Interview conducted by Mychealla RiceMay 17 2019
In this interview, Don Welch from MTI Instruments talks to AZoM using capacitance sensors in industrial applications.
How is new market demand driving changes in capacitance needs?
Traditionally, capacitance has been employed in high-end applications like lens focusing, or piezo positioning where accuracy and precision were the driving factors. It is not surprising the technology lends itself very well to semiconductor, electronics and R&D applications. Although we see these markets and customers extremely important to the continued advancement of our technology, we also see large opportunities in other areas by combining the intrinsic values of capacitance, with the market demand for higher resolution, low-cost sensor alternatives. With this new platform, the customer does get the best of both worlds: high resolution at a justifiable cost.
Currently, MTI is only working with OEMs who have the need for internal integration of these sensors into their own product. Our success stems from the fact that we will customize our flexible platform to fit the particular application; hence creating a fairly sophisticated unique sensor at a reasonable cost. In our experience, sensors can also create opportunities to differentiate your product from competition. We have worked with at least one customer that used the new capability to market their products differently gaining and edge by marketing their products with the slogan “internal continuous self-monitoring.”
What are the important parameters that you need to consider when selecting a traditional capacitance sensor?
The most important parameter is the range that needs to be measured. We typically start out by asking customers how far away they need to measure. Capacitance sensors are quite precise and measure extremely small distances of around a few millimeters. The next important parameter to consider would be what resolution is needed. Typically, we can provide 10,000:1 in terms of resolution and in some cases, better than that.
Other important parameters are whether the gap is clean and what the maximum sensor diameter that you can have in your application. A lot of people have restricted space, so the sensor needs to be small. We can then perform range extension. For example, MTI’s Digital Accumeasure has multiple range extension that allows smaller probes to sense further away than other past traditional amplifiers.
With our new low-cost platform customer are not as focused on the above parameters as much as they are looking for miniaturization, wireless capability, stability, and acceptable resolution at a much affordable price which enables them to add more sensors, and embed them into their systems to monitor critical parameters.
Capacitance-based measurement probes have long been employed as a means of non-contact measurement of electrically conductive materials. Why is this considered better?
Capacitance can be very accurate. By marrying a processor to a capacitance measurement, we can make the measurements very linear and accurate in terms of other sensing technologies.
The target does not have to be conductive as we have ways around that, but in general, we want a conductive target. With the digital capacitance sensors that we have now, the accuracy is getting to the point where physically we cannot improve it any more. We are starting to run up against the laws of physics.
We have also addressed problems of stability. Early capacitance probes had drifty components in the amplifiers. By using digital means now, we have gotten stability below 200 parts per million, because the components are better at using digital techniques.
Capacitance can be a linear measurement or a non-linear measurement. Most people have highly non-linear measurements, and with the microprocessor, in there we can linearize it. We also have a technique called constant current, were using analog techniques we can obtain a linear measurement.
Capacitive Non-contact Measurement Products Overview
Capacitive measuring is considered the most reliable and stable non-contact measuring techniques? How will this benefit applications?
The capacitance of air does not change much if the humidity, temperature or pressure changes. They are very small physical parameters that affect capacitance measurements, making measuring the capacitance of a gap highly stable when considering the basic capacitance equation.
Where applications need long-term stability and high resolution, and you do not want drifting, thus capacitance can be cheaper, better than a laser, and more stable than any current or other types of measurements that are affected by temperature.
Capacitance is not affected by temperature, humidity, and pressure. Why is this perfect for industrial applications?
Based on those parameters, we can operate in extremely high temperatures of up to around 1,200 degrees Celsius. As long as our actual parts don't melt, we can make measurements there. We have also operated in high pressure and vacuum environments.
As an example, this is useful for measurements that need to be made in space programs where they are trying to simulate space. To obtain these conditions it requires cold, cryogenic temperatures of around four degrees Kelvin at almost absolute vac and around 10 to the minus 8 Torr. We can then build probes that work in those environments.
