This article aims to describe the best methods for soldering sensors produced by Merit Sensor using automated equipment. For the best performance, all profiles should be evaluated and tested.
A growing number of companies have stopped using the traditional tin-lead (Sn/Pb) solder in circuit board manufacturing due to concerns over the safety of lead and new regulations banning its use, such as the Restriction on Hazardous Substances (RoHS) Directive in Europe. The RoHS Directive prohibits the European sale of new electrical and electronic equipment containing more than the specified levels of mercury, cadmium, lead, polybrominated biphenyl (PBB), hexavalent chromium, and polybrominated diphenyl ether (PBDE) flame retardants.
Merit Sensor offers pressure sensors that are mounted on ceramic substrates and are RoHS compliant. To ensure a good solder joint for most PCB connections, the lead-free solder pads are plated with AgPt.
Either Pb-free or Pb-containing solder process can be used to for soldering Merit Sensor parts. This article is intended to guide end users on how to solder Merit Sensor parts using either Pb-containing solder or Pb-free solder.
Products should be soldered with Pb-free solder in order to meet the RoHS directive.
Soldering with Pb-Free Solder
Since the pressure sensors from Merit Sensor are fabricated on ceramic; a Pb-free solder should be selected that is compatible with the solder pads. Merit Sensor recommends using solder alloys with SnAgCu that have a melting point of 217-221 °C. The Pb-free solder alloys in the SnAgCu family are shown in Table 1.
Table 1. Pb-free solder alloys of the SnAgCu family.
Metal |
Mix Ratio |
Sn (tin) |
95.5 – 96.5% |
Ag (silver) |
3.0 – 4.0% |
Cu (copper) |
0.5 – 0.7% |
When compared to Pb-containing solder (See Figure 1), the surface of Pb-free solder alloys can look considerably different. In addition, a Pb-free solder joint will have a matte, or dull, finish, when compared to a Pb-containing solder joint. This is because when Pb-free alloys begin to cool, the surface of the solder joint will become rough, which is attributed to the increased volume contraction of the Pb-free alloys. Most often, the Pb-free solder joints are smaller than Pb-containing solder joints but this would have no impact on the reliability as these are only cosmetic characteristics.
.jpg)
Figure 1. Examples of a Pb-containing solder joint (left) and a typical finished surface of a Pb-free solder joint (right).
When compared to Pb-containing solders, a reflow soldering profile for Pb-free soldering demands a higher melting point. Since the process time for Pb-free solder is shorter than Pb-containing solder, the temperature differences on the board should be minimized. For this very reason, Merit Sensor does not suggest IR Reflow systems for Pb-free soldering. Instead, it recommends using forced convection reflow systems in order to ensure a successful Pb-free reflow soldering.
The pressure sensors available from Merit Sensor can be soldered with profiles that are based on the standard IPC/JEDEC J-STD-020C (January 2004). Each process must be evaluated in order to find the best temperature profile. The board and the solder paste used will define the best temperature profile.
Table 2 and Figure 2 below show the suggested profile according to IPC/JEDEC J-STD-020C.
Table 2. Pb-free classification reflow profile according to IPC/JEDEC J-STD-020C.
Profile Feature
Pb-Free Assembly
(IPC/JEDEC J-STD-020 Revision C) |
Package thickness ≥ 2.5 mm or
Package volume ≥ 350 mm3 |
Package thickness ≥ 2.5 mm or
Package volume < 350 mm3 |
Average ramp-up rate (Tsmax to Tp) |
3 °C/second max. |
Preheat
– temperature Min (Tsmin)
– temperature Max (Tsmax)
– time (min to max) (ts) |
150 °C
200 °C
60-120 seconds |
Time maintained above
– temperature (TL)
– time (tL) |
217 °C
60-150 seconds |
Peak temperature (Tp) |
245 +0/-5 °C |
250 +0/-5 °C |
Time within 5 °C of actual peak temperature (tp) |
20-40 seconds |
Ramp down rate |
6 °C/second max. |
Time 25 °C to peak temperature |
8 minutes max. |
.jpg)
Figure 2. Pb-free Classification reflow profile according to IPC/JEDEC J-STD-020.
