Direct drive motors have been in existence for several years, but it is only with the recent increase in demand for improved performance that they have become more commonly employed.
.jpg)
In this piece, the use of direct drives is compared and contrasted against more traditional motor arrangement, and the range of available position feedback options are discussed.
Direct Drive Terminology
The term 'Direct Drive' can be used to describe any motor, which directly drives a load or rotor without transmission components, such as gears, pulleys or chains. Most typically, the term is used to describe brushless, permanent-magnet, synchronous motors, which transmit their torque directly to their load or rotor.
These motors frequently have a short axial height in relation to their diameter and a large through bore. Direct drive motors, which produce a perpetual torque when stationary or moving over short angular ranges, are also sometimes referred to as 'Torque motors'.
How do Direct Drive Motors Work?
Direct drive motors operate in a manner largely similar to that of the majority of brushless DC motors. Magnets are fixed to the motor's rotor, and windings are arranged on the motor's stator. As the windings are energized, they create electromagnetic fields which either attract or repel the rotor's magnets.
A controlled motion is achieved through appropriate switching or commutation of power to the windings. Both linear and rotary direct drive motors are available, but rotary versions are by far the most commonly employed.
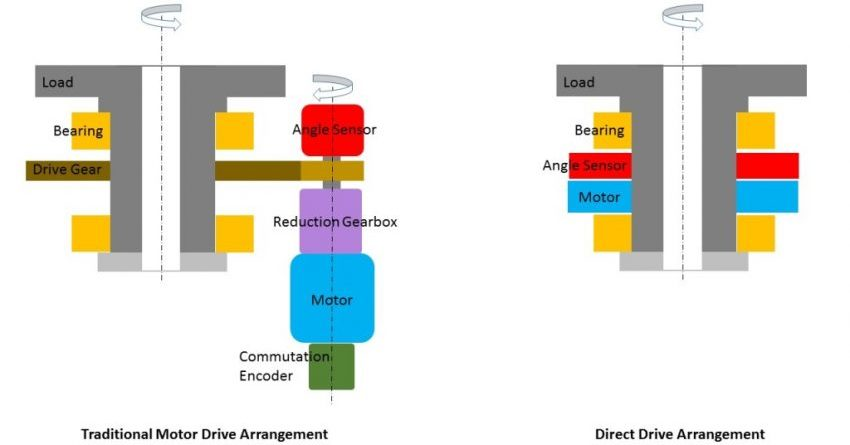
Image Credit: Celera Motion
Direct drive motors with diameters of >1 m are possible, and can produce torque of >10000 Nm. Direct drive motors are often 'frameless', meaning they are supplied without a housing, bearings or feedback sensor.
This allows machine builders and system integrators to adapt their housing, shaft and bearing design to enhance overall size, shape, weight and dynamic performance.
A design engineer is likely to choose a direct drive for two key reasons. These are dynamic performance and shape factor. Rather than managing a coupling, gearbox, belts or chains, a direct drive motor fixes directly to the load, meaning there is no hysteresis, backlash or 'lost motion' regardless of the direction of movement.
Motors which are somewhat flat with a large hole in the center, allowing slip-rings, pipes and cables to pass through, offer a design advantage that should not be undervalued.
The benefits of the direct drive approach include:
- Outstanding dynamic performance and precise control of position and / or speed
- No backlash or wear
- High reliability, due to a small number of elements and the removal of gears, pulleys, seals, bearings etc.
- Compact, with low axial height and large bore possible
- Low torque ripple or 'cogging'
- Energy efficiency from eradication of losses in intermediate mechanical elements
- Minimal acoustic noise or self-induced vibration
- Minimal maintenance
- Low cooling requirements as a result of beneficial thermal geometry
- Relatively large airgaps - simple installation and improved resistance to shock.
The most commonly thought of disadvantage of direct drive motors - that they are most costly than traditional motors - is, in fact, often more a perception than a fact.