We can operate in what we call extremely difficult atmospheres, climates, temperatures, and hazardous conditions. We can also build probes with the current so low that they are intrinsically safe to be used in an explosive environment. So most industrial environments are tame compared to the extream conditions we can operate in.
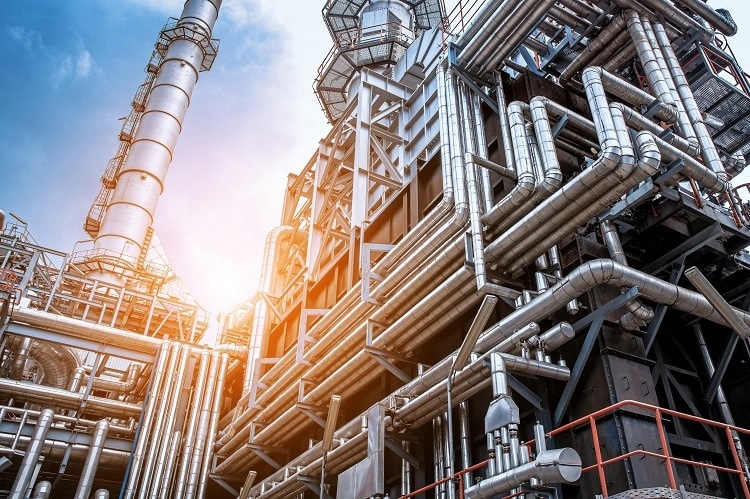
Image Credits: shutterstock.com/RedIvory
What are the factors that you need to consider when embedding a capacitance sensor into an industrial application, and can you give us any examples or any ones that you know of?
The critical points are having a clean gap, range < 15 mm , frequency response < 5kHz and resolution greater than 1 /10,000 of range . Furthermore, you need to consider if the target is conductive or can be grounded. When embedding a probe, we are taking our capacitance technology and trying to adapt it to a measurement that somebody is trying to make, for example, pressure.
If we take a metallic diaphragm and place it in front of an embedded capacitance probe, we can measure the deflection very accurately, as the pressure pushes on that diaphragm in a sealed sensor. We can turn a physical parameter, such as pressure, into a very highly stable capacitance reading proportional to pressure.
What benefits can the capacitance probes bring to the industrial applications that other methods cannot?
We have made recent advances with the digital capacitance technology that others do not have. By using a microprocessor to sample the capacitance, we have increased stability. We have been able to make our probes smaller and this has enabled something called range extension with high accuracy. This allows you to take a probe designed to work up to one millimeter and get the sensor to work up to 10 millimeters by reducing the current and using digital techniques and filtering.
A benefit of capacitance is where we embedded into a wind turbine with an extremely high magnetic field (two tesla), to monitor the armature gap as the wind turbine rotates. Capacitance is immune to magnetic fields and we use our range extension technology to be able to see that 10 millimeter gap while having good stability for a period of around 10 years. The digital techniques that we use with the capacitance amplifiers are embedded and do not need pulling out and recalibrating.
Another advantage is the absolute accuracy that we obtain using capacitance. When you calibrate your probe to measure a gap, it is not affected by things like the temperature of the target or the material of the target. This means we can look at either a stator iron core or at a rare earth magnet and measure that absolute distance without any kind of recalibration. Capacitance probes can be miniaturized through lithography techniques. We have printed capacitance probes using advanced 3D printing methods. The circuitry can also be miniaturized. We have even embedded the amplifier circuitry into the probe body.
The stable calibration requirements allow these things to be embedded in other people's products. We can then measure things such as vibration or seismic activity. Companies who are trying to make these types of measurements and are using some other sensing technology may want to consider capacitance due to the low cost and high accuracy of it.
