Pressure-sensitive paint (PSP) has gained much attention as a non-intrusive pressure measurement technique for fluid mechanics. This methodology has been used for wind tunnel testing, surface pressure measurement on rotating objects, low-density gas flow measurements, oxygen concentration distribution measurements, and micro-scale gas flow measurements.
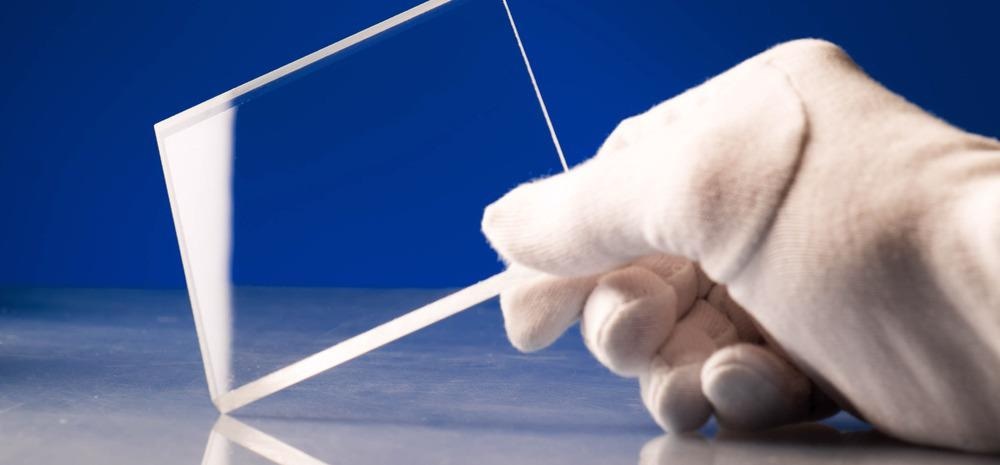
Image Credit: luchschenF/Shutterstock.com
The pressure distribution on a surface to which a PSP coating is applied can be measured by detecting the variation of the luminescence intensity emitted from the pressure-sensitive dyes in the PSP coating. A PSP coating cannot be applied to a plastic surface without resistance to organic solvents. Thus, a sticker-like PSP coating is useful because it does not require the application of an organic solvent and a high level of skill.
In recent years, there have been many studies on the fabrication methods of nano-sheets for wearable sensors and in vitro cellular studies. In general, nano-sheets have unique properties including high transparency, high flexibility, noncovalent adhesion, and excellent electrical and thermal properties due to a large size-aspect ratio. Properties like high flexibility and noncovalent adhesion also make them suitable for PSP.
This article discusses the fabrication of freestanding pressure-sensitive nano-sheet (PSNS) using a sacrificial layer process. The fabricated PSNS can be peeled off from the substrate and attached to another surface.
The basic properties of PSNF fabricated by a spin-coating method were analyzed before mass-production by a roll-to-roll process. Pressure- and temperature-sensitivity, luminescence lifetime, and the quantum yield of the fabricated PSNS have also been investigated.
Methodology
Two kinds of PSNSs with different polymers: poly(1-trimethylsilyl-propyne) (PTMSP) and poly(L-lactic acid) (PLLA) were prepared. PTMSP is known as a glassy polymer with high gas permeability and is usually used as a binder of PSP. However, PTMSP is not used for the fabrication of nano-sheets.
PLLA is one of the polymer materials used to fabricate a nano-sheet by a spin-coating method and a roll-to-roll process, but it is not used as a binder of PSP. As a pressure-sensitive dye, Pt(II) meso-tetra(pentafluorophenyl)porphine (PtTFPP) was employed for both PSNS samples. PtTFPP is widely used as a pressure-sensitive dye due to high pressure sensitivity and optical stability.
Figure 1 shows the PSNS fabrication process used in this study.
