Non-contact sensors using capacitive and eddy-current technologies each represent a unique blend of advantages and disadvantages for a variety of applications. This comparison of the two technologies’ will help in selecting the best technology for one's application. The comparison is summarized in Table 1.
Table 1. Comparison between capacitive and eddy-current technologies.
Factor |
Capacitive |
Eddy-Current |
Dirty Environments |
- |
•• |
Small Targets |
•• |
• |
Large Range |
• |
•• |
Thin Materials |
•• |
• |
Material Versatility |
•• |
• |
Multiple Probes |
•• |
• |
Probe Mounting Ease |
•• |
• |
Resolution |
•• |
• |
Bandwidth |
• |
•• |
Cost |
• |
•• |
Sensor Construction
The capacitive sensor has a sensing element at the center. This generates an electric field used to sense the distance to the target. The guard ring is separated from the sensing element by an insulating layer also made of stainless steel. The guard ring surrounds the sensing element and focuses the electric field toward the target.
A few electronic components are connected to the sensing element and guard ring. All these internal assemblies are covered by an insulating layer and encased in a stainless steel housing. The housing is connected to the grounded shield of the cable as shown in Figure 1.
.gif)
Figure 1. Capacitive probe construction.
An eddy current probe contains a sensing coil. The coil is encapsulated in plastic and epoxy and installed in a stainless steel housing. Since the magnetic field of an eddy-current sensor is not as easily focused as the electric field of a capacitive sensor, the epoxy covered coil extends from the steel housing to allow the full sensing field to engage the target as shown in Figure 2.
.gif)
Figure 2. Eddy-current probe construction.
The target is engaged over a certain area by the sensing field of a non-contact sensor’s probe. The size of this area is called the spot size. Spot size is always proportional to the diameter of the probe. The ratio between the probe diameter and spot size is significantly different for capacitive and eddy-current sensors.
Capacitive sensors use an electric field for sensing. This field is focused by a guard ring on the probe resulting in a spot size about 30% larger than the sensing element diameter as shown in Figure 3.
.gif)
Figure 3. Capacitive probe spot size.
Eddy-current sensors use magnetic fields that completely surround the end of the probe. This creates a comparatively large sensing field resulting in a spot size approximately three times the probe’s sensing coil diameter as shown in Figure 4.
.jpg)
Figure 4. Eddy-Current probe spot size.
Sensing Technique
Capacitive and eddy-current sensors use different techniques to determine the position of the target. Capacitive sensors used for precision displacement measurement use a high-frequency electric field, usually between 500kHz and 1MHz. To focus the sensing field on the target, a guard ring creates a separate but identical electric field which isolates the sensing element’s field from everything but the target as shown in Figure 5.
.jpg)
Figure 5. Capacitive probe guarding.
Changes in the distance between the probe and the target change the capacitance which in turn changes the current flow in the sensing element. The sensor's electronics produce a calibrated output voltage which is proportional to the magnitude of this current flow, resulting in an indication of the target position.
Eddy Current in Conductive Target
Eddy-current sensors use magnetic fields to sense the distance to the target. Sensing begins by passing an alternating current through the sensing coil. This creates an alternating magnetic field around the coil. When this alternating magnetic field interacts with the conductive target, it induces a current in the target material called an eddy current. This eddy current produces its own magnetic field which opposes the sensing coil’s field as shown in Figure 6.
.jpg)
Figure 6. The magnetic field induces an eddy current in the conductive target.
Error Sources
Eddy-current sensors use changes in a magnetic field to determine the distance to the target; capacitive sensors use changes in capacitance. There are factors other than the distance to the target that can also change a magnetic field or capacitance. These factors represent potential error sources in your application.
- Gap Contamination - The gap between the sensor and target can become contaminated by dust, liquids such as coolant, and other materials that are not part of the intended measurement. Another factor that affects capacitance is the dielectric constant (e) of the material in the gap between the target and sensor.
- Target Thickness - Capacitive and eddy-current sensors have different requirements for target thickness. The electric field of a capacitive sensor can only engage the surface of the target with no significant penetration into the material. The magnetic field of an eddy-current sensor must penetrate the surface of the target in order to induce eddy currents in the material. If the material is too thin, smaller eddy currents in the target produce a weaker magnetic field. This results in the sensor having reduced sensitivity and a smaller signal-to-noise ratio.
- Target Materials and Rotating Targets - Capacitive and eddy-current sensors respond disparately to differences in the target material. The magnetic field of an eddy-current sensor penetrates the target and induces an eddy current in the material which creates a magnetic field that opposes the field from the probe. Eddy-current sensors calibrated for non-magnetic materials are not likely to function at all when used with magnetic materials. When using eddy-current sensors for precise measurements, it is critical that the sensor be calibrated for the specific material used in the application.
- Environmental Parameters: Temperature and Vacuum - Because of differences in the sensing physics and the associated differences in driver electronics, capacitive and eddy-current sensors have different probe operating temperature ranges and vacuum compatibility. Lion Precision capacitive and eddy-current probes have different operating temperature ranges. Vacuum compatible probes are subjected to an extra cleaning process and special packaging to remove foreign materials that may threaten a delicate vacuum environment.
Probe Mounting
Due to the difference in the shape and reactive nature of the sensing fields of capacitive and eddy-current sensors, the technologies have different probe mounting requirements. Eddy-current probes produce comparatively large magnetic fields. The field diameter is at least three times larger than the probe diameter and greater than three diameters for large probes.
If multiple probes are mounted close together, the magnetic fields will interact. This interaction will create errors in the sensor outputs. If this type of mounting is unavoidable, sensors based on digital technology such as the ECL202 can be specially calibrated to reduce or eliminate the interference from adjacent probes.
The electric fields of capacitive probes are only emitted from the front surface of the probe. The field has a slightly conical shape resulting in a spot size of about 30% larger than the sensing area diameter. All Lion Precision multiple channel systems are synchronized, eliminating any concern about this error source.
Conclusions
There are many factors to consider when choosing between capacitive and eddy-current displacement sensors. Any application that involves measurement area contaminants such as liquids or waste material requires eddy-current sensing. Capacitive sensors require a clean environment. Small targets will be more easily measured with capacitive sensors because of the comparatively small size of the capacitive sensing field. When eddy-current sensing is required, special calibration can be used with small targets.
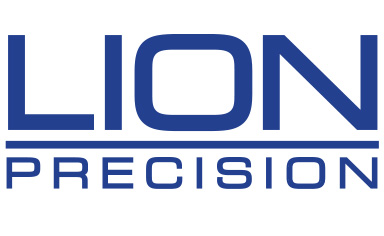
This information has been sourced, reviewed, and adapted from materials provided by Lion Precision.
For more information on this source, please visit Lion Precision.