The selection of the best point level or liquid level sensor to monitor the inventory of valuable liquid, powder and solid chemicals is a challenging task. However, by means of customization options, it is possible to design the sensor that matches the specifications of the inventory measurement.
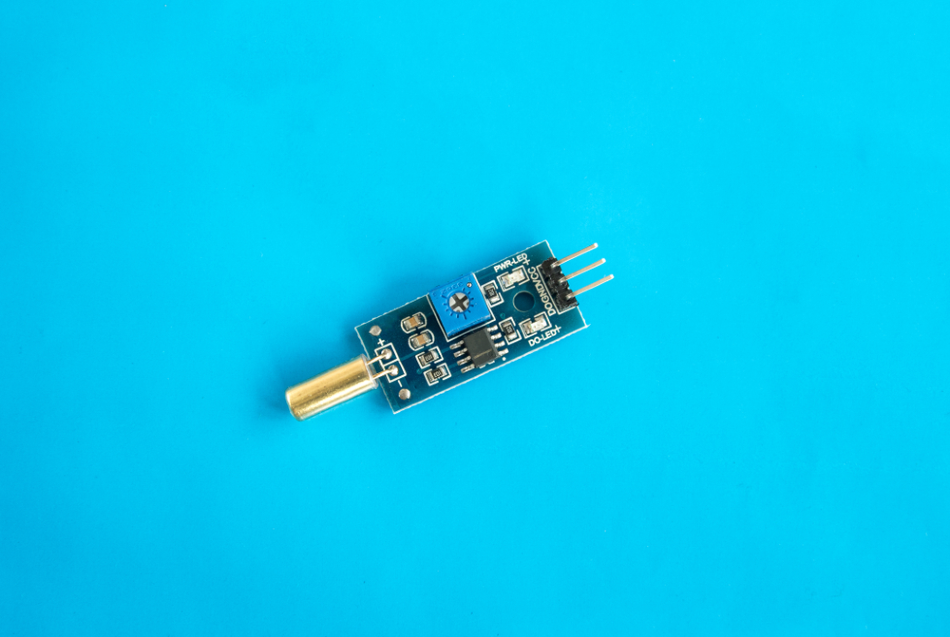
Image Credit: Shutterstock/AlexReut
With the availability of different kinds of sensors and a number of options, the decision-making and product-specification processes become extremely difficult. The utility of a level measurement sensor in a specific application can be optimized with a customized level sensor.
The following devices have more options to manufacture a device based on users’ specifications:
- Ultrasonic level sensors
- Magnetostrictive sensors
- Pressure transducers
- Tilt switches
- Diaphragm switches
- Vibrating rods
- Capacitance probes
- Rotaries
These sensors show promise in providing precise and repeatable level detection. However, each sensor will achieve its optimal performance level when designed for a particular application. Customized point level indicators will provide the best solution depending on whether the vessels have corrosive materials, sanitary regulations, high temperatures, thick walls or any one of the many specifications.
Rotaries
Rotary level indicators are designed for high, mid and low-level detection applications in tanks, bins or other vessels carrying bulk solids and powder. They are linked to an alarm panel or combined to a PLC. As the contents of the tank achieve a specific limit, the indicators are programmed to transmit audible or visual alerts. These alarms prevent overfilling or depletion of tank which could be an expensive and unwanted outcome of incapable level monitoring system.
It is possible to customize inventory management to each vessel using galvanized or stainless steel extension options. Vertical rotaries are suitable for applications where the rotary is operated as a high-level alarm. Most of the operators avoid filling the vessels completely and leave a certain amount of headroom. It is possible to overcome this situation by using a customized shaft length that is adjusted according to the desired amount of headroom. An alert will be sent by a rotary shaft customized for high-level detection as the material achieves the desired limit so as to prevent bin overfill.
In order to address the issues related to lump material level measurement, another extension option is manufactured. Flexible shaft rotaries are suitable for high level detection in heavy materials or other lump solids. In all these cases, heavy materials tend to damage a rigid extension. A flexible cable in place of a fixed solid shaft extension is linked to the rotary and mounted on top of the vessel. With its extra movement capabilities, the rotary can detect high levels under a complex condition without bending a rigid rotary extension shaft.
Horizontal rotary extensions can be used to provide a clear structure of the shaft and paddle in case the vessel carrying the material to be measured has thick bin walls, including a concrete silo that allows the rotary to perform its task. Horizontal extensions allow the side-mounted rotaries to carry out high, mid or low-level detection in a vessel. This design enables the rotary to be attached via the side of a bin wall, thereby minimizing the damage risk during operation.
Adjustable top mounted rotaries can be used to place varying material levels in a bin or silo as they allow convenient changes without replacing the device or entering the bin. They are mounted on top of the bin, and include an adjustable coupling capable of moving up and down the shaft length. With this movement, the rotary can accommodate material levels that are subjected to changes.