While the cost of a direct drive motor may be higher in a simple comparison, a more holistic view, which accounts for the eradication of intermediate gears, couplings and maintenance, in addition to the reduction in overall mechanical simplification, demonstrates that direct drive arrangements are , perhaps unexpectedly, the most cost effective and high-performance solution in many applications.
Typical examples of direct drive applications are found in gimbals, such as antenna systems (eg vehicle mounted satellite communications), surveillance & CCTV cameras, scanners, telescopes, electro-optics, rate tables, and radar systems. Uses can also be observed in CNC machine tools, packaging equipment, robotics and even advanced record turntables.
Where direct drives have a reasonably small bore (<2”), there are a number of options for position feedback sensors based on optical, magnetic, capacitive and inductive technologies. For larger bores, the main choices are frameless resolvers, ring encoders and inductive encoders.
Frameless Resolvers
The terms frameless resolver, slab resolver or pancake resolver generally refer to a resolver whose axial height is low in relation to its diameter. Technically, 'frameless' means that the resolver does not have a housing. However, among engineers, it is common to use the term frameless in reference to a resolver with a small height and large diameter.
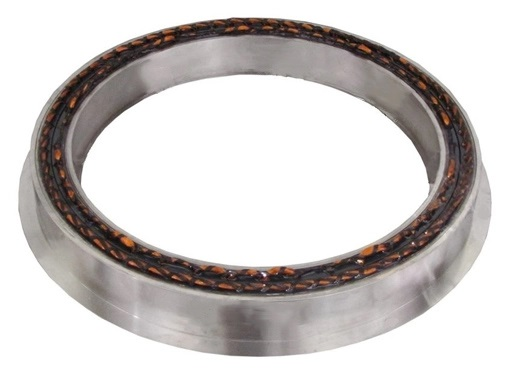
Figure 1. A frameless resolver with low axial height and large diameter. Image Credit: Celera Motion
Most resolvers are brushless rather than brushed, but are all founded on transformer principles, making them inductive angle sensors. The position of a resolver's rotor varies in relation to its stator and the electromagnetic coupling between the rotor and stator also shows variance. This can be observed as the resolver's output signals vary sinusoidally in relation to the excitation or input signal.
Resolvers may be deemed 'single speed', 'two speed', 'four speed', etc. This denotes the number of instances in which that the resolver's output uniquely differs over a single revolution. A single speed resolver's output is unique over 1 rev; a two speed resolver's output is unique over any 180 degrees within 1 rev; a four speed resolver's output is unique over any 90 degrees within 1 rev, and so on.
Resolvers have an outstanding track record in safety-related applications, particularly in civil aerospace. However, despite being highly rugged and reliable, they are often large, weighty and challenging to customize.
Ring Encoders
Ring encoders may also be referred to as large hollow bore encoders or large through shaft encoders. As is the case with frameless resolvers, each of these terms denotes an encoder whose axial height is low in relation to its diameter. Ring encoders are generally optical or magnetic.
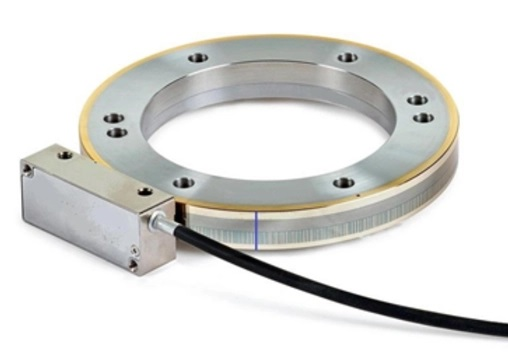
Figure 2. A ring encoder with low axial height and large diameter. Image Credit: Celera Motion
The optical encoder engages the scanning of a fine grating or “scale” lit up by an LED light source. The scale, rotary or linear, is made up of clear and opaque “lines” that are organized in a 50-50 duty cycle. The quantity of transparent areas on the disc links to the scale pitch, which expresses the encoder's resolution.
