The paper industry is the primary raw material industry of the national economy and an essential industry intricately linked to social civilization and economic development.
The paper-making process is a sophisticated industrial mass and heat transfer process divided into two sections: pulping and paper-making. Cooking, washing, screening, and bleaching are all part of the pulping process.
Paper material preparation, pulp flow, paper surface formation, wet paper press dehydration, drying, paper sheet calendering, and coiling are the main steps in the paper-making process. The recovery method promotes environmental preservation by focusing on evaporation, combustion, and causticization.
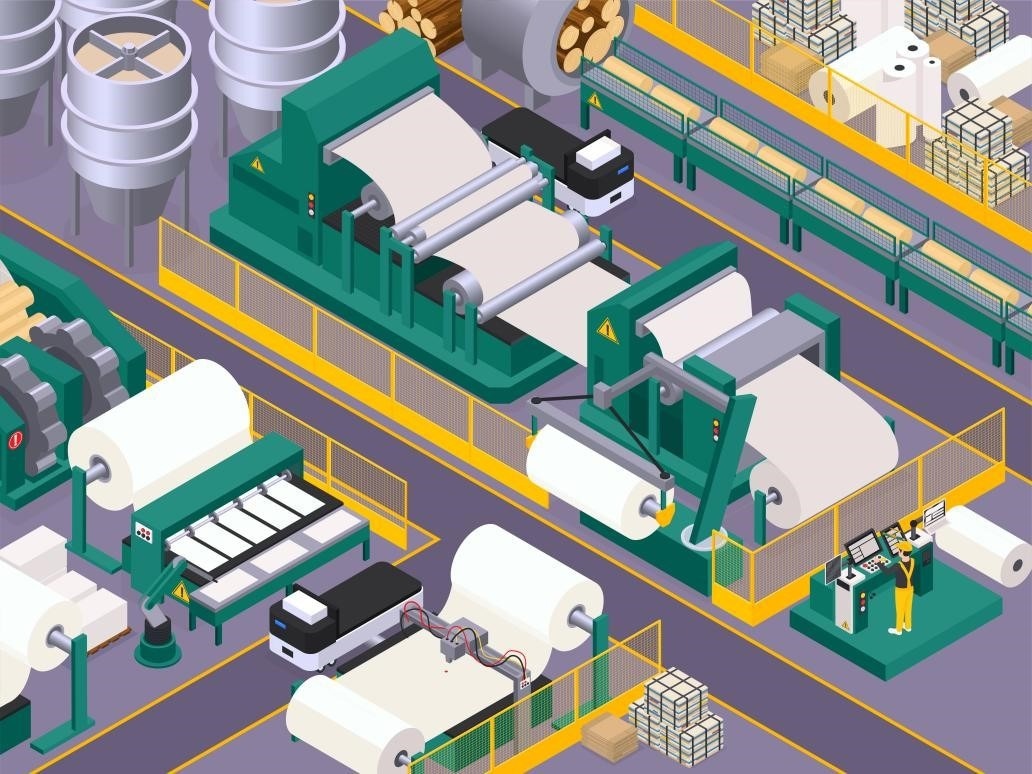
Image Credit: Micro Sensor Co., Ltd
A wide assortment of containers, such as towers, pools, tanks, and barrels, are used in pulp and paper manufacturing. All types of pulp used in production must be housed, shipped, and processed in these containers. Enterprises have introduced computer control systems to maintain the precision and efficiency of the entire process, and the need for intelligent pressure transmitters has also increased.
In conjunction with the computer control system, the intelligent pressure transmitter can measure pressure, differential pressure, flow, liquid level, and other information in the pulp and paper production process, significantly improving the equipment’s production capacity and lowering product consumption and operating costs.
Application System
One of the automation technologies of the pulp and paper production process that may realize optimal control of the industrial production process is the Distributed Control System. The DCS structure is separated into four layers: the field instrument layer, the control unit layer, the factory layer, and the management layer.