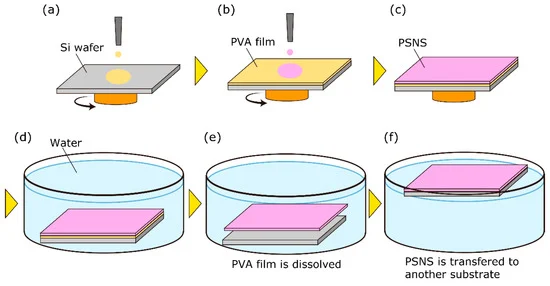
Figure 1. Schematic of PSNS fabrication process based on a sacrificial layer process using a spin-coating method. (a) PVA solution is spin-coated on Si wafer. (b) PSNS is spin-coated on the PVA film. (c) fabricated PSNS and PVA film. (d) Obtained film is immersed in water. (e) PVA film is dissolved and freestanding PSNS is obtained. (f) PSNS is transferred to another substrate. Image Credit: Matsuda et al., 2021.
Figure 2 shows the typical example of the PLLA-PSNS transferred from a silicon wafer to another one. The images were taken by iPhone 8.
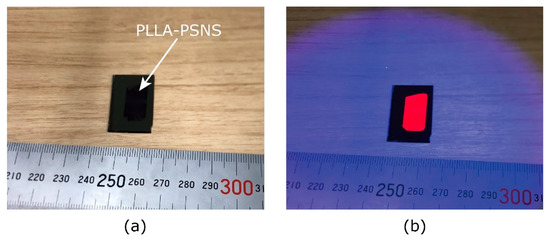
Figure 2. Typical example of PLLA-PSNS transferred on silicon wafer. (a) PLLA-PSNS image without illumination. (b) PLLA-PSNS image with illumination. Image Credit: Matsuda et al., 2021.
The pressure and temperature sensitivity of the fabricated PSNSs were investigated using a calibration chamber. The PSNS samples were placed in the calibration chamber, and the pressure in it was monitored and controlled by a pressure controller. The temperature in the chamber was measured by a thermistor; a Peltier device and a temperature controller were also utilized.
For the pressure-sensitivity test, the pressure in the chamber was controlled in the range of 50 to 110 kPa, and the temperature was maintained at 25 °C. For the temperature-sensitivity test, the temperature in the chamber was controlled in the range from 20 to 45 °C, and the pressure was maintained at atmospheric pressure.
The PSNS was illuminated by an LED device, the central wavelength of which was 395 nm. A CCD camera captured the emission from the PSNS with a band-pass filter of 630 ± 30 nm.
An absolute quantum yield spectrometer measured the quantum yields of the fabricated PSNSs. A lifetime spectrometer measured the lifetimes of the phosphorescence emitted from the PSNS samples. In the lifetime spectrometer, the lifetime is obtained by fitting the data with triple exponential functions.
Results
The results of the pressure- and the temperature-sensitivity test are shown in Figures 3 and 4, respectively. The error bars indicate the standard deviation of the intensity ratio on the sample coupons.
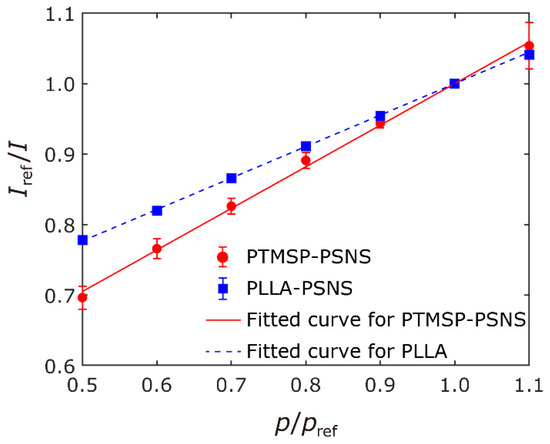
Figure 3. Stern–Volmer plots for PTMSP-PSNS and PLLA-PSNS samples. Image Credit: Matsuda et al., 2021.
