When selecting a non-contact capacitive displacement sensor, a number of important parameters need to be considered including the target size and shape, guarding method and bandwidth. Non-contact capacitive displacement sensors are not only able to operate in clean environments, but also in dirty and dusty industrial areas as well. Modular designed sensors with threaded bodies are also available, which further simplifies the mounting of these sensors in industrial or process manufacturing environments.
The Precision of Capacitive Sensors
The capacitive measuring principle based on traditional methods used to determine distance, displacement and position measurement. As one of the most reliable and thermally stable of the non-contact displacement measuring techniques, capacitive sensors are capable of achieving resolutions that are much lower than one nanometer (nm). Capacitive sensors operate on a non-contact, wear-free basis that allow for their results to exhibit excellent linearity, reproducibility and resolution. While sub-micrometer precision is reached in common industrial environments, high precision sub-nanometre measurements are currently only possible in clean environments, where dirt, dust, oil or moisture are not present.
Capacitive measurement systems are also suitable for the detection of fast moving objects and dynamic high speed processes, as these sensors are capable of acquiring fast, reliable measurements of motion sequences. Capacitive sensors are also suitable for use in vacuums and ultra high vacuum applications.
The Principle of Non-Contact Capacitive Sensors
Non-contact capacitive sensors operate by measuring changes in electrical capacitance, which is a term used to describe how two conductive objects with a space between them respond to a voltage difference that is applied directly to them. When a voltage is applied to the conductors, an electrical field is generated in the space between them, thereby causing positive and negative charges to collect on each object. Capacitive sensors therefore function by using an alternating voltage that causes the charges present on each object to continually reverse their positions. This creates an alternating electric current that is detected by the sensor. The capacitance is directly proportional to the surface area of the objects and the dielectric constant of the material between them, and is also inversely proportional to the distance between them.
The principle of capacitive displacement measurement is based on the operation of an ideal plate-type capacitor. The distance displacement of the sensor and the measurement object generates a change in the total capacity. If an alternating current of constant frequency and constant amplitude flows through the sensor capacitor, the amplitude of the alternating voltage on the sensor becomes directly proportional to the distance to the target, or the ground electrode. This change in distance between the measurement object and the controller is detected and processed, followed by an output value that reflects the measurement taken by the controller through different outputs.
.jpg)
To ensure that the sensors are acquiring stable measurements, a continuous dielectric constant between the sensor and the target is required, as the system depends on both the distance between the electrodes as well as its ability to react to dielectric changes within the measuring gap. To achieve the highest possible measurement precision, such as that which is within the nanometre range, the environment should be relatively clean and dry.
The most important factor to ensure stable measurements involve the maintenance of a continuous dielectric constant between the sensor and the target. The operating environment therefore must be relatively clean and dry, otherwise any oil or moisture present within the air gap, for example, could potentially affect the measurement performance of the sensor by causing drift and changes in the output signal. It is important to note that some dust or dirt in the air gap is acceptable, as the sensors typically operate at such high resolutions that the effects of some dust particles is quite low.
Material Types
The capacitive measuring system employs an electromagnetic process that measures on electrically conductive objects with a constant sensitivity and linearity. The system evaluates the reactance of the plate capacitor, which can change in proportion to the distance. As there is no interference caused by the optical characteristics of the target, even transparent or reflective surfaces can be measured at high precision. The conductive measurements of metals, silicon, graphite and water can be measured through this technique.
Capacitive sensors are also capable of measuring insulating materials such as plastics, ceramics, glass, oils and adhesives. When employed for this purpose, the sensor grounding acts as the ground electrode and the insulating material as a coupling medium. An almost linear output signal for the insulators can also be achieved through the use of a special electronic circuitry. Capacitive displacement sensors are typically used on metals, however it is important to consult the sensor supplier prior to measuring the insulators.