Field equipment monitors, records, and controls various process parameters, such as pressure and temperature. The foundation of control is obtaining precise and reliable process parameters. As a result, monitoring the DCS system is vital.
Related Products
The intelligent pressure transmitter MDM6000 series utilizes the latest monocrystalline silicon piezoresistance technology and can produce 4 ~ 20 mA+HART, Modbus-RTU/RS485, and other standard signals. The product has a capability that allows for two-way communication in the control room, transmitter site, and other locations connected to the control loop to complete parameter setting, monitoring, and testing.
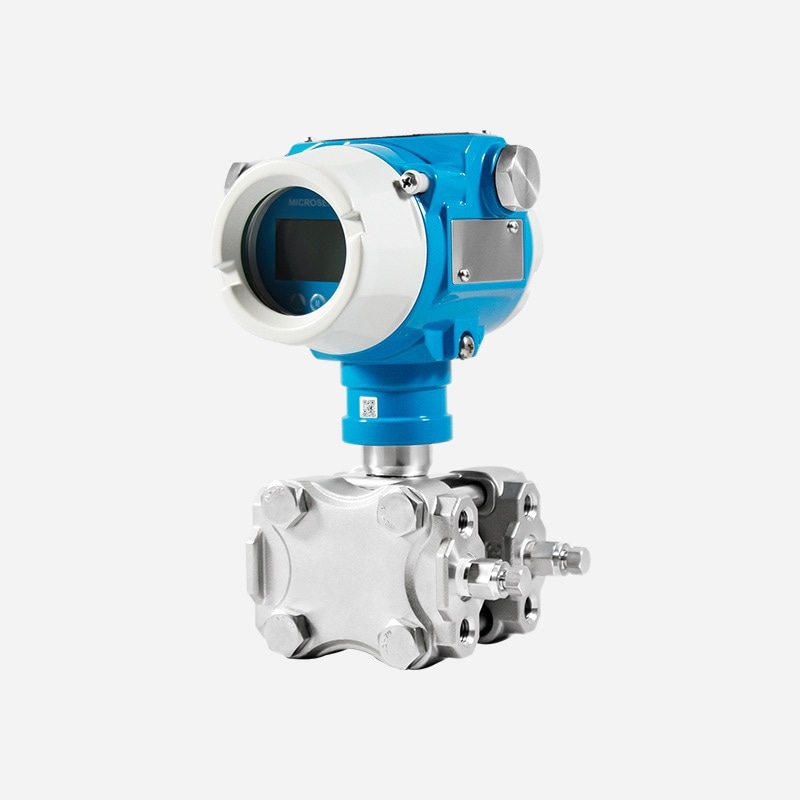
Image Credit: Micro Sensor Co., Ltd
- Accuracy: ±0.075%, ±0.1%, ±0.2%
- Range: 60 mbar ~400 bar
- Long-term stability: ±0.2% SPAN/five years
- Medium temperature: –45 ℃ ~ 105 ℃
- Working temperature: –40 ° C ~ 85 °C
- Power supply: 10.5 V/16.5 V~55 V DC
- Output signal: 4 mA ~ 20 mA DC+HART, Modbus-RTU/RS485
- Protection: IP67
- Certification: Intrinsically Safe (NEPSI), Explosion Proof (NEPSI), CSA, CE (TUV), RoHS, IP67, HART
The MTM4831 temperature transmitter can directly measure temperatures ranging from –200 °C to 500 °C of diverse liquid, gas, or solid surfaces. It does linearity corrections on temperature sensing elements using a specific temperature module and outputs a conventional analog/digital signal.
Temperature measurement is simple to employ in various applications thanks to the many outputs.