Use of nitrogen – owing to oxidation and increased temperature of Pb-free solder, it may be necessary to work in nitrogen if air leads to unsatisfactory solder joints. However, most Pb-free solder pastes can be used in air. If the solder joints do not have sufficient wetting, then nitrogen may be used.
Hand Soldering – Merit Sensor does not suggest hand soldering. Pb-free soldering needs an excess amount of energy when compared to Pb-containing solder alloys. The heat transfer to the solder joint is crucial and should never be attempted with a soldering iron.
When using a soldering iron, it must be remembered that Pb-free soldering requires a fast heat transfer to achieve a successful solder joint. It may require a longer duration and/or an increase in tip temperature to 360-390 °C. It is highly advised to use solder stations of at least 80 watts of power. Pre-heating can be used to reduce the amount of heat caused on the surrounding components during hand soldering, as is done with reflow soldering.
Soldering Pressure Sensors with Pb-Containing Solder
In case Pb-containing solder is used, temperatures should not go beyond 225 °C for 30 seconds. Merit pressure sensors should be soldered with “no-clean” type solder paste which has a melting point of 179 °C and contains 62%Sn36%Pb2%Ag. Containing 2%Ag, the solder paste considerably reduces the migration of silver from the AgPt pad into the solder paste. However, 63%Sn37%Pb solder paste is not recommended for use. Proper reflow profile for SnPb solder is shown in Table 3 and Figure 3.
Table 3. SnPb classification reflow profile according to IPC/JEDEC J-STD-020C.
Profile Feature
Sn-Pb Eutectic Soldering
(IPC/JEDEC J-STD-020 Revision C) |
Package thickness ≥ 2.5 mm or
Package volume ≥ 350 mm3 |
Package thickness ≥ 2.5 mm or
Package volume < 350 mm3 |
Average ramp-up rate (Tsmax to Tp) |
3 °C/second max. |
Preheat
– temperature Min (Tsmin)
– temperature Max (Tsmax)
– time (min to max) (ts) |
100 °C
150 °C
60-120 seconds |
Time maintained above
– temperature (TL)
– time (tL) |
183 °C
60-150 seconds |
Peak temperature (Tp) |
225 +0/-5 °C |
Time within 5 °C of actual peak temperature (tp) |
10-30 seconds |
Ramp down rate |
6 °C/second max. |
Time 25 °C to peak temperature |
6 minutes max. |
.jpg)
Figure 3. SnPb Classification reflow profile according to IPC/EDEC J-STD-020C.
If the reflow process is followed accurately, then the solder joint should be able to cover the entire solder pad of the ceramic PCB (See Figure 4 - left). Manual soldering, in the majority of cases, will lead to overheating of the device because of the high thermal conductivity of the ceramic. Too low of a temperature will lead to incomplete soldering, that will further lead to a weak connection to the PCB as can be seen in Figure 4 (middle & right). The middle solder joint is an example of a sufficient solder. Yet, that solder failed to wet out and cover the entire pad. The joint on the right was exposed to low heat and insufficient solder, which resulted in poor pad coverage as well as a weak joint as the solder balled up. To optimize the solder profile and ensure that none of the maximum temperatures are exceeded, it is recommended to attach a thermocouple to the sensor.
.jpg)
Figure 4. Example of good solder joint (left) and bad solder joints (middle & right).
Stress Normalization Delay for Calibration
For best results before calibration, Merit Sensor suggests that any surface mount pressure sensor be allowed to rest at room temperature for atleast 48 hours before calibration. The stress induced by reflow soldering will often normalize within this period and help enhance product calibration.
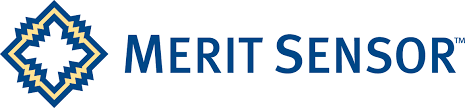
This information has been sourced, reviewed and adapted from materials provided by Merit Sensor.
For more information on this source, please visit Merit Sensor.