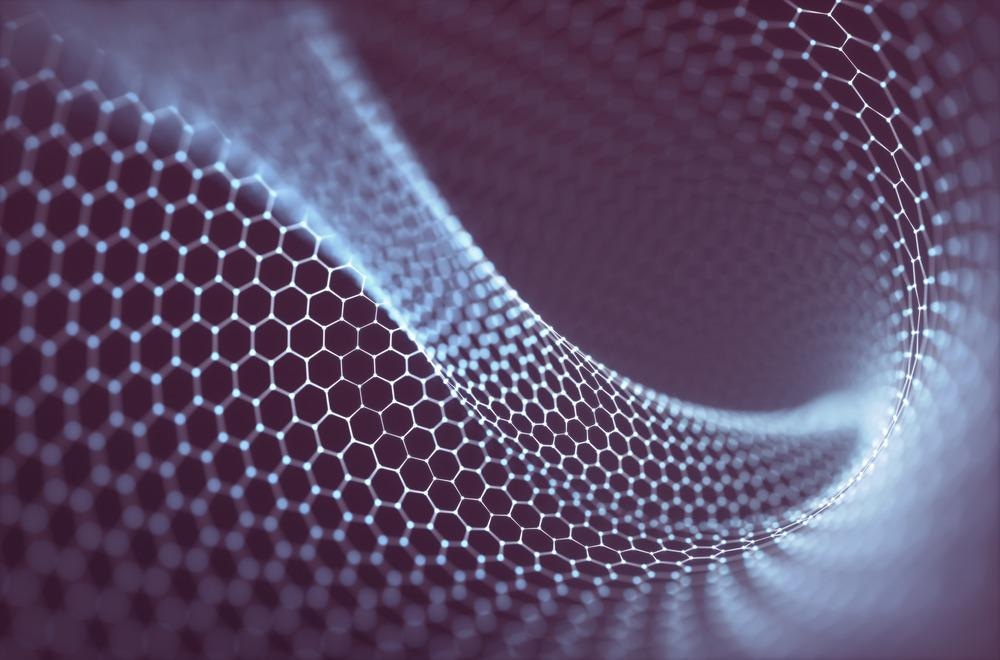
Image Credit: ktsdesign/Shutterstock.com
The printed sensors developed by the team are 50 times more sensitive when compared to the industry standard and also exceed other similar nano-enabled sensors in terms of flexibility—a crucial metric that is perceived as a game-changer in the industry.
Boosting flexibility and sensitivity without decreasing performance makes the new technology the perfect candidate for the emerging fields of medical diagnostic devices and wearable electronics.
The research team, headed by Professor Jonathan Coleman from the School of Physics at College Dublin and one of the leading nanoscientists in the world, revealed that they can create a cost-effective, printed, graphene nanocomposite strain sensor.
The researchers devised a technique to create G-putty-based inks that can be printed as a thin film on band-aids and elastic substrates and can also be fixed effortlessly to the skin.
Formulating and testing inks of varying viscosities (runniness), the researchers discovered that they could customize G-Putty inks based on printing technology and application. The team has published their findings in the Small journal.
In medical environments, strain sensors are a highly useful diagnostic tool and they are used to quantify the variations in mechanical strain, like pulse rate, or variations in the ability of a stroke victim to swallow. A strain sensor operates by identifying this mechanical change and changing it into a proportional electrical signal, and thus serves as a mechanical-electrical converter.
While strain sensors are presently unavailable on the market, they are chiefly made from metal foil that presents certain limitations in terms of sensitivity, versatility, and wearability.
My team and I have previously created nanocomposites of graphene with polymers like those found in rubberbands and silly putty. We have now turned G-putty, our highly malleable graphene blended silly putty, into an ink blend that has excellent mechanical and electrical properties. Our inks have the advantage that they can be turned into a working device using industrial printing methods, from screen-printing, to aerosol and mechanical deposition.
Jonathan Coleman, Professor, School of Physics, Trinity College Dublin
“An additional benefit of our very low-cost system is that we can control a variety of different parameters during the manufacturing process, which gives us the ability to tune the sensitivity of our material for specific applications calling for detection of really minute strains,” added Professor Coleman.
In the global medical device market, present market trends indicate that this analysis is well placed within the move to tunable, personalized, wearable sensors that can be worn on the skin or easily integrated into clothing.
In 2020, the wearable medical device market was pegged at USD $16 billion with predictions for considerable growth, specifically in remote patient monitoring devices and a growing focus on lifestyle and fitness monitoring.
The researchers are aiming to transform the scientific study into a product.
The development of these sensors represents a considerable step forward for the area of wearable diagnostic devices—devices which can be printed in custom patterns and comfortably mounted to a patient’s skin to monitor a range of different biological processes.
Dr Daniel O’Driscoll, School of Physics, Trinity College Dublin
O’Driscoll continued, “We’re currently exploring applications to monitor real-time breathing and pulse, joint motion and gait, and early labour in pregnancy. Because our sensors combine high sensitivity, stability and a large sensing range with the ability to print bespoke patterns onto flexible, wearable substrates, we can tailor the sensor to the application.”
The methods used to produce these devices are low cost and easily scalable—essential criteria for producing a diagnostic device for wide-scale use.
Dr Daniel O’Driscoll, School of Physics, Trinity College Dublin
Professor Coleman recently received a European Research Council Proof of Concept grant to work on these outcomes to design a prototype for a commercial product. The team is ultimately aiming to find prospective industry partners and investors and establish a spin-out around the technology targeting both medical and recreational applications.
Journal Reference:
O’Driscoll, D. P., et al. (2021) Printable G‐Putty for Frequency‐ and Rate‐Independent, High‐Performance Strain Sensors. Small. doi.org/10.1002/smll.202006542.