- Power Supply: 10 V~30 V DC (Typical:24 V DC)15 V~30 V DC (Display)
- Temperature Ranges: –200 ℃, 0 ℃~500 ℃
- Output: 4 mA~20 mA DC; 4 mA~20 mA DC+HART; 4 mA~20 mA DC + RS485; RS485; Thermal Resistance
- Accuracy
- ±0.25%FS (–20 ℃…0 ℃~105 ℃ )
- ±0.5%FS (–40 ℃…0 ℃~150 ℃)
- ±1.0%FS (–200 ℃…0 ℃~500 ℃)
- Stability: ±0.5%FS/year (general)
- Display: 4-digit LCD/LED
- Relative Humidity: <95%
- Ambient Temperature: –25 ℃~70 ℃
- Flameproof Sign: Ex d IIB T6 Gb
Application
The most prevalent measurements in pulp and paper production are liquid level and pressure measurements, and the medium is usually pulp, steam, clean water, white water, chemicals, and paint. Distinct measuring items require different transmitter kinds; otherwise, the measurement purpose will not be met, and subsequent maintenance will be more complex.
Since pulp is the water suspension of papermaking fiber in pulping and papermaking, it is easy to form flocculation, causing blocking and hardening. Therefore, the flange-type intelligent pressure transmitter is suited for pulp liquid level and pressure measurement. Choose between a single flange intelligent pressure transmitter and a flange intelligent remote pressure transmitter based on the installation site and equipment conditions.
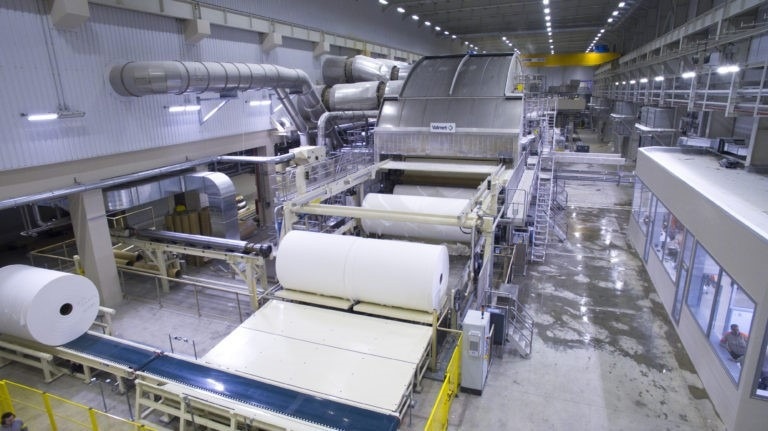
Image Credit: Micro Sensor Co., Ltd
When measuring the pressure of a medium with high viscosity and easy scaling, such as pulp, white water, black liquor, and so on, it is needed to raise the diameter of the impulse pipe and install a valve outside the pressure tap to allow for dredging and cleaning of the impulse pipe without shutting it down.
When monitoring the liquid level of readily precipitated substances, such as white mud and pulp with the flat flange pressure transmitter, a flushing valve shall be provided on the short pipe to flush periodically to ensure that the pressure tap is unblocked and precisely measured.
If the transmitter’s zero position and range are shown to be different from the actual measured value after a period of usage, the transmitter must be removed and the diaphragm cleaned on a regular basis.
Chemical pulping, deinking chemical preparation, and coating preparation and storage all require liquid level and pressure measurements in the pulp and paper industry. The vast majority of these media are corrosive or viscous liquids. For measurement, a flat flange pressure transmitter with a corrosion-resistant diaphragm, such as stainless steel, should be used.
Value
MicroSensor effectively assisted a paper mill in improving equipment operation efficiency and paper quality in a 300,000-ton corrugated paper project.
- Reduces the time and cost of manual inspection significantly
- Improves operational efficiency and product quality effectively
- Provides a solid foundation for future data analysis
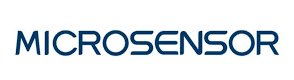
This information has been sourced, reviewed and adapted from materials provided by Micro Sensor Co., Ltd.
For more information on this source, please visit Micro Sensor Co., Ltd.