Columbia’s strain sensors are the industry standard for demanding stress and strain measurement requirements. Columbia’s strain sensors are thermally compensated and use foil strain gauges constructed in a robust housing.

Image Credit: Columbia Research Laboratories, Inc.
Having been fully military flight-qualified and FAA DO-160 qualified, Columbia’s sensors have a substantial history in military aircraft applications. Historically, the company’s sensors have seen extensive use in aerospace applications, but they are also a fantastic fit for structural monitoring, railway stress monitoring and commercial aviation.
Columbia Research Laboratories’ family of strain sensors allows critical undercarriage structures and surfaces to be monitored with greater accuracy than when using counting accelerometer methods.
Using direct strain measurement in aircraft applications, in place of the counting accelerometer methods, a more accurate representation of the fatigue loading a tactical aircraft experiences under various conditions of weight, speed, and mission configuration is provided.
Critical areas, including under carriage structures and control surfaces, may be monitored with greater accuracy for potential fatigue damage induced by high-stress landings and high-g maneuvers.
Columbia’s rugged sensors are easily installed and create access to new areas of opportunity for monitoring critical structures in both high-performance military tactical aircraft and commercial aircraft.
By utilizing the strain sensors in combination with level sensing and recording systems, a stress-related history can be maintained for structures or assemblies which may be subject to damage or abuse during maintenance and overhaul operations, as well as monitoring the stress loading encountered in normal flight operations.
The use of stress histories together with established S-N (fatigue life) curves for materials that are commonly used will allow the development of safer, more economical maintenance and overhaul programs through the application of end of useful life predictions.
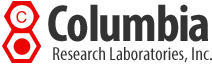
This information has been sourced, reviewed and adapted from materials provided by Columbia Research Laboratories, Inc.
For more information on this source, please visit Columbia Research Laboratories, Inc.