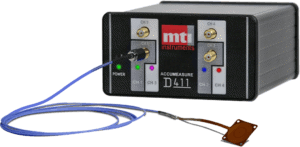
Could you tell us about the primary benefit of the new version of the Digital AccuMeasure Gen 3 Capacitance System?
The Gen 3 is a higher resolution version of what we have done previously with the Digital Accumeasure Gen 1 & 2. We can measure smaller step size with a positioning stage, it will have much better accuracy. For example, semiconductor lithography focus stages require extremely high resolution for small IC line widths down to 7 nanometers.
It also eliminates second party data acquisition systems, which results in less accuracy due to DAQ sampling noise.
What are the differences between the analog and the digital systems for industrial applications?
If you are using a closed-loop system and cannot tolerate any latency, which is necessary for some applications, then we fall back on our analog products. For the most part though, digital is the way to go as it involves far less processing.
Furthermore, there are a couple of inexpensive, cheap applications where customers have analog circuitry and they want to hook up to our amplifiers. They tend to prefer the analog output for that.
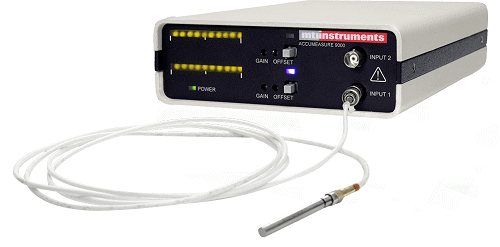
Are there other applications that can benefit from MTI's capacitance-based measurement products, and how would they benefit from them?
There are several physical parameters that you could measure with capacitances. For example, right now we are working with a chipset for measuring seismic motion which uses a MEMS capacitance sensor and very low noise ASIC amplifier. As the seismic motion shakes the sensor, the capacitance changes and we can measure that capacitance to a very high degree of accuracy (Think micro g’s) . We are also working on low cost capacitive gap sensors that are wireless and battery operated.
Another thing we can do is measure Coriolis force using capacitance, which then can be embedded in a flow meter. Other uses include measuring vibration, measuring pressure in very hostile atmospheres, and measuring biomass.
An example of the latter is to measure how much water is absorbed into something. I have worked with a professor who was trying to measure ice build-up in a sea chest on a ship. Think about how the ice crystals start to form - he did not want to clog up the pumps on the ship, causing them to fail. They wanted to detect that the water was changing to ice, and we were able to do that using capacitance.
We can also measure liquid level. Many years ago, I worked with the Army Corp of Engineers out in San Francisco where they had the San Francisco Bay model - a fully hydrodynamic set-up almost like a giant swimming pool, which was used to model the flow and currents in the San Francisco Bay. They used capacitance to measure the heights of the water.
It was very good at measuring liquid level. It can also detect liquid level through an insulator. Imagine a bottle, for example, being filled up with water; we can measure the level of the water in that bottle without touching the water. This is especially useful in applications involving dangerous fluids.
We can detect things like grease build-up in flumes over stoves, or we can detect metal contamination in food and textiles. Furthermore, we can also build things like low-force load cells to measure very weak forces.
Those are just some examples, although there are many more. We are excited about trying to start embedding our sensors in all these other applications so that we can save lives, improve safety, and make measurements faster and cheaper with our capacitance technology.
About Don Welch
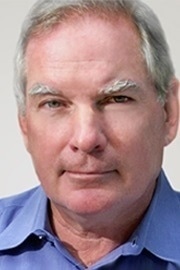
Don Welch has been working at MTI Instruments for over 30 years, initially as a R&D engineer then Director of Engineering, then Director of New Business Development.
Don enjoys working with customers to solve applications issues and has extensive industry experience with all types of sensors being used in a wide variety of industrial applications.
Don holds a BSEE from Union College.
Disclaimer: The views expressed here are those of the interviewee and do not necessarily represent the views of AZoM.com Limited (T/A) AZoNetwork, the owner and operator of this website. This disclaimer forms part of the Terms and Conditions of use of this website.