Industrial hygiene is defined as “the science of anticipating, recognizing, evaluating, and controlling workplace conditions that may cause workers’ injury or illness.” by The United States Occupational Safety and Health Administration (OSHA). Put simply, it is the professional study of worker protection.
The identification and control of hazardous atmospheres is a key concern of industrial hygiene. There are a number of ways that hazardous atmospheres may arise in the workplace and may contain asphyxiating agents, flammable or combustible gases, corrosive, irritating, or toxic gases and vapors.
These environmental hazards are usually invisible to the body’s senses and pose a risk to the continuous operation of a plant in addition to worker safety, life and health. Reliable techniques of hazardous gas monitoring are able to help to mitigate these substantial risks.
For the majority of gas detectors currently available on the market, the only way to confirm accurate readings is to expose the instrument to a known concentration of test gas. This can be time-consuming (especially for inaccessible sensors), laborious, intrusive and add to maintenance costs.
What Causes a Sensor to Lose Accuracy?
Fixed gas detectors typically include a number of different varieties of sensors. The atmosphere where the instrument is utilized can have a huge influence on the sensors.
Each type of sensor employs a slightly different detection principle. Sensors may suffer degraded performance or be poisoned or if they are exposed to certain substances or environmental conditions.
The types of conditions that influence the accuracy of sensors vary between different sensors, and electrochemical sensors are particularly affected by the environment. Creating electrochemical reactions is fairly simple, but controlling and maintaining results from these reactions can be difficult.
It is well known that gas sensors have limited lifetimes, and their sensitivities can deteriorate from unintentional exposure to vibration, some gases and shock. Gas flow to the sensor can also be hindered by dust and dirt. This is one key reason why a user must carry out functional checks, frequent inspections, maintenance and calibrations.
Electrochemical Sensors
Electrochemical sensors utilize an electrochemical reaction to produce a current which is proportional to the gas concentration. The sensor is a chamber that contains a gel or electrolyte and electrodes.
The gas sample enters the casing through a membrane, reduction takes place at the counter electrode, and oxidation happens at the working electrode, resulting in ions flow which produces a current.
Measurement of this current is converted into a displayed gas reading. While some electrochemical sensors utilized to measure toxic gases are not worn out or consumed by exposure to CO or H2S, such as carbon monoxide (CO) and hydrogen sulfide (H2S), they still need to be replaced eventually.
The life of the sensor is usually limited by the electrolyte or one or more of the electrodes. The sensitivity will require response checking or periodic recalibration. The loss of sensitivity may sometimes be sudden and dramatic, even though CO and H2S sensors may last for years without a huge loss of sensitivity.
Sensitivity may also be reduced by incidental exposure to other substances. For example, many electrochemical sensors can be affected permanently by exposure to organic solvents and alcohols. The performance of CO and H2S sensors is well known to be affected by exposure to methanol.
What Do the Regulations Say?
Major international standards for performance of combustible and oxygen detectors1 provide a general warning about possible adverse effects on sensors from airborne contaminants such as dust, wet, oily adhesive sprays and mists. This is also valid for toxic sensors.
Most notably, they can lead to the loss of sensitivity or even block the diffusion path for gas to the sensor inlet. Paint overspray or deliberate painting can also affect gas detector availability.
Clear mitigating recommendations are provided for regular inspection by a competent person, including calibration and the visual inspection of not only the transmitter but also the gas sensor inlets for blockages.
How Often to Calibrate Gas Monitors?
International gas detection standards (ISA / IEC / EN 60079-29-2 – p. 8.12) supplies guidance that periodic calibrations will be required in addition to functional checks, which are detailed in manufacturers’ instruction manuals and local regulations.
Due to the fact that the conditions of use can be different, there is no one rule for maintenance frequency that can fit all applications.
Calibration is Important, But What Happens in Between?
Between calibration periods, the performance of a gas detector is unknown, so defining the calibration intervals for optimal safety becomes a key challenge. That is why environmental and site conditions should be considered, which can lead to a large difference in required calibration periods ranging from days to months.
Both the accuracy of the readings and the proper performance of the instrument’s alarms can be verified by exposing the instrument to a known concentration test gas.
Failure to periodically test and document the performance of fixed gas detectors can leave a facility open to regulatory citations or fines, in addition to increased liability exposure if a worker is injured in an accident.