A mini-rotary is the best choice for level measurement in smaller bins or hoppers with confined space. The small size of the mini- rotary designed to control material levels in compact spaces enables it to operate in an environment where other devices may not fit easily. The small, mini-rotaries have a rugged design and can deal with a number of light to heavy materials. The motor is mounted on the top or side of a bin, and can rotate when there is no material. With the increase in the material level, the operator is alerted by the sound from an alarm.
Fail-safe rotary level indicators are provided with a sophisticated technology where a system alerts the power loss, and motor/electronics failure in addition to monitoring vessel levels. This type of rotary is one of the best choices for applications that demand continuous operation, thanks to its progressive fail-safe capabilities. This is also preferred when operators need to constantly keep a track on the unit’s status. These rotaries ideal for a wide range of bulk solids, and can either be mounted on the top or side of the vessels.
In the presence of corrosive materials, a stainless steel process connection can be used along with a rotary so as to ensure a prolonged service life of the device and more precise measurement. Rotaries with the connection are designed such that all the materials that make contact with the bin are stainless steel. This ensures that stainless steel process connections are ideal for food and pharmaceutical applications with sanitary needs. It is also ideal for rugged applications, such as those that involve caustic or corrosive materials.
A heat tube can be included to distance electronics that are far away from the heat source when external temperatures outside the bin become higher. Heat tubes are attached to the top or side mounted rotaries in environments with elevated temperatures. Using these tubes, the rotary can be extended beyond insulation on the outside of a vessel.
Rotary customization options include:
- Heat tubes
- Stainless steel process connections
- Fail-safe rotaries
- Mini rotaries
- Adjustable top mount rotaries
- Horizontal rotary extensions
- Flexible shaft rotaries
- Vertical rotaries
The rotary device can be further customized by choosing one of the many paddle options, besides a myriad of rotary extensions and custom fittings. This also ensures high performance of the device. An appropriate selection of paddle will enhance the rotary’s function irrespective of the measurement of the levels of light or heavy material.
In order to achieve the suitable fit for each vessel, the diameter of the options for single blade, double blade, three-vane and bayonet style paddles is varied. Collapsible rotary paddles are available to avoid the entry of personnel into the bins. The paddles are made up of stainless steel or nylon, and are attached to the top and side mounted rotary level indicators.
Capacitance Probes
Capacitance probes are point level indicators designed for high or low level detection. They are fixed in chutes, silos, tanks, bins and other vessels for monitoring the inventory accurately in a number of material storage applications. They are also provided with various customization options that make sure the device is properly designed to meet the needs of unique inventory management. Using these sensors, the content levels can be monitored easily with precision in environments containing clinging, sticky or dusty materials.
By detecting variations in dielectric constants, these probes are capable of sensing small changes in the presence or absence of the material. The capacitance probe ensures interference-free operation in which the signals of other equipment operating in the radio spectrum are uninterrupted. Material settling is possible by programming an adjustable time delay. These probes can be used for different applications, and consist of options for solid and flexible extensions.
The capacitance probe options are also available for materials with rigorous sanitary regulations and can be used under these operational and CIP requirements.
The capacitance probes integrated with remote electronics are best suited for extreme conditions like high vibration and high temperatures. The electronics of these sensors are placed in a remote housing, away from the probe so as to provide precise results under extreme conditions. These probes are highly reliable in a number of slurries, solids, liquids and powders, thanks to its adjustable sensitivity.
Capacitance probes with auto calibration facilitate simple and automatic calibration and external testing without removing the unit’s cover. The calibration is performed within few seconds using a specific magnet.
For materials management in small spaces, compact capacitance probes and flush mount play a major role. Flush mounted probes are non-intrusive and can be used in confined spaces where material flow can cause damage to a standard probe.
Compact capacitance probes can be used in pipes, chutes, silos, tanks or other tight spaces, and provide reliable level measurement and plugged chute detection where proximity switches may not be suitable.
Bendable capacitance probes can also be used in tight spaces, and offer a bendable attachment for applications that prevent a straight probe installation due to obstructions. This is a side-mounted probe designed for high and low detection in smaller containers.
The following are the made-to-order options of capacitance probes:
- Bendable probes
- Compact probes
- Flush mount
- Auto calibration
- Remote electronics
- Sanitary applications
Vibrating Rods
Vibrating rods or vibrating switches are reliable point level indicators designed for the detection of plugged chutes or for high and low detection. Different options of these sensors match the vibrating rod with the specific inventory management application.
Although standard vibrating rods can be used in a wide range of materials, its insertion length will prevent the rod from achieving its peak performance capabilities. In such situations, mini vibrating rods serve as an ideal solution. These sensors can either be top-mounted or side-mounted in small bins and silos. Their design overcomes the problems related to the changes in material density, temperature, humidity and dielectric constant. Mini vibrating rods have sensitivity adjustments suitable for operating in materials, ranging from light and fluffy to heavy and clingy.
