UV-cure compounds are available in 100 percent reactive formulations. One feature of these compounds is that they are not oxygen-inhibited and they exhibit fast curing rates at ambient temperatures and in the presence of air. This eliminates the need for special equipment for atmospheric control - a nitrogen atmosphere, for example - to effect tack-free cures. Equally important for selected formulations, cure continues in the dark after UV exposure until all the UV reacting species have been consumed, thus making the most economical use of UV energy.
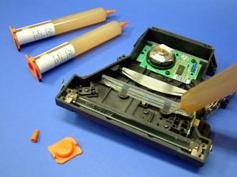
Secondly, these compounds can be cured in significant cross-section thicknesses up to ½" and more for specific formulations. In sharp contrast, most older UV curing compounds are limited to depths of less than 10 mils. This "in depth" curing feature greatly extends the range of electrical/electronic applications to potting and encapsulants including sensitive electronic components (IC chips, light emitting diodes, high voltage coils, and optical fibers). Additionally, applications are extended to printed wiring boards, capacitor seals, and electrical connectors. Maximum dimensional accuracy is assured even with "in depth" pottings and encapsulations because the UV-cure compounds cure with minimum shrinkage without the evolution of solvents or other volatiles.
Thirdly, the compounds produce coatings, bonds, pottings, and encapsulations with service capability over a temperature range from -80° to +350°F. Because of their superior chemical resistance, they can function without difficulty for long time periods, even in adverse environmental conditions, such as the presence of moisture and heat.
There are a variety of other reported advantages to using these UV-cure compounds. One-component systems, for example, require no labor-intensive weighing and mixing. Production schedules are simplified due to the elimination of pot life problems and lengthy ambient temperature cures, (often with post-cure requirements), or the use of oven equipment for elevated temperature cures.
Long term stability is possible when stored at ambient temperatures in the absence of UV light. No loss of pertinent application and/or performance properties is apparent after prolonged storage for six months or more in the absence of UV light, and activation occurs only when exposed to UV light of 250-350nm.
These 100 percent reactive polymer systems are said to assure minimal shrinkage upon cure and provide optimum dimensional accuracy and stability due to the absence of solvents and other volatiles. Complete cures are achieved without residual surface tackiness at ambient temperatures and in the presence of air.
Our UV product line consists of epoxies, polyurethanes, polyesters and acrylics. We offer a wide variety of products. Grades vary in viscosity, cure speed, hardness, strength, chemical resistance, thermal stability, electrical insulation, optical properties, etc. Special formulations have outstanding abrasion resistance, enhanced temperature resistance, USP Class VI approval, withstand exposure to sterilants and are non-yellowing. Our compounds are presently employed in the medical, electronics, appliance, optical, photonic, military, automotive and many other industries. Applications range from bonding lenses, voice coils, magnets, syringes, and catheters to alternators, LED's, headlamps, sensors, wire tacking and connectors.
Some of Our Most Popular UV Curable Products...
UV15 |
Low viscosity, rigid UV curable system with superb thermal stability. Also capable of spin coating. |
UV18S |
UV curable system with superior resistance to chemicals, particularly solvents. |
UV15X-6MED-2 |
UV curing system with high flexibility that is biocompatible per USP Class VI testing. |
UV15-7DC |
Dual cure UV system with a secondary heat cure mechanism (250°F) for “shadowed out areas” (those not available to the UV light source). |
UV15-7TK1A |
Specialty UV curable translucent paste that is ideal for sealing and bonding. |
Applications
The polymer systems can be cured at ambient temperatures and in the presence of air with commercially available UV lamps in very short time periods (1 minute or less). While 200-300 watt/linear inch, medium pressure mercury vapor lamps are recommended for industrial operations, a variety of other lamp equipment also can be used, providing their output includes UV light of 250-350nm wavelengths. Cures can even be achieved with low intensity UV sources, but cure times will be significantly longer and may require several minutes or more.
No solvents or other volatiles are released during curing. Curing can be accomplished solely at ambient temperatures or can be accelerated by heat. In general, a thicker layer of UV curing material will require somewhat longer exposure to UV light than a thinner one, but the relationship is not directly proportional. Also, the rate of cure increases with the amount of UV intensity deposited on the surface -but again the relationship is not directly proportional. The rate of curing furthermore depends on the distance of the surface of the UV curing polymer system from the UV radiation source.
When cured by UV light, these compounds, used in thermoset coatings, adhesive/sealants, pottings, and encapsulations, reportedly provide durability, strength, hardness, impact resistance, adhesion, electrical insulation characteristics, and inertness to many chemicals, including water and common solvents.
For optimum adhesion, substrates must be carefully cleaned before application, especially because of the possible presence of oils, greases, release agents, dirt, and other contaminants. In many cases, such as with metals and other inorganic substrates, the degree of cleanliness can be ascertained by a simple test which involves spreading a few drops of cool water on the surface. If the water spreads over the area with a continuous film, parts are sufficiently clean for further processing; if the water beads or stays in puddles, EPA acceptable solvents such as IPA or acetone should be used for degreasing. The water test should then be repeated before applying the UV-cure compound.
The various compounds have been successfully applied on many different substrates such as polyester and polyimide films, sputtered metal films, and high purity alumina ceramics. Successful operations are being carried out with high automated, continuous processing equipment featuring line speeds of 80 ft/min and more.