Guidelines are also supplied for the calibration, validation and use of personal, portable gas detection instrumentation by The International Safety Equipment Association (ISEA).2 The ISEA defines three levels of calibration or other validation of performance as:
- Full calibration
- Calibration check
- Bump test
Yet, the ISEA does not supply a similar statement of the validation of permanently installed gas monitoring equipment.
There are guidelines on choosing and deploying monitors for permanent applications, but calibration frequency and other instrument validation are usually left to site-specific requirements or the instrument manufacturers’ recommendations.
Manufacturer’s recommendations usually suggest 90 to 180-day calibration intervals, with no requirement to perform periodic validation checks. So, these requirements place a large burden of responsibility on the organization installing the instrumentation, the end-user of gas detection instrumentation, and the manufacturer of the instrument.
The purchase and general availability of calibration devices, gases and supplies, in addition to the burden of record keeping, is necessitated by the requirement for regular, periodic calibration and event-driven calibration necessitates.
This burden becomes clearer, recognizing that many industrial sites require each worker to carry a personal gas detection instrument which may easily exceed 1,000 units at a particular site, together with permanently mounted and area monitoring instrumentation for the same gaseous hazards.
Lastly, the information gap between permanent and portable gas detection instrumentation is glaring; the need for at least daily validation for portable instruments versus 90 to 180-day cycles of full calibration for permanent instruments.
It is worth noting that permanent and portable instruments typically use the same type of electrochemical sensors.
Calibration Procedures
Usually, calibration is a two-step procedure – the zero and the span. Firstly, the sensor is zeroed by utilizing ambient air after confirming that the target gas is not present or by utilizing a suitable gas from a cylinder.
Exposing the instrument to the calibration gas that contains a known concentration of the target gas the sensor is designed to measure is the next step. The readings are then adjusted in order to match these values.
The very first sensor functionality that is tested is often easily overlooked in considering these operations. It is the physical delivery of test gas from the cylinder to the sensor itself. When the sensor begins to measure the test gas, the question “is the diffusion path to the sensor sufficiently open and clear to allow the sensor to detect gas?” is answered.
When applying gas to a sensor for either a manual gas calibration or a bump test, this is the first determination that is made. The sensor carries out its function to translate chemical information into user accessible information (indicated by the concentration readouts, alarms, etc.) once the calibration or simulant gas reaches the sensor.
Lengthening the Interval Between Calibration Checks
By periodically and automatically carrying out self-checks on the sensor and monitoring its inlet for blockages which would prevent gas detection without user intervention or the application of calibration gas, MSA’s XCell® sensors with TruCal technology greatly decrease this burden.
Numerous objectives are accomplished by using this revolutionary technology, including extending calibration intervals, eliminating the need for bump checks and providing the user with the assurance that the sensor is measuring accurately, healthy and capable of detecting gas.
This is done by combining an internal electronic interrogation of the sensor functionality (Pulse Check) with an acoustic system that monitors the flame path (sinter/frit) for blockages, which would stop gas from reaching the sensor (Diffusion Supervision).
Every 6 hours, interpreting the results of these two tests and either adjusting the sensor’s sensitivity or alerting the end-user the sensor’s inlet is blocked is automatically carried out without any user intervention.
Pulse Check
In order to calculate gas response, the pulse check utilizes MSA’s patented technology by applying an electronic pulse to the sensor and analyzing the response curve, as seen in Fig. 1. TruCal can quantify gains and losses in output sensitivity through proprietary algorithms, which lead to real-time accuracy adjustments during the pulse check.
