Established in 1998 in San Sebastián, Spain, STT Systems focuses on advanced motion analysis and machine vision solutions. The company serves various industries, including biomechanics, sports, and industrial quality control. Its divisions—Visio (machine vision) and Motio (biomechanics)—create tailored software solutions, while the Creatio branch emphasizes research and development in sensor technology, artificial intelligence, and machine learning.
Stemmer Imaging
As a leader in machine vision, Stemmer Imaging offers innovative solutions for the inspection, measurement, and quality control of products during manufacturing. The company collaborates with clients across multiple sectors, providing expert guidance on implementing imaging systems to tackle complex automation challenges.

Configuration used for the assembly of a Gocator system for car body scanning. Image Credit: LMI Technologies Inc.
The Challenge
At the Seat Martorell facility of the Volkswagen Group, the primary challenge was to ensure proper inspection of automotive blanks—metal components that would later be transformed into car parts—for the presence of necessary bolts. Missing bolts could result in significant delays, costly rework, and potential stoppages in the assembly line. It was crucial to detect missing bolts as early as possible in the production line, specifically right after the welding process, to minimize disruptions downstream.
- Early Detection: Identify missing bolts promptly to prevent delays and rework.
- Automation: Streamline the inspection process to reduce manual intervention and lower labor costs.
- Traceability: Ensure quality control and data analysis through complete traceability of each component.
The Solution
In collaboration with LMI Technologies, STT Systems, and Stemmer Imaging, an automated quality inspection system was developed to detect missing bolts on automotive blanks. This system integrates multiple Gocator 3D sensors along with an RFID tracking system for real-time analysis and traceability.
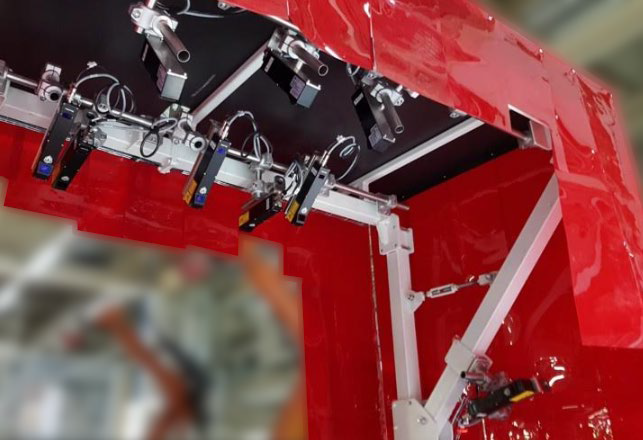
Bolting System with Gocator 3D Smart Sensors. Image Credit: LMI Technologies Inc.
Key Components of the Solution:
- Gocator 3D Sensors: A series of Gocator sensors, including models 2490 and 2380, were strategically placed to scan the blanks from various angles, generating high-resolution 3D point clouds. This data was crucial for determining the presence of each required bolt.
- RFID Tracking: Each blank was equipped with an RFID tag that could be scanned automatically using antennas positioned along the production line. This setup enabled the system to link inspection results with specific blanks, ensuring complete traceability.
- Automation and Integration: The inspection system was seamlessly integrated with the production line's Programmable Logic Controller (PLC). Upon inspection completion, the system could automatically decide whether to divert blanks for manual inspection or allow them to proceed. If missing bolts were detected, the system communicated the necessary actions for manual rework.
- Database Integration: All inspection results were stored in a centralized database, facilitating historical data analysis, statistical reporting, and ongoing performance monitoring. This system provided traceability for each blank and real-time insights into the production process.
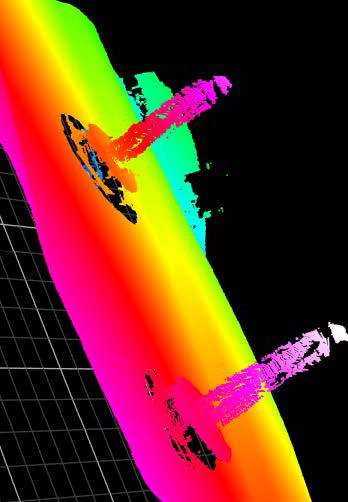
Scan showing 3D image of two bolts. Image Credit: LMI Technologies Inc.
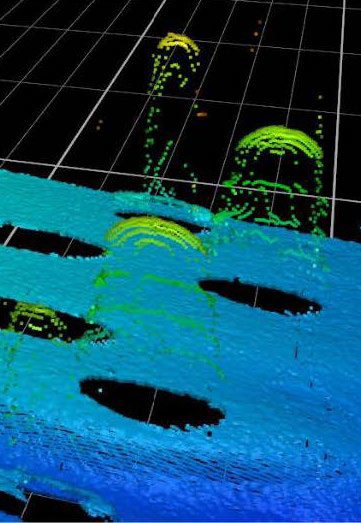
Scan showing 3D image of three bolts. Image Credit: LMI Technologies Inc.
The Result
Implementing the automated inspection system at Seat Martorell led to significant enhancements in production line efficiency.
- High Throughput: Thousands of blanks are processed daily, with each blank automatically inspected for missing bolts. The system accurately identifies defects, detecting up to 1% of blanks in certain batches that were found to be defective.
- Reduced Downtime: By detecting and addressing missing bolts early, the system significantly minimized production stops, allowing corrective actions to be taken upstream instead of at the final assembly stage.
- Improved OEE (Overall Equipment Efficiency): The system's capabilities reduced downtime, enhanced overall production flow, and led to fewer quality control issues, increasing the production line's overall efficiency.
- Labor Savings: By decreasing the need for manual inspections, the solution enabled human resources to be allocated only when necessary for rework, resulting in considerable reductions in labor costs.
The automated bolt inspection system has dramatically improved Seat Martorel’s production efficiency. By detecting missing bolts early in the process, they’ve minimized costly delays and rework, while boosting overall equipment efficiency and reducing labor costs. The integration of Gocator 3D sensors and RFID tracking has given them real-time traceability and data insights that support continuous process improvement.
Iker Urgandarin, CEO of STT Systems
Next Steps
Looking ahead, the automated bolt inspection system is set to further improve the efficiency of Seat Martorell’s production line by:
- Early Detection: Preventing costly rework by identifying missing bolts at the earliest possible stage.
- Reduced Downtime: Minimizing production stops enhances overall production capacity and Overall Equipment Efficiency (OEE).
- Continuous Improvement: Supporting ongoing improvement initiatives through comprehensive data collection and analysis, facilitating preventive maintenance and process optimization.
The system's scalability enables future expansion, accommodating more complex inspections and adapting to evolving quality control requirements.
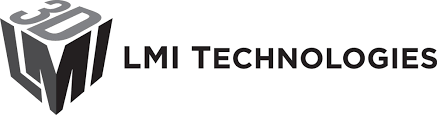
This information has been sourced, reviewed and adapted from materials provided by LMI Technologies Inc.
For more information on this source, please visit LMI Technologies Inc.