Active Guarding
In most capacitive sensing applications, the sensor is one of the conductive objects whereas the target object is the other. To acquire accurate measurements, the electric field from the sensing area must be contained within the space that exists between the sensor and the target. If the field is able to spread to other items or areas on the target, a change in the position of the other item will be measured as a change in the position of the target. Active guarding is therefore a useful technique to ensure that this does event does not occur.
Most sensor suppliers use a guard ring principle, however other suppliers, such as Micro-Epsilon, instead offer a guard ring principle that is combined with a special triaxial cable, a technique that they describe as double guarding. To measure extremely small distances can potentially cause an equally small change in the signal, which indicates that only a few electrons exist between the sensor and the controller. If only small leakage (parasitic) currents flow on the path from sensor to the controller, the distance measurement is no longer accurate. Therefore, more complex triaxial cables are required to determine accurate measurements.
.jpg)
The Micro-Epsilon RF cables provide excellent shielding characteristics to actively guard the field in order to ensure a consistently high signal quality with low noise. Micro-Epsilon has also developed other, unique cables that allow for cable lengths of up to eight meters to be utilized without requiring an additional preamplifier, which can simultaneously enable full exchangeability between the sensor, controller and cable. While the previous outgas-optimized and oxygen-free (CCx) triaxial cables are suitable for different applications from very low temperatures to laboratories and semiconductor production facilities, these cables are specifically designed for use in industrial environments, where long cable lengths are particularly advantageous.
High Stability
As thermally induced conductivity changes of the measuring object have no influence on measurements, the capacitive principle is reliable even with fluctuations in temperature. In addition to temperature stability, the long term stability also guarantees a reliable operation over numerous years without requiring the replacement of any parts or components.
Calibration
In experimental environments where the measuring range will vary depending upon the type of test being performed, the user requires a capacitive measurement system that allows this. A system that requires recalibration prior to each use of a different measuring range could be costly and time consuming, therefore it is important to select a sensor supplier that can offer a system in which various capacitive sensors can be exchanged without requiring recalibration of the sensor by the supplier.
Electrical Runout and Bandwidth
Electrical runout occurs in rotating ferrous targets as a repeatable error for each revolution on the system output. This runout can be caused by small variations in the permeability and conductivity along the circumference of, for example, a rotating shaft. As eddy current displacement sensors are primarily affected by electrical runout, capacitive sensors are completely unaffected by this problem.
Capacitive sensors are based on an analog circuit and therefore function by using a measurement frequency or bandwidth as compared to other sensors that utilized a measuring rate. This difference in measurement determination allows for these sensors to be suitable for measuring vibration, amplitude, oscillation and shaft runout. Some suppliers offer capacitive sensors that measure up to 20 kHz (-3 dB) bandwidths, which allow for these sensors to be ideal for high speed measurements on rotating shafts.
Target Size and Shape
The target size is a critical consideration required for the selection of a sensor that will be utilized for a specific application. The further the sensor is from the target, the larger the minimum target size. If the target area is too small, the electric field will tend to wrap around the sides of the target as a result of the electric field extending further than it was during the factory calibration, which will subsequently measure the target as further away. In general, capacitive sensors will require a target size ratio of 1:1 with the size of the measurement electrode. Smaller or narrower targets can be measured, however it is important to note that some targets will require special adaptation from the supplier.
Since most sensors are calibrated to a flat target, measuring the shape of target is also critical for the determination of accurate results. Therefore a target with a curved surface will most likely cause errors. As the sensor will measure the average distance to the target, the gap at zero volts will be different to when the sensor was calibrated. The electric field behaves differently on a curved surface as compared to a flat surface, therefore if a curved or non-flat surface must be measured, the measurement system can be calibrated by the supplier to the final target shape. However, it is recommended that prior consultation with the sensor supplier is conducted, as some customization will be required.
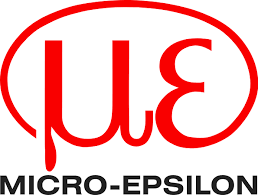
This information has been sourced, reviewed and adapted from materials provided by Micro-Epsilon.
For more information on this source, please visit Micro-Epsilon.