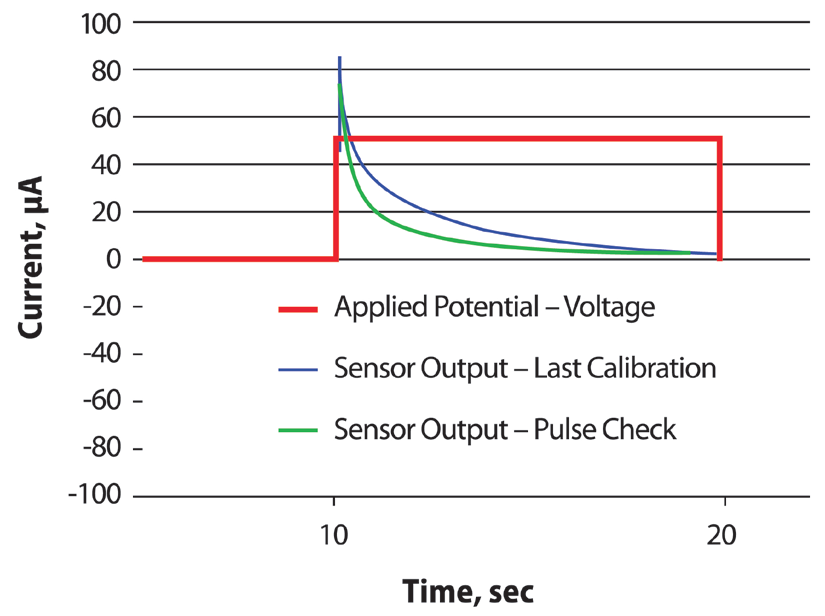
Figure 1. Pulse Check. Image Credit: MSA Safety
Other than its age, a sensor’s change in sensitivity is usually caused by its environment, including pressure, temperature and humidity. The pulse check electronically calculates the change in sensor output response. A pulse is applied to the sensor, where the response is analyzed and compared to the last manual gas calibration.
This is employed to monitor for any alteration in the sensor’s sensitivity and adjust it to be in line with the last gas calibration if necessary. It also confirms that the internal sensor components are properly functioning.
Sensor output sensitivity consists of quantifiable aspects of internal sensor components. As is traditionally applied during a manual calibration, sensitivity can be measured without using test gas.
Output from a regression model is employed to establish whether the sensor requires its sensitivity adjusting to correspond with the last manual gas calibration, or it will indicate that a manual calibration is required because of an extreme change in its sensitivity.
This automatic adjustment in the sensor’s sensitivity is known as Adaptive Environmental Compensation (AEC). Such adjustment is viable because of MSA‘s application-specific integrated circuit (ASIC) utilized in MSA’s XCell Sensors.
The pulse check takes less than 1 second, happens four times per day, and does not affect the transmitter’s analog output or take the instrument off-line.
Diffusion Supervision
Although they are impressive, if the target gas is unable to reach the internal electrochemical cell due to a physical blockage of the sensor’s inlet (as illustrated in Fig. 2), the sensor’s Pulse Check and AEC features are of little value to the end-user.
Almost all gas detection instruments that are deployed for industrial hygiene applications have protective membranes to protect both the internal components of the instrument and the sensor.
The majority, if not all of these instruments, are designed in such a way that they protect the sensor and the instrument itself from dusts, particles, sprays and liquid intrusion. In order to prevent the internal electronics from causing an explosion, instruments that are utilized in hazardous areas also often have a flame arrestor or sinter/frit.
The correct functionality of the instrument requires that the gas passes effectively and efficiently through such protective barriers. If the inlet to the sensor is blocked and the gas cannot reach the electrochemical cell, then figures of merit like the sensor’s precision, response time and accuracy to the target gas are irrelevant.
Unfortunately, instrument diffusion membranes or sinters/frits can become partially or fully blocked from a variety of causes during normal operation and use. These include paint or glue, mud, overspray or vapor, sand, dust and dirt, water and/or ice, insect or animal deposits, or any other extraneous diffusion impeding substances or events.
Blockage of the diffusion path into the instrument and sensor may be partial or complete. ‘Blockage’ may be simply that there is a physical disruption of the flow path, or it could be because of the presence of reactive or absorptive materials deposited on membranes or frits.
A common example of this might be liquid water or excess moisture, which will dissolve common toxic gases such as hydrogen sulfide (H2S), sulfur dioxide (SO2), or chlorine (Cl2).
Blockage of diffusion membranes or other gas entry paths could lead to alterations to the precision or accuracy of the instrument, or it may influence the response time of the instrument.
As previously described, periodic bump tests are an established technique for supplying a relatively high degree of assurance that the gas detector is properly functional, at least at the time and place that the bump check was carried out.
Yet, bump testing an instrument is labor-intensive (depending on the number of sensors and where they are located throughout a facility), time-consuming and calibration gas can be expensive.
Users of fixed H2S and CO gas detectors that take advantage of this new Diffusion Supervision technology are able to reduce their cost of ownership significantly, as no maintenance of any kind (unless called for by the detector) is needed for up to two years.
