Dedicated to developing innovative hydrokinetic turbines to generate “green” energy from the motion of the sea, Irish company Tidal Energy Limited (TEL) recently had a pressing need for a way of accurately of measuring the power produced by its scale-model prototypes.
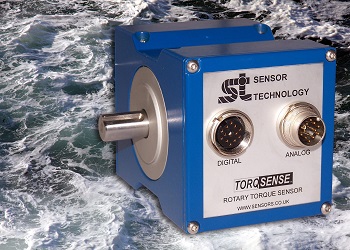
Equipment from Sensor Technology provided a convenient and dependable solution where other methods had failed.
TEL was established in 2008 by Marine Scientist, David Baird, and Civil Engineer, John Lambe, who realised that the growing demand for renewable energy sources meant that there would be good market for efficient and cost-effective marine hydrokinetic turbines.
They resolved to pool their expertise to develop suitable products, using a low cost approach – instead of expensive tow tanks for prototype testing, TEL would use its existing resources, including boats and moorings, and would test their prototype turbines under real operating conditions in the open sea.
When it came to measuring the power produced by the turbines, however, TEL found that it had a problem. In order to calculate the power, it needed to be able to measure both the rotational speed of the turbine shaft and the torque being transmitted by the shaft. While the speed measurement was straightforward, measuring the torque accurately presented rather more of a challenge.
Initially, the company used a de Prony Brake system for torque measurement. This essentially relies on measuring the force produced in a friction band around the shaft. Unfortunately, this system, while simple, was cumbersome to work with and, in addition, its numerous inherent sources of error meant that TEL was unable to achieve the required level of accuracy in its measurements.
A better solution proved elusive, however, particularly as the torque measuring system would need to operate in a wet and salty marine environment. Ultimately, after searching the market for a cost-effective product that would meet its needs, TEL found the RWT410/420 series of TorqSense rotary torque sensors from Sensor Technology.
These innovative sensors are available in three different body sizes and six different shaft sizes, covering torque measurements from 1 Nm to 13,000 Nm, which made it easy for TEL to choose a sensor that exactly met its requirements.
Like all of the sensors in the TorqSense range, the RWT410/420 series uses novel sensing technology that depends for its operation on surface acoustic wave (SAW) transducers. These transducers comprise two thin metal electrodes, in the form of interlocking “fingers”, on a piezoelectric substrate such as quartz. When an RF signal of the correct frequency is applied to the transducer, surface acoustic waves are set up, and the transducer behaves as a resonant circuit.
The essential feature, however, is that if the substrate is deformed, the resonant frequency changes. When the transducer is attached to a drive shaft, the deformation of the substrate and hence the change in resonant frequency is related to the torque applied to the shaft. In other words, the transducer, in effect, becomes a frequency-dependent strain gauge.
Since the transducers operate at radio frequencies, it is easy to couple signals to them wirelessly. Hence, TorqSense sensors that incorporate the SAW transducer technology can be used on rotating shafts, and can provide data continuously without the need for the inherently unreliable brushes and slip rings that are often found in traditional torque measurement systems.
In addition to accurately measuring shaft torque, the sensors also measure rotational speed and, by combining these two measured values internally, they can produce an output that directly indicates shaft power, which was exactly what was needed in the TEL application. TorqSense sensors also feature robust sealed construction, allowing them to operate reliably in marine and other challenging environments.
In the TEL application, the RWT410/420 sensor is used in conjunction with Sensor Technology’s TorqView software package. This runs on a laptop PC that is taken on board the boat when the scale-model hydrokinetic turbines are being tested, and provides a direct real-time readout of the power produced by the turbine. The software also logs data from the sensor so that this can be analysed further after the test has been completed.
We’ve now been using the TorqSense sensor for over two years and it’s proving absolutely invaluable in our work.
It’s easy to use, it’s reliable, and it consistently delivers accurate results that are playing a key role in helping us to refine the design of our hydrokinetic turbines. In short, it’s an exceptionally useful product, and I have no hesitation in recommending it.
David Baird - TEL