There are many devices that are available commercially to detect the level of materials in silos, tanks, and bins. However, level data is always enough to accurately calculate what is in inventory.
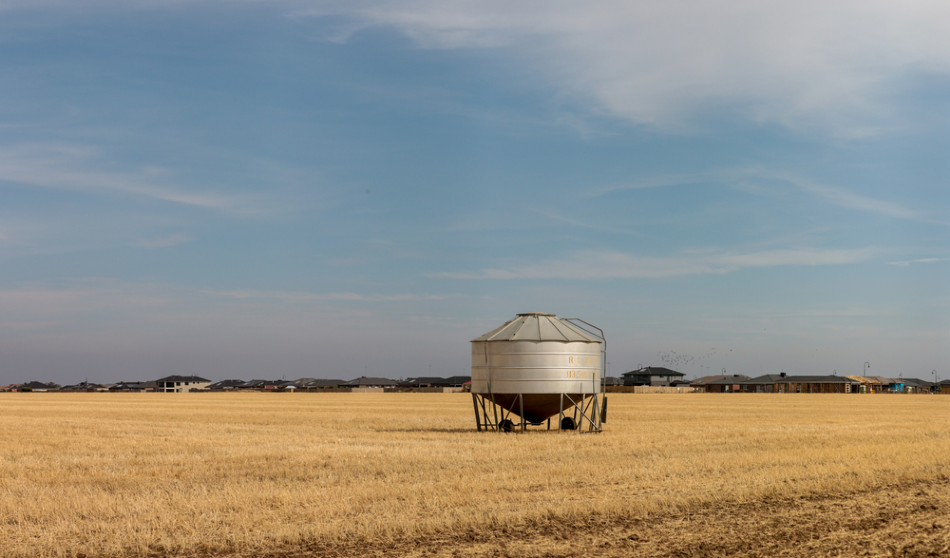
Image Credit: Shutterstock/f.ield of vision
To determine the volume of material on hand and the dollar value of that specific inventory, a single measurement point may not be sufficient data to calculate a precise volume estimate.
Due to their tendency to develop irregular topography in the silo, this can be especially true in solids and powders as many fail to flow freely. An inaccurate volume estimate would be obtained if inventory volume is based upon a single measurement from a single point in the silo.
Multiple Points Really Matter
Acoustics-based technology used in sensors known as 3DLevelScanners, or generically known as scanners, is very different from other sensor varieties. These devices are capable of scanning the material surface in order to take multiple measurements, by considering the low and high spots in the silo.
Scanning the surface also identifies conditions such as cone down or cone up, as well as buildup that may exist along the vessel’s sidewall. The data obtained from multiple measuring points is processed using improved firmware and algorithms, and when integrated with the silo’s parameters loaded into the software, it is possible to provide a highly accurate volume estimate. Extra data, such as the lowest, highest, and average level of the material is also supplied.
Getting Reliable Performance in Heavy Dust
One of the main challenges solids and powders present is the presence of increasing amounts of dust, which can make specific types of sensors unreliable or inaccurate until the dust settles. A scanner working at extremely low frequencies is not actually disturbed by dust and can function reliably and consistently despite the varied conditions of the vessel.
This technology has been demonstrated in a variety of challenging materials such as talc powder, fly ash, silica granules, polyethylene powder, detergents, carbon black, flour and alumina powder.
Self-Cleaning Sensors Minimize Maintenance
A clean sensor is considered to be more reliable and measures accurately in order to ensure that inventory levels are accurately maintained. The exclusive materials and design used to develop scanners ensure that the surface resists the accumulation of dust particles that remain suspended in the air at the top of the vessel.
Additionally, the acoustic pulses generate a “chirping” sound that resonates and produces an almost indiscernible vibration which cleans the inner side of the scanner. The sensor continues to be operational and clean without the requirement to run an air purge to the top portion of the vessel, which can be expensive.
Overcoming Problems with Clingy Materials
If a silo is filled with extremely dusty materials, the silo should be integrated with a sensor that has the potential to withstand in the most adverse situations. This type of application requires a scanner with a Teflon coating on the antenna horn and that resists the buildup of dust even when the bin is filled with warm materials and it is cold outside.
This option is useful when the sensor is used to measure clingy materials such as cement, detergent, concrete, cocoa, sugar, salt, lime, potash, soda ash, talc, calcium carbonate, alumina, or flour.
