A dynamic and nonlinear test environment was needed to accomplish the actuator test architecture taking all the possible conditions into consideration. The Nonlinear Test Bed for Actuators (NTBA) was developed to measure and record a range of physical properties during nonlinear load experiments.
Two different kinds of loads (for example, load motor with harmonic drive, and a non-linear load produced by a four-bar linkage) can be applied to reproduce the most common conditions during the real operation of the actuator. The NTBA will verify if it is possible to accurately meet the proposed prime mover criteria through experimentation and their usefulness in developing the operational performance envelopes. This article discusses the procedure to construct the testbed and the potential of each component in the testbed to yield the necessary physical performance information.
Overview of the Test Bed
The initial inspiration of RRG for developing the Nonlinear Test Bed was to find the performance envelope plots for Permanent Magnet Synchronous Motors; however, the Test-bed had to be sufficiently flexible to be employed for a range of prime movers and also future research endeavors involving condition-based maintenance (CBM). The required operational characteristics of the testbed were defined on the basis of these goals. The maximum power is nearly 10 HP with a maximum speed of up to 5000 RPM.
All components are clasped tightly against a range of load profiles by long black steel rails. In order to resist force in the vertical direction and in the horizontal direction, the rails have ½” threaded holes on the top and ¼” holes in the side, respectively. The screws make it possible to adjust the alignment.
.jpg)
Figure 1. Mechanical Components
The testbed is intended to overcome misalignments issues posed by manufacturing tolerances and to be modular. The supporting blocks have four threaded screws to shift the force to the surface of the testbed by determining the angle and height with regards to the horizontal surface of the testbed. The screws meant for the supporting blocks and the screws meant for the rails help in the accurate positioning of each component. Furthermore, the rails are developed to be modular, so that a large number of configurations can be attained as long as the height from the surface of the testbed to the rotational center is below 6”.
The safety of the testbed was an added concern. The emergency stop switch is incorporated into the testbed to halt the functioning of the testbed in an emergency situation. It has two power relays to cut the supply of the current to the amplifiers for the motors and an extra switch to halt the operation of the enclosure is opened. Additionally, in order to prevent the transfer of a large force from the load to the actuator under test, the brake is on and the clutch is off by default.
The large enclosure is formed over the testbed while the system operates. In due course, this system will be employed to test with large amounts of jerky motion, and therefore, the possibility for parts to fly off the system in case of improper connection or breakage during testing is high. The enclosure will safeguard the user.
Figure 1 shows the mechanical component set-up for the testbed. This testbed is developed for the dynamic test, and therefore, the load motor is employed to create a range of load types. The four-bar linkage generates the nonlinear periodic load. The unique load type is chosen to demonstrate the practical condition for the given test motor. The clutch and the brake are a single unit and they work simultaneously. This means that if the brake is on, the clutch is off and vice versa.
The torque sensor is required to quantify the torque between the test motor and the load motor. The encoders calculate the velocity, position, and acceleration. Furthermore, each component is connected to the remaining system using three bellows couplings. The couplings were carefully selected to tolerate over 40 Lf-ft in the rotational direction
.jpg)
Figure 2. Electrical Components
The electrical component set-up for the testbed is illustrated in Figure 2. The frame itself is composed of wood to prevent electrical hazards. The interconnection module is set up for the connection lines between each mechanical component and the motion controller. As there are several thick cable lines entering the box, they should be put together closely and properly. The interface box is made for the torque sensor. This box transmits the torque signal from the sensor to the controller. The heat sink and cooling are required by the motor amplifiers and power supplies.
At the time of testing, an enormous amount of heat will be produced by the amplifiers and power supplies and hence it has four fans that operate to minimize the heat. The solid-state relay is employed to control the operation of the brake and clutch. The current sensor will quantify the amount of current flow through the wire from the amplifier to the test motor. Furthermore, the temperature sensors are fitted within the test motor, and the voltage signals sent from the temperature are scaled down by the calibration circuit. Each and every component will be described comprehensively later.
