Resistors, thermocouples, and diodes are the most commonly used temperature sensors for cryogenic applications. The selection of a suitable sensor is based on application, sensitivity, response time and response range, packaging, stability, ease of use, and optimum cost.
Environmental conditions are also crucial to sensor selection because environmental effects such as magnetic fields and ionizing radiation can influence accuracy. Mounting requirements can suggest specific packaging.
Resistive Elements
Resistors are the most widely used temperature sensors for low temperature applications and are classified into Positive Temperature Coefficient (PTC) and Negative Temperature Coefficient (NTC).
PTC resistors are generally a pure metal or a combination of pure metals and small amount of impurities such as rhodium-iron and platinum-cobalt. Semiconductors such as germanium exhibit NTC behavior.
CernoxTM RTDs (Figure 1) are the most widely used sensor at temperatures = 0.2K. This zirconium oxynitride sensor has a monotonic response curve and can be used in the temperature range of 0.1-420K.
Their sensitivity is comparable to a platinum RTD at room temperature. CernoxTM RTDs exhibited a low magnetic field induced temperature error in studies involving temperatures down to 2K and fields up to 32 Tesla. They offer fast thermal response and low magnetoresistance and show superior stability during exposure to ionizing radiation.
![CernoxTM RTDs offer a wide range, low magnetoresistance, and fast thermal response. (Lake Shore CX- AA [left] and CX-SD sensors)](https://www.azosensors.com/image-handler/picture/2018/5/ImageForArticle_504(1).jpg)
Figure 1. CernoxTM RTDs offer a wide range, low magnetoresistance, and fast thermal response. (Lake Shore CX- AA [left] and CX-SD sensors)
Ruthenium-oxide RTDs are thick film sensors fabricated from bismuth ruthenate or ruthenium oxide paste, and useful from temperatures of 40K down to 10mK. However, their sensitivity decreases rapidly at temperatures less than 10K.
Most devices are not monotonic to room temperatures. They exhibit very low magnetoresistance below 1K. It is essential to subject these sensors to thermal shock up to 60 times before calibration to ensure stability.
The following table lists different types of PTC and NTC resistors, their range of use and typical applications:
Type |
Features |
Range of Use |
Applications |
Positive Temperature Coefficient (PTC) Resistors |
Platinum |
Available as industrial grade or standards grade. Industrial grade devices are available in ceramic or glass encapsulation and are interchangeable to an internationally recognized response curve (IEC 751). Sensitivity decreases as temperature decreases. |
15 K to 725 K ITS-90 between 13.8033 K, the triple point e-H2, and 1234.93 K (Range is package dependent) |
Industry standard when highest level of stability and accuracy is needed |
Rhodium-Iron |
Available as industrial grade or standards grade. Wide temperature range; highly stable |
0.65 K to 800 K |
High precision and accuracy over wide temperature ranges |
Negative Temperature Coefficient (NTC) Resistors |
Germanium |
Highly stable; very high sensitivity at low temperatures allows for submillikelvin control |
0.05 K to 100 K (secondary standard) |
Useful for high accuracy work below 30 K when no magnetic field is present |
Carbon-Glass |
Low magnetoresistance effect; extremely high sensitivity at low temperatures allows for submillikelvin control. |
1.4 K to 325 K |
Useful for wide range thermometry in magnetic fields |
CernoxTM |
Wide range; monotonic response curve; small size; fast thermal response; very low magnetoresistance effect; radiation hard |
0.1 K to 420 K |
Useful for wide range thermometry in magnetic fields and ionizing radiation. |
Ruthenium-oxide RTDs |
Low magnetoresistance below 20 K |
10 mK to 40 K |
Thermometry below 1 K with or without magnetic fields |
Diodes
Silicon diodes (Figure 2) are used in many applications for a temperature range of 1-500K, thanks to their user friendliness, large sensitivity, high signal, interchangeability and straightforward instrumentation.
However, they are less appealing in very low temperature applications due to self-heating problems caused by their relatively high power dissipation. The temperature dependence of the forward voltage drop in a p-n junction biased at steady current is the working principle of the diode thermometry.
.jpg)
Figure 2. Silicon diodes are easy to use and highly interchangeable, making them ideal for use in many cryogenic applications for temperatures from 1 K to 500 K. (Lake Shore DT-670-SD)
It is much easier to perform diode measurements when compared to RTD measurements, but less accuracy makes diodes unsuitable for high precision studies. Silicon diodes are highly responsive to a magnetic field and its orientation at temperatures below 40K.
