutic vaccines, proteins, and other biologics. Precise control of temperature, pressure, and pH inside bioreactors is vital for the optimization of cell growth and maximization of product yield.
Differential pressure sensors assist with the maintenance of optimal conditions during bioprocesses by continuously recording pressure variations inside the bioreactor vessel. Pressure impacts the oxygen transfer rate and mass transfer of nutrients to cells. Pressure fluctuations can also damage delicate cells, and sub-optimal pressures can slow cell growth and reduce product expression.
Differential pressure sensors connected to the bioreactor supply real-time internal pressure data, allowing deviations from the required pressure to be instantly identified and corrected via automated feedback control or manually adjusting parameters such as aeration rate. The tight control of bioreactor pressure provided by differential pressure sensors ensures healthy cell cultures and consistent, high-yield production runs.
Filtration Processes
Bioprocessing filtration, such as microfiltration, ultrafiltration, depth filtration, and diafiltration, separates and purifies the required biopharmaceutical product from the cell culture medium.
Pressure across the filter increases as the filter membrane captures solids and builds up foulants. Through continuous monitoring of the pressure differential, any increase can be instantly detected, indicating the need for filter cleaning or replacement, thus maintaining efficiency. This is important as an excessively fouled filter has the potential to rupture or cause contamination of the product.
The use of differential pressure sensors ensures rapid identification of decreases in filtration performance, flagging the need to interrupt production for filter cleaning or replacement. This ensures that filtration processes operate at peak efficiency for maximum productivity. Close control over filter fouling also improves filter durability.
Sterile Processing
The maintenance of sterile conditions is vital for effective and safe bioprocessing, as any level of contamination can render the entire biopharmaceutical product unsafe and unusable.
Differential pressure sensors monitor and regulate pressure differentials between cleanrooms, filling lines, isolators, and other processing areas, identifying potential breaches and containment failures through the detection of minute variations in pressure. Rapid alerts enable operators to take corrective actions to restore optimal pressures and prevent contamination.
Tight pressure differentials between 0.5 and 15 Pascals are maintained between high and low sterility areas. Positive pressures are employed in highly sterile areas to push clean air outwards, while negative pressures are used to draw potentially contaminated air into areas of lower sterility.
Differential pressure sensors continuously control the polarized airflow, and sudden drops in pressure gradients set off alarms to alert personnel. Real-time monitoring and control of sterile zones helps minimize risk during aseptic processing.
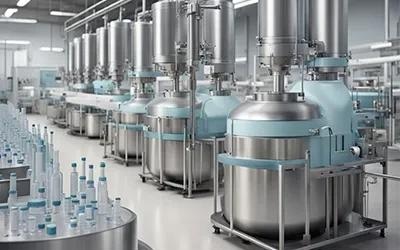
Figure 1. Sterile bioprocessing facility. Image Credit: Superior Sensor Technology
Tangential Flow Filtration
The Tangential Flow Filtration (TFF) process is vital for the concentration and purification of products such as pharmaceuticals, antibodies, and vaccines. TFF employs a membrane filter with specific pore sizes to separate soluble components from cell cultures and maintain a continuous tangential flow across the surface of the membrane.
Continuous recirculation allows for high throughput while minimizing fouling and buildup on the filter surface. In contrast with standard filtration, where flow is perpendicular to the filter, tangential flow minimizes the risk of clogging. TFF is particularly suited to the processing of large volumes with high recovery and concentration factors.
Optimizing TFF results in high-concentration yields and purities. Differential pressure sensors monitor the pressure across membranes during TFF processes, helping optimize and control the purification and concentration of the product.
Pump Control
Constant, reliable flow rate control and pressure conditions are essential throughout bioprocessing workflows. The measurement of variations in pressure across a pump using differential pressure sensors provides real-time data on flow rates and backpressure. This data enables pump speed and valve positions to be precisely adjusted to guarantee the desired rate of movement of liquids through the system.
In large-scale bioprocessing, multiple pumps can be integrated to transfer liquids between seed reactors, production bioreactors, and downstream purification steps. Differential pressure sensors help synchronize pumping systems, allowing for the orchestration of continuous workflows and optimization of material movement between interdependent process units.
Leak Detection
Rapid leak detection helps maintain product quality and safety. Sudden pressure drops can indicate system breaches, such as loose fittings, defective seals, and cracks in equipment. Without rapid identification, products can be lost, and contaminants can enter the system.
Differential pressure sensors for leak detection are often combined with automated alarm systems. Visual and audible alarms are activated when sensors detect a pressure drop outside of set limits. Alarms give an early warning to personnel who can correct the issue before significant contamination or losses occur. Sensors can also isolate the exact location of the pressure drop.
In the case of high-value biopharmaceutical products, even minor leaks can lead to significant financial implications. Contaminated products can also have severe consequences on the health and safety of patients.
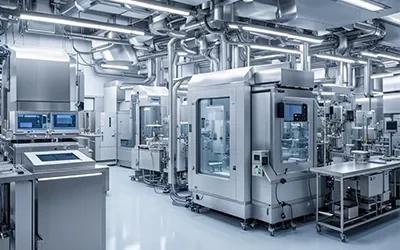
Figure 2. Bioprocessing lab. Image Credit: Superior Sensor Technology
Process Optimization
Differential pressure sensors deliver real-time process data, facilitating the optimization and fine-tuning of bioprocessing conditions. Fluctuations or variations are rapidly detected due to continuous monitoring of pressure variations throughout the bioprocessing workflow. Adjustments can be made to parameters such as temperature, flow rates, and agitation, maintaining consistent and ideal conditions inside bioreactors during filtration, sterile processing, and other steps.
Benefits
Differential pressure sensors deliver a variety of benefits, making them invaluable for the control of bioprocessing applications:
- Real-time data: Pressure sensors provide continuous, real-time data rather than periodic manual testing, enabling immediate detection of process deviations.
- Precise control: Accurate pressure measurements enable precise control over bioprocess parameters such as flow rates, concentrations, and separation processes.
- Early problem detection: Sudden pressure changes can be indicative of issues including leakage and clogging. Early detection enables rapid responses to avoid contamination and losses.
- Process optimization: Pressure data can be analyzed, allowing processes to be fine-tuned, maximizing productivity, yield, and quality.
- Reduced contamination risk: The maintenance of optimal pressure differentials minimizes the risk of contamination in sterile processes and cleanrooms.
- Automation enablement: Pressure sensors enable increased bioprocess automation, reducing labor requirements.
- Improved efficiency: Waste, downtime, and variability are reduced by maintaining ideal conditions.
- Reduced costs: Process enhancements generate significant value, and lower failure rates reduce costs.
Conclusion
Differential pressure sensors play a key role in bioprocessing, facilitating real-time monitoring and close control of critical parameters. They are employed across most areas of biopharmaceutical manufacturing, from the maintenance of aseptic conditions to product purification optimization.
By providing continuous pressure data, differential pressure sensors provide invaluable insights into the health of bioreactors, pumps, filtration systems, and cleanrooms. Sudden pressure changes can be indicative of leaks and blockages, and their detection allows for rapid troubleshooting. The comprehensive data generated by differential pressure sensors also allows for process optimization and the fine-tuning of conditions in real-time, maximizing product quality and yield.
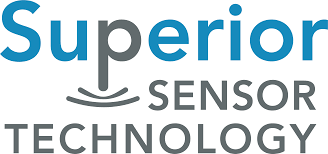
This information has been sourced, reviewed, and adapted from materials provided by Superior Sensor Technology
For more information on this source, please visit Superior Sensor Technology