Currently, calibrating gas detection devices with electrochemical cells every 90 days is the best practice. However, the devices available on the market at present can just communicate the end of life of a cell during calibration.
As a result, the 89 days between calibrations remain obscure to the end user since the cell could have failed at any time. TruCal technology decreases this unknown phase to 6 hours with self-checks four times a day. Although other companies claim to offer comparable functionality in their sensors, when looked closely, their check of the sensor is just a continuity test. The issue is that the electrochemical cells hardly ever fail in a way that interrupts the circuit. Rather, they lose sensitivity to such an extent that they can no longer respond to gas — a condition that can only be found out at the time of a full calibration.
Consider a car battery for instance; some days the car will not start. The battery still holds some voltage and turns on the radio; however, that is little consolation when trying to get to a specific place. Wouldn’t it be great if the car warns two weeks earlier that the battery is about to fail? Competitive sensor checks are just like knowing that the car’s battery is dead and can no longer be started. TruCal provides advance warning to replace the car’s battery before you end up being stranded.
TruCal Technology from MSA
MSA’s patented XCell® sensors have powered the TruCal technology. The pulse check inside the sensor offers a reliable sensor interrogation technique that spots and rectifies changes in output sensitivity. The pulse check employs MSA’s patented technology to compute gas response by applying an electronic pulse to the sensor and examining the response curve. MSA can compute gains and losses in output sensitivity through proprietary algorithms, resulting in real-time accuracy adjustments at the time of the pulse check. Besides saving time, users can be sure of accurate indication of sensor functionality.
The pulse check electronically quantifies the variation in sensor output response. A pulse is applied to the sensor where the response is analyzed and used to represent the output sensitivity of the sensor, and check whether internal sensor components are working properly. Sensor output sensitivity includes quantifiable features of internal sensor components. It is possible to measure sensitivity without using gas. The pulse check analysis employs measurements related to the sensor’s electrode catalytic loading to determine output sensitivity variations and increases or decreases in ionic conductivity.
Calculated sensitivity is based on a regression model in which initial sensitivity levels from the last calibration and measured changes in sensor response function to succeeding electronic checks are used. In order to determine sensor accuracy, calculated sensitivity is compared with stored sensitivity from the previous pulse check and the most recent gas calibration. Output from regression is used to determine whether sensors have to be calibrated again or whether they are within tolerable variation from the sensitivity level of previous calibration.
In a day, the pulse check takes place four times. If the variation measured in sensor response is within an acceptable range, a correction is made to the measured output to modify sensor response for accuracy without using calibration gas. This is called Adaptive Environmental Compensation (AEC). This involves comparing the stimulated responses with the last calibration and makes suitable adjustments. Such adjustment can be made with MSA’s application-specific integrated circuit (ASIC) used in MSA’s XCell® Sensors.
.jpg)
In short, TruCal technology from MSA assures that a sensor is present and operating within its predetermined sensitivity range and is adjusted to account for change or drift since the pulse check event or the most recent calibration. The instrument will alert the user about the need for gas calibration if the output signal drifts outside of the acceptable range.
Applications of the TruCal Technology
TruCal enables the following six actions:
- Verifies whether the sensor is operating under normal conditions
- Compensates for sensitivity drift caused by variations in environmental conditions
- Suggests when a full calibration should be carried out
- Alerts when there is a need to change a sensor in the near future
- Reports the health and life condition as “Fair” or “Good”
- Notifies the end user when the device can no longer monitor the area. A fault is initiated as a result.
TruCal technology is incorporated only in the new 5000 platform from MSA. This platform has combined state-of-the-art technology such as extensive calibration cycles, dual sensor capability, Bluetooth® wireless communication, and non-intrusive touch button operation providing advantages such as a low total cost of ownership and a completely new user experience, rendering this platform years ahead of its time.
Design elements such as an industry first, touch interface, and a bright Organic LED (OLED) display for an easy visual status indication guarantees the safety of workers and the plant. Apart from the improved interface, the ULTIMA® X5000 enables great visibility with two side LED indicators for normal operation, fault as well as alarm indication. It is possible to upgrade the detector easily as it shares the exact mounting footprint as the ULTIMA X series, rendering installation easy with the existing wiring and conduit.
.jpg)
MSA ULTIMA X5000 gas monitor (dual sensor)
Benefits Offered by the 5000 Series
The sensing power is doubled by the 5000 series dual sensing technology with just half of the conduit or wiring of a single gas transmitter. It is possible to remotely mount and mix sensor combinations to satisfy the needs of gas detection. The 5000 series is the most flexible transmitters since the maximum remote mounting distances have increased.
The 5000 series offers the required data granularity in places where it is needed. Optional Bluetooth wireless communication enables secure access to fault, sensor health, and detailed gas information on a mobile device and also maintains the simplicity of the analog signal for each sensor. Modbus as well as HART protocols are available as a standard on the 5000 series, making it the most dynamic offering of communication protocols than any existing industry transmitter. Status can be checked and notifications obtained up to 23 m or 75 feet away, and calibration can be started and progress monitored through the X/S Connect app. The setup time can be reduced by at least 50%.
.jpg)
General Monitors S5000 gas monitor (dual sensor)
Conclusion
With the ability to go up to 1.5 years between calibrations using MSA’s breakthrough TruCal technology, maintenance time and expense can be reduced by half. TruCal sets a new industry standard for longer warranties, longer sensor life, extended calibration cycles, better stability, and a number of sensor status checks per day to guarantee operation. The 5000 Series comes with a three-year sensor warranty and a five-year expected life cycle on toxic and combustible digital sensors.
MSA has been innovating and developing revolutionary gas detection products since 1914. There is a reason why MSA is known as The Safety Company. MSA’s objective, on a daily basis, is to offer workers with reliable, high-quality instruments, products, and services to help guarantee a safe return home once the work is completed.
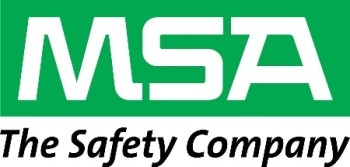
This information has been sourced, reviewed and adapted from materials provided by MSA - The Safety Company.
For more information on this source, please visit MSA - The Safety Company.