However, diode sensors based on GaAs or GaAlAs (Figure 3) are usable in strong magnetic fields. Their signal and sensitivities are higher than silicon diodes, but they need to be calibrated individually as they are not interchangeable.
.jpg)
Figure 3. GaAs or GaAlAs can be used in higher magnetic fields than silicon diodes, but they must be individually calibrated. (Lake Shore TG120-P GaAlA diode)
Thermocouples
Thermocouples work based on the principle of the Seebeck effect and can be used to measure low mass or differential temperatures. In situ calibration is essential because the wire as a whole affects the output voltage if it passes through a temperature gradient. Mechanical strain, homogeneity, variations in wire composition can influence the temperature readings.
Common types of thermocouples include nickel-10% chromium versus nickel-5% aluminum and silicon (Type K); nickel-10% chromium versus constantan (Type E); and copper versus constantan (Type T).
Type E thermocouples are suitable for applications in the temperature range of 3-1144K and in inert or oxidizing atmospheres. All common thermocouples types other than Types E and K feature one leg of a high thermal conductivity material and require small wire diameters, heat sinking or small temperature gradients to avoid the influence on measurement caused by heat conduction along the wire.
Although thermocouples require only a voltmeter for measurement, they are not suitable for many cryogenic temperature measurements due to the requirement for a temperature reference junction.
Using thermocouples as low temperature thermometers in a magnetic field is a challenging task due to the dependency of the thermoelectric power on both the magnetic field and temperature.
Cryogenic Sensors
Paramagnetic thermometry is the most commonly used temperature sensor for thermometry below 20mK. It applies the Curie-Weiss law for magnetic susceptibility. The paramagnetic susceptibility, χ, is inversely proportional to the temperature.
A mutual inductance technique is used to measure the susceptibility, which can then be utilized with a Superconducting Quantum Interference Device for optimum sensitivity. Besides being used for ultra-low temperatures, this type of thermometry is employed for high-resolution thermometry at elevated temperatures.
A melting pressure thermometer consists of both solid and liquid phases in a stable volume. A capacitive sensor measures the pressure changes caused by temperature. The He-3 melting pressure thermometer consists of intrinsic fixed points and was employed for defining the Provisional Low Temperature Scale of 2000 (PLTS-2000). The voltage noise or Johnson noise across a resistor is measured by a noise thermometer.
A nuclear orientation thermometer (NOT) works on the basis of the anisotropic emission of gamma radiation from a radioactive material in a mildly magnetized host matrix. When properly implemented, NOT yields a direct measure of the temperature.
The most commonly used isotope for NOT is cobalt-60, covering approximately a 1mK to 50mK temperature range. The achievable uncertainty is normally 1% of temperature, but it relies on the source strength, counting times for the radiation intensity, and temperature.
Since capacitors are immune to magnetic fields, they are used in temperature control applications in high magnetic fields. Some temperature controllers employ a resistance temperature sensor for temperature control in zero magnetic field, and use a capacitance sensor to maintain the temperature in field. The physical size and low thermal diffusivity of the dielectric material influence the time response of capacitance sensors.
About Lake Shore Cryotronics
Supporting advanced research since 1968, Lake Shore is a leading innovator in measurement and control solutions for materials characterization under extreme temperature and magnetic field conditions.
High-performance product solutions from Lake Shore include cryogenic temperature sensors and instrumentation, magnetic test and measurement instruments, probe stations, and precision materials characterizations systems that explore the electronic and magnetic properties of next-generation materials.
Lake Shore serves an international base of research customers at leading university, government, aerospace, and commercial research institutions and is supported by a global network of sales and service facilities.
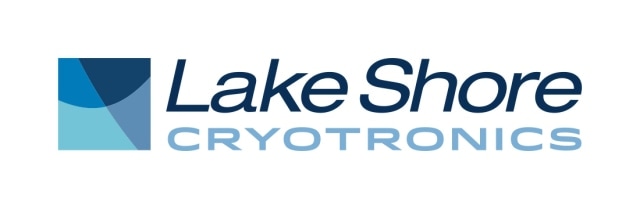
This information has been sourced, reviewed and adapted from materials provided by Lake Shore Cryotronics.
For more information on this source, please visit Lake Shore Cryotronics.