Operations of the Test Bed
After setting up the testbed with all of the necessary electrical and mechanical components, signal wires are linked from the controller to each component. The power lines for each piece of measurement tools and amplifiers are linked to power supplies. Hall sensors and encoders require a voltage of 5 V, and their power is supplied from the controller interconnection block. The current sensor requires a voltage of +/-15 V, therefore, it has its own power supply. Moreover, thermisters need a voltage of +/-15 V and they draw power from the same power supply.
In the case of a power surge, the current flow is disconnected using two power relays. Each of the power relays is linked in series between the power supply and amplifier. A voltage divider circuit is also built so as to draw the voltage signals from the test motor. These signals are reduced to +/-10 V.
The sensor signals are transmitted to the motion controller via the interconnection block. Eleven input signals will be obtained: three current signals, three voltage signals, one torque signal, and four temperature signals. Since there are only eight input channels in the Galil motion controller, the additional signals will be collected using a National Instrument’s Data Acquisition Board. Encoder and hall signals are required in the test motor to send feedback to the amplifier. These signals are required to complete the sinusoidal commutation loop to operate the test motor.
There is no need for the load motor to feedback the position signals and hall signals to the amplifier since the load motor commutates the current signals in the motion controller instead of the amplifier. As the test motor amplifier ground is not separated from the power line, the grounds for the amplifier and motion controller are linked to the earth. Furthermore, the one to one ratio of the isolated power transformer is used to transfer the voltage range of around +/-76 VDC to the voltage output range between 0 VDC and 169 VDC. Eventually, the engagement of the brake and clutch is controlled using one of the digital output channels. This signal will be transmitted to the brake and clutch in an emergency situation or at the time of the operation.
The Galil motion controller gives more than 100 commands for defining motion and machine parameters. It includes commands to begin an action, question status, and configure the filters and controllers. These commands can be transmitted in binary or ASCII. These Galil’s commands assist the user to create, store and implement several complex application programs. Furthermore, Galil offers DLL files to generate the program with the help of C/C++, Visual Basic, or Labview. All of these features will assist users to develop a real-time operating system with quick sampling and feedback update speed.
Conclusion
The Nonlinear Test Bed will offer test capabilities for a broad variety of characteristics and several different actuators. Usually, the load motor and test motor run at their highest speed; however, the torque potential of the test motor is yet to be determined. The performance of the test motor will be assessed on the basis of the test protocol for completion of one of the missions for the ONR all-electric ship program.
Sources and Further Reading
- Seongho Kang, Daniel J. Cox, Delbert Tesar, “Design of Actuator Endurance and Reliability Test Bed”, Proceedings of ASME DETC’00, ASME 2000 Design Engineering Technical Conferences, Baltimore, Maryland, September, 2000
- Mark Marrs, “Design of an Advanced, High-Precision. Seven Degree-of-Freedom Modular Robotic Manipulator”, Master Thesis, Approved by Delbert Tesar, 1997
- David Le, “Development and Integration of a Fault Tolerance Test Bed Environment for Space Application”, Master Thesis, Approved by Delbert Tesar, 1997
- Kollmorgen Goldline Brushless Motor Series manual, Kollmorgen, 2002
- Advanced Motion Controls, PWM Servo Amplifiers Manual, 1999-2000 Catalog and Technical Manual, http://www.a-m-c.com
- Warner Electric, Clutches, Brakes and Controls master Catalog, 2000 http://www.warnerelectric.com
- Drafts, William, Acoustic Wave Technology Sensors, Sensors Magazine, Oct. 2000.
- Torqsense Non-Contact Rotary Torque Measurement, Wen Technology, Inc., 2000.
- Honeywell, Technical Report for Hall Current Sensor, http://www.honeywell.com
- Quality Thermistor INC. http://www.thermistor.com, 2002.
- Bechwidth, T. G. et al, Mechanical Measurements, 5th ed., Addison-Wesley Publishing Co., 1995. pg 239-242.
- R+W Coupling Technology, http://www.rw-america.com
- Galil Motion Controller, DMC-1700/1800 Manual, http://www.galilmc.com
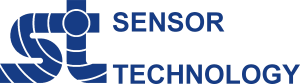
This information has been sourced, reviewed and adapted from materials provided by Sensor Technology.
For more information on this source, please visit Sensor Technology.