The sensor produces a voltage proportionate to the incident light intensity. As the sensor moves relative to the scale, the voltage varies sinusoidally. Optical encoders offer excellent accuracy, however they are comparatively fragile and vulnerable to contaminants.
A magnetic encoder makes use of a multi-pole magnet track. The sensor, Hall-effect or magnetoresistive, measures the variation in magnet flux as the magnetic poles move in relation to the sensor. As in the optical encoder, sine and cosine signals can be produced. Magnetic encoders are sturdy, small in size and can be highly economical.
However, magnetic encoders are vulnerable to magnetic fields. It is challenging to produce a fine pitch magnetic track limiting resolution. Repeatability is lessened by hysteresis and accuracy is varied over operating temperature range. The magnetic track is somewhat brittle and can be vulnerable to shock.
Inductive Encoders
Inductive encoders (IncOders) employ the same central physics as resolvers, however, their digital electrical outputs are aligned with those of optical encoders. In this manner, they boast the benefits of being reliable and sturdy, in the manner of resolvers, but also have a simple to operate electrical interface.
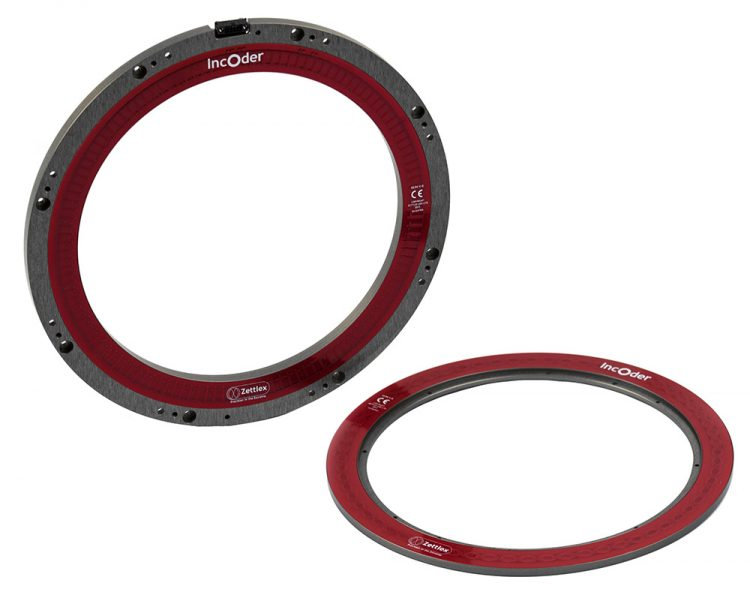
Figure 3. A large bore, low height inductive encoder. Image Credit: Celera Motion
In contrast to the design of resolvers, all necessary electronics are housed within the incoder's stator. This means that the electrical interface is generally a low voltage DC supply, which creates a digital data output representing absolute angle or change in angle.
In contrast to a ring encoder, the incoder's measurement is not made at a single point but rather across the full planar faces of rotor and stator. This means that incoders are less vulnerable to inaccuracies from non-concentric rotation, making their installation relatively simple.
Incoders are especially suitable for applications such as gimbals and turntables, where both low axial height and a large through bore are required.
Incoders can be obtained in absolute and incremental formats with high-resolution digital outputs (up to 4,000,000 counts per revolution), such as SSI, SPI, BiSS-C and AquadB pulses. A number of devices can also be employed as replacements for potentiometers with 0-5 V and 0-10 V outputs.
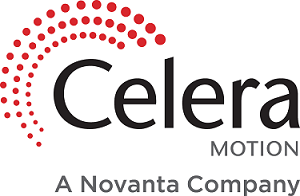
This information has been sourced, reviewed and adapted from materials provided by Celera Motion.
For more information on this source, please visit Celera Motion.