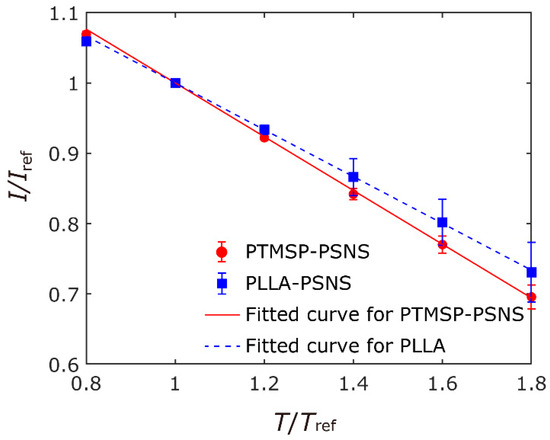
Figure 4. Result of temperature calibration tests for PTMSP-PSNS and PLLA-PSNS samples. Image Credit: Matsuda et al., 2021.
The quantum yields of PTMSP-PSNS and PTMSP-PSNS on a Teflon and an aluminum plate were measured at atmospheric pressure and the temperature of 24 °C. The results are shown in Table 1.
Table 1. Quantum yields of PTMSP-PSNS and PLLA-PSNS.
|
Quantum Yield
(Teflon Plate) |
Quantum Yield
(Aluminum Plate) |
PTMSP-PSNS |
0.014 |
0.007 |
PLLA-PSMS |
0.091 |
0.059 |
In contrast to quantum efficiency, lifetime differences between the PSNS on the Teflon and on the aluminum was minor (within 10%). Figure 5 shows the phosphorescence decay curves of the PTMSP-PSNS and the PLLA-PSNS samples on the Teflon plate at atmospheric pressure and the temperature of 24 °C measured by the lifetime spectrometer.
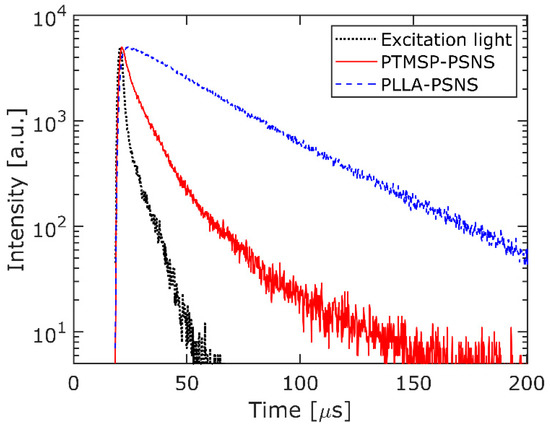
Figure 5. Phosphorescence decay curves for PTMSP-PSNS and PLLA-PSNS. Image Credit: Matsuda et al., 2021.
Conclusion
Two kinds of pressure-sensitive nano-sheet (PSNS) were fabricated based on PTMSP and PLLA as a polymer binder and called them PTMSP-PSNS and PLLA-PSNS, respectively. PtTFPP was used as a pressure-sensitive dye. The fabricated PSNS can be peeled off from the substrate by dissolving a sacrificial film PVA and can be transferred to another substrate.
Although both PTMSP-PSNS and PLLA-PSNS were fabricated by a spin-coater with the same rotational speed, the thicknesses of PTMSP-PSNS and PLLA-PSNS were 22 nm and 91 nm, respectively. This difference in the thickness was considered to be due to the viscosity between the PTMSP and the PLLA organic solution.
The pressure sensitivity of both PSNSs was examined, finding that of PTMSP-PSNS (0.59%/kPa) to be higher than that of PLLA-PSNS (0.45%/kPa). The pressure sensitivity of the fabricated PSNS is similar to those of conventional PSPs.
The quantum yield of PLLA-PSNS is much higher than that of PTMSP-PSNS and the lifetime of PLLA-PSNS is much longer than that of PTMSP-PSNS. These results show that the oxygen quenching in PLLA-PSNS is prevented by the low oxygen permeability of PLLA. Furthermore, it is validated that a white substrate enhances the quantum yield of PSNS.
This study investigated the fundamental properties of PSNS. In the future, the spatial uniformity of PSNS should be investigated for micro-scale flow applications, and a roll-to-roll fabrication method providing larger PSNS for the application of wind tunnel testing should be analyzed.