In order to measure sound across the sensor’s inlet, Diffusion Supervision uses proprietary acoustic mechanical design and algorithms. The difference in the sound is detected if the inlet is blocked and the unit is put into fault. Diffusion Supervision detects the clearance and returns to normal operation when the obstruction is removed.
Diffusion Supervision technology uses a microphone and speaker, which are connected by a sound channel that runs across the sensor inlet. The sound the speaker emits travels through the flame arrestor when the sensor inlet is not blocked, and minimal sound is detected by the microphone.
The tone is reflected by the blocked flame arrestor and the microphone detects a stronger signal If the sensor inlet is blocked. The Diffusion Supervision is part of the TruCal test and happens every 6 hours, the same interval as Adaptive Environmental Compensation.
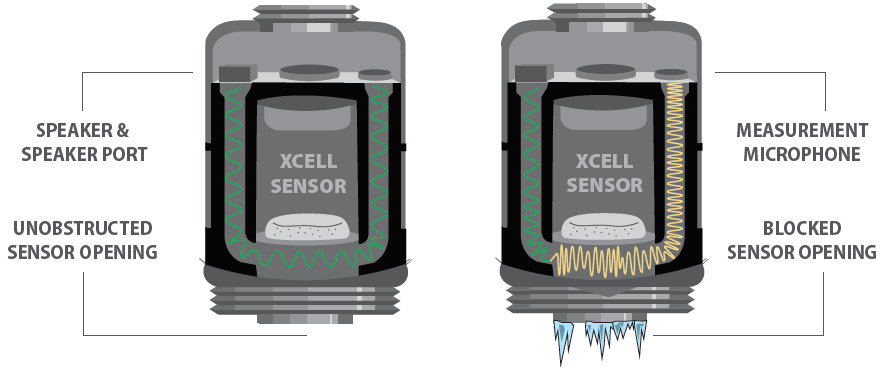
Figure 2. Illustration of an unblocked sensor opening (left) versus a blocked one (right). Image Credit: MSA Safety
Environmental Testing
The problem is electrochemical cells rarely fail in a manner that disrupts the circuit. Instead, they lose sensitivity to a point where they can no longer respond to gas, a condition only seen during a manual gas calibration.
When considering a car battery, one day you get in your car and it will not start. It still turns the radio on and holds some voltage, but that is not useful when you are trying to reach your destination.
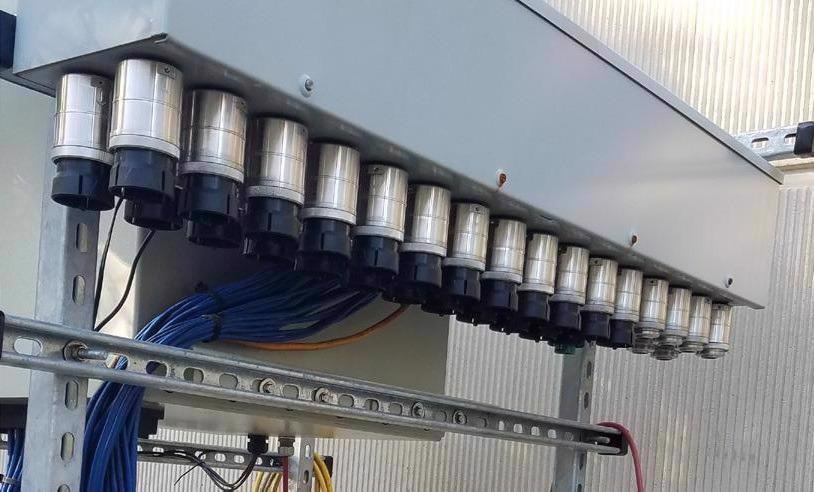
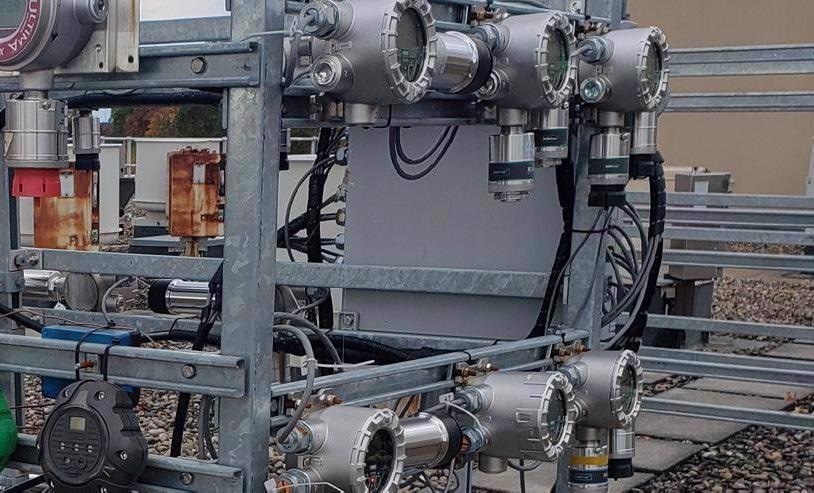
Figure 3. Test areas at MSA provide an open air environment that serve as the primary range for sensor test operations. Image Credit: MSA Safety
Competitive sensor checks are similar to knowing that a car’s battery is dead and a car can no longer start. TruCal gives advance warning to replace your battery and TruCal technology has been tested extensively to ensure that it performs under different environmental conditions (see Fig. 3).