Non-Contact Sensors Prevent Contamination
With an acoustic sensor, there is nothing that comes into contact with the material, making it extremely safe to use in granules, powders, or other varieties of solids. There is no risk of equipment becoming disconnected or getting stuck in deep material, and possibly damaging the equipment or structure present in the base of the silo.
Replacing cables or probes that can wear out over time is also not required. Eliminating contact with material guarantees a long life with minimal preventive cost or maintenance.
Inventory Management with Fewer Accidents
Climbing silos to take measurements is not required when the inventory monitoring is completely automated. This saves time and also removes the risk of falls and the resulting injuries.
Today, plants handle OSHA requirements related to climbing and entering silos and risk huge fines when they are identified as being in violation. The installation of an automated inventory monitoring system enables the execution of material management from a personal computer within the safety of an office.
Level and Volume Measurement
3DLevelScanners are available in a wide range of models and provide a variety of options in order to modify the device to the application. Selecting an ideal model for an application requires the correct communication of an individual’s expectations of the technology and how they plan to utilize the data obtained from the device. Several plants aim to have an extremely high level of inventory accuracy.
Numerous variables - including information about the vessel size, the material measured, and the presence of the structure inside the vessel - determine the accuracy of the scanner. As the scanner measures multiple points it must have a clear view of the material surface, so the installation site is also of significance.
The simplest model of a scanner is known as reliable level (RL). The model measures materials directly below the device using a narrow beam.
It is capable of penetrating high levels of dust and can perform in conditions where other models of level sensors tend to be inaccurate or unreliable. Therefore, RL is usually employed when highly reliable level measurement data are desired on a constant basis. It is often employed in smaller or narrow silos for materials that are free flowing and not prone to build up.
The S model can be employed when more complex information is essential in vessels up to 14 feet in diameter. The model is developed to measure volume from an average level in the vessel based on measurements from multiple points taken within a 30° beam angle. The S model can also be used to obtain measurements of wider silos. However, due to the 30° beam angle, the entire material surface may not be covered, resulting in decreased accuracy in very wide vessels.
A broader 70° beam angle is used by the M model. This makes the model suitable for silos that have uneven topography and that have larger diameters of up to 45 feet. It also provides addition information such as the average, highest and lowest distances based of measurements from multiple points.
A scanner can offer high levels of volume accuracy, from 1 to 3% of total stored volume, because of its potential to scan the material surface and consider irregularities. The MV model stands at the top of the model spectrum as it offers all that is offered by M, and comes with an additional visualization feature.
The MV model uses high levels of processing power and complex algorithms to create a 3D image of the silo. The image can reveal if the cone is down or up, where the low and high spots are, and can defect sidewall buildup. This unique visualization feature can help to detect if the vessel requires to be cleaned out and help in managing the filling and discharging sites. The MV model is generally used in large silos, of up to 45 inches in diameter, to measure powders, such as flours and materials that pile up randomly.
More Measures to Improve Inventory Management
If a bin is extremely large or wide (over 45 inches in diameter) a multiple scanner system can be integrated with two or more scanners. The MVL model delivers high volume accuracy in some of the largest silos by adding a controller that synchronizes the measurements from all of the scanners on a silo.
The number of scanners required on the silo is established by the size of the silo and the preferred level of accuracy. The MVL model can also provide a 3D visualization of the material surface from the measurements obtained from all the scanners.
MVL 3D Level Sensor System for Inventory Management — BinMaster
If there is no need for visualization, the ML model provides the same level of accuracy without the required visualization. This provides a more cost-effective option when budgets are limited.
Silos can be challenging structures to determine and they mostly come with certain surprises which need to be slightly worked around. For instance, at times a structure will be present at the top of the silo and a measurement device may attempt to measure the structure rather than the material. Neck extensions have been specifically developed for scanners that enable them to clear the structure and beyond it to acquire a precise measurement of the material.
Angled mounting flanges are developed to maintain the level of the device, whereas angled mounting adapters can be employed when the device needs to be directed at a problematic silo.
Acoustic sensors have only been available in the North American market since 2009 and yet they have already redefined inventory management by estimating the volume accurately and all without leaving the safety of an office.
The inventory information obtained from such devices enhances operations in various ways: by enabling well-timed purchasing and replenishment, minimizing safety stock, and making inventory valuation much more accurate. The scanner has considerably benefited plant personnel, making them much more efficient and keeping them safe from climbing silos. Scanners have taken inventory management to a whole new level.

This information has been sourced, reviewed and adapted from materials provided by BinMaster.
For more information on this source, please visit BinMaster.