Continue reading: Taking the Pressure Off for Soft Robotics with Flexible Hybrid Sensor Breakthrough
Journal Reference:
Matsuda, Y., Orimo, R., Abe, Y., Hiraiwa, Y., Okamura, Y., Sunami, Y. (2021) Pressure-Sensitive Nano-Sheet for Optical Pressure Measurement. Sensors. Available at: https://doi.org/10.3390/s21217168.
References and Further Reading
- Liu, T & Sullivan, J P (2005). Pressure and Temperature Sensitive Paints; Springer: Berlin, Germany.
- Bell, J. H., et al. (2001) Surface Pressure Measurements using Luminescent coatings. Annual Review of Fluid Mechanics, 33, pp. 155–206. doi.org/10.1146/annurev.fluid.33.1.155.
- Gregory, J. W., et al. (2008) A review of pressure-sensitive paint for high-speed and unsteady aerodynamics. Proceedings of the Institution of Mechanical Engineers, Part G: Journal of Aerospace Engineering, 222, pp. 249–290. doi.org/10.1243/09544100JAERO243.
- Liu, T., et al. (2021) Pressure and Temperature Sensitive Paints, 2nd ed.; Springer: Cham, Switzerland.
- Disotell, K. J., et al. (2016) Global surface pressure measurements of static and dynamic stall on a wind turbine airfoil at low Reynolds number. Experiments in Fluids, 57, p. 82. doi.org/10.1007/s00348-016-2175-z.
- Sugioka, Y., et al. (2018) Experimental analysis of transonic buffet on a 3D swept wing using fast-response pressure-sensitive paint. Experiments in Fluids, 59, p. 108. doi.org/10.1007/s00348-018-2565-5.
- Running, C. L., et al. (2019) Hypersonic boundary-layer separation detection with pressure-sensitive paint for a cone at high angle of attack. Experiments in Fluids, 60, p. 23. doi.org/10.1007/s00348-018-2665-2.
- Jiao, L., et al. (2019) Resolving vortex-induced pressure fluctuations on a cylinder in rotor wake using fast-responding pressure-sensitive paint. Physics of Fluids, 31, p. 055106. doi.org/10.1063/1.5092944.
- Peng, D., et al. (2020) Experimental study on hypersonic shock–body interaction between bodies in close proximity using translucent fast pressure- and temperature-sensitive paints. Experiments in Fluids, 61, p. 120. doi.org/10.1007/s00348-020-02948-0.
- Inoue, T., et al. (2021) Data-Driven Approach for Noise Reduction in Pressure-Sensitive Paint Data Based on Modal Expansion and Time-Series Data at Optimally Placed Points. arXiv, arXiv:2103.00931.
- Egami, Y., et al. (2021) Ruthenium-based fast-responding pressure-sensitive paint for measuring small pressure fluctuation in low-speed flow field. Measurement Science and Technology, 32, p. 024003. doi.org/10.1088/1361-6501/abb916.
- Kameya, T., et al. (2012) Pressure-sensitive paint measurement on co-rotating disks in a hard disk drive. Optics and Lasers in Engineering, 50, pp. 82–86. doi.org/10.1016/j.optlaseng.2011.06.022.
- Disotell, K. J., et al. (2014) Single-shot temperature- and pressure-sensitive paint measurements on an unsteady helicopter blade. Experiments in Fluids, 55, p. 1671. doi.org/10.1007/s00348-014-1671-2.
- Peng, D., et al. (2017) Single-shot lifetime-based PSP and TSP measurements on turbocharger compressor blades. Experiments in Fluids, 58, p. 127. doi.org/10.1007/s00348-017-2416-9.
- Wong, O. D., et al. (2018) Blade Tip Pressure Measurements Using Pressure-Sensitive Paint. Journal of the American Helicopter Society, 63, pp. 1–11. doi.org/10.4050/JAHS.63.012001.
