Although red laser triangulation displacement sensors have been in use for more than 20 years, blue laser versions are also now available. Before selecting which colour to use, it is important to understand which type performs best on which target materials, says Chris Jones, Managing Director at Micro-Epsilon UK.
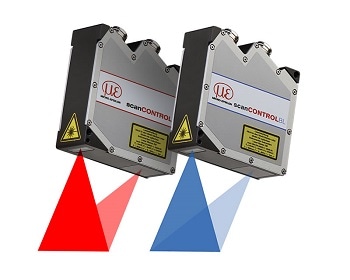
Laser triangulation is one of the most widely known non-contact methods of industrial displacement measurement. Traditionally, this sensor technology uses a red laser light source. Red laser sensors have been in use for over 20 years now and are known to perform well and have improved in recent years to provide good measurement stability on a wide range of dynamically changing surfaces, including low reflectivity and matt surfaces, as well as on fast-moving objects. However, on certain materials, red laser sensors perform less well. So when is it best to use a blue laser triangulation sensor over a red one? To answer this, a number of factors need to be considered.
Laser triangulation principle
In the laser triangulation principle, a laser diode projects a visible point of light onto the surface of the object being measured. The back-scattered light reflected from this point is then projected onto a CCD or CMOS array by a high quality optical lens system. If the target changes position with respect to the sensor, the movement of the reflected light is projected on a different part of the CCD array and analysed to output the exact position of the target. The measurements are processed digitally in the integral controller and then converted into a scaled output via analogue (I/U) and digital interface RS422, Ethernet or EtherCAT.
Target material
The measurement object or target material itself is critical in determining if a stable measurement can be achieved. Certain objects or materials such as red-hot glowing metals emit a high proportion of light at the wavelengths in which red lasers operate. This floods the CCD/CMOS detector and therefore stable measurements cannot be achieved. As the target becomes hotter and so emits higher intensity light, the laser measurement fails completely.
However, a blue laser works at a shorter wavelength of 405nm, which is far from the red part of the visible spectrum. This means it is unaffected by the emitted light, which is blocked from entering the detector by using a simple optical filter, ensuring very stable signals. While blue laser sensors were originally developed for the steel processing industry for use on red-hot glowing metals, as well as for automotive brake disc deformation testing and for measuring vibration on exhaust manifolds, other applications for blue laser sensors have since been discovered.
Other materials
When measuring on organic materials, foodstuffs, transparent or translucent materials (e.g. plastics), due to its shorter wavelength, blue laser light has a lower intensity and so penetrates significantly less into the surface than a red laser. Conventional red laser light penetrates more into the target material and is diffused there, resulting in a de-focused spot on the target surface. This results in a blurred spot being reflected back onto the detector, which means the sensor cannot define an exact distance. In contrast, the blue laser light does not penetrate into the target object due to its reduced wavelength and intensity. The blue laser produces a very small focused laser point on the surface, providing stable and precise measurement results.
Highly polished surfaces
In addition, due to its shorter wavelength, blue laser sensors also perform better on highly polished or gloss surfaces. A red laser light is distorted by the shiny surface, resulting in a “speckle” effect. This produces increased signal noise on the detector and therefore a loss of measurement accuracy. In contrast, the shorter wavelength of the blue laser sensor performs extremely well with much less speckling, resulting in much lower noise levels, typically by a factor of two to three compared to red laser sensors.
2D/3D profile measurements
The advantages of triangulation using a blue laser light not only apply to one-dimensional measurements (i.e. distance, displacement, thickness and vibration) but also to multi-dimensional 2D and 3D inspection such as profile or contour measurements. Here, using blue laser sensors rather than red have opened up new measurement applications that were previously not possible using red laser sensors. Profile measurement of red-hot glowing metals, organic materials, foodstuffs, transparent and highly polished surfaces are best carried out using a blue laser profile sensor.
When red is best
It is important to stress that in a high percentage of measurement applications, red laser sensors will be more suitable than blue laser sensors. With its higher intensity, a red laser sensor performs better on lower reflectivity or matt surfaces, particularly on fast-moving targets. In addition, suppliers typically offer more variants and options for red laser sensors in terms of sensor performance, measuring ranges and more cost effective solutions.
Summary
When selecting a laser triangulation sensor for a displacement, distance or profile measurement application, it is essential to consider the temperature and surface characteristics of the target object. Questions need to be considered such as does the material or surface change dynamically as the measurements are taking place? Does the target appearance change from dark to white? How fast is the target object moving and how accurate do the measurements need to be? This will dictate whether a blue or red laser is more suitable for the application. In addition, some suppliers can offer both blue and red laser sensors in their product portfolio, which may result in a customer receiving more impartial advice prior to purchasing, as well as improved technical advice and support.
For more information, please call the Micro-Epsilon sales department on 0151 355 6070 or email [email protected]