Other common substrates upon which the UV-cure polymer systems have been applied include glasses, silicon and other semiconductors, and optical fibers (including silicas and acrylic plastics). Also included are paper and paperboards, sputtered and ion-plated coatings, elastomers, and printing wiring boards (including epoxy/glass boards).
Polyolefins such as polyethylene and polypropylene, as well as fluorocarbon polymers such as polytetrafluoroethylene and various chlorinated fluorocarbon resins, require special surface treatments to obtain adequate adhesion. The new UV-cure compounds have been formulated to enhance adhesion to even difficult-to-bond substrates. They are said to consistently be able to exceed stringent electrical /electronic requirements in many high volume critical product applications, even upon prolonged exposure in hostile environments, including high energy radiation.
The UV-cure polymer systems are finding wide acceptance not only in the so called "high tech" electrical/electronic industries and fiber optics processing, but also for a variety of other applications with cure-on-demand - a most desirable feature.
Typical Applications for Master Bond UV Curable Systems
OPTICAL/LCD/LCP |
- Bonding glass and plastic fibers to fiber optic connectors and ferrules
- Optical Replication
- Coating, potting, or bonding optically clear and/or optically sensitive components and indicators
- Mounting fiber optics
- Fiber optics splicing
- Fiber optic and lens bundling and terminating
- Lens and prism bonding
|
- Encapsulation of detectors
- Fillet bond where good optical transmission in UV, visible, or infrared range is required
- Mounting, fixturing, laminating, tacking, bonding, and sealing of borescopes (remote video scopes) and doublets (stacked lenses)
- YAG Lasers (Yttrium aluminum garnet-synthetic crystalline material. Used in manufacturing, and to mark/cut metals)
- LCD Laminations
- Polarizer Laminations
- LCD Sealant
|
MEDICAL (Meets USP Class VI standard for disposable devices. Can resist appropriate sterilization for disposables.) |
- Needle assembly and bonding (heat exchanger assembly, metal bonding, transducer assembly, potting, bonding connectors)
- Respiratory devices
- Breathing mask assembly
- Tracheotomy tube assembly
- Resuscitator apparatus
- Bags for storing liquid contents (drips, IV, saline, waste, etc.)
- Can be used to fabricate "Form in place" gaskets
|
- Catheter bonding, sealing, and assembly
- Guide wire assembly
- Bore tube sealing
- Balloon bonding
- Sensor attachment
- Tube joining
- Catheter hubs
- Bonding of plastics including PVC & SEBS (styrene-ethylene/butylene-styrene)
|
ELECTRONIC |
- Encapsulation and coating for environmental protection [shadowed out areas can be cured with heat (double cure)]
- Glob top
- Strain relief or chip encapsulation
- Precision application to specific electronic assembly areas
- Thin coating, wicking, and underfill
- Plastic bonding, potting, and sealing
- Wire tacking and coating
|
- Capacitor bonding
- Chip bonding
- Tamper-proofing components
- Prevent coils from unwinding
- Sealing and potting electrical components
- HGA (head gimbal assembly) and tamper-proofing
|
BONDING/LAMINATION (NON-OPTICAL) |
- Polishing
- Protective coating for abrasion resistance, and water or chemical resistance
- Crystal assembly
- Glass laminations/sealing/potting/bonding
- Bonding metal, steel, and aluminum to glass
- High peel/cleavage strength for glass and metal bonding
- Bonding transparent plastics such as acrylics and polycarbonate to various metals
- Flexible plastic assemblies
- Flexible and rigid bonding of clear plastics
- Rapid bonding and sealing of plastics to stainless steel, polycarbonate, and PVC
|
- Mirror assembly
- Bonding glass to thermoset plastics, polycarbonates, acrylics, phenolic, and filled plastics
- Spin coating UV curables for glass and other substances
- Glass cationic epoxy and encapsulant
- Gap filling of non-flat, irregular and handmade glass
- Bond plastic to ABS, CAP, MBS, PBT, PET, PP, PS, PVC, SAN, Valox, acrylic, brass, ceramic, glass PETG, nylon polyimide, polarized and polyester film, polycarbonate, polystyrene, polyurethane, styrene mylar
- Wire harness assembly
- Plastic potting, laminating, and sealing
- Sealing PVC, PET, A-PET, R-PET clamshell packages
- Bonding rigid fittings to flexible tubing
|
SPECIALTY PRODUCTS |
- MEMS Device-internal casting and bonding
|
- Nano-silica filled system with superior physical properties especially dimensional stability and low shrinkage
|
Electronic Grade Polymers for Electronic Manufacturing by Master Bond
Master Bond's line of microelectronic formulations consists of epoxies, silicones, polyurethanes, acrylics and latex solutions. They include electrically insulative, thermally conductive and electrically conductive systems. Both one and two component compounds are available for use. These products are currently employed in applications ranging from heat sinking to glob tops to surface mounting. Many of these compounds have unique properties such as low thermal expansion coefficients, exceptionally high thermal conductivity, low stress, etc. Master Bond is also actively engaged in developing new products to keep pace with the rapid technological advancements in the microelectronic industry ranging from flip-chip technology to advanced die-attach processes.
Master Bond offers specialty systems for computers, telecommunications devices, audio/video devices, avionics and aerospace applications, as well as automotive manufacturing, interactive circuitry and advanced semiconductor equipment.