- Niimi, T., et al. (2005) Application of Pressure-Sensitive Paints to Low-Pressure Range. Journal of Thermophysics and Heat Transfer, 19, pp. 9–16. doi.org/10.2514/1.5047.
- Mori, H., et al. (2006) Pressure sensitive paint suitable to high Knudsen number regime. Measurement Science and Technology, 17, pp. 1242–1246. https://doi.org/10.1088/0957-0233/17/6/S02.
- Kasai, M., et al. (2021) Frequency Response of Pressure-Sensitive Paints under Low-Pressure Conditions. Sensors, 21, p. 3187. doi.org/10.3390/s21093187.
- Matsuda, Y., et al. (2011) Unsteady 2D measurement of dissolved oxygen distribution using luminescent sensor film. Sensors and Actuators B: Chemical, 160, pp. 1464–1467. doi.org/10.1016/j.snb.2011.07.031.
- Huang, C.-Y., et al. (2020) Application of pressure-sensitive paint for the characterization of mixing with various gases in T-type micromixers. International Journal of Heat and Mass Transfer, 156, p. 119710. doi.org/10.1016/j.ijheatmasstransfer.2020.119710.
- Huang, C., et al. (2007) Microchannel Pressure Measurements Using Molecular Sensors. Journal of Microelectromechanical Systems, 16, pp. 777–785. doi.org/10.1109/JMEMS.2007.892914.
- Nagai, H., et al. (2008) Pressure-Sensitive Paint Measurement of Pressure Distribution in a Supersonic Micronozzle. AIAA Journal, 46, pp. 215–222. doi.org/10.2514/1.28371.
- Matsuda, Y., et al. (2011) Pressure-sensitive molecular film for investigation of micro gas flows. Microfluid. Nanofluid., 10, pp. 165–171.
- Matsuda, Y., et al. (2011) Pressure-sensitive channel chip for visualization measurement of micro gas flows. Microfluidics and Nanofluidics, 11, pp. 507–510. doi.org/10.1007/s10404-010-0664-6.
- Li, X., et al. (2008) Highly conducting graphene sheets and Langmuir-Blodgett films. Nature Nanotechnology, 3, pp. 538–542. doi.org/10.1038/nnano.2008.210.
- Okamura, Y., et al. (2009) Free-Standing Biodegradable Poly(lactic acid) Nanosheet for Sealing Operations in Surgery. Advanced Materials, 21, pp. 4388–4392. doi.org/10.1002/adma.200901035.
- Coleman, J. N., et al. (2011) Two-Dimensional Nanosheets Produced by Liquid Exfoliation of Layered Materials. Science, 331, pp. 568–571. https://doi.org/10.1126/science.1194975.
- Okamoto, M., et al. (2017) Sandwich fixation of electronic elements using freestanding elastomeric nanosheets for low-temperature device processes. Journal of Materials Chemistry C, 5, pp. 1321–1327. doi.org/10.1039/C6TC04469G.
- Zhang, S., et al. (2017) Mini Review: Nanosheet Technology towards Biomedical Application. Nanomaterials, 7, p. 246. doi.org/10.3390/nano7090246.
- Huang, W., et al. (2018) Applications of Nanosheets in Frontier Cellular Research. Nanomaterials, 8, p. 519. doi.org/10.3390/nano8070519.
- Matsuda, Y., et al. (2007) Development of pressure sensitive molecular film applicable to pressure measurement for high Knudsen number flows. Experiments in Fluids, 42, pp. 543–550. doi.org/10.1007/s00348-007-0259-5.
- Matsuda, Y., et al. (2009) Extension and characterization of pressure-sensitive molecular film. Experiments in Fluids, 47, pp. 1025–1032. doi.org/10.1007/s00348-009-0694-6.
- Langmuir, I (1917) The constitution and fundamental properties of solids and liquids. II. Liquids 1. Journal of the American Chemical Society, 39, pp. 1848–1906. doi.org/10.1021/ja02254a006.
- Ulman, A (1991) An Introduction to Ultrathin Organic Films; Academic Press: San Diego, CA, USA. Available at: doi.org/10.1016/B978-0-08-092631-5.50009-9.