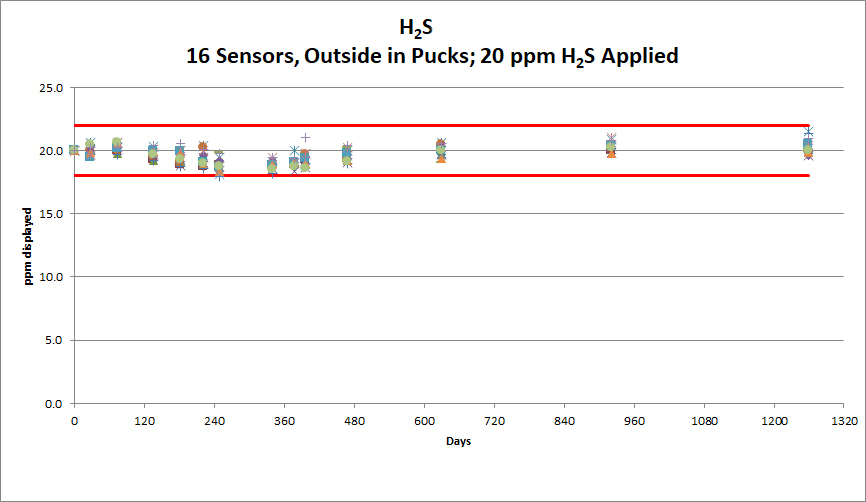
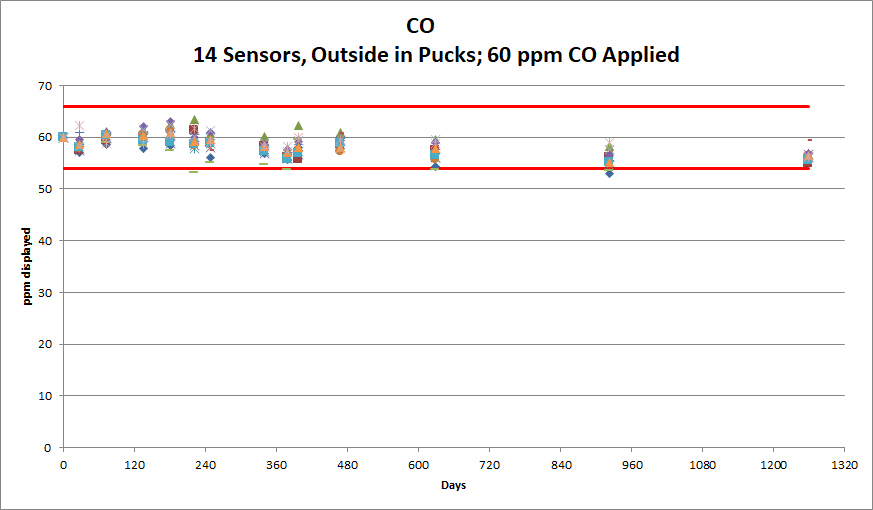
Figure 4. Sensor Accuracy – Outdoor Testing Without Calibrations – Displayed Value. Image Credit: MSA Safety
As shown in Fig. 4, the accuracy and T90 response times have performed flawlessly with constant exposure to the elements, even without calibration. These sensors have been installed on the roof of MSA’s manufacturing facility in Western Pennsylvania and are exposed to all climates: wind, snow, sun, hot, cold, rain, humid and dry.