A flexible extended vibrating rod is another feature for point level detection such as detection in extremely light and fluffy chemicals. These sensors employ a reinforced cable that is custom manufactured according to the required length, which allows variation in the insertion length from a few inches to several feet. Rigid vibrating rod extensions are present in tanks with a sturdier rod and are also made to customized lengths. These extensions are ideal for top mount locations with galvanized or stainless steel options and allow easy flow of material and prevention of buildup.
For point level detection in sediments present beneath water, vibrating rods are preferred. It is suitable for the detection of the level of submersed solids settled in liquid-containing tank. The vibrating rod vibrates in the water, and stops vibrating when the solid material reaches the probe level. The facility operators are then alerted through an alarm to remove the sediment. This point level indicator can often be used to detect chemical levels and other solid materials settled in tanks with wastewater produced through chemical processing.
Advanced options of vibrating rods include:
- Sediment level detection vibrating rods
- Rigid extended vibrating rods
- Flexible extended vibrating rods
- Mini vibrating rods
Diaphragm Switch
As the material reaches the switch level in the silo, tank or bin, a sensitive microswitch is activated to operate a diaphragm or pressure switch. The diaphragm or pressure switch transmits an alert to start or end a process or an alert to a high, medium or low level in a vessel. This switch mounted within or out of a vessel consists of options used for a number of high performance applications.
For environments that involve combustible dust, automatic point level indication is provided by a diaphragm switch. The diaphragm switch is capable of sensing free-flowing, dry materials and can be installed to detect high, medium and low levels. The inventory can be easily monitored by programming audible or visual alerts. Rugged construction of diaphragm switch enables reliable performance in vessels for a long period of time.
A plugged chute detector is a kind of diaphragm switch specifically designed for sending alerts when a chute is plugged. This pressure switch is composed of rugged materials and suitable for applications in chutes that carry flowing granular or pelleted materials. As most of the plugged chute detectors have explosion-proof certification, they are suitable for operation with volatile materials.
Tilt Switch
A tilt switch is designed for applications like plugged chute detection and point level detection. The switch tips with the increase in material level and raises an alarm sound by activating microswitch.
Tilt switches are vertically suspended over an open pile, a conveyor belt and a silo. In some cases, mercury-free tilt switch option may be required due to environmental compliance. This kind of switch is fixed on the vessel roof and deployed for high level detection. Its operation principles are similar to that of normal tilt switch, yet it avoids mercury contamination and concerns related to disposal of mercury. Both the tilt switches feature sphere or paddle attachments for the shaft end and customizable shaft lengths. The tilt switch that fulfills the specific length requirements will be of great importance in materials management.
Liquid Level Sensors
Liquid level sensors are used in various applications of chemical tanks. Some of the common types of liquid level sensors include the following:
- Ultrasonic level sensors
- Magnetostrictive sensors
- Pressure transducers
One of the most common types of liquid level sensors include the pressure transducers or pressure transmitters, which can be used in process as well as storage conditions. They are cheap and efficient for applications that involve a wide variety of chemicals. In order to suit the design of the vessel and the application, both submersible sensors and models are available for external mounting. External mounting of sensors are favorable for tanks present in extreme environmental conditions.
The parameters like high vibration, hazardous locations, water spray and wash downs, dirt and fine dust, and outdoor installation in inclement weather can be very well managed by a heavy-duty pressure transducer. A submersible pressure sensor is suitable for use in any liquid, and also used in wastewater and leachate tanks. For industrial applications that involve both liquids and gases, amplified output pressure sensors may be preferred. These are inexpensive sensors with prolonged service life and high accuracy.
Magnetostrictive level sensors are a form of continuous float level transmitters suitable for a wide range of chemicals. They can be used for tedious applications that demand a heavy duty sensor. They are provided with a simple setup, long service life and feature with hazardous location certifications critical for the chemical industry.
They are also used in process tanks, wastewater lift stations and chemical tanks, providing reliable results. They are also suitable for applications that involve violent turbulence within the tanks, without any bent probes or stuck floats. A two-float design enables monitoring of both the top level and the interface level using a single sensor, and hence these sensors can be used to detect interface levels within the production tanks.
Ultrasonic level sensors are used for monitoring tank levels with precision and accuracy. These are non-contact liquid level sensors, which provide remote monitoring of small to large tanks and various hazardous location approvals. Ultrasonic sensors are known to provide reliable results in applications like industrial waste management and chemical processing. One of the most common uses of ultrasonic sensors includes measurement of the level or volume of a body of liquid in a tank, pit or well. These sensors come in a variety of models, which make the plant managers decide the most suitable sensor for their facility.
Conclusion
Customized devices are the best option due to the absence of a blanket solution to address level indication problems. These devices are manufactured to suit the specific requirements of each unique application.
This keen requirement will further ensure accurate level detection, prolonged lifespan of products, and minimum maintenance costs. With a wide range of devices, from rotaries to ultrasonic level sensors, the efforts to identify the appropriate features required in a level indicator will be paid back over time.

This information has been sourced, reviewed and adapted from materials provided by BinMaster.
For more information on this source, please visit BinMaster.