- Sakamura, Y., et al. (2015) Development and characterization of a pressure-sensitive luminescent coating based on Pt(II)-porphyrin self-assembled monolayers. Measurement Science and Technology, 26, p. 064002. doi.org/10.1088/0957-0233/26/6/064002.
- Lakowicz, J R (2006) Principles of Fluorescence Spectroscopy, 3rd ed.; Springer: New York City, NY, USA.
- Yamaguchi, H., et al. (2009) Discussion on measurement mechanism of pressure-sensitive paints. Sensors and Actuators B: Chemical, 142, pp. 224–229. doi.org/10.1016/j.snb.2009.07.022.
- Egami, Y., et al. (2019) Effects of solvents for luminophore on dynamic and static characteristics of sprayable polymer/ceramic pressure-sensitive paint. Sensors and Actuators A: Physical, 286, pp. 188–194. doi.org/10.1016/j.sna.2018.12.034.
- Matsuda, Y., et al. (2017) Fine printing of pressure- and temperature-sensitive paints using commercial inkjet printer. Sensors and Actuators B: Chemical, 250, pp. 563–568. doi.org/10.1016/j.snb.2017.04.188.
- Claucherty, S & Sakaue, H (2017) An optical-chemical sensor using rhodamine B on anodized-aluminum for surface temperature measurement from 150 to 500K. Sensors and Actuators B: Chemical, 240, pp. 956–961. doi.org/10.1016/j.snb.2016.09.053.
- Asai, K., et al. (2002) Novel Pressure-Sensitive Paint for Cryogenic and Unsteady Wind-Tunnel Testing. Journal of Thermophysics and Heat Transfer, 16, pp. 109–115. doi.org/10.2514/2.6658.
- Mori, H., et al. (2005) Molecular number flux detection using oxygen sensitive luminophore. Physics of Fluids, 17, p. 100610. doi.org/10.1063/1.1921927.
- Okamura, Y., et al. (2013) Fragmentation of poly(lactic acid) nanosheets and patchwork treatment for burn wounds. Advanced Materials, 25, pp. 545–551. doi.org/10.1063/1.1921927.
- Komachi, T., et al. (2017) Adhesive and robust multilayered poly(lactic acid) nanosheets for hemostatic dressing in liver injury model. Journal of Biomedical Materials Research Part B: Applied Biomaterials, 105, pp. 1747–1757. doi.org/10.1002/jbm.b.33714.
- Zhang, S., et al. (2018) Tactile Sliding Behavior of R2R Mass-Produced PLLA Nanosheet towards Biomedical Device in Skin Applications. Nanomaterials, 8, p. 210. doi.org/10.3390/nano8040210.
- Kameya, T., et al. (2014) Dual luminescent arrays sensor fabricated by inkjet-printing of pressure- and temperature-sensitive paints. Sensors and Actuators B: Chemical, 190, pp. 70–77. doi.org/10.1016/j.snb.2013.08.011.
- Huang, C.-Y., et al. (2015) The applications of pressure-sensitive paint in microfluidic systems. Microfluidics and Nanofluidics, 18, pp. 739–753. doi.org/10.1007/s10404-014-1510-z.
- Matsuda, Y., et al. (2013) ZnS–AgInS2 nanoparticles as a temperature sensor. Sensors and Actuators B: Chemical, 176, pp. 505–508. doi.org/10.1016/j.snb.2012.09.005.
- Masuda, T., et al. (1983) Poly[1-(trimethylsilyl)-1-propyne]: A new high polymer synthesized with transition-metal catalysts and characterized by extremely high gas permeability. Journal of the American Chemical Society, 105, pp. 7473–7474. doi.org/10.1021/ja00363a061.
- Nagai, K., et al. (2001) Poly[1-(trimethylsilyl)-1-propyne] and related polymers: Synthesis, properties and functions. Progress in Polymer Science, 26, pp. 721–798. doi.org/10.1016/S0079-6700(01)00008-9.