Each of these sensors was calibrated before installation and have been intermittently gas tested to verify response. There were sixteen H2S sensors and fourteen CO sensors.
For over three years, no calibrations have been performed on any of these sensors, and Adaptive Environmental Compensation (AEC) has been testing the sensor every six hours and adjusting sensor response to account for alterations in its sensitivity because of sensor degradation and environmental conditions.
All of these sensors are still performing accurately even after no calibrations and three years of exposure to the elements, even meeting the stringent ISA performance requirements for toxic gas detection.
The XCell sensors with TruCal are expected to perform within stated performance specifications without manual calibration for two years. There is no requirement for a functional safety check/bump test for sensors with Diffusion Supervision. This is based on over 1,200 days of testing of the XCell H2S and CO sensors.
MSA has also measured the T90 response time of each sensor in addition to the accuracy testing. The H2S sensors’ T90 times are still less than 35 seconds, and the CO sensors’ T90 times are less than 10 seconds even after three years without any calibration or maintenance, as seen in Fig. 5.
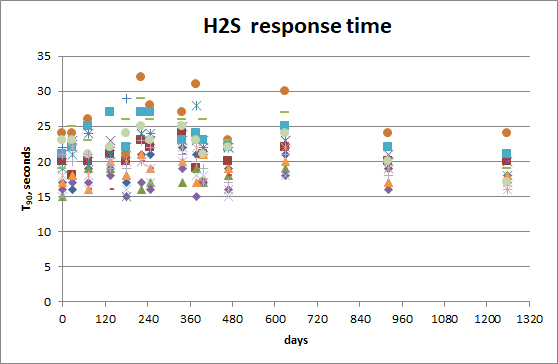
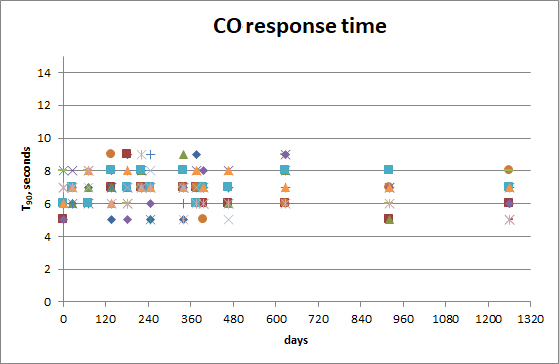
Figure 5. Sensor Response Times – Outdoor Testing Without Calibrations – T90 Response. Image Credit: MSA Safety
Conclusion
In order to account for any drift and to notify if a manual gas calibration or sensor exchange is required, TruCal’s self-checking technology corrects sensor sensitivity. TruCal reassures the user the detector is functioning correctly and can detect gas by proactively carrying out a self-check every six hours.
Six actions that TruCal enables:
- Compensates for sensitivity drift due to its age or changing environmental conditions.
- Confirms that the sensor is operating normally.
- Recommends when a full manual gas calibration should be performed.
- Reports the life and health status as 'Good' or 'Fair.'
- Warns when a sensor has to be replaced in the near future.
- Alerts the end-user that the device is no longer able to monitor the area. A fault will initiate.
TruCal sensors from MSA sets a new standard for reliability while lowering the cost of ownership. MSA has been innovating and creating revolutionary gas detection products since 1914. Their goal is to provide workers with high quality, dependable products, instruments and service to help ensure a safe return home when the work is finished.
References
- ISA / IEC / EN 60079-29-2 (p. 8.3.3.10) Explosive atmospheres Part 29-2: Gas detectors — Selection, installation, use and maintenance of detectors for flammable gases and oxygen.
- ISEA Statement of Validation of Operation for Direct Reading Portable Gas Monitors
This information has been sourced, reviewed and adapted from materials provided by MSA Safety.
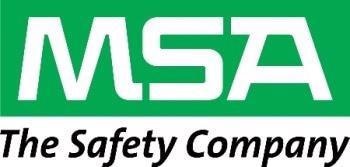
For more information on